Cartridge Heater: 10 Tips for Efficient Use
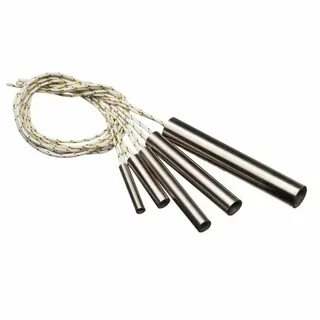
Today, every cartridge heater manufacturer produces these industrial workhorses to provide precise heat in various applications. But even the best cartridge heater needs proper care and attention to deliver optimal performance and longevity. Let’s delve into ten essential tips to maximize the efficiency and lifespan of your cartridge heaters. Tip 1: Understand Your Cartridge Heater Before diving into operation, grasp the fundamentals of your cartridge heater. This includes its wattage, voltage, length, diameter, and sheath material. Wattage and voltage: Ensure correct power supply for optimal performance and safety. Dimensions: Accurate measurements prevent installation issues and heat transfer problems. Sheath material: Choose the right material based on the application environment. Tip 2: Proper Installation Incorrect installation can lead to premature failure and safety hazards. Follow manufacturer guidelines meticulously. Secure mounting: Use suitable clamps or brackets to prevent movement. Thermal conductivity: Ensure good thermal contact between the heater and the heated medium. Electrical connections: Tighten connections to avoid overheating and potential fires. Tip 3: Temperature Control Overheating can drastically reduce a cartridge heater’s lifespan. Invest in a reliable temperature controller. Accurate sensors: Use precise temperature sensors for effective control. PID controllers: Consider advanced PID controllers for precise temperature regulation. Regular calibration: Ensure accurate temperature readings through calibration. Tip 4: Prevent Overloading Overloading can cause the heater to burn out. Calculate the required wattage carefully. Load matching: Ensure the heater’s wattage aligns with the application’s heat demand. Thermal calculations: Conduct proper heat transfer calculations to prevent overloading. Safety margins: Incorporate safety factors to avoid unexpected surges. Tip 5: Clean Regularly Accumulated dirt and debris can hinder heat transfer and reduce efficiency. Inspection schedule: Regularly inspect the heater for contaminants. Cleaning methods: Use appropriate cleaning methods based on the environment. Preventative measures: Implement measures to minimize contamination. Tip 6: Monitor Wear and Tear Regular inspections help identify potential issues before they escalate. Visual checks: Look for signs of damage, such as cracks or discoloration. Performance evaluation: Monitor heating performance for any decline. Replacement planning: Have spare heaters ready to avoid production disruptions. Tip 7: Optimize Thermal Conductivity Efficient heat transfer is crucial for optimal performance. Thermal interface materials: Use thermal paste or grease to improve contact. Heater placement: Position the heater for maximum heat dissipation. Material selection: Choose materials with high thermal conductivity for the heated components. Tip 8: Consider Thermal Cycling Frequent on/off cycles can shorten heater life. Minimize thermal shock. Ramp-up and cool-down times: Gradually increase and decrease temperature. Soft starters: Use soft starters to reduce voltage spikes. Insulation: Insulate the heater to maintain temperature during off-cycles. Tip 9: Emergency Shutdown Implement safety measures to protect against overheating and fires. Thermal cut-offs: Install thermal cut-offs as a backup safety measure. Fire suppression systems: Consider using fire suppression systems in hazardous areas. Emergency procedures: Develop clear emergency procedures for heater-related incidents. Tip 10: Proper Storage Store unused cartridge heaters in a cool, dry place to preserve their condition. Original packaging: Use original packaging or protective containers. Moisture protection: Store heaters in moisture-free environments. Avoid physical damage: Handle heaters carefully to prevent damage. By following these tips, you can significantly extend the life of your cartridge heaters and optimize their performance. Remember, preventive maintenance is key to avoiding costly breakdowns and ensuring uninterrupted production.
7 Must-Know Facts About 3D Printer Heaters
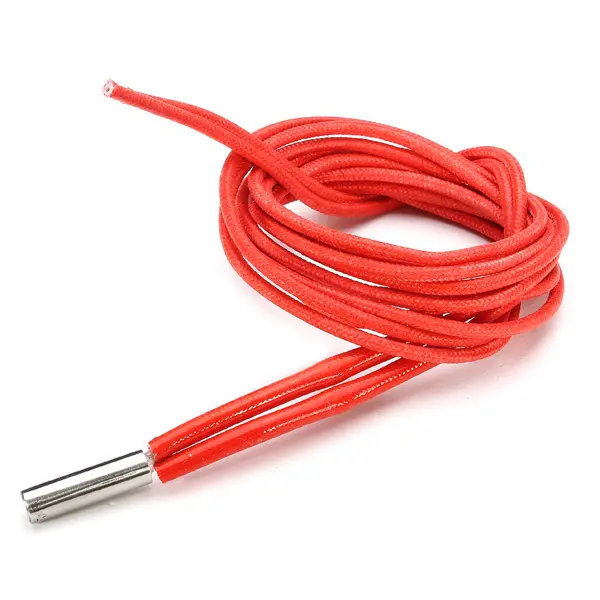
3D printing has changed the way we create objects. At the heart of this technology lies a crucial component – the heater. A 3D printer heater manufacturer plays a key role in the quality and efficiency of 3D prints. This blog post will uncover seven essential facts about 3D printer heaters that every enthusiast and professional should know. 1. The Role of Heaters in 3D Printing 3D printer heaters are the unsung heroes of the printing process. They melt the plastic filament, turning it into a liquid that can be shaped into amazing 3D objects. Without proper heating, your prints would be weak, brittle, or might not even form at all. Heaters work in two main areas of a 3D printer: The extruder: This is where the plastic filament is melted. The print bed: This keeps the printed object warm to prevent warping. The right temperature is crucial. Too hot, and your plastic might burn or lose its properties. Too cold, and it won’t stick together well. That’s why understanding heaters is so important for successful 3D printing. 2. Types of 3D Printer Heaters There are several types of heaters used in 3D printers. Each has its own strengths and best uses: Cartridge Heaters: These are the most common. They’re small, cylindrical, and fit snugly into the heater block. Ceramic Heaters: These heat up quickly and evenly. They’re often used in high-end printers. Silicone Heaters: These are flat and flexible. They’re great for heating print beds. Induction Heaters: These use electromagnetic fields to heat metal. They’re fast but more complex. Nichrome Wire: This is a resistive wire that heats up when electricity flows through it. Choosing the right type depends on your printer design and what you’re printing. Some materials need higher temperatures, while others work best with steady, lower heat. 3. The Impact of Heater Quality on Print Results The quality of your 3D printer heater can make or break your prints. High-quality heaters from reputable manufacturers offer several benefits: Consistent Temperature: They maintain a steady temperature, which is crucial for print quality. Fast Heating: Good heaters reach the desired temperature quickly, saving you time. Durability: They last longer, saving you money and hassle in the long run. Safety: Quality heaters have built-in safety features to prevent overheating. Poor quality heaters can lead to: Uneven heating Temperature fluctuations Slow warm-up times Premature failure Investing in a good heater can significantly improve your 3D printing results. It’s not just about the initial cost – think about the long-term benefits and the quality of your prints. 4. Temperature Control and Its Importance Precise temperature control is vital in 3D printing. Different materials need different temperatures: PLA: 180-230°C ABS: 210-250°C PETG: 230-250°C Nylon: 240-260°C These temperatures aren’t just suggestions. They’re critical for proper melting and layer adhesion. Modern 3D printers use thermistors or thermocouples to measure temperature. These sensors work with the printer’s control board to maintain the right heat. Good temperature control also affects: Layer Adhesion: Proper heat ensures layers stick together well. Warping: Correct bed temperature prevents the base of prints from curling up. Surface Finish: The right temperature gives smoother, more professional-looking prints. Advanced printers even allow for temperature changes during printing. This can help with complex shapes or multi-material prints. 5. Energy Efficiency and Power Consumption 3D printing can use a lot of energy, especially for long prints. Heaters are often the biggest power consumers in a 3D printer. Here’s why efficiency matters: Cost: More efficient heaters mean lower electricity bills. Environmental Impact: Less energy use is better for the planet. Print Time: Efficient heaters warm up faster, reducing overall print time. Some ways to improve efficiency: Insulation: Good insulation around the heater block and print bed reduces heat loss. PID Tuning: This adjusts how the printer controls the heater, optimizing power use. Smart Power Management: Some printers reduce power to heaters when not in use. Modern 3D printer heater manufacturers are focusing on creating more efficient heating systems. This not only saves energy but also improves print quality by maintaining more stable temperatures. 6. Maintenance and Longevity of 3D Printer Heaters Like any part of a 3D printer, heaters need care to last. Proper maintenance can extend the life of your heater and improve print quality. Here are some tips: Regular Cleaning: Remove any plastic buildup around the heater block. Check Connections: Loose wires can cause temperature fluctuations or failures. Monitor Performance: Watch for signs of inconsistent heating or longer warm-up times. Replace Thermistors: These sensors can wear out over time, affecting temperature accuracy. Signs that your heater might need replacement: Inconsistent temperatures Difficulty reaching or maintaining temperature Visible damage to the heater or its wires Most heaters last for hundreds or even thousands of hours of printing. But their lifespan can vary based on usage and quality. Keeping spare heaters on hand can prevent long downtimes if a replacement is needed. 7. Future Trends in 3D Printer Heater Technology The world of 3D printing is always advancing, and heater technology is no exception. Here are some exciting trends to watch: Faster Heating: New materials and designs are allowing for quicker warm-up times. More Precise Control: Advanced algorithms are improving temperature stability. Multi-Zone Heating: Some printers now use multiple heaters for more complex temperature control. Smart Heaters: IoT-enabled heaters that can be monitored and controlled remotely. Energy Harvesting: Some researchers are exploring ways to capture and reuse heat energy in 3D printers. New Materials: Heaters designed for exotic filaments that require very high or precise temperatures. Miniaturization: As 3D printers get smaller, heaters are shrinking too, without losing efficiency. These advancements promise to make 3D printing faster, more efficient, and capable of working with an even wider range of materials. Final Words 3D printer heaters are a critical component that often doesn’t get the attention it deserves. Understanding these seven facts can help you choose the right printer, maintain it properly, and get the best results from your 3D printing projects. As technology continues to advance,
Top 5 MI Heating Cable Benefits for Industries
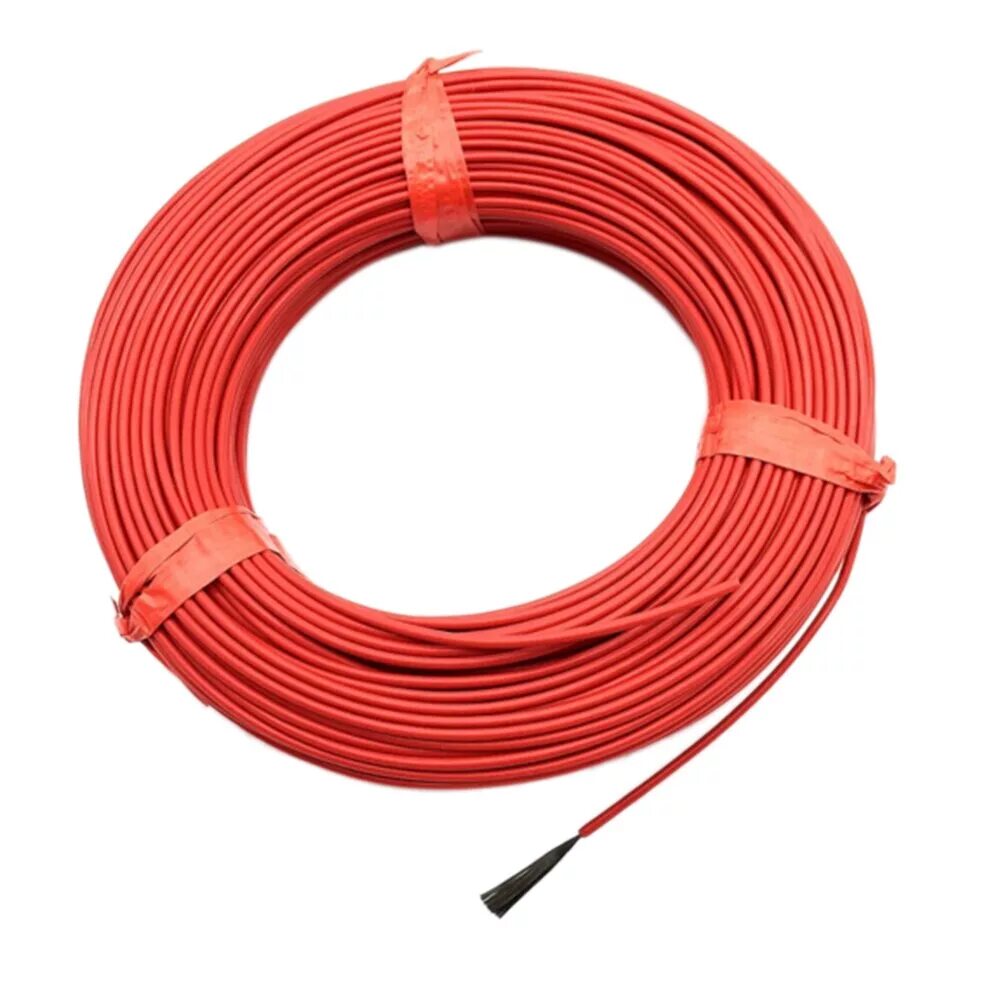
Reliable heating solutions are crucial in every industrial application. MI Heating Cable stands out as a top choice for many industries. This innovative technology offers numerous advantages that can boost efficiency and safety in various applications. Let’s explore the top five benefits of MI Heating Cable and why it’s becoming increasingly popular among industry professionals. 1. Superior Temperature Control One of the most significant advantages of MI Heating Cable is its ability to provide precise temperature control. This feature is essential in many industrial processes where maintaining a specific temperature is critical. Consistent heat distribution: MI Heating Cable ensures even heat distribution along its entire length, eliminating hot or cold spots. Quick response time: The cable reacts rapidly to temperature changes, allowing for swift adjustments. Wide temperature range: It can operate effectively from sub-zero temperatures up to 600°C (1112°F). Real-life example: In a pharmaceutical manufacturing plant, MI Heating Cable is used to maintain a constant temperature in storage tanks. This precise control helps preserve the quality and efficacy of sensitive medications. 2. Durability and Longevity MI Heating Cable is built to last, making it an excellent investment for industries looking for long-term heating solutions. Robust construction: The cable’s mineral insulation and metal sheath provide exceptional protection against mechanical damage. Resistance to harsh environments: It can withstand extreme conditions, including high temperatures, chemicals, and moisture. Minimal maintenance: Due to its sturdy design, MI Heating Cable requires less upkeep compared to other heating systems. According to a recent study, MI Heating Cable installations have an average lifespan of 20-30 years, significantly longer than many alternative heating solutions. 3. Energy Efficiency In an era where energy conservation is paramount, MI Heating Cable offers impressive energy efficiency benefits. Low heat loss: The cable’s design minimizes heat loss, ensuring that most of the energy is used for its intended purpose. Zoned heating: It allows for targeted heating of specific areas, reducing overall energy consumption. Compatibility with smart controls: MI Heating Cable can be integrated with advanced control systems for optimized energy use. A food processing plant reported a 15% reduction in energy costs after switching to MI Heating Cable for their pipe freeze protection system. 4. Versatility in Applications The adaptability of MI Heating Cable makes it suitable for a wide range of industrial applications. Process temperature maintenance: Keeps pipes, tanks, and vessels at the required temperature. Freeze protection: Prevents water lines and equipment from freezing in cold climates. Snow and ice melting: Used in walkways, ramps, and roofs to prevent ice buildup. Heat tracing: Maintains viscosity in fluid transport systems. For example, an oil refinery in Alaska uses MI Heating Cable to prevent crude oil from solidifying in pipelines during harsh winter months. 5. Enhanced Safety Features Safety is a top priority in any industrial setting, and MI Heating Cable offers several features that contribute to a safer working environment. Low fire risk: The mineral insulation is non-flammable, reducing the risk of fires. No toxic fumes: Unlike some plastic-insulated cables, MI Heating Cable doesn’t emit harmful fumes when heated. Grounded metal sheath: Provides an extra layer of electrical safety. Fail-safe design: If damaged, the cable typically fails in an open circuit, preventing overheating. A chemical processing facility reported zero safety incidents related to their heating system in the five years since installing MI Heating Cable. Final Words MI Heating Cable offers numerous benefits for industries, from superior temperature control to enhanced safety features. Its durability, energy efficiency, and versatility make it an excellent choice for a wide range of applications. By choosing MI Heating Cable, businesses can improve their processes, reduce energy costs, and create safer working environments. As technology advances, we can expect to see even more innovative applications for this versatile heating solution in the future.
5 Practical Ways to Use Quartz Infrared Tube Heater
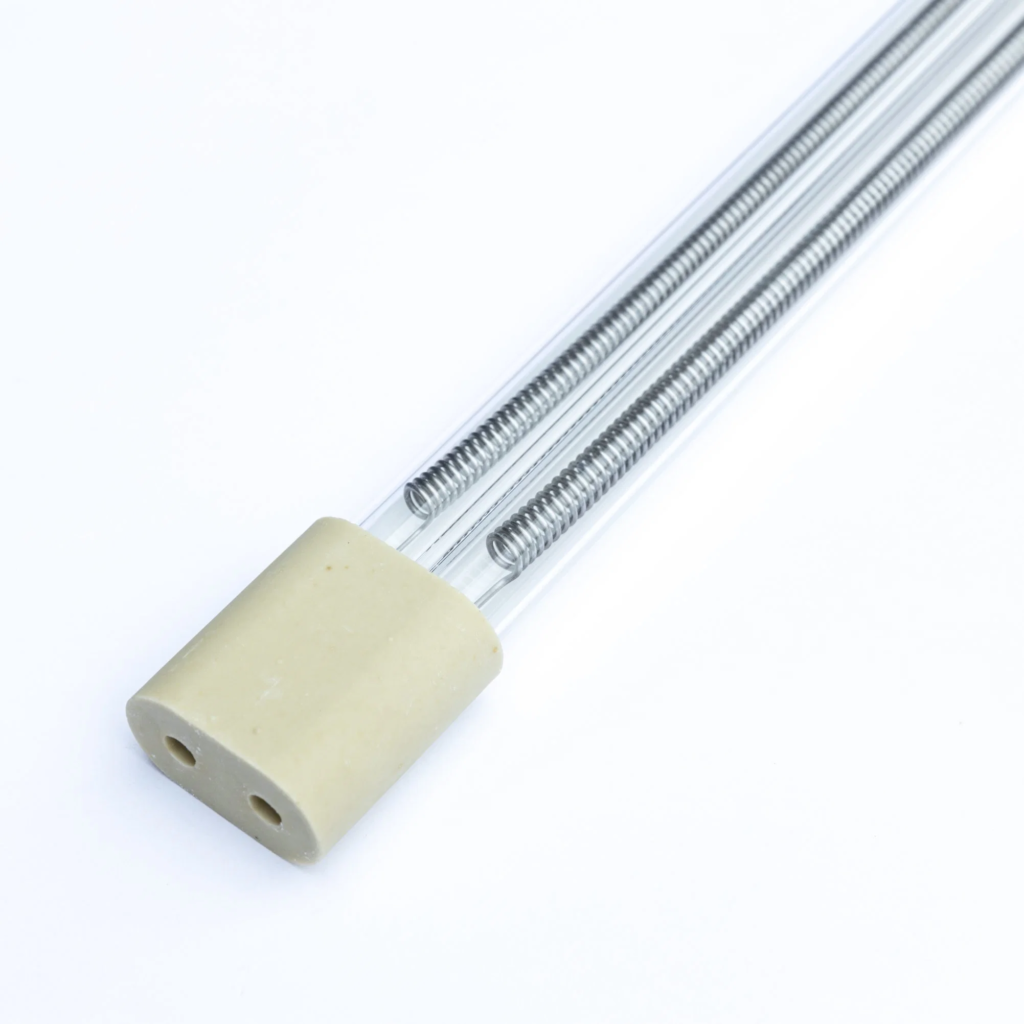
When it comes to efficient heating solutions, the Quartz Infrared Tube Heater stands out. This powerful heating device offers quick and targeted warmth. It’s becoming a go-to choice for many homeowners and businesses. Let’s explore five practical ways to use this versatile heater. 1. Outdoor Patio Heating Extend your outdoor living season with a Quartz Infrared Tube Heater. These heaters are perfect for patios and decks. Quick heat: They warm up in seconds, providing instant comfort. Energy-efficient: They heat objects, not air, saving energy. Weather-resistant: Many models can withstand light rain and wind. A recent study showed that restaurants with outdoor heating increased their revenue by 30% during colder months. One popular café in Chicago used quartz infrared heaters to keep their patio open year-round. They saw a 25% boost in winter sales. 2. Garage Workshop Heating Transform your cold garage into a cozy workshop with a Quartz Infrared Tube Heater. Targeted heating: Focus warmth on your work area. Safe for flammable materials: They don’t heat the air, reducing fire risks. Low maintenance: No moving parts means less wear and tear. John, a woodworker from Minnesota, installed a quartz infrared heater in his garage. He can now work comfortably even when it’s -20°F outside. His productivity increased by 40% during the winter months. 3. Greenhouse Heating Quartz Infrared Tube Heaters are ideal for maintaining optimal temperatures in greenhouses. Plant-friendly: They don’t dry out the air like some heaters. Even heat distribution: Ensures all plants receive equal warmth. Energy-saving: Can be programmed to run only when needed. A small organic farm in Vermont used these heaters to extend their growing season. They were able to harvest fresh tomatoes two months longer than usual. This resulted in a 15% increase in annual revenue. 4. Industrial Spot Heating In large warehouses or factories, heating the entire space can be costly. Quartz Infrared Tube Heaters offer a smart solution. Zone heating: Heat only occupied areas. Quick warm-up: Ideal for areas with high traffic but intermittent use. Silent operation: No noisy fans or motors. A manufacturing plant in Texas installed these heaters above workstations. They reduced their overall heating costs by 35%. Employee comfort and productivity also improved significantly. 5. Sports Arena Seating Keep fans comfortable during outdoor sporting events with strategically placed Quartz Infrared Tube Heaters. Directional heat: Can be aimed at specific seating sections. Instant on/off: No need to pre-heat before the game. Clean heat: No fumes or odors to distract from the game. A minor league baseball stadium in Colorado installed these heaters above their VIP seating area. They saw a 20% increase in premium ticket sales for early and late-season games. As we move towards more energy-efficient solutions, these heaters are likely to become even more popular. Conclusion Quartz Infrared Tube Heaters offer versatile heating solutions for various settings. From outdoor patios to industrial workspaces, they provide efficient and targeted warmth. Their energy-saving features and low maintenance make them a smart choice for many applications. They offer a balance of comfort, efficiency, and practicality. Whether you’re a homeowner looking to extend your outdoor season or a business owner aiming to cut heating costs, consider a Quartz Infrared Tube Heater.
5 Practical Ways to Use Immersion Tubular Heater
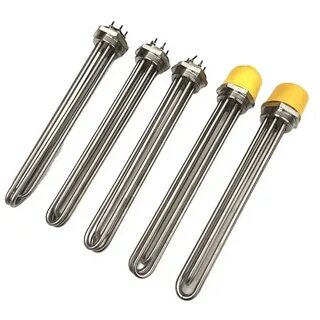
Heating solutions play a crucial role in many industries and everyday applications. The Immersion Tubular Heater stands out as a versatile and efficient option. This powerful heating device can transform various processes and improve outcomes in surprising ways. We will explore five practical uses for the Immersion Tubular Heater that show its flexibility and effectiveness. 1. Enhancing Food Processing In the food industry, maintaining precise temperatures is key to quality and safety. Immersion Tubular Heaters excel in this area, offering several benefits: Consistent heating: They provide even heat distribution, crucial for large-scale cooking and pasteurization. Quick temperature changes: Rapid heating and cooling help in processing different food items efficiently. Sanitary design: Their smooth surface is easy to clean, meeting strict food safety standards. A recent study showed that using Immersion Tubular Heaters in dairy pasteurization improved energy efficiency by 15% compared to traditional methods. 2. Improving Chemical Processing Chemical reactions often require specific temperatures to proceed correctly. Immersion Tubular Heaters offer precise control, making them ideal for this industry. Temperature accuracy: They can maintain temperatures within ±1°C, crucial for sensitive reactions. Corrosion resistance: Many models come with special coatings to withstand harsh chemicals. Customizable designs: Heaters can be shaped to fit various tank sizes and configurations. In a real-world example, a pharmaceutical company used custom Immersion Tubular Heaters to speed up their drug synthesis process by 20%. This led to faster production times and lower costs. 3. Enhancing Water Treatment Clean water is essential, and Immersion Tubular Heaters play a vital role in water treatment processes. Efficient heating: They can quickly heat large volumes of water for purification. Energy-saving: Direct immersion means less heat loss compared to external heating methods. Scalability: Heaters can be easily added or removed to adjust to changing needs. 4. Powering Industrial Cleaning Many industries rely on hot water and steam for cleaning. Immersion Tubular Heaters offer an efficient solution for these applications. High-temperature capability: They can produce water hot enough for steam generation. Durability: Built to withstand frequent use in demanding environments. Safety features: Many models include automatic shut-off to prevent overheating. 5. Supporting Renewable Energy Systems As the world shifts towards renewable energy, Immersion Tubular Heaters are finding new roles in supporting these systems. Solar thermal support: They can provide backup heating for solar water heaters on cloudy days. Biomass processing: Heaters help maintain optimal temperatures in biogas digesters. Energy storage: They’re used in thermal energy storage systems to store excess renewable energy as heat. Last Word The immersion tubular heater proves its worth across various industries and applications. From food processing to renewable energy support, its versatility and efficiency make it a valuable tool. As technology advances, we can expect to see even more innovative uses for these powerful heating devices. Whether you’re in manufacturing, water treatment, or exploring new energy solutions, consider how an immersion tubular heater might improve your processes.
5 Applications of Best Flange Tubular Heater in Manufacturing
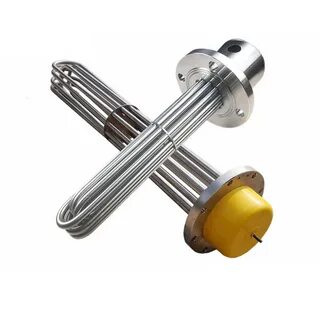
Heating plays a crucial role in many manufacturing processes. The best flange tubular heater stands out as a top choice for various industrial applications. These heaters are known for their efficiency, durability, and versatility. Let’s explore five key ways manufacturers are using these heaters to improve their operations and product quality. 1. Plastic Molding and Extrusion Plastic molding and extrusion processes rely heavily on precise temperature control. The best flange tubular heater excels in this area, offering several benefits: Even heat distribution: These heaters provide uniform heat across the mold or extruder barrel. Quick temperature changes: They can rapidly heat up or cool down, allowing for faster production cycles. Energy efficiency: Flange tubular heaters use less energy compared to other heating methods. A recent study showed that manufacturers using flange tubular heaters in plastic molding saw a 15% increase in production speed. This boost in efficiency can lead to significant cost savings over time. 2. Food Processing Equipment In the food industry, maintaining proper temperatures is crucial for safety and quality. Flange tubular heaters are ideal for various food processing applications: Cooking and baking: They provide consistent heat for ovens and cooking equipment. Sterilization: These heaters can reach the high temperatures needed for sterilizing equipment. Packaging: They help seal packaging materials safely and efficiently. For example, a large bakery in Chicago switched to flange tubular heaters in their ovens. They reported a 20% improvement in baking consistency and a 10% reduction in energy costs. 3. Chemical Processing Chemical reactions often require specific temperatures to occur. The best flange tubular heater offers precise control for these sensitive processes: Reactor vessels: They can maintain exact temperatures for complex chemical reactions. Storage tanks: These heaters keep chemicals at the right temperature during storage. Distillation columns: They provide the heat needed for the effective separation of compounds. 4. Aerospace Manufacturing The aerospace industry demands high precision in all aspects of manufacturing. Flange tubular heaters meet these strict requirements: Composite curing: They provide the exact heat needed for curing advanced materials. Metal heat treatment: These heaters can reach the high temperatures required for treating aerospace alloys. Environmental testing: They’re used in chambers that simulate extreme conditions for aircraft parts. 5. Semiconductor Production The semiconductor industry relies on ultra-clean and precise manufacturing processes. Flange tubular heaters play a vital role: Wafer processing: They provide the heat needed for various stages of chip production. Clean room heating: These heaters can be designed to meet strict cleanliness standards. Chemical vapor deposition: They supply the heat for this critical step in semiconductor manufacturing. A major chip manufacturer in Taiwan reported a 40% decrease in heating-related defects after upgrading to high-quality flange tubular heaters. Wrap Up The best flange tubular heater has proven its worth across various manufacturing sectors. As industries continue to evolve, the role of these heaters is likely to grow even further. Manufacturers looking to improve their processes should consider the benefits of flange tubular heaters. With their versatility and performance, they can be a game-changer in many industrial applications. The examples we’ve seen show that investing in quality heating solutions can lead to significant improvements in productivity and product quality.
How Do Electric Tube Heaters Work?
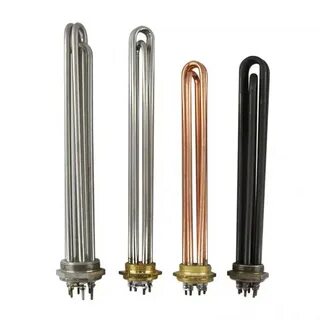
An electric tubular heater is a vital tool used in various industries for efficient and targeted heating. Understanding how these heaters work is essential, whether you’re looking to improve your knowledge or make informed decisions for your business. This blog post will enlighten you about the mechanics of electric tube heaters, breaking down their components and applications in simple terms. What is an Electric Tubular Heater? Electric tubular heaters are versatile heating elements used for warming solids, liquids, and gases. They are designed to convert electrical energy into heat with high efficiency. The heaters are made of a metal tube, usually stainless steel, with an insulated heating coil inside. This coil heats up when electricity passes through it, and the surrounding metal tube transfers the heat to the material being heated. Sheath Material: The outer tube is typically made from durable materials like stainless steel or Incoloy, which can withstand high temperatures and resist corrosion. Heating Coil: Inside the tube, a coil made of resistance wire (usually nickel-chromium) is the primary source of heat. Insulation: Magnesium oxide powder surrounds the heating coil inside the tube. This material not only insulates the coil electrically but also transfers heat from the coil to the tube efficiently. How Does an Electric Tubular Heater Work? Electric tubular heaters operate by generating heat through electrical resistance. When electricity flows through the resistance wire in the heating coil, it generates heat. This heat is then conducted to the outer metal sheath, which transfers it to the medium that needs to be heated, whether it’s air, water, oil, or another substance. These heaters can be designed to provide either direct or indirect heating. In direct heating, the heater comes into direct contact with the material to be heated, such as in immersion heaters used for heating water. In indirect heating, the heater warms the surrounding air or liquid, which then heats the target material, like in ovens or industrial heating systems. Applications of Electric Tubular Heaters Electric tubular heaters are used in various industries due to their versatility and reliability. HVAC Systems: They are commonly used in heating, ventilation, and air conditioning systems to maintain comfortable temperatures in buildings. Food Processing: In the food industry, these heaters ensure consistent temperatures for cooking, baking, and drying processes, maintaining food safety and quality. Industrial Equipment: They are used in machinery that requires controlled heating, such as plastic molding machines and packaging equipment. Laboratory Instruments: In laboratories, electric tubular heaters provide precise and consistent heat for experiments and testing. Water Heating: Electric tubular heaters are often used in water heaters and boilers, providing efficient and reliable heating. Benefits of Electric Tubular Heater Electric tubular heaters offer several advantages that make them a popular choice across various applications. Energy Efficiency: These heaters are designed to convert nearly all the electrical energy into heat, making them highly efficient. Durability: Made from robust materials like stainless steel, they can withstand high temperatures and harsh conditions, ensuring long-lasting performance. Versatility: With the ability to heat solids, liquids, and gases, electric tubular heaters are versatile and can be customized for specific applications. Precise Temperature Control: These heaters offer accurate and consistent heating, which is crucial in processes where temperature control is vital. Last Word Understanding how an electric tubular heater works is crucial for anyone involved in industries that rely on precise and efficient heating. These heaters offer a combination of energy efficiency, durability, and versatility that makes them invaluable in various applications. By choosing the right heater and maintaining it properly, you can ensure optimal performance and longevity, making them a reliable choice for your heating needs.
What is the Purpose of a Band Heater?
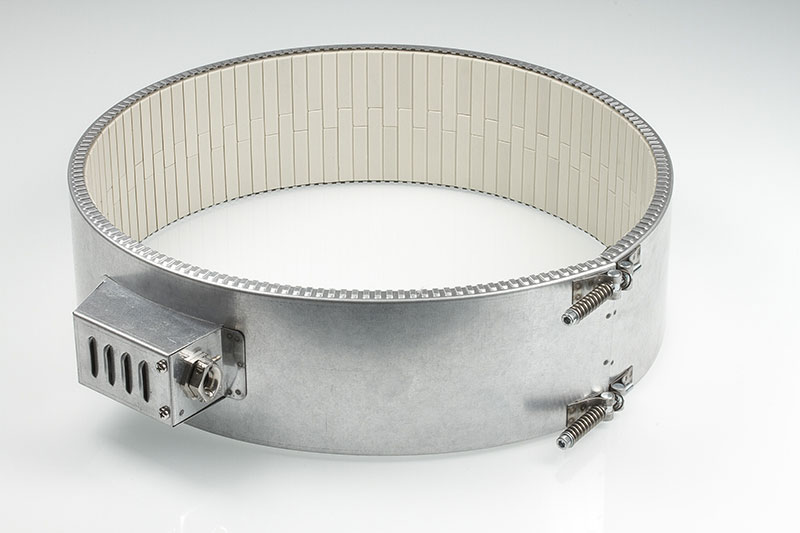
Understanding the role of a band heater is crucial, especially if you’re working with equipment that demands precise temperature control. Whether you’re familiar with industrial heating or just getting started, knowing what a band heater manufacturer offers can make all the difference. These heaters are vital in many industries, ensuring that machines and processes run smoothly and efficiently. How Does a Band Heater Work? Band heaters are cylindrical devices designed to heat cylindrical objects. They fit snugly around the surface of a cylinder, providing even and consistent heat. Sheath Material: The outer layer is usually made of stainless steel, which is durable and resistant to oxidation at high temperatures. Insulation: Inside the heater, layers of insulation, such as mica or ceramic, help prevent heat loss and ensure that most of the energy is directed towards heating the cylinder. Heating Element: The core component is a wire made of materials like nickel-chromium, which heats up when electricity flows through it. This design allows the band heater to evenly distribute heat, which is essential for applications requiring uniform temperatures. What are The Common Applications of Band Heaters Band heaters are used in a variety of settings. Their ability to maintain consistent temperatures makes them invaluable in several industries. Plastic Industry: In plastic injection molding machines, band heaters maintain the temperature of the barrels, ensuring that the plastic melts uniformly. Packaging Industry: They are used to seal packages by providing the necessary heat to bonding surfaces. Food Industry: Band heaters help maintain the temperature of processing equipment, ensuring that food products are cooked or processed at consistent temperatures. Chemical Industry: In chemical processing, maintaining precise temperatures is critical for reactions. Band heaters are used to ensure that vessels and pipes remain at the required temperature. Textile Industry: They keep dye vats and other processing equipment at consistent temperatures, ensuring that colors are applied evenly. What are The Types of Band Heaters There are several types of band heaters, each designed for specific applications. Mica Band Heaters: These are the most common type and are suitable for applications requiring lower watt densities. They are ideal for plastic processing machinery. Ceramic Band Heaters: These are used in applications that require high temperatures and are known for their energy efficiency due to the ceramic insulation. Nozzle Heaters: A specialized type of band heater, nozzle heaters are used in machines that have smaller surfaces to heat, such as the nozzles of injection molding machines. Benefits of Using a Band Heater Band heaters offer several benefits, making them a preferred choice in various industries. Efficient Heat Transfer: Band heaters are designed to provide direct heat to the surface they wrap around, making them highly efficient. Durability: Made from high-quality materials, they are built to withstand harsh industrial environments. Energy Savings: The insulation within band heaters minimizes heat loss, reducing energy consumption. Customizable: A band heater manufacturer can customize these heaters to meet specific needs, including size, wattage, and material. Wrap Up Understanding the purpose of a band heater is essential for anyone involved in industries that require precise temperature control. From their construction to their applications, band heaters play a key role in maintaining the quality and efficiency of various processes. By choosing a reliable band heater manufacturer, you can ensure that your equipment runs efficiently and meets your specific heating needs. These heaters are more than just tools; they are essential components that keep many industries running smoothly.