5 Applications of Finned Tubular Heater in Industries
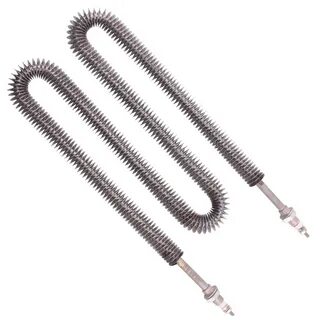
A finned tubular heater always stands out as a powerful and efficient solution in industrial applications. This unique heating device has gained popularity across various sectors due to its versatility and effectiveness. From food processing to aerospace, the Finned Tubular Heater is making waves in how industries approach their heating needs. 1. Food Processing: Maintaining Optimal Temperatures The food industry relies heavily on precise temperature control to ensure product quality and safety. Finned Tubular Heaters play a crucial role in this sector. Uniform heating: The fins on these heaters help spread heat evenly, preventing hot spots that could spoil food. Quick temperature adjustments: Rapid heating and cooling capabilities allow for swift changes in production lines. Sanitary design: The smooth surface of these heaters makes them easy to clean, meeting strict hygiene standards. These heaters are also used in: Chocolate tempering machines Industrial fryers Food packaging equipment The ability to maintain steady temperatures within 1°C has made Finned Tubular Heaters a go-to choice for food processors aiming for top-notch quality. 2. Aerospace: Defrosting and De-icing The aerospace industry faces unique challenges when it comes to heating, especially in harsh weather conditions. Finned Tubular Heaters have found an important place in this field. Aircraft de-icing: These heaters are used in ground equipment to quickly melt ice on aircraft surfaces. Runway heating: Embedded in runway surfaces, they prevent ice formation and ensure safe takeoffs and landings. Sensor protection: Critical sensors on aircraft are kept ice-free using these efficient heaters. The heaters’ ability to operate in extreme cold, sometimes as low as -40°C, makes them ideal for aerospace applications. Their durability in harsh conditions has led to a 50% increase in their use in airport ground equipment over the past five years. 3. Plastic Manufacturing: Precision Molding The plastic industry relies on exact temperature control for molding and extrusion processes. Finned Tubular Heaters excel in this area. Even heat distribution: The finned design ensures uniform heating across molds, preventing defects. Energy efficiency: These heaters transfer heat more effectively, reducing power consumption. Compact size: Their slim profile allows for installation in tight spaces within molding machines. These heaters are also used in: Plastic extrusion lines Blow molding machines Thermoforming equipment The precision offered by Finned Tubular Heaters has led to a 25% increase in their adoption in the plastic industry over the past three years. 4. HVAC Systems: Efficient Air Heating Heating, Ventilation, and Air Conditioning (HVAC) systems benefit greatly from the use of Finned Tubular Heaters. Compact design: These heaters fit easily into ductwork, saving space in HVAC installations. Quick response: They heat up rapidly, allowing for fast temperature adjustments in buildings. Low maintenance: Their simple design means fewer parts that can break down or need replacing. These heaters are also used in: Industrial dryers Air curtains Heat recovery systems The efficiency of Finned Tubular Heaters has led to a 40% increase in their use in commercial HVAC systems since 2020. 5. Chemical Processing: Maintaining Reaction Temperatures In the chemical industry, maintaining precise temperatures is crucial for successful reactions and product quality. Corrosion resistance: Many Finned Tubular Heaters are made with materials that resist chemical corrosion. Explosion-proof options: Special models are available for use in hazardous environments. Fine temperature control: These heaters can maintain temperatures within 0.5°C, crucial for sensitive chemical processes. These heaters are also used in: Distillation columns Storage tank heating Pipeline pre-heating The reliability of Finned Tubular Heaters in maintaining exact temperatures has led to a 35% increase in their adoption in the chemical processing industry over the past four years. Final Words Finned Tubular Heaters have proven their worth across various industries. Their versatility, efficiency, and precision make them an excellent choice for many heating applications. As technology advances, we can expect to see even more innovative uses for these powerful heating devices. From food processing to chemical reactions, Finned Tubular Heaters are helping industries improve their processes, reduce costs, and enhance product quality.
5 Reasons Why You Need a Mold Cartridge Heater Manufacturer for Manufacturing Needs

Mold cartridge heater manufacturers are essential partners in optimizing manufacturing processes. These specialists design, produce, and supply heaters tailored to specific industrial needs, ensuring precise temperature control and efficient heat transfer. Whether you’re in the plastics, rubber, or food industry, collaborating with a reliable mold cartridge heater manufacturer is crucial for achieving production excellence. Reason 1: Consistent and Precise Temperature Control Maintaining consistent and precise temperature control is paramount in manufacturing. Mold cartridge heaters excel in this area, offering several advantages: Uniform Heat Distribution: Cartridge heaters are designed to distribute heat evenly across the mold cavity, preventing hot or cold spots. This uniformity is essential for producing products with consistent dimensions and quality. Rapid Heat-Up and Cool-Down Times: These heaters quickly reach the desired temperature, reducing cycle times and increasing production efficiency. Similarly, they cool down rapidly, allowing for faster mold turnover. Accurate Temperature Regulation: With advanced temperature controllers, mold cartridge heaters can maintain precise temperature settings, ensuring product consistency and minimizing defects. Reason 2: Enhanced Product Quality High-quality products are the cornerstone of business success. Mold cartridge heaters contribute significantly to product quality by: Preventing Defects: Consistent temperature control reduces the risk of defects such as warping, shrinkage, and burns. This leads to a higher percentage of acceptable products and less waste. Improving Product Performance: Precise temperature management can enhance product performance characteristics, such as strength, durability, and flexibility. Meeting Industry Standards: Many industries have stringent quality standards. Mold cartridge heaters help manufacturers meet these requirements by ensuring product consistency and reliability. Reason 3: Increased Production Efficiency Efficiency is key to maximizing profits in manufacturing. Mold cartridge heaters boost production efficiency through: Reduced Cycle Times: Faster heat-up and cool-down times translate to shorter cycle times, allowing for more production runs within a given period. Optimized Energy Consumption: Efficient heat transfer minimizes energy waste, leading to lower operating costs. Improved Equipment Uptime: Reliable mold cartridge heaters reduce downtime caused by equipment failures, maintaining production continuity. Reason 4: Versatility and Adaptability Mold cartridge heaters are incredibly versatile and can be adapted to various manufacturing processes and equipment: Wide Range of Sizes and Wattages: Cartridge heaters are available in various sizes and wattages to suit different mold cavities and heating requirements. Customizable Designs: Manufacturers can often customize cartridge heaters to meet specific application needs, ensuring optimal performance. Easy Installation and Replacement: These heaters are relatively simple to install and replace, minimizing downtime and maintenance costs. Reason 5: Long Lifespan and Durability Investing in high-quality equipment is essential for long-term profitability. Mold cartridge heaters offer: Durable Construction: Constructed from robust materials, cartridge heaters can withstand harsh manufacturing environments and temperature fluctuations. Extended Lifespan: With proper care and maintenance, mold cartridge heaters can have a long lifespan, reducing replacement costs. Cost-Effective Solution: While the initial investment might be higher, the long-term benefits in terms of efficiency, product quality, and reduced downtime make mold cartridge heaters a cost-effective choice. Last Word Mold cartridge heater manufacturers are invaluable partners in achieving manufacturing excellence. By providing custom-designed, high-performance heaters, these experts help businesses optimize production processes, enhance product quality, and improve overall efficiency. If you’re looking to elevate your manufacturing operations, collaborating with a reputable mold cartridge heater manufacturer will be your best decision.