3 Innovations from Leading Band Heater Manufacturers
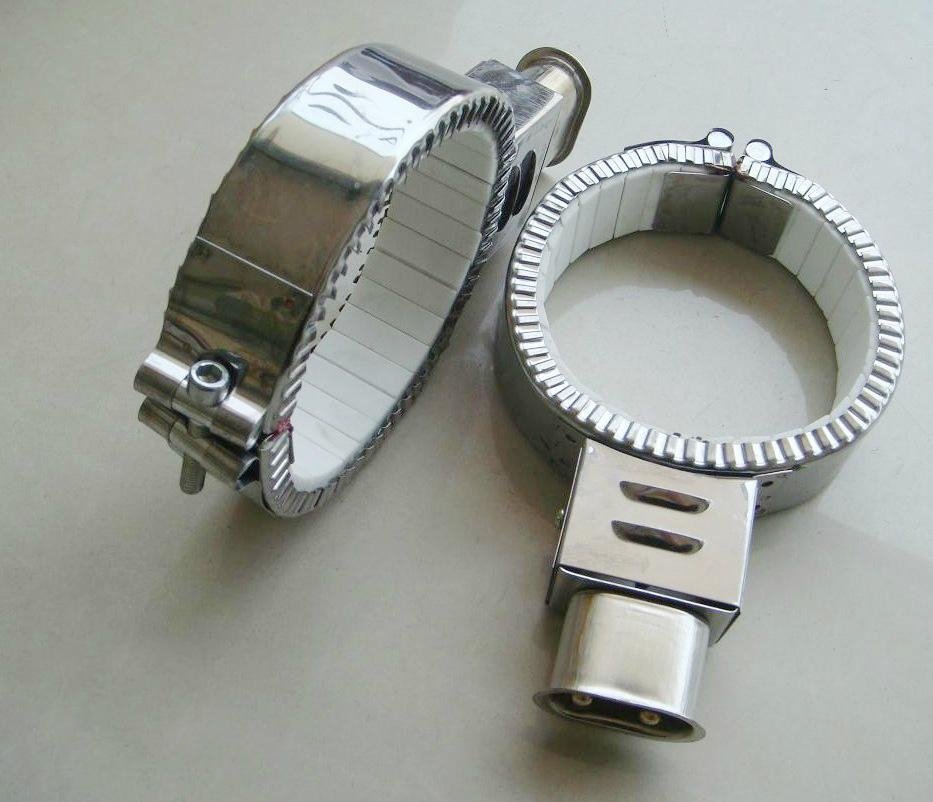
Every band heater manufacturer is constantly pushing the boundaries of design and technology to create even more efficient and effective heating solutions for industrial applications. These unsung heroes play a crucial role in various industries, ensuring optimal temperatures for processes like pipe heating, tank heating, and mold temperature control. But what exciting advancements are on the horizon? Let’s explore 3 innovative trends shaping the future of band heaters: Self-Regulating Band Heaters: Traditional band heaters rely on external controls to maintain a set temperature. However, self-regulating band heaters are a game-changer, offering automatic temperature control for a more streamlined and efficient heating process. Here’s how they work: PTC (Positive Temperature Coefficient) Material: The key lies in the use of a special PTC material within the band heater element. This material exhibits unique electrical properties. As the temperature rises, the electrical resistance of the PTC material also increases. Automatic Temperature Control: As the band heater heats up, the increasing resistance automatically reduces the current flow. This self-regulating mechanism prevents overheating and maintains a consistent temperature without the need for external controls. Benefits of Self-Regulating Band Heaters: Simplified Operation: Eliminates the need for complex temperature controllers, simplifying installation and maintenance. Energy Efficiency: Reduces energy consumption by automatically adjusting power output based on temperature needs. Improved Safety: Minimizes the risk of overheating, promoting safer operation in various industrial settings. High-Performance Materials for Extreme Applications: Band heater manufacturers are developing innovative materials that can withstand extreme temperatures and harsh environments. This opens doors for new applications in demanding industries: Advanced Mica Insulation: Mica is a natural mineral known for its excellent heat resistance and electrical insulating properties. New advancements in mica processing have led to even higher-performing mica insulation, allowing band heaters to operate at even higher temperatures. Specialized Alloys for Corrosion Resistance: In highly corrosive environments, traditional band heater materials can degrade. Manufacturers are developing new alloys that resist corrosion, ensuring long-lasting performance in applications like chemical processing or marine environments. Flexible and Expandable Heating Elements: Certain applications require heating elements that can conform to irregular shapes or expand and contract with temperature fluctuations. New materials like silicone rubber or high-temperature fabrics offer increased flexibility and expandability, making band heaters more versatile. Smart Band Heaters with Integrated Monitoring and Control: The future of band heaters lies in connectivity and intelligent control. Imagine band heaters that can not only heat objects but also monitor performance and communicate data: Embedded Sensors: Band heaters with integrated temperature sensors can provide real-time feedback on heating performance, allowing for precise control and process optimization. Wireless Connectivity: Imagine band heaters that connect to a wireless network, enabling remote monitoring and control. This allows for adjustments to be made from anywhere, improving process efficiency and reducing downtime. Predictive Maintenance: Smart band heaters can analyze data and predict potential failures before they occur. This proactive approach to maintenance can save companies time and money by preventing costly breakdowns. Last Word These innovative trends from leading band heater manufacturers offer a glimpse into the future of industrial heating. Self-regulating band heaters promise simplified operation and energy savings. As these advancements continue, band heaters will play an even more critical role in ensuring optimal temperatures and efficient processes across various industries.
Top 3 Electric Tubular Heaters for Efficient Heating
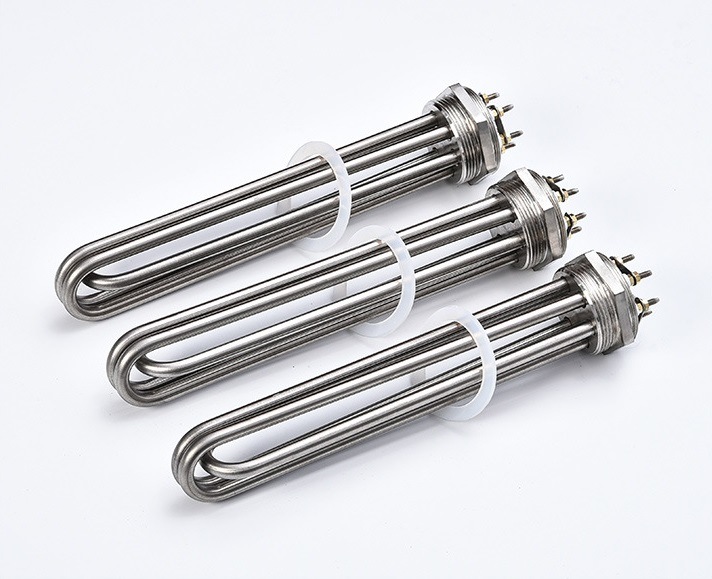
Feeling a chill in the air? As the seasons change, staying warm and comfortable indoors becomes a priority. But cranking up the central heating can be expensive and inefficient. Enter the electric tubular heater, a versatile and energy-saving solution for keeping specific areas toasty. These compact and powerful heaters use electricity to generate warmth, offering a targeted heating option for rooms or spaces that might get neglected by your central heating system. This blog explores the top 3 electric tubular heaters for efficient heating, ensuring you find the perfect fit for your needs: Finned Tubular Heaters: These are the workhorses of the electric tubular heater world, offering exceptional efficiency and versatility. How it Works: Finned tubular heaters feature a metal tube containing a heating element. Fins are attached to the tube, increasing the surface area and maximizing heat radiation into the surrounding air. Benefits: Efficient Heat Transfer: Fins provide a large surface area for efficient heat transfer, warming the room quickly and evenly. Durable Construction: The metal casing and fins ensure long-lasting performance. Versatility: Finned tubular heaters come in various sizes, wattages, and configurations, making them suitable for a wide range of applications. Applications: Finned tubular heaters are ideal for: Workshops and Garages: Provide warmth for working on projects during colder months. Basements and Attics: Combat the chill in these often-neglected spaces. Sunrooms and Patios: Extend the use of these areas during cooler seasons. Immersion Tubular Heaters: Perfect for liquids and gases, immersion tubular heaters provide targeted heating within tanks, pipes, or vessels. How it Works: Immersion tubular heaters are submerged directly into the liquid or gas you want to heat. The heating element transfers heat directly to the surrounding medium, ensuring efficient and fast heating. Benefits: Precise Heating: Immersion heaters provide targeted heating within the liquid or gas, minimizing heat loss to the surrounding environment. Fast Heating: The direct contact with the medium allows for rapid temperature increase. Durable Construction: Immersion heaters are built with materials resistant to corrosion and high temperatures. Applications: Immersion tubular heaters are commonly used for: Aquariums and Ponds: Maintain a consistent and comfortable temperature for your fish. Pool and Spa Heating: Provide supplemental or primary heating for pools and spas. Chemical Processing: Heat liquids and gases for various industrial applications. Infrared Tubular Heaters: These innovative heaters use infrared radiation to deliver a gentle, radiant warmth that penetrates objects directly. How it Works: Infrared tubular heaters generate invisible infrared waves that heat objects they come into contact with, including people and furniture. This differs from traditional heaters that warm the air itself. Benefits: Targeted Heating: Infrared heaters provide warmth directly to people and objects within their range, creating a comfortable and localized heating zone. Energy-Efficient: Infrared heaters don’t waste energy heating the air, making them a more efficient option for spot heating. Quiet Operation: Infrared heaters operate silently, making them ideal for bedrooms or quiet spaces. Applications: Infrared tubular heaters are well-suited for: Outdoor Patios and Decks: Enjoy comfortable warmth even on chilly evenings outdoors. Spot Heating in Workshops or Garages: Provide warmth to specific work areas without heating the entire space. Animal Husbandry: Maintain comfortable temperatures for livestock or pets in barns or sheds.
5 Benefits of Using Tubular Heaters with Thermostats
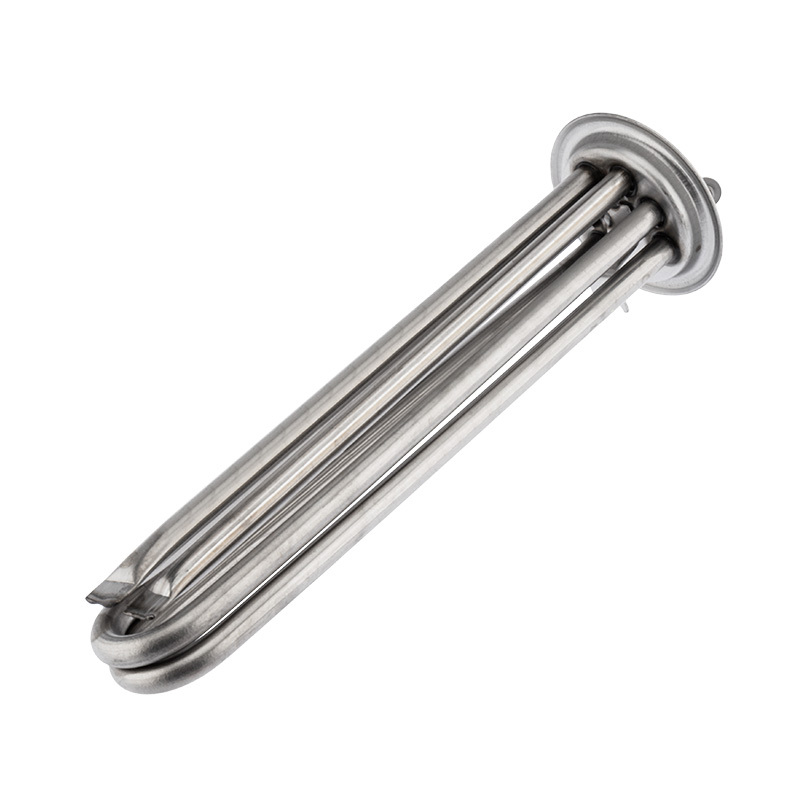
Ever wondered how your toaster gets hot enough to brown your bread perfectly, or how a space heater keeps you warm on a chilly day? The answer lies in a hidden hero: the tubular heater with thermostat. These unsung champions are versatile heating elements found in countless everyday appliances and industrial processes. But what exactly are they, and why are they so beneficial? Tubular heaters with thermostats combine the efficient heating power of tubular heaters with the precise control of a thermostat. Let’s break down the magic behind them: Tubular Heaters: Imagine a long, thin tube filled with a special resistance wire. When electricity flows through the wire, it heats up, transferring that heat to the surrounding environment. This is the basic principle behind a tubular heater. They come in various sizes, wattages, and sheath materials to suit different applications. Thermostats: A thermostat acts like a watchful guard, constantly monitoring the temperature. Once the desired temperature is reached, the thermostat automatically switches off the power supply to the tubular heater. When the temperature drops below the set point, the thermostat kicks back in, turning the heater on and maintaining a consistent temperature. Now that we understand the basic components, let’s explore the 5 key benefits of using tubular heaters with thermostats: Precise Temperature Control: The biggest advantage of this duo is their ability to maintain a precise and consistent temperature. The thermostat acts like a control center, ensuring your appliance or environment reaches the desired temperature and stays there. This is crucial for various applications, from keeping food warm in a buffet to ensuring optimal drying conditions in an industrial setting. Energy Efficiency: Since the thermostat automatically regulates the heater, it only operates when needed. This prevents unnecessary energy consumption and reduces your electricity bills. Imagine your space heater constantly running at full blast, even when the room is already warm. A tubular heater with a thermostat eliminates this waste, making it an energy-saving choice. Enhanced Safety: Overheating is a potential hazard with any heating element. However, the built-in thermostat in these systems prevents this risk. When the desired temperature is reached, the thermostat shuts off the power, eliminating the possibility of overheating and potential fire hazards. This safety feature adds peace of mind, especially when using heaters in close proximity to flammable materials. Increased Lifespan: By preventing overheating, tubular heaters with thermostats extend the lifespan of the heating element. Consistent and controlled operation reduces wear and tear, allowing the heater to function optimally for a longer period. This translates to fewer replacements and maintenance costs in the long run. Versatility for Various Applications: The combination of efficient heating and precise temperature control makes tubular heaters with thermostats incredibly versatile. Here are just a few examples of their wide range of applications: Household Appliances: Toasters, coffee makers, clothes dryers, and space heaters often rely on tubular heaters with thermostats for controlled heating. Industrial Processes: These heaters are used in food processing, plastic molding, and various industrial drying applications where maintaining a specific temperature is crucial. Medical Equipment: Sterilization equipment and laboratory incubators utilize tubular heaters with thermostats for precise temperature control. Last Word From keeping your morning coffee hot to ensuring optimal drying conditions in an industrial setting, these systems offer a powerful and reliable heating solution. So, the next time you encounter a perfectly toasted bagel or experience the comforting warmth of a space heater, remember the silent hero behind it all: the tubular heater with thermostat.
Top 5 CO2 Heater Manufacturers for Industrial Needs
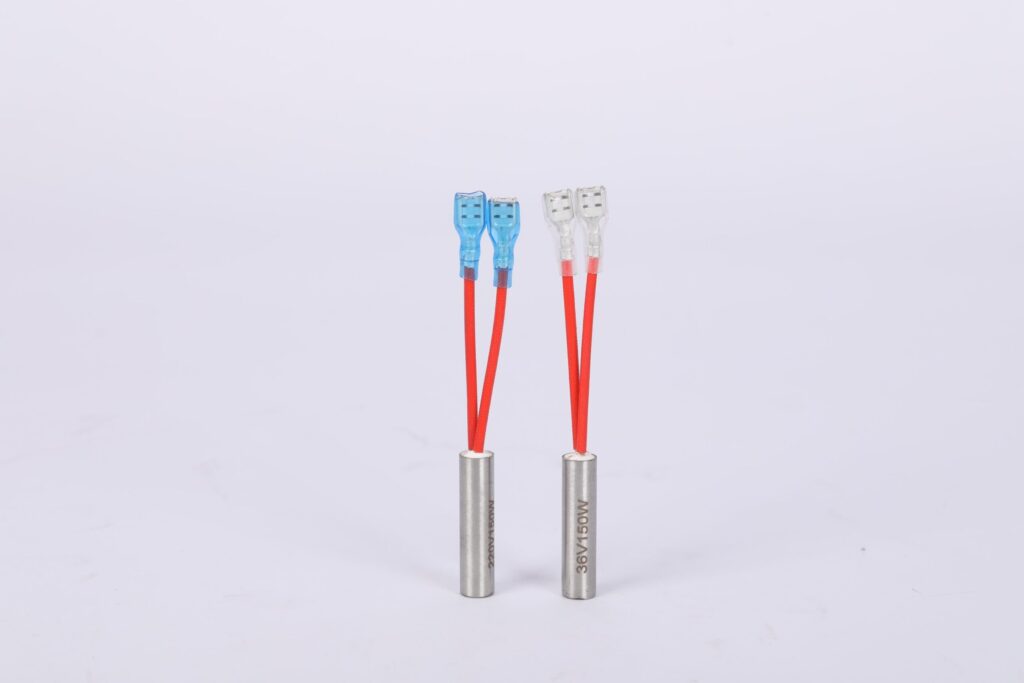
Carbon dioxide (CO2) heaters play a vital role in various industrial applications, ensuring optimal gas flow and preventing freezing or malfunction of equipment. Choosing the right CO2 heater manufacturer is crucial for businesses that rely on consistent and reliable gas pressure. This guide explores the top 5 CO2 heater manufacturers known for their quality products and commitment to industrial needs. CHERI: CHERI is a leading manufacturer of industrial gas equipment, including top-of-the-line CO2 heaters. They offer a wide range of models to suit various applications, with features like: Durable stainless steel construction for long-lasting performance in harsh industrial environments. Adjustable temperature control for precise heating and optimal gas flow. Safety features like pressure relief valves and overheat protection for safe operation. Multiple connection options for easy integration into existing gas lines. Vikane: Vikane is a global leader in fumigation and pest control solutions. They also offer a reliable line of CO2 heaters specifically designed for their fumigation systems. Vikane CO2 heaters are known for: High efficiency for fast and effective heating of CO2 gas. Compact design for easy installation in fumigation chambers. Corrosion-resistant materials to withstand harsh fumigation chemicals. User-friendly controls for easy operation and temperature adjustment. Lenco Welding Accessories Ltd.: Lenco is a trusted name in welding equipment and supplies. They offer a variety of CO2 heaters specifically designed for MIG (Metal Inert Gas) welding applications. Lenco CO2 heaters are known for: Portable and lightweight design for easy use and movement around the worksite. Fast heating times to ensure consistent gas flow and prevent welding issues. Multiple voltage options for compatibility with different power sources. Durable construction to withstand the demands of a busy welding environment. Richu Industrial: Richu Industrial is a Chinese manufacturer specializing in gas welding and cutting equipment. They offer a cost-effective line of CO2 heaters suitable for various industrial applications. Richu CO2 heaters are known for: Affordable pricing for budget-conscious businesses. Simple and user-friendly design for easy operation and maintenance. Compatibility with various gas regulators for increased versatility. Availability in different sizes to suit specific gas flow requirements. MISATU Gas Technology Group: MISATU Gas Technology Group is a Chinese manufacturer of industrial gas equipment, including CO2 heaters. They offer a range of models with features like: Automatic temperature control for consistent gas flow and reduced operator intervention. High-quality brass construction for long-lasting performance and corrosion resistance. Multiple safety features for safe and reliable operation. Compatibility with various gas flow rates for different industrial needs. Choosing the Right CO2 Heater Manufacturer: When selecting a CO2 heater manufacturer for your industrial needs, consider the following factors: Application: Choose a manufacturer that offers CO2 heaters specifically designed for your industry and application. For example, a welding supply store may carry different CO2 heaters than a fumigation company. Features: Consider the features that are important to you, such as temperature control, portability, safety features, and compatibility with your existing equipment. Price: CO2 heater prices can vary depending on the manufacturer, features, and quality. Set a budget and choose a manufacturer that offers good value for your money. Customer Service: Choose a manufacturer with a reputation for excellent customer service. This is important in case you need technical support or replacement parts. Wrap Up Investing in a high-quality CO2 heater from a reputable manufacturer is essential for ensuring efficient and reliable gas flow in your industrial applications. The manufacturers listed above are a great starting point for your research. By considering your specific needs and these helpful tips, you can find the perfect CO2 heater to keep your operations running smoothly.
3 Key Features of a Cartridge Heater with Thermocouple
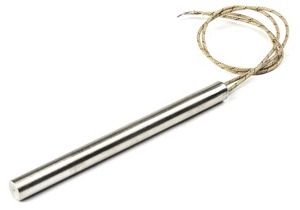
Imagine needing to precisely heat a metal block in a machine. A regular heating element might work, but how do you know you’ve reached the exact temperature? Enter the cartridge heater with thermocouple, a dynamic duo in the world of industrial heating. This power couple combines a heating element with a built-in temperature sensor, offering precise temperature control for various industrial applications. This guide explores the 3 key features of cartridge heaters with thermocouples and explains why they’re a game-changer for precise heating needs: Accurate Temperature Control with Thermocouples: Thermocouple Basics: A thermocouple is a tiny sensor made of two dissimilar metals joined at one end. When this junction heats up, a tiny voltage is produced. The higher the temperature, the greater the voltage. Precise Temperature Monitoring: The cartridge heater with thermocouple positions the thermocouple right next to the heating element. As the heater warms up, the thermocouple continuously measures the temperature and sends the signal to a temperature controller. Temperature Controller Takes Charge: The temperature controller receives the signal from the thermocouple. It compares this reading to the desired temperature setting and adjusts the power going to the heater element accordingly. This creates a feedback loop, ensuring the heater maintains the exact temperature needed. Compact and Versatile Design: Cylindrical Shape: Cartridge heaters are typically cylindrical, allowing them to be inserted directly into drilled holes in metal components. This ensures efficient heat transfer directly to the object being heated. Variety of Sizes and Wattages: Cartridge heaters with thermocouples come in various diameters and lengths to fit different applications. They also offer a wide range of wattages to meet the specific heating requirements of your project. Durable Construction: Made from high-temperature resistant materials like stainless steel, these heaters can withstand harsh industrial environments. Benefits of Compact Design: Easy Installation: The compact size and cylindrical shape make cartridge heaters with thermocouples simple to install in various equipment. They require minimal space and can be easily integrated into existing machinery. Efficient Heat Transfer: Direct insertion into the object being heated minimizes heat loss and ensures efficient energy transfer. This leads to faster heating times and improved process efficiency. Wide Range of Applications: Their versatility makes them suitable for various industrial applications, including: Plastic welding 3D printing Food processing equipment Packaging machinery Laboratory equipment Long Service Life and Reliability: High-Quality Materials: Manufactured with robust materials and robust construction techniques, cartridge heaters with thermocouples are built to last. They can withstand high temperatures and demanding industrial environments. Reduced Maintenance Needs: The built-in thermocouple continuously monitors the temperature, preventing overheating and extending the lifespan of the heater element. This translates to less downtime for maintenance and repairs. Reliable Performance: Precise temperature control and robust construction ensure reliable performance over an extended period. This translates to consistent results and fewer unexpected disruptions in your operation. Wrap Up A cartridge heater with thermocouple offers precise temperature control, a compact design, and a long service life. They are a valuable asset for various industrial applications requiring accurate and reliable heating. By understanding these key features, you can make informed decisions when choosing the right heating solution for your specific needs.
How Cartridge Heaters Can Optimize Your Manufacturing Process
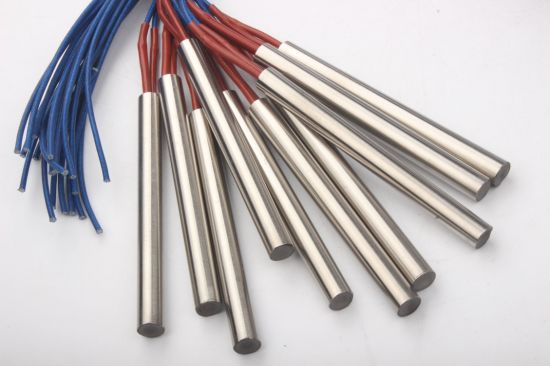
Imagine a world where heating elements are precise, efficient, and adaptable to various manufacturing needs. This isn’t science fiction! A cartridge heater manufacturer offers a solution: compact, versatile heating elements called cartridge heaters. These powerful tools can significantly optimize your manufacturing process by delivering precise and controlled heat exactly where it’s needed. In this guide, we’ll explore how cartridge heaters can revolutionize your production line, boosting efficiency, improving product quality, and reducing costs. What are Cartridge Heaters? Cartridge heaters are cylindrical-shaped heating elements designed for direct insertion into machinery or equipment. They consist of a metal sheath containing a high-resistance wire coil and insulating magnesium oxide. When electricity passes through the coil, it generates heat that transfers directly to the surrounding object. Benefits of Using Cartridge Heaters in Manufacturing: Precise Heat Control: Cartridge heaters offer exceptional temperature control due to their close contact with the target object. This ensures consistent and even heating, crucial for many manufacturing processes. Fast Heating and Cooling: The compact design of cartridge heaters allows for rapid heating and cooling cycles. This minimizes downtime between cycles and improves overall production efficiency. High-Watt Densities: Cartridge heaters pack a punch! They can generate high heat outputs despite their small size, making them ideal for various applications requiring concentrated heat. Durability and Versatility: Cartridge heaters are built to withstand harsh industrial environments. They come in various sheath materials, diameters, and lengths to meet diverse manufacturing needs. Long Service Life: The robust design and high-quality materials ensure a long lifespan for cartridge heaters, minimizing replacement costs and downtime. Easy Installation and Maintenance: Cartridge heaters are simple to install and require minimal maintenance. This reduces production setup time and ongoing maintenance costs. Applications of Cartridge Heaters in Manufacturing: Cartridge heaters have a wide range of applications across various manufacturing industries. Here are some examples: Plastic Processing: Used for melting and molding plastics in processes like injection molding, thermoforming, and heat sealing. Food and Beverage Industry: Heating food processing equipment, sterilizing containers, and maintaining specific temperatures during food production. Packaging Industry: Sealing packages, activating adhesives, and maintaining consistent temperatures for heat-shrink wrapping. Textile Manufacturing: Drying fabrics, activating dyes, and heat-setting textiles for wrinkle resistance. Electronics Manufacturing: Soldering components, curing adhesives, and maintaining precise temperatures for delicate electronic components. Medical Device Manufacturing: Sterilizing equipment, heating components during assembly, and maintaining specific temperatures for medical device production. Choosing the Right Cartridge Heater Manufacturer: With so many cartridge heater manufacturers on the market, selecting the right partner is crucial. Here are some factors to consider: Experience and Expertise: Choose a manufacturer with a proven track record and extensive experience in your specific industry. Product Quality and Certifications: Look for a manufacturer that prioritizes quality materials and adheres to relevant industry standards and certifications. Customizability Options: Many manufacturers offer custom cartridge heaters to meet your specific needs. Choose one that can accommodate your unique requirements. Customer Service and Support: Reliable customer service and technical support are essential for troubleshooting and ensuring smooth operation. Optimizing Your Manufacturing Process with Cartridge Heaters By incorporating cartridge heaters into your manufacturing process, you can achieve significant benefits: Improved Product Quality: Precise heat control ensures consistent product quality, reducing rejects and rework. Enhanced Production Efficiency: Faster heating and cooling cycles minimize downtime and increase production output. Reduced Energy Consumption: The efficient design of cartridge heaters minimizes energy waste, lowering your operating costs. Minimized Downtime: Durable construction and easy maintenance reduce equipment failures and downtime. Wrap Up Cartridge heaters are a powerful tool for any manufacturer seeking to optimize their production process. Their versatility, efficiency, and precise heat control can significantly improve product quality, boost production output, and ultimately, contribute to your business success. So, consider partnering with a reputable cartridge heater manufacturer and explore how these innovative heating elements can revolutionize your manufacturing line!