3 Reasons Why Cartridge Heater is a Must in Industrial Applications
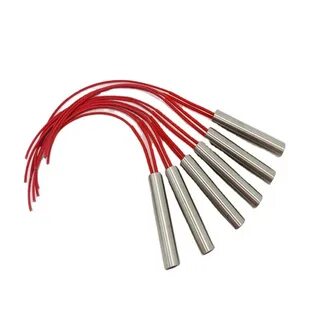
A cartridge heater is indispensable in the industrial sector, widely relied upon to deliver efficient, high-temperature heating for various processes. Known for their compact yet powerful build, these heaters fit into tight spaces, delivering precise heat where it’s needed most. From manufacturing to automotive and beyond, cartridge heaters enhance operational efficiency, help maintain quality, and lower costs. Let’s delve into the top reasons why a cartridge heater is essential in industrial applications, backed by research and real-world insights. 1. High-Temperature Efficiency and Precision Control One of the main advantages of using a cartridge heater in industrial applications is its high-temperature capability and precision. Many industries rely on heating elements that can reach temperatures above 1,200°F (649°C) to ensure effective processing. Here’s how cartridge heaters excel in these demanding environments: Efficient Heat Distribution: Cartridge heaters feature a unique design that allows them to heat up quickly and distribute heat evenly. This is essential in industries like plastic molding and packaging where consistent heat levels directly impact product quality. Precision Control: Advanced cartridge heaters often include control mechanisms that allow for precise temperature adjustments, ensuring no energy is wasted and that materials aren’t damaged by overheating. With these features, cartridge heaters help maintain the thermal stability needed for industries such as automotive manufacturing and 3D printing, where even minor temperature variations can impact the outcome. 2. Durability and Reliability in Harsh Environments Industrial environments are often harsh, with exposure to chemicals, high-pressure settings, and rough handling. Cartridge heaters are designed to withstand these challenges, making them a durable and long-lasting heating solution: Stainless Steel Sheathing: Many cartridge heaters are built with stainless steel or other corrosion-resistant materials, which protect against environmental wear and tear. This is vital in industries like pharmaceutical and chemical processing. High Watt Density: Cartridge heaters can operate at high watt densities, meaning they can produce a lot of heat in a small space without degrading. This allows them to maintain consistent performance over time. In high-demand applications, these heaters often last thousands of hours without requiring replacement, significantly reducing maintenance costs and downtime. 3. Versatility Across Multiple Industrial Uses The versatility of cartridge heaters makes them suitable for a wide array of industrial applications, including food production, metalworking, and automotive manufacturing. They can be customized in terms of size, wattage, and voltage, making them adaptable to specific needs: Plastic Injection Molding: Cartridge heaters provide the precise and rapid heating required for molding materials into specific shapes. Consistent heat application ensures high-quality, defect-free products. Packaging Machinery: Packaging industries rely on cartridge heaters to seal products effectively. The consistent and controlled heat ensures seals are strong and leak-proof, which is especially crucial in food and medical packaging. Hot Runner Systems: These systems use cartridge heaters to keep the plastic material molten, allowing for efficient flow into molds and reducing material waste. Final Words For industrial operations that demand efficient, durable, and precise heating solutions, cartridge heater stands out as a top choice. With their wide adaptability and ability to operate in high-stress environments, cartridge heaters prove essential for optimizing production quality and efficiency.
What Are the Types of Heating Cable
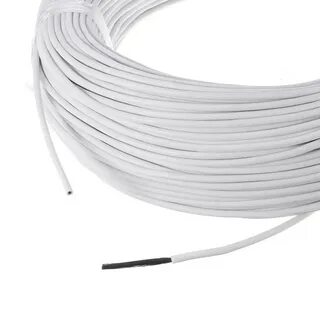
Heating cable technology is a game-changer for maintaining warmth in various environments and is essential in areas where temperature regulation is critical. Heating cable is designed to combat frost, prevent pipes from freezing, and maintain consistent warmth for specific equipment or structures. They are used in industrial settings, homes, and even in agriculture. With advancements in technology, different types of heating cables are now available, each suited to specific needs and applications. In this post, we’ll break down the main types of a heating cable and the benefits of each. 1. Self-Regulating Heating Cables Self-regulating heating cables automatically adjust their output based on the ambient temperature, making them one of the most energy-efficient options. Key Features: Adjusts heating output according to environmental temperature. Offers high safety by reducing the risk of overheating. Suitable for protecting pipes, roofs, and gutters. Application: Commonly used for freeze protection of pipes and maintaining optimal temperatures in process pipes in industrial settings. These cables are also popular for roof and gutter de-icing systems. Benefits: Energy Efficient: Reduces power consumption when the temperature is mild. Long-Lasting: Designed to last years with minimal maintenance. Safe: Automatically adjusts power levels, minimizing overheating risks. 2. Constant Wattage Heating Cables Constant wattage heating cables provide a consistent level of heat regardless of the surrounding temperature. Unlike self-regulating cables, they do not adjust based on external temperatures, making them ideal for situations where steady, continuous heating is required. Key Features: Provides a stable wattage output. Suitable for environments where temperature control is critical. Available in various wattage capacities to meet specific heating demands. Application: These cables are widely used in temperature-sensitive areas like laboratories or environments where the temperature must remain stable. Benefits: Precision Heating: Delivers stable heat output for consistent performance. Wide Application: Useful in both commercial and industrial settings. Effective: Maintains temperature in harsh environments where fluctuations can be problematic. 3. Mineral Insulated (MI) Heating Cables Mineral Insulated heating cables are durable and ideal for high-temperature applications. These cables consist of a metal conductor insulated with magnesium oxide, which can withstand extreme conditions without degrading. Key Features: Withstands temperatures up to 1000°C. Highly resistant to chemical exposure and mechanical stress. Provides reliable heat in high-temperature processes. Application: Used in heavy industries such as oil and gas, power generation, and chemical processing plants. Benefits: High Durability: Ideal for environments with corrosive chemicals and extreme temperatures. High-Performance Output: Delivers steady heat even under demanding conditions. Safety: Highly resistant to fire and can function in explosive environments. 4. Series Resistance Heating Cables Series resistance cables work by maintaining consistent resistance along the cable, delivering heat over its entire length. These cables are used in applications where precise lengths and specific wattages are needed. Key Features: Customizable to specific lengths and wattage requirements. Ensures uniform heating along the cable. Can be tailored for complex installations. Application: Ideal for specialized industrial applications, such as long pipelines or equipment that requires uniform heating over extensive areas. Benefits: Flexible Design: Easily customized to match various industrial setups. Uniform Heating: Delivers consistent warmth across the cable’s length. Customizable: Manufactured to meet precise requirements, making them perfect for unique applications. Final Thoughts Heating cables are a critical component in temperature-sensitive applications across industries, homes, and commercial spaces. Selecting the right type depends on specific requirements, environmental conditions, and budget. Whether you’re looking to keep pipes from freezing, control heat in process applications, or manage de-icing systems, choosing the right heating cable can help ensure reliable performance and energy efficiency.
5 Benefits of a High Temperature Cable
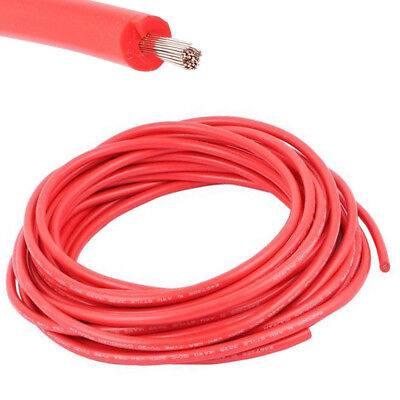
A high temperature cable is essential for industries where heat resistance and performance reliability are critical. These cables are engineered to handle extreme temperatures, ensuring safety and functionality in demanding applications. From industrial machinery to aerospace systems, their role in maintaining seamless operations cannot be overstated. Here are five key benefits of using high-temperature cables, with actionable insights. 1. Enhanced Heat Resistance High-temperature cables are designed to withstand extreme heat without degradation. Temperature Tolerance: These cables can endure temperatures as high as 1,000°F (538°C) or more, depending on the material. Safety Assurance: They minimize the risk of insulation melting, which is critical in aerospace, automotive, and manufacturing industries. This capability ensures longevity and reduces the risk of system failures under heat stress. 2. Durability in Harsh Environments High-temperature cables are built to last, even in environments with harsh conditions like abrasion, chemicals, or moisture. Chemical Resistance: Materials like PTFE and silicone provide resistance to chemicals and oils. Abrasion Protection: Reinforced coatings protect cables from physical wear, ideal for heavy-duty equipment. These features reduce replacement costs and enhance reliability. 3. Electrical Stability Even under high temperatures, these cables maintain consistent electrical properties. Reduced Signal Loss: High-temperature cables minimize signal interference, ensuring precise operations in machinery. Stable Conductivity: They handle voltage fluctuations effectively, safeguarding sensitive systems. This makes them a go-to choice for medical devices and robotics. 4. Versatility Across Industries High temperature cable is adaptable to numerous applications. Industrial Heating: Used in ovens, furnaces, and kilns, they can handle constant exposure to heat. Automotive Systems: Essential for engines and exhaust systems where extreme heat is prevalent. Aerospace Applications: Withstand the high temperatures of aircraft engines and space systems. This versatility ensures their applicability across a wide range of sectors. 5. Compliance with Safety Standards Manufacturers of high-temperature cables adhere to stringent industry standards. ISO and UL Certifications: These certifications ensure that cables meet high-performance criteria. Fire Safety: Many cables are flame-resistant, reducing risks in sensitive environments like data centers and laboratories. This compliance ensures peace of mind for industries requiring robust safety measures. Final Words A high temperature cable is more than just a heat-resistant solution. It is a reliable, durable, and versatile component for various industries. Its ability to perform under extreme conditions ensures efficiency, safety, and cost-effectiveness in critical applications.
How to Select a Hot Runner Heater Supplier
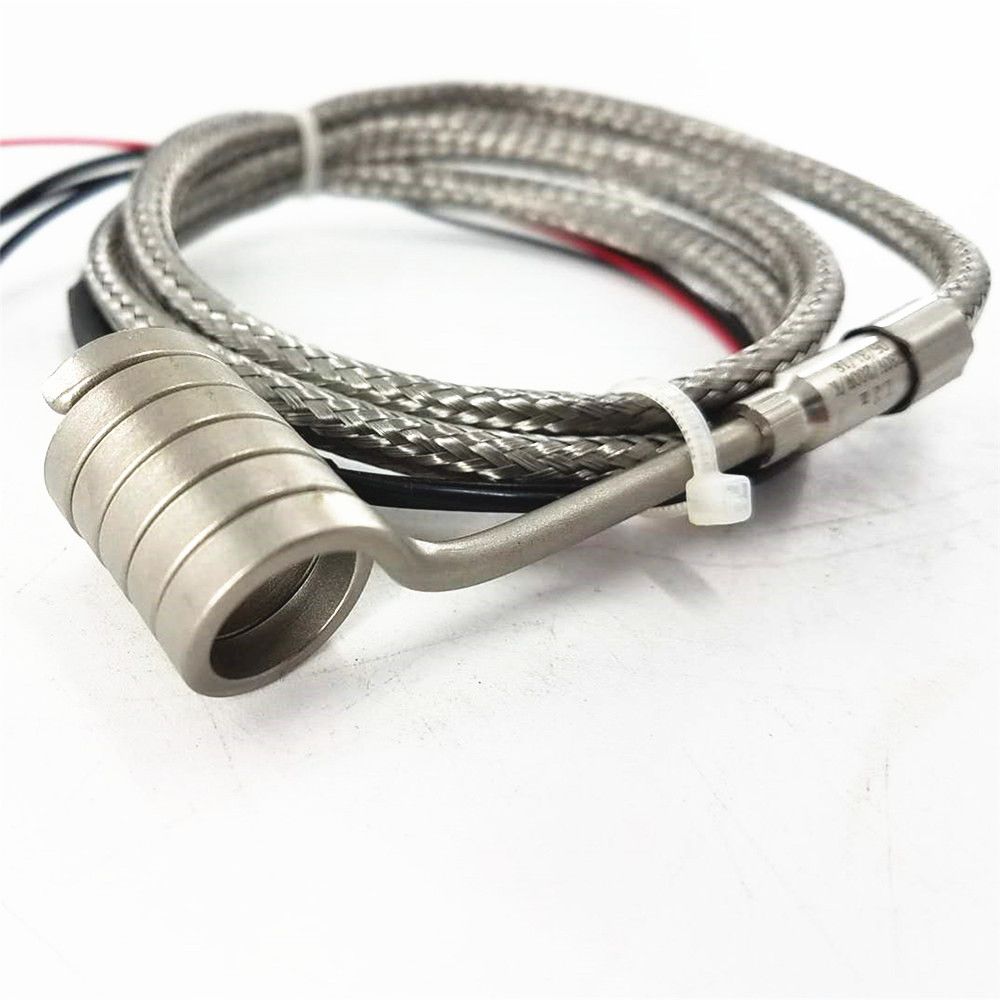
Choosing the right hot runner heater supplier can significantly impact the efficiency and output of your plastic molding processes. A reliable supplier ensures consistent heat delivery, reduced downtime, and superior product quality. However, not all suppliers offer the same level of service and product excellence. Here’s a research-driven guide to selecting the right hot runner heater partner for your industrial heating needs. 1. Evaluate the Supplier’s Product Quality The quality of a hot runner heater directly affects the performance of your system. Before committing to a supplier, verify the durability, efficiency, and reliability of their products. Materials Used: Look for heaters built with high-quality alloys, such as stainless steel or nickel, which resist corrosion and withstand high temperatures. Precision Heating: Check whether the heaters deliver uniform heat distribution. Consistency is essential in plastic molding to avoid product defects. Longevity: A high-quality hot runner heater should last thousands of cycles without degradation. Suppliers should provide data on their products’ lifespan under different operating conditions. 2. Assess Industry Experience and Reputation A supplier with extensive experience in the plastic molding industry is more likely to understand your specific requirements. Proven Track Record: Research the supplier’s history of delivering heaters for industries like automotive, medical, and consumer goods manufacturing. A supplier with expertise in these sectors is familiar with complex heating demands. Client Testimonials and Reviews: Read reviews from existing clients to gauge satisfaction with the supplier’s products and services. Certifications and Standards: Ensure the supplier complies with industry standards such as ISO 9001 or CE certifications. These indicate a commitment to quality and safety. 3. Customization Options for Specific Needs Every molding application has unique requirements. A competent supplier should offer customized hot runner heater solutions tailored to your system. Custom Sizes and Shapes: Suppliers should provide heaters in various diameters and lengths to match the design of your hot runner system. Voltage and Wattage Customization: The ability to fine-tune watt density and power requirements ensures optimal performance. Temperature Sensors: Some suppliers integrate advanced temperature control features, enabling precise adjustments to avoid overheating. 4. Technical Support and After-Sales Services Strong technical support is essential for seamless operations, especially in industries where downtime can be costly. Installation Assistance: Suppliers should provide detailed manuals, videos, or even on-site support for heater installation. Troubleshooting Help: Ensure the supplier offers responsive customer service for resolving issues quickly. Spare Parts Availability: A reliable supplier keeps essential components in stock to minimize delays in case of repairs. 5. Competitive Pricing Without Compromising Quality While pricing is an important factor, it should not come at the expense of quality or reliability. Transparent Quotes: Request detailed quotes that include product specifications, warranties, and delivery timelines. Hidden charges can inflate costs over time. Bulk Discounts: If your operations require large quantities of heaters, explore whether the supplier offers volume-based discounts. Red Flags to Avoid While selecting a supplier, be cautious of: Inconsistent Product Quality: Suppliers with frequent negative reviews about durability or performance. Limited Warranty Periods: Short warranties may indicate a lack of confidence in their products. Poor Communication: Delayed responses and unclear terms can cause operational challenges. Final Words Partnering with the right hot runner heater supplier is crucial for maintaining efficient plastic molding processes. From quality products to robust after-sales support, a supplier’s capabilities should align with your operational needs. For reliable solutions, consider trusted names like Jabeens, who offer expertise and high-performance heaters tailored to modern industry demands.
5 Reasons Why a Pipeline Heater is a Must in Industrial Manufacturing
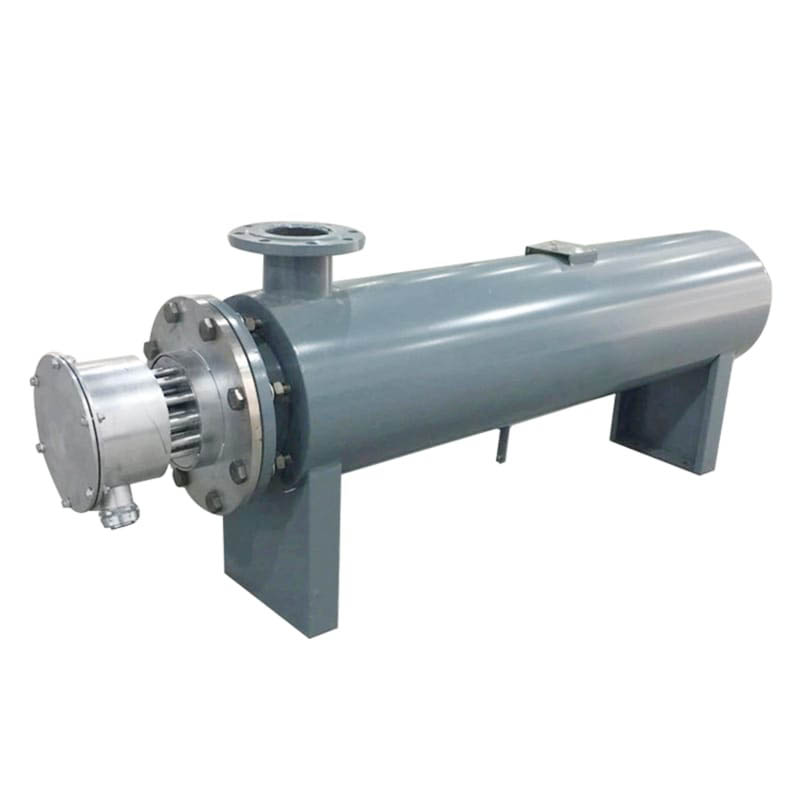
In industries like oil and gas, petrochemical, and food production, maintaining precise temperatures within pipelines is critical. A pipeline heater is a specialized tool designed to regulate the temperature of liquids and gases flowing through pipelines. Without it, efficiency, safety, and product quality can be compromised. This blog explains why a pipeline heater is indispensable in industrial manufacturing and highlights the unique benefits it offers. 1. Enhances Process Efficiency Pipeline heaters are crucial for maintaining consistent temperatures, which directly improves process efficiency. In industries like oil and gas, where substances such as crude oil and natural gas flow through pipelines, maintaining optimal viscosity is vital. Reduces Energy Loss: By keeping materials at the desired temperature, pipeline heaters minimize the energy required to reheat substances later in the process. Prevents Clogging: Materials like crude oil can solidify or thicken at low temperatures. Pipeline heaters ensure a smooth flow, preventing costly clogs. Supports Continuous Operations: With reduced interruptions due to temperature issues, industries can maintain round-the-clock operations efficiently. This efficiency translates to increased output and lower operational costs. 2. Protects Equipment from Wear and Tear Industrial pipelines face significant stress when temperature fluctuations occur. These fluctuations can cause materials to expand and contract, leading to wear and tear. Prevents Corrosion: A consistent temperature prevents condensation, which could lead to corrosion inside the pipeline. Reduces Mechanical Stress: Temperature control mitigates the strain on valves and joints, extending the life of the pipeline infrastructure. By minimizing equipment damage, pipeline heaters save industries significant maintenance costs over time. 3. Ensures Safety and Compliance Temperature mismanagement in pipelines can lead to hazardous situations, especially in industries handling flammable or volatile substances. Pipeline heaters play a vital role in ensuring safety. Prevents Freezing: In cold climates, fluids in pipelines can freeze, causing blockages and potential ruptures. Pipeline heaters eliminate this risk. Reduces Pressure Build-Up: Proper heating ensures that gases expand predictably, avoiding dangerous pressure spikes. Meets Regulatory Standards: Many industries are required to comply with strict temperature and safety regulations. Pipeline heaters help meet these standards reliably. Safety is not just a priority but a necessity in industrial manufacturing. 4. Supports Product Quality In manufacturing, the quality of the final product often depends on maintaining precise conditions during production. Pipeline heaters play a key role in ensuring this consistency. Prevents Contamination: Materials flowing through pipelines are less likely to degrade or mix with impurities when maintained at the correct temperature. Improves End-Product Uniformity: In food manufacturing, for instance, maintaining even heating can prevent texture and taste inconsistencies. By supporting quality assurance, pipeline heaters help industries deliver reliable products. 5. Adapts to Diverse Applications Pipeline heaters are versatile, making them suitable for a wide range of industrial processes. Oil and Gas: Used to heat crude oil, natural gas, and other hydrocarbons, ensuring efficient transport and processing. Chemical Processing: Maintain specific temperatures for reactions and material flows. Food and Beverage: Essential for transporting liquids like syrup or chocolate, which need to stay at precise temperatures. This adaptability ensures that pipeline heaters remain an essential component across diverse industries.
5 Benefits of a Tubular Heating Element
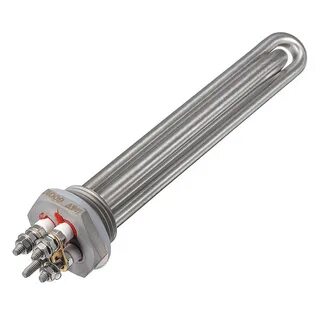
When it comes to heating solutions, tubular heater technology stands out due to its versatility and efficiency. These heating elements are used in countless applications, from industrial machinery to domestic appliances. But why are they so widely chosen? Below are five key benefits of a tubular heater that make it a top choice for heating systems. 1. Efficient Heat Distribution A tubular heater provides uniform heating over a wide surface area. Its design ensures that heat is evenly distributed, which is essential for many applications like: Home appliances: Like ovens or water heaters, where consistent heating is needed. Industrial uses: In manufacturing processes that require uniform temperature control. By ensuring a consistent temperature, tubular heaters can improve performance, reduce energy waste, and prevent hotspots that could damage sensitive equipment. 2. Versatility Across Industries One of the main reasons tubular heaters are so widely used is their flexibility in design. They can be customized to meet the specific needs of different environments. Some key areas where tubular heaters excel include: Residential: Water heaters, underfloor heating, and air conditioning systems. Commercial: Food warmers, beverage dispensers, and vending machines. Industrial: Tanks, pipes, and machinery that require precise temperature control. The ability to adapt the heater’s shape and size to different applications is a major advantage. 3. Long Lifespan and Durability Durability is another standout feature of a tubular heater. When properly maintained, these heaters have a long lifespan, even in harsh environments. Factors contributing to their durability include: Corrosion resistance: Many tubular heaters are designed with materials like stainless steel, which can withstand exposure to moisture and corrosive substances. Heat resistance: They perform well in high-temperature conditions without degradation. As a result, these heaters often require less frequent replacement, offering significant cost savings over time. 4. Energy Efficiency and Cost Savings Energy consumption is always a key consideration in heating systems. Tubular heaters are designed to operate efficiently, converting most of the electrical energy into heat. This leads to: Lower operating costs: Because more energy is converted into heat, the system doesn’t need to work as hard, reducing energy bills. Reduced maintenance costs: Their longevity and durability mean fewer repairs and replacements are required. This efficiency is especially critical for businesses that rely on large-scale heating systems, where reducing energy waste can translate into substantial savings. 5. Easy Installation and Maintenance Unlike some other types of heating elements, tubular heaters are straightforward to install and maintain. Their design makes them easy to integrate into existing systems, and maintenance is relatively simple: Quick installation: Due to their modular design, they can be easily added to a system without significant changes. Low-maintenance: With proper care, they require minimal upkeep, lowering operational downtime. The simplicity of both installation and maintenance makes them a practical choice for both residential and industrial applications. Final Words From consistent heat distribution to ease of installation, tubular heaters provide a range of benefits that make them indispensable in various applications. Whether you’re looking for an energy-efficient heating solution or need a durable, long-lasting heating element, a tubular heater is a wise investment. Their versatility across industries, combined with low maintenance and cost-effectiveness, ensures that they remain one of the best choices for heating needs.
5 Top Benefits of a Silicone Rubber Heater
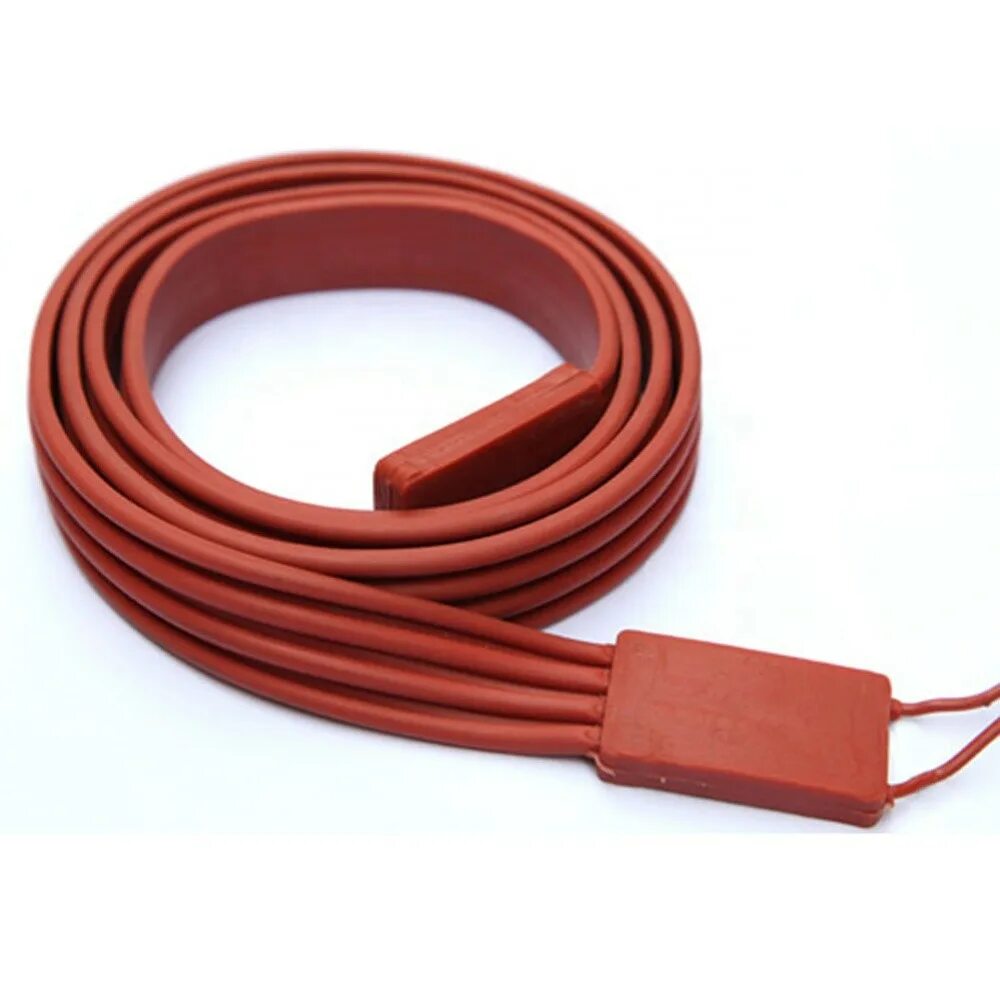
A silicone rubber heater stands out as a versatile and efficient heating solution across industries. Known for its flexibility and durability, it delivers reliable performance in diverse applications, from medical devices to aerospace. This heater type combines innovative materials and technology to provide precise temperature control, essential for critical processes. Here are the top benefits that make a silicone rubber heater an indispensable tool for industries. 1. Flexibility in Design and Application Silicone rubber heaters offer unmatched design flexibility. Their lightweight and thin construction allow them to be custom-made to fit complex surfaces, enabling precise heating in applications that require intricate shapes. Custom Shapes and Sizes: These heaters can be tailored to match unique contours, such as irregular or cylindrical surfaces. Ease of Installation: Adhesive backing or vulcanized attachments make them easy to integrate into equipment. This flexibility is especially beneficial in industries like medical diagnostics, where equipment demands heating precision without adding bulk. 2. Superior Temperature Control and Uniform Heat Distribution Consistency is critical when it comes to industrial heating. A silicone rubber heater ensures uniform heat distribution, eliminating cold spots that could disrupt operations. Temperature Range: These heaters operate efficiently between -60°C to 230°C, accommodating a variety of industrial needs. Integrated Sensors: Many silicone rubber heaters come with built-in thermocouples or RTDs for accurate temperature monitoring. Such precise control is invaluable in processes like 3D printing, where consistent heat directly impacts product quality. 3. Exceptional Durability in Challenging Environments Harsh environments demand robust heating solutions. Silicone rubber heaters excel in such conditions due to their resilient materials. Moisture and Chemical Resistance: The silicone outer layer protects the heater from water, oil, and chemical damage, making it ideal for food processing and pharmaceutical applications. Mechanical Toughness: Their durability ensures they can withstand repeated flexing and mechanical stress without compromising functionality. This resilience contributes to longer service life, reducing downtime and replacement costs. 4. Energy Efficiency and Cost-Effectiveness Silicone rubber heaters are designed for energy efficiency. They generate heat precisely where needed, reducing energy wastage. Low Thermal Mass: Their thin construction enables rapid heating and cooling, which lowers energy consumption. Localized Heating: They eliminate the need for heating entire systems, focusing on specific areas to improve efficiency. This efficiency not only reduces operational costs but also minimizes the carbon footprint, aligning with modern sustainability goals. 5. Wide Range of Industrial Applications The adaptability of silicone rubber heaters extends their use across numerous industries, such as: Medical: Pre-heating diagnostic devices and ensuring consistent performance in imaging equipment. Aerospace: De-icing components and maintaining optimal temperatures in sensitive avionics. Automotive: Warming batteries in electric vehicles for enhanced performance during colder climates. Electronics: Protecting sensitive components from temperature fluctuations. Their versatility makes them a go-to solution for industries that demand precision and reliability. Final Words A silicone rubber heater is not just a heating element; it’s a strategic asset for industries requiring precision, durability, and efficiency. From customized designs to consistent performance in harsh environments, these heaters cater to the most demanding applications. Their role in improving operational efficiency and reducing costs makes them indispensable for modern industrial processes.
5 Best Uses of a Thermocouple
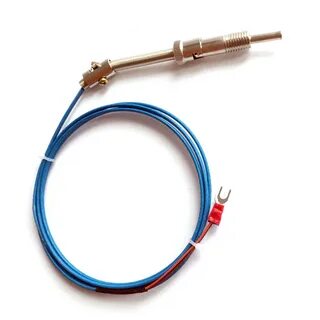
A thermocouple is one of the most reliable and widely used temperature measurement tools in industrial and scientific applications. Its ability to measure extreme temperatures with accuracy makes it indispensable. From manufacturing to energy management, thermocouples serve as critical components in systems where temperature control is vital. This article will uncover unique and specific ways a thermocouple is transforming operations across industries. 1. Industrial Temperature Monitoring In manufacturing and heavy industries, thermocouples are essential for accurate temperature control: Steel and Metal Processing: Thermocouples are used to monitor high-temperature furnaces, ensuring metals like steel and aluminum achieve their desired properties during processing. Chemical Manufacturing: Precise temperature readings are critical during chemical reactions to avoid process failures or unsafe outcomes. Industries requiring temperatures above 1,800°F rely heavily on thermocouples because of their durability and capability to handle extreme conditions. 2. Power Generation Systems Thermocouples play a critical role in energy management and power generation: Gas Turbines: In power plants, thermocouples measure turbine temperatures to optimize performance and prevent overheating. Boiler Systems: Temperature feedback ensures that boilers maintain the required steam pressure for efficient power generation. By providing real-time data, thermocouples contribute to the efficiency and safety of energy systems, minimizing downtime and potential hazards. 3. Food Processing and Safety The food industry depends on thermocouples for maintaining the safety and quality of products: Cooking and Pasteurization: Thermocouples are used to verify that food reaches the right internal temperatures to eliminate harmful bacteria. Cold Storage Monitoring: Low-temperature thermocouples ensure food stays within the safe range during storage and transport. With foodborne illnesses a major concern globally, thermocouples ensure compliance with safety standards and help prevent contamination. 4. Medical and Laboratory Applications Thermocouples are integral in the healthcare and scientific research sectors: Sterilization Equipment: Autoclaves use thermocouples to monitor high-temperature steam sterilization processes. Cryogenics: Thermocouples measure ultra-low temperatures in applications like organ preservation and vaccine storage. In laboratories, thermocouples support experiments requiring exact temperature settings, ensuring consistent and repeatable results. 5. Automotive and Aerospace Industries Modern vehicles and aerospace systems depend on thermocouples for efficiency and safety: Engine Testing: Thermocouples monitor internal engine temperatures to enhance performance and reduce emissions. Aircraft Safety: In aviation, thermocouples measure temperatures in jet engines and exhaust systems to ensure optimal operation under extreme conditions. With the growing focus on sustainability, thermocouples are helping manufacturers meet stringent efficiency standards. Why Thermocouples Are Essential Thermocouples are valued for their: Wide Temperature Range: Capable of measuring from -200°C to over 2,000°C, they are versatile across applications. Durability: They function reliably in extreme environments, from industrial furnaces to cryogenic systems. Cost-Effectiveness: With simple construction and high reliability, thermocouples are economical for long-term use. Final Words Thermocouples are much more than temperature sensors; they are enablers of efficiency, safety, and quality across industries. Their ability to withstand extreme conditions while providing accurate data makes them indispensable. Whether in manufacturing, food safety, or aerospace, thermocouples ensure processes run smoothly and products meet the highest standards.
How to Clean a Ceramic Radiant Tube Heater?
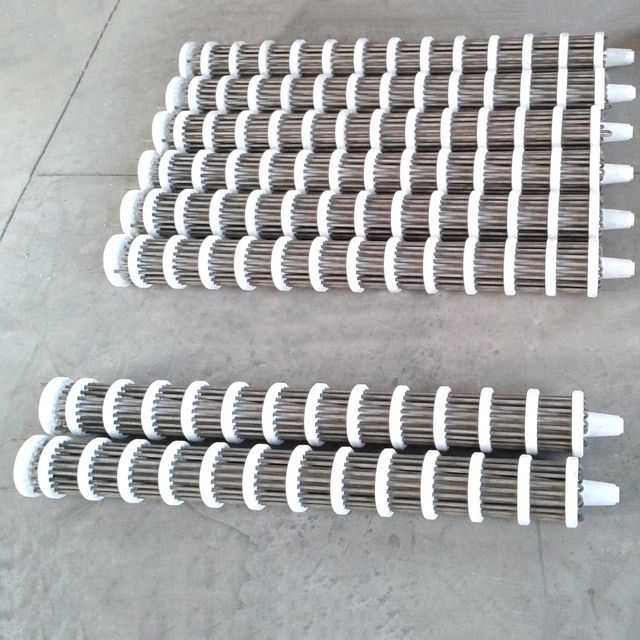
A ceramic radiant tube heater is a reliable choice for efficient heating in various industrial and residential settings. However, neglecting regular maintenance can reduce its efficiency and lifespan. Proper cleaning not only ensures optimal performance but also minimizes energy consumption and potential safety hazards. This step-by-step guide will help you clean your radiant tube heater effectively while protecting its delicate components. Why Cleaning a Ceramic Radiant Tube Heater Is Crucial Dust, dirt, and carbon build-up can accumulate on the surface of your ceramic radiant tube heater over time. These deposits obstruct heat transfer, leading to: Reduced heating efficiency Higher energy bills Increased wear and tear on the heating element Potential fire hazards due to overheating A regular cleaning schedule ensures the heater operates at peak performance and lasts longer. Tools and Materials You’ll Need Before starting, gather the following essentials: Soft-bristle brush (non-abrasive to avoid damaging the ceramic surface) Microfiber cloth (to prevent scratches) Vacuum cleaner with a hose attachment Isopropyl alcohol (for stubborn stains or grease) Compressed air canister (optional, for hard-to-reach areas) Protective gloves (to avoid direct contact with debris or cleaning agents) Safety Precautions Before Cleaning Safety should always come first. Follow these steps before cleaning your ceramic radiant tube heater: Turn off the heater and unplug it from the power source. Allow the heater to cool completely to avoid burns. Wear protective gloves to handle components safely. Read the user manual for any specific cleaning instructions or warnings. Step-by-Step Cleaning Guide 1. Remove Surface Dust and Debris Start by cleaning visible dirt: Use a soft-bristle brush to gently loosen dust on the ceramic elements and surrounding areas. Employ a vacuum cleaner with a hose attachment to remove loosened debris. If the heater has a grille or vent, clean it thoroughly with the brush. 2. Clean the Ceramic Surface The ceramic surface is delicate and requires careful handling: Dampen a microfiber cloth with isopropyl alcohol. Wipe the surface gently to remove stains or grease. Avoid soaking the cloth to prevent moisture from seeping into electrical components. 3. Inspect and Clean the Heating Element Examine the heating element for dirt or residue: Use a compressed air canister to blow away any debris from tight spaces. If accessible, lightly brush the element with a soft-bristle brush. 4. Check Ventilation Areas Clogged ventilation can impact the heater’s efficiency: Vacuum or wipe down vents and air intake areas. Ensure no obstructions remain that could block airflow. Maintenance Tips to Extend the Life of Your Heater Clean every three months if the heater operates in dusty or greasy environments. Inspect the heater for wear or damage during each cleaning session. Store the heater in a dry, dust-free environment when not in use. Replace worn-out parts, such as grilles or filters, to maintain performance. FAQs About Ceramic Radiant Tube Heater Cleaning How often should I clean my ceramic radiant tube heater? Clean it every 3–6 months, depending on usage and environmental conditions. Can I use water to clean the heater? Avoid using water directly. Instead, use a damp microfiber cloth to clean surfaces safely. What if my heater still smells after cleaning? A lingering smell may indicate deeper issues. Contact a professional for inspection. Final Thoughts Regular cleaning of your ceramic radiant tube heater is a simple yet essential task. It ensures efficiency, enhances safety, and prolongs the device’s lifespan. By following these detailed steps and maintenance tips, your heater will deliver consistent performance for years to come. Keep your heating system in top condition, and enjoy its benefits without unnecessary downtime or costs.
What are the Types of Cartridge Heater With Thermocouple
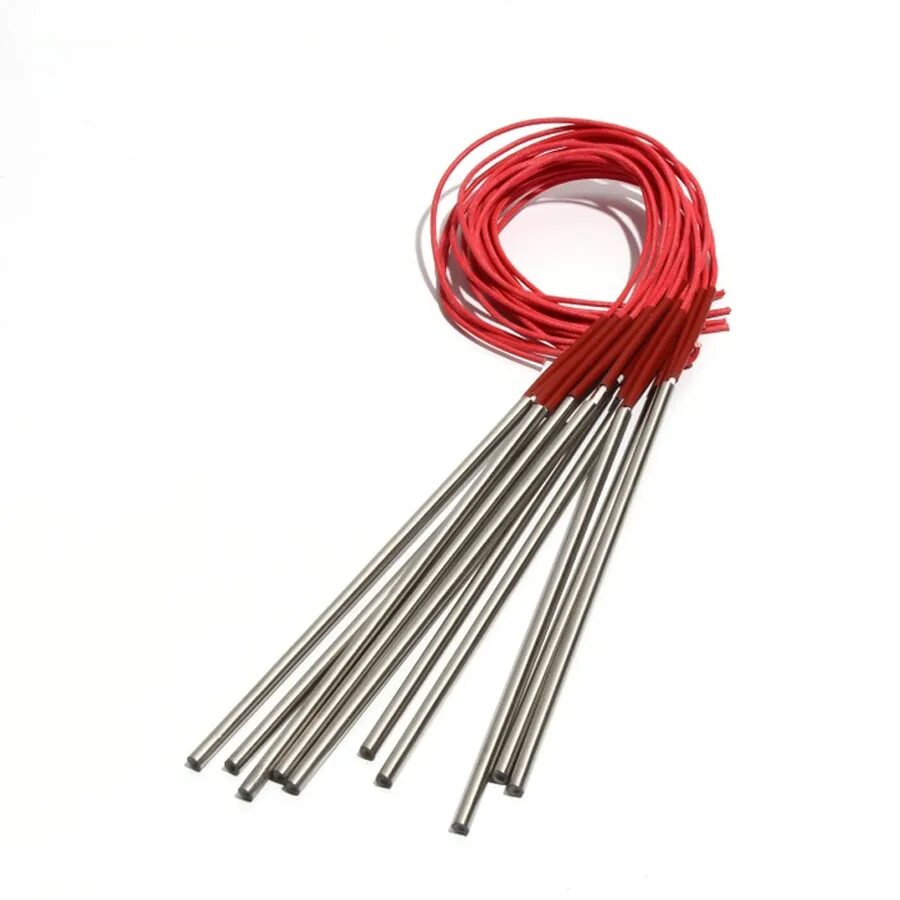
Industrial heating systems demand precision, and a cartridge heater with thermocouple is one of the most reliable tools for the job. This combination provides consistent heat delivery and accurate temperature monitoring, essential for various industrial applications. From manufacturing to food processing, understanding the types of a cartridge heater with thermocouple can help you choose the right solution for your operations. Why Combine a Cartridge Heater with a Thermocouple? The integration of a thermocouple in a cartridge heater enhances temperature regulation. This feature is critical in applications requiring precise heat control. It ensures that materials are neither overheated nor under-processed, protecting equipment and ensuring consistent production outcomes. Key benefits include: Real-Time Temperature Monitoring: Thermocouples provide instant feedback on temperature fluctuations. Energy Efficiency: By preventing overheating, this system reduces energy waste. Process Optimization: Industries like plastic molding and pharmaceutical manufacturing benefit from controlled heating environments. Let’s examine the different types of cartridge heaters with thermocouples and their applications. 1. Standard Cartridge Heater With Thermocouple This is the most common type used across industries. It features an integrated thermocouple, often placed internally or externally, depending on the application. Internal Thermocouple: Placed inside the heater for direct measurement of core temperature. This is ideal for high-precision tasks like scientific instrument heating. External Thermocouple: Positioned outside the heater for surface temperature monitoring. Commonly used in metalworking and packaging machinery. The versatility of these heaters makes them suitable for both low-watt density and high-watt density applications. 2. Swaged Cartridge Heater With Thermocouple Swaged heaters are designed for high-performance applications. These heaters are built with compacted insulation, which enhances heat transfer and durability. Advantages: High Watt Density: Can deliver significant heat within small spaces. Durability: Resistant to vibration and thermal cycling, making it perfect for automotive manufacturing. The thermocouple in these heaters ensures tight temperature control, critical for minimizing material waste. 3. Split Cartridge Heater With Thermocouple Split cartridge heaters offer flexibility and easy installation. Their design allows them to expand or contract, ensuring a secure fit in varying diameters. Key Applications: Injection Molding: Perfect for maintaining consistent temperatures in molds. Food Processing: Ensures uniform heat for tasks like sealing and cooking. The embedded thermocouple provides accurate temperature readings, helping maintain product quality. 4. Miniature Cartridge Heater With Thermocouple Compact but powerful, miniature cartridge heaters are ideal for applications with limited space. Despite their small size, they deliver precise heating and temperature control. Best For: Medical Equipment: Used in devices requiring delicate heat control. 3D Printing: Ensures stable heating in intricate printing components. Thermocouples integrated into these heaters ensure the accuracy needed for sensitive tasks. Choosing the Right Cartridge Heater With Thermocouple When selecting a heater, consider the following: Application Requirements: High-precision industries like aerospace demand swaged heaters, while food processing may need split designs. Temperature Range: Evaluate the maximum and minimum temperatures needed for your processes. Installation Space: Miniature heaters are ideal for tight spaces, while standard options fit broader applications. Final Words A cartridge heater with thermocouple offers unmatched precision, durability, and versatility. Whether it’s for manufacturing, medical, or food processing, understanding the various types can optimize your processes and improve operational efficiency.