What is the Purpose of a Tubular Heater?
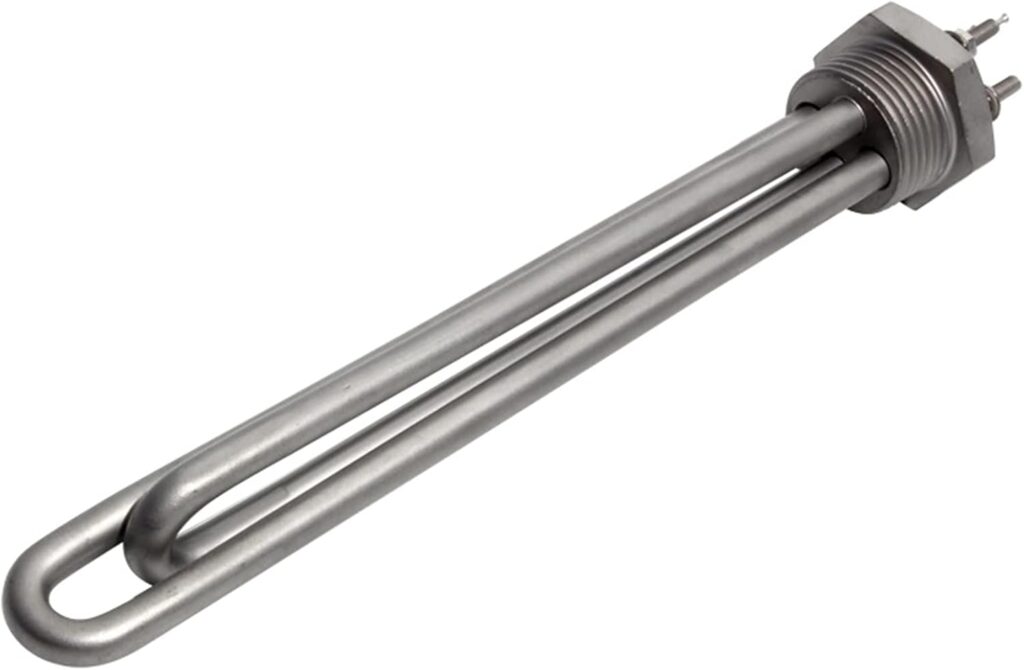
A tubular heater with thermostat is an essential component in various heating applications. Whether you’re dealing with industrial machinery or home appliances, understanding the role of this heating element can significantly enhance the efficiency of your operations. The tubular heater with thermostat provides controlled heat, ensuring that your equipment operates at optimal temperatures without the risk of overheating. How Does a Tube Heater Work? A tube heater operates by converting electrical energy into heat. This heat is then distributed evenly across the surface of the tube, making it ideal for applications that require consistent and reliable heat. Construction: Tube heaters are typically made of a metal sheath, such as stainless steel, which houses the heating element. The element inside is usually a coil of resistance wire, similar to that found in cartridge heaters. Thermostat Integration: The addition of a thermostat allows for precise temperature control. This prevents overheating, which can damage both the heater and the material being heated. Heat Distribution: The design of the tube allows for even heat distribution, making it suitable for applications where uniform heating is crucial. Applications of Tube Heaters Tube heaters are incredibly versatile and can be found in a wide range of applications. Here’s where they shine: Industrial Heating: Tube heaters are commonly used in industrial processes, such as drying, curing, and melting, where precise and reliable heat is required. HVAC Systems: In heating, ventilation, and air conditioning systems, tube heaters help maintain consistent temperatures, ensuring comfort and efficiency. Food Processing: Tube heaters play a critical role in food processing by providing controlled heat for cooking, baking, and maintaining the right temperature for food safety. Greenhouse Heating: Tube heaters are also used in greenhouses to provide consistent warmth, promoting healthy plant growth even in colder climates. Benefits of Using a Tube Heater with Thermostat Choosing a tubular heater with thermostat offers several advantages: Energy Efficiency: The thermostat allows the heater to maintain the desired temperature without consuming excess energy. This leads to lower energy costs and a more sustainable operation. Safety: The built-in thermostat prevents the heater from overheating, reducing the risk of fire or damage to the equipment. Longevity: By preventing overheating, the thermostat also extends the life of the heater, reducing the need for frequent replacements. Versatility: Tube heaters with thermostats can be used in a variety of applications, from industrial processes to residential heating, making them a versatile choice for different heating needs. Final Words The tubular heater with thermostat is a vital tool in various industries, providing controlled and consistent heat where it’s needed most. Understanding its purpose and benefits can help you make informed decisions about its use in your operations. With proper maintenance and the right choice of heater, you can ensure efficient and safe heating for years to come.
What is the Application of a Band Heater?
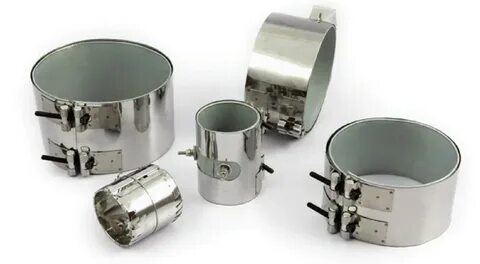
When working with machinery and industrial equipment, maintaining the right temperature is crucial for smooth operation. This is where a band heater plays a vital role. Designed to heat cylindrical surfaces, band heaters are indispensable in many industrial processes. If you are looking for reliable heating solutions, working with a trusted band heater manufacturer ensures you get the right equipment for your needs. Common Applications of Band Heaters Band heaters are versatile and find use in a variety of industries. Below are some of the most common applications: Plastic Injection Molding: In plastic molding, band heaters are used to maintain the correct temperature of the molds. This ensures that the plastic material flows smoothly and sets properly, resulting in high-quality finished products. Extrusion Processes: Band heaters are essential in extrusion processes, where materials like plastic or rubber are pushed through a mold to create products like pipes, sheets, or films. Maintaining the right temperature is crucial for ensuring the material’s consistency and preventing defects. Food and Beverage Industry: Band heaters help maintain the right temperature for food processing equipment, ensuring that products are cooked evenly and safely. They are also used in machinery like coffee urns and food warmers. Chemical and Pharmaceutical Industry: Band heaters are used to heat tanks and vessels, ensuring that chemicals and pharmaceuticals are processed at the correct temperatures. This is essential for reactions and formulations that require precise thermal conditions. Printing Industry: In the printing industry, band heaters help maintain the temperature of ink and rollers, ensuring that the printing process is smooth and the quality of the print is high. How to Choose the Right Band Heater Manufacturer Selecting the right band heater manufacturer is essential for ensuring that you get a product that meets your specific needs. Here are some factors to consider: Customization: A good manufacturer will offer custom options, allowing you to choose the right size, wattage, and sheath material for your application. Quality Control: Reliable manufacturers adhere to strict quality control standards, ensuring that every band heater is built to last and performs reliably. Technical Support: A manufacturer that offers technical support can help you select the right heater and troubleshoot any issues that may arise during installation or operation. Energy Efficiency: Look for manufacturers that design band heaters with energy efficiency in mind, as this can lead to cost savings and reduced environmental impact. Wrap Up Understanding what the application of a band heater is, and how it functions, is essential for anyone involved in industries that rely on precise temperature control. From plastic molding to food processing, band heaters play a critical role in ensuring that industrial processes run smoothly and efficiently. Working with a reputable band heater manufacturer like Cheri ensures that you get a reliable product tailored to your specific needs, backed by quality assurance and technical support. By following proper maintenance practices, you can extend the life of your band heater and keep your operations running at peak efficiency.
Where is a Thermocouple Used?
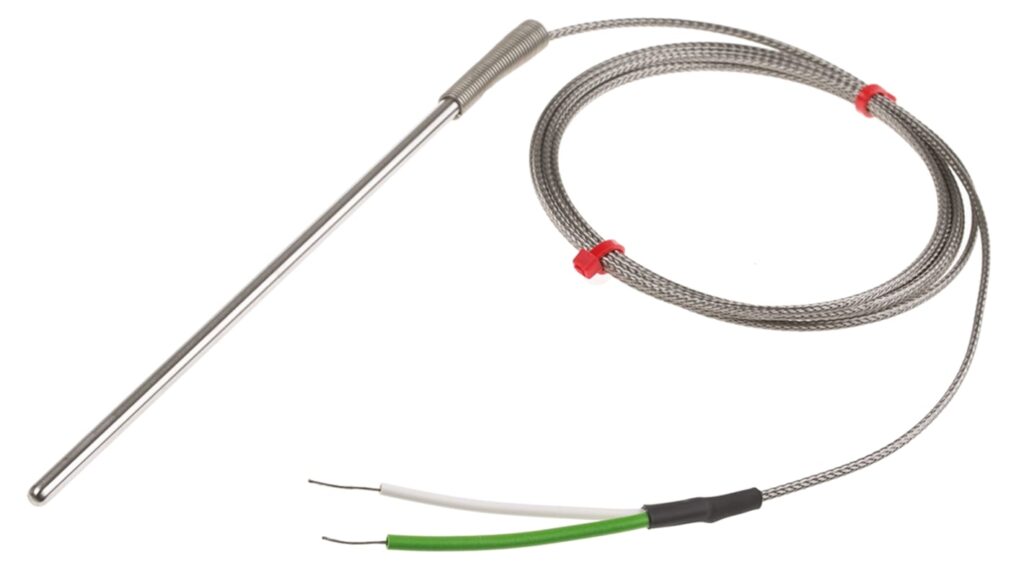
When considering the various devices that measure temperature, the thermocouple stands out for its versatility and reliability. Whether you are familiar with the work of a thermocouple manufacturer or just beginning to explore this field, understanding where thermocouples are used can provide valuable insight. Thermocouples are essential in many industries due to their ability to accurately measure extreme temperatures. How Does a Thermocouple Work? A thermocouple consists of two different metals joined at one end. When these metals experience a temperature difference, they generate a small electrical voltage. This voltage is then interpreted to measure the temperature. The simplicity of this design allows thermocouples to be both durable and responsive, making them suitable for various applications. Durability: Thermocouples are built to withstand harsh environments, from extreme heat to corrosive conditions. Versatility: They can measure temperatures ranging from very low to extremely high, depending on the metals used. Quick Response: The small size and direct contact of thermocouples allow them to respond quickly to temperature changes. Applications of Thermocouples in Different Industries Thermocouples are used across a wide range of industries, each with unique requirements and challenges. 1. Industrial Manufacturing In manufacturing, controlling temperature is critical for ensuring product quality. Thermocouples are used in: Furnaces and Kilns: To monitor and control the high temperatures required for metalworking and ceramics. Plastic Extrusion: Where precise temperature control is needed to shape and form plastic materials. Heat Treatment: To ensure that metals are heated to the correct temperature for processes like hardening or annealing. 2. Aerospace Industry In the aerospace sector, the ability to measure temperature accurately is crucial for safety and performance: Engines: Thermocouples monitor the temperatures in jet engines, ensuring they operate within safe limits. Exhaust Systems: They measure the temperature of exhaust gases to assess engine performance and emissions. Spacecraft: Thermocouples are used in spacecraft to monitor critical systems, ensuring they function correctly in the extreme conditions of space. 3. Medical Field Thermocouples also play a vital role in medical equipment, where precise temperature measurement is often a matter of life and death: Sterilization Equipment: They monitor the high temperatures needed to sterilize medical instruments. Incubators: Thermocouples ensure that the temperature inside infant incubators remains stable and safe. Cryotherapy: They are used in cryotherapy chambers to monitor the extremely low temperatures required for treatment. Why Should I Choose a Thermocouple Manufacturer? Choosing the right thermocouple manufacturer can make a significant difference in the performance and reliability of the thermocouples you use. Here’s why: Customization: A good manufacturer can provide thermocouples tailored to your specific needs, whether that means different metal combinations or special sheathing materials. Quality Control: Reputable manufacturers have strict quality control processes to ensure that each thermocouple meets industry standards. Technical Support: Expert manufacturers offer support to help you select the right type of thermocouple for your application and assist with any issues that arise during use. Types of Thermocouples and Their Specific Uses Different types of thermocouples are designed for specific applications, depending on the materials used: Type K (Nickel-Chromium / Nickel-Alumel): Commonly used in general-purpose applications due to its wide temperature range and affordability. Type J (Iron / Constantan): Often used in older equipment, it’s suitable for lower temperature applications. Type T (Copper / Constantan): Best for low-temperature measurements, such as in cryogenics. Type S (Platinum Rhodium / Platinum): Used in high-temperature applications, like in the aerospace industry and laboratory settings. Maintenance and Care for Thermocouples To ensure your thermocouples function correctly and last as long as possible, regular maintenance is essential: Regular Inspections: Check thermocouples for signs of wear, corrosion, or damage. Calibration: Regularly calibrate thermocouples to ensure accuracy, especially in critical applications. Proper Installation: Ensure thermocouples are installed correctly, with secure connections and appropriate protective sheathing. Wrap Up Understanding where a thermocouple is used offers insight into the importance of this simple yet essential device in various industries. From manufacturing to aerospace and medical applications, thermocouples provide the precise temperature measurements necessary for safe and efficient operations. Partnering with a reliable thermocouple manufacturer ensures that you receive high-quality, customized solutions tailored to your specific needs. With proper care and maintenance, thermocouples can provide accurate temperature readings for many years, making them an invaluable tool in countless applications.
What is a Cartridge Heater?
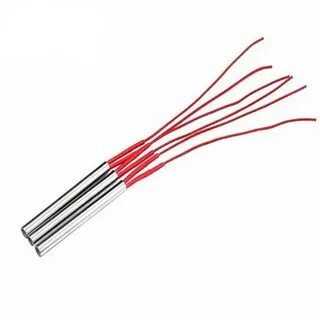
A cartridge heater is an essential tool in various industries, known for its ability to deliver precise, localized heat. Whether you’re involved in manufacturing or exploring options for heating solutions, understanding the importance of choosing a reliable Cartridge Heater Manufacturer is crucial. Cartridge heaters are not just simple devices; they are carefully engineered to provide efficient heating for specific applications. How Do Cartridge Heaters Work? Cartridge heaters are designed to transfer heat effectively to their surroundings, making them ideal for heating metal parts or molds. Here’s a closer look at how they function: Construction: The core of a cartridge heater is a resistance wire made of nickel-chromium, which converts electrical energy into heat. This wire is tightly wound around a ceramic core and encased in a metal sheath, usually made of stainless steel. The sheath protects the heater and ensures even heat distribution. Insulation: The resistance wire is insulated with magnesium oxide, which not only serves as an electrical insulator but also enhances thermal conductivity. This allows the heat generated by the wire to transfer efficiently to the sheath and subsequently to the surrounding material. Design: Cartridge heaters are designed to fit snugly into drilled holes, ensuring close contact with the material being heated. This design maximizes heat transfer and minimizes energy loss. Types of Cartridge Heaters Understanding the different types of cartridge heaters can help in selecting the right one for your needs: High-Density Cartridge Heaters: These heaters offer a high watt density, making them suitable for applications that require rapid heating and high temperatures. Low-Density Cartridge Heaters: Used in applications where lower temperatures are sufficient, these heaters are ideal for sensitive materials. Split-Sheath Cartridge Heaters: Designed to expand when heated, these heaters ensure better contact with the surrounding material, improving heat transfer efficiency. Why Choose a Reputable Cartridge Heater Manufacturer? Selecting a trustworthy Cartridge Heater Manufacturer like Cheri is critical for ensuring the quality and performance of your heaters. Here’s why: Customization: A good manufacturer can provide customized solutions tailored to your specific needs, whether you require a particular size, wattage, or material. Quality Control: Reputable manufacturers adhere to strict quality control standards, ensuring that each heater is reliable and long-lasting. Technical Expertise: With the right manufacturer, you gain access to expert advice and support, helping you choose the best heater for your application and troubleshoot any issues. Durability: High-quality materials and construction techniques result in heaters that can withstand harsh conditions and last longer, reducing the need for frequent replacements. Maintenance Tips for Cartridge Heaters Proper maintenance can extend the life of your cartridge heaters and ensure they perform optimally: Regular Checks: Inspect heaters regularly for signs of wear, such as discoloration or damaged wires. Correct Installation: Ensure that the heater is installed snugly in the drilled hole to optimize heat transfer and prevent damage. Temperature Control: Use temperature controllers to prevent overheating, which can damage both the heater and the material it’s heating. Clean Environment: Keep the heater and its surroundings clean to prevent contamination that could affect performance. Wrap Up Understanding what a cartridge heater is and how it functions is essential for anyone involved in industries that require precise heating solutions. By selecting a reliable Cartridge Heater Manufacturer, you can ensure that your operations run smoothly and efficiently. With the right maintenance practices, your cartridge heaters can provide consistent performance, helping you achieve the desired results in your applications.