5 Unique Features of a Pipeline Heater
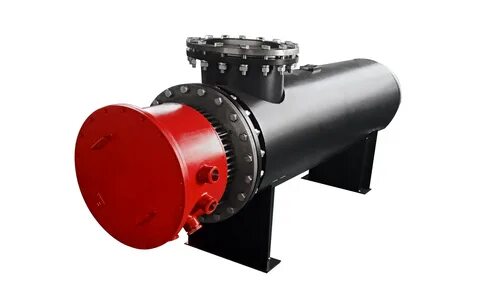
A pipeline heater plays a crucial role in industries that require precise temperature control for the transportation of liquids or gases. From preventing material blockages to ensuring efficient flow, these heaters provide unmatched reliability in challenging environments. Their innovative design and advanced features make them a valuable asset across industries such as oil and gas, chemical processing, and food production. Below are the five unique features of a pipeline heater that set it apart. 1. Exceptional Heat Uniformity Uniform heating is a critical requirement in pipelines, as inconsistent temperatures can lead to blockages and material degradation. Pipeline heaters are designed to deliver consistent heat distribution throughout the pipeline, ensuring smooth operation. Even Heat Transfer: The heaters are engineered to avoid hot or cold spots, critical for materials sensitive to temperature changes. Custom Heating Elements: Many models include heating elements tailored to the pipeline’s material and fluid type, enhancing overall performance. Energy Efficiency: Uniform heating prevents energy waste, reducing operating costs. Industries like chemical manufacturing benefit greatly from this feature as it prevents chemical reactions caused by temperature inconsistencies. 2. High-Temperature Capability Pipeline heaters are built to handle extreme temperatures, making them ideal for demanding applications. Many heaters can achieve operating temperatures above 500°F (260°C), essential for high-temperature processes. Thermal Stability: They maintain consistent output even during temperature fluctuations. Material Compatibility: High-temperature models are compatible with a range of materials, including viscous fluids and heavy oils. In oil and gas pipelines, this feature ensures smooth transportation of crude oil, which often requires elevated temperatures to flow efficiently. 3. Corrosion Resistance for Longevity Pipelines often transport substances that are chemically reactive or corrosive. A key feature of modern pipeline heaters is their corrosion-resistant construction, which ensures long-term durability. Protective Sheathing: Most heaters use materials like stainless steel or Inconel to resist corrosion. Chemical Resistance: Specialized coatings can handle aggressive chemicals and harsh environments. This durability minimizes maintenance costs and prevents unexpected downtime, especially in industries like pharmaceuticals and water treatment. 4. Built-In Safety Mechanisms Safety is paramount in industrial applications, and pipeline heaters incorporate robust features to protect equipment and personnel. Overheat Protection: Sensors detect abnormal temperatures and shut down the system to prevent damage. Explosion-Proof Designs: Heaters in hazardous environments, such as refineries, are engineered to prevent explosions. Leak Detection Systems: Advanced models include systems to identify leaks and immediately alert operators. These safety features make pipeline heaters reliable for high-risk environments, ensuring compliance with industry standards. 5. Customizable Configurations for Versatility Pipeline heaters can be customized to meet the specific needs of any application. This versatility allows them to perform seamlessly across various industries. Size and Wattage Options: They come in a wide range of sizes and power outputs to suit different pipeline lengths and capacities. Fluid-Specific Designs: Heaters can be optimized for transporting oils, gases, or chemicals. Remote Monitoring: Many models now include IoT-enabled systems for real-time monitoring and control. For industries like food production, this adaptability ensures precise temperature control, maintaining product quality and safety. Wrap Up A pipeline heater ensures operational efficiency and product integrity in industries dependent on fluid transportation. Their ability to deliver consistent heat, withstand harsh conditions, and adapt to various needs makes them a must-have solution. By investing in a high-quality pipeline heater, industries can reduce downtime, lower energy costs, and enhance overall productivity.
5 Benefits of a Hot Runner Heater
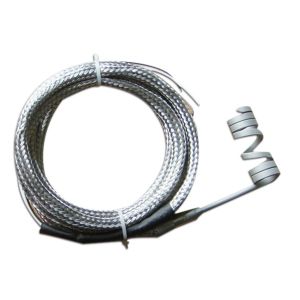
A Hot Runner Heater is critical in industries that rely on injection molding for mass production. Its precise heating capability ensures consistent material flow, reducing waste and improving efficiency. Industries such as automotive, consumer goods, and electronics depend on these systems to meet the growing demand for high-quality products. Here are five key benefits of using a hot runner heater in industrial applications. 1. Enhanced Production Efficiency A hot runner heater is designed to optimize production processes, particularly in injection molding. By keeping the material in a molten state, it minimizes interruptions during molding cycles. Reduced Cycle Times: Materials flow seamlessly through the system, speeding up production cycles. Consistent Flow: Unlike traditional systems, hot runner heaters maintain uniform temperature, ensuring smooth material movement without clogs. This improvement in efficiency directly impacts production output, making it a must-have for large-scale operations. 2. Improved Product Quality Uniform heating is crucial for producing defect-free products. Hot runner heaters excel in maintaining consistent temperatures across all molding cavities. No Cold Spots: The heater eliminates temperature fluctuations, preventing uneven material cooling. Precise Mold Filling: It ensures every cavity is filled correctly, reducing material voids and imperfections. With better temperature control, manufacturers produce higher-quality products with minimal defects. 3. Significant Material Savings Traditional injection molding systems often waste material due to runner scraps. Hot runner heaters eliminate this issue entirely. No Runner Scrap: As the system keeps the material molten, there’s no leftover runner waste. Lower Resin Consumption: Manufacturers save on raw material costs, especially for expensive resins. This reduction in waste directly contributes to lower production costs, making operations more sustainable. 4. Flexibility in Design Hot runner heaters allow for more complex product designs, opening up possibilities for advanced manufacturing. Supports Multi-Cavity Molds: The heaters work efficiently with molds that have multiple cavities, ensuring consistent heating for intricate designs. Improved Aesthetics: By eliminating weld lines and cold slugs, products have a smoother finish. This flexibility is particularly beneficial for industries such as electronics and medical equipment, where precision is paramount. 5. Long-Term Cost Efficiency Although the initial investment for a hot runner system may be higher, the long-term savings are substantial. Reduced Maintenance Costs: The system requires less maintenance compared to cold runner setups, saving time and money. Energy Efficiency: Hot runner heaters are energy-efficient, consuming less power while maintaining optimal performance. Over time, these factors lead to significant operational savings, boosting profitability. Last Word A Hot Runner Heater is more than a heating element; it’s a cornerstone of modern injection molding. Its ability to enhance efficiency, improve quality, save materials, support intricate designs, and reduce long-term costs makes it an invaluable tool for manufacturers. For industries looking to scale production while maintaining quality, hot runner heaters offer a reliable and cost-effective solution.
3 Reasons Why Industries Need High Temperature Cable
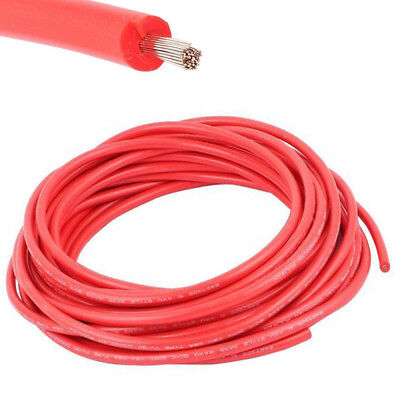
The industrial sector demands reliable and robust components, especially in extreme temperature settings. One crucial element that powers this reliability is the high temperature cable. From manufacturing to aerospace, high-temperature cables are essential for maintaining safety, efficiency, and durability in rigorous conditions. In this article, we’ll uncover the top reasons why a high temperature cable is indispensable for industry, supported by the latest data and insights. 1. Superior Heat Resistance Ensures Safety and Reliability One of the primary benefits of using high temperature cable in industrial settings is its ability to withstand extreme heat while maintaining safe and reliable operation. In environments where temperatures regularly exceed 250°C (482°F), regular cables would degrade or fail, posing severe safety risks. High-temperature cables, however, are engineered for these conditions, making them indispensable for high-stress applications: Enhanced Safety: High-temperature cables prevent fires and system failures by maintaining insulation integrity in high-heat environments. Industries like steel production and oil refineries rely on these cables to prevent accidents caused by cable breakdown. Reliable Operation: Even at peak loads, these cables don’t overheat or degrade, ensuring continuous and safe operations. A study by Grand View Research reports that the global high-temperature cable market is projected to grow at a CAGR of 4.1% from 2023 to 2030, driven largely by the demand for fire-resistant solutions in industrial settings. For facilities operating around-the-clock, high-temperature cables are a critical investment that pays off in both safety and performance. 2. Exceptional Durability Reduces Maintenance Costs Industrial applications demand cables that can withstand not only heat but also wear, abrasion, and exposure to chemicals. High-temperature cables meet these demands with durable materials such as silicone, fiberglass, and PTFE insulation: Extended Cable Lifespan: High-temperature cables offer increased resistance to wear and tear, extending the lifespan of the wiring systems. This reduces the frequency and costs associated with replacements. Low Maintenance: Industries can expect reduced downtime due to cable failures. In fact, maintenance teams report an average reduction of 25% in cable-related issues after switching to high-temperature cables, according to data from market research firm Mordor Intelligence. For industries like automotive manufacturing and food processing, where high temperatures and heavy machinery wear down equipment, these cables provide a cost-effective and low-maintenance solution. 3. Versatile Applications Across Multiple Sectors High-temperature cables are widely adaptable and are used in various industrial sectors due to their flexibility and compatibility with different environments. Here are a few examples of how these cables benefit specific industries: Aerospace: With extreme conditions in aircraft and spacecraft, high-temperature cables are necessary to ensure electrical systems remain functional even during intense heat and pressure. Petrochemical Industry: Refineries and chemical plants need cables that withstand both high temperatures and exposure to corrosive substances. High-temperature cables provide both qualities, protecting critical equipment and reducing environmental risks. Renewable Energy: In solar power plants, high-temperature cables are essential for handling elevated temperatures in PV systems, allowing consistent energy transfer without degradation. These diverse applications highlight how high-temperature cables are tailored to meet specific industrial needs, making them vital in maintaining operational efficiency and worker safety. Advantages of Using High Temperature Cables in Industry In summary, high-temperature cables provide numerous advantages, including: Enhanced Safety: Reduce risks of fire and insulation failure. Cost-Effectiveness: Lower maintenance and replacement costs. Broad Applicability: Suitable for diverse and high-demand sectors. Final Thoughts Investing in high temperature cable solutions is more than just meeting industry standards—it’s about securing reliable and durable connections that enhance productivity and safety across sectors. For any industrial operation facing extreme conditions, high-temperature cables prove essential to maintaining efficiency and minimizing risks.
What is a Heating Cable – A Short Guide
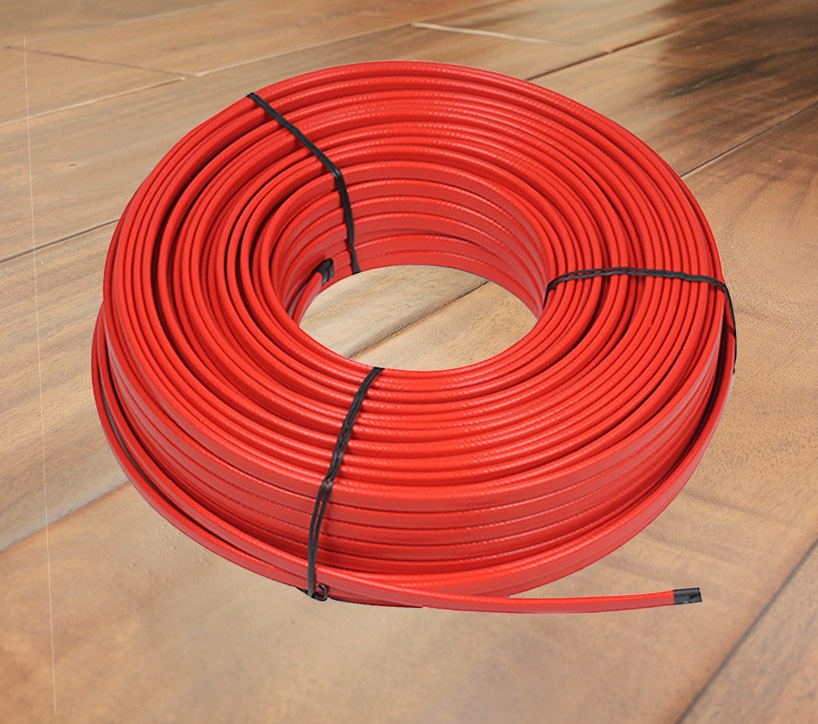
In cold environments, pipes and equipment are at risk of freezing, which can lead to costly damage and hazardous conditions. Heating cable provides a reliable, efficient solution to this problem. Designed to maintain consistent temperatures, heating cables are essential in industries and homes that need to prevent freeze-ups, ensure safety, and maintain smooth operations. In this guide, we’ll explore the uses, types, and benefits of heating cables. Understanding Heating Cable A heating cable is an electrical cable with a built-in heating element that transfers heat directly to pipes, surfaces, or spaces where temperature control is critical. Commonly used in industrial, commercial, and residential settings, heating cables come in various types designed for specific applications, each with unique properties and capabilities. Heating cables not only protect pipes but are also used for de-icing, snow melting, and maintaining specific temperatures in industrial processes. Types of Heating Cable Heating cables are categorized based on how they produce and maintain heat. Here are the most common types: Self-Regulating Heating Cables These cables adjust their heat output depending on the surrounding temperature. They’re energy-efficient, providing more heat when it’s colder and reducing output when the environment warms. Ideal for freeze protection in pipes and roof de-icing. Minimal risk of overheating, as they naturally decrease power in warmer conditions. Constant Wattage Heating Cables These cables supply a consistent level of heat regardless of temperature variations. Often used in applications that require a stable temperature. Suitable for industrial applications where precise heat maintenance is essential. Series Resistance Heating Cables Designed for long lengths, these cables use a specific resistance value to generate heat. Often found in petrochemical and oil facilities for freeze protection and process maintenance. Require careful installation, as their length must match the application to ensure safety. Key Benefits of a Heating Cable Heating cables offer numerous advantages across multiple settings: Pipe Protection: Prevents pipe bursts and flow obstructions in freezing temperatures, saving money on repairs and replacement. Roof and Gutter De-Icing: Keeps gutters and roof edges clear of ice dams, which can damage structures. Snow Melting for Driveways: Offers a safe, slip-free environment by melting snow and ice on outdoor surfaces. Industrial Temperature Maintenance: Maintains necessary temperatures in sensitive industrial processes, ensuring product consistency and safety. Installation and Safety Tips Proper installation is crucial for heating cables to function safely and effectively. Here are a few tips: Avoid Overlapping: Overlapping heating cables can cause overheating and damage the insulation. Always follow the manufacturer’s guidelines. Use Appropriate Insulation: Proper insulation helps heating cables perform efficiently, especially in freezing environments. Monitor and Test Regularly: Periodic checks ensure the cables are in good working condition and reduce the risk of unexpected failure. Final Words Heating cables are a powerful tool for maintaining temperature control in a wide range of applications. Whether you need to protect pipes, prevent ice buildup, or sustain specific temperatures in industrial processes, selecting the right heating cable can offer durability, efficiency, and safety. Reliable providers like Cheri Heater offers a range of heating cables tailored to meet both residential and commercial needs, ensuring your systems stay safe and operational in any environment.
How to Select the Right Cartridge Heater
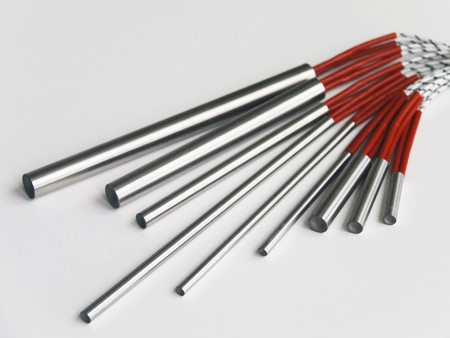
Choosing the right cartridge heater can make a significant difference in achieving optimal heating efficiency for various industrial applications. These heaters are known for their compact design, precise heating, and efficiency, making them essential in industries such as plastic manufacturing, packaging, and medical equipment. However, with a range of options available, finding the right fit can be challenging. In this guide, we’ll discuss key factors to select the right cartridge heater to help you make an informed choice. 1. Understand Your Application’s Temperature Requirements Each application has a unique temperature range and heating duration requirement. A heater that’s too powerful or not powerful enough could lead to uneven heating or even system failure. Here’s what to consider: Max Operating Temperature: Cartridge heaters can operate at temperatures as high as 1400°F (760°C), but always confirm the max operating limits for your application. Thermal Transfer Efficiency: Ensure the heater has optimal heat transfer properties to match the material’s conductivity. Temperature Control Precision: Applications with strict tolerances require heaters that can maintain steady temperatures. 2. Consider the Heater’s Watt Densityof Your Cartridge Heater Watt density (W/in²) is crucial as it determines the heater’s power in relation to its surface area. Selecting the right watt density impacts the heater’s longevity and performance: Low Watt Density (10-30 W/in²): Best for applications needing gentle heat, like food equipment. Medium Watt Density (30-50 W/in²): Ideal for plastics and rubber manufacturing. High Watt Density (50+ W/in²): Suitable for high-temperature applications such as mold heating and metal processing. A miscalculated watt density can lead to excessive heating or premature burnout, so be clear on your application’s needs. 3. Select the Right Sheath Material The heater’s sheath is the outer layer that directly affects its durability and compatibility with the surrounding environment. Common sheath materials include: Stainless Steel: Highly resistant to corrosion and suitable for food and medical industries. Incoloy: Ideal for extreme temperatures and corrosion-prone environments. Nickel: Great for high-conductivity applications where rapid heat transfer is essential. 4. Determine the Proper Diameter and Length of Your Cartridge Heater Your cartridge heater must fit precisely within the drilled holes or mounting points to ensure efficient heat transfer. Measure accurately: Diameter: Ensure a snug fit; the diameter should ideally be 0.002-0.003 inches smaller than the drilled hole. Length: Choose a length that optimally covers the heat transfer area. 5. Ensure Proper Voltage and Power Compatibility Confirm that the heater’s voltage matches the power supply in your facility. Mismatched voltage can lead to inadequate heating or damage to the heater and connected systems. Single-Phase or Three-Phase Options: Industrial heaters often come in both options. Match your facility’s electrical setup. Adjustable Voltage Options: If your application requires variable temperatures, consider heaters that allow for adjustable voltage. 6. Evaluate Lead Type and Exit Options Cartridge heaters offer various lead configurations to suit different environments and handling needs: Flexible Lead Wire: Good for applications with movement; check insulation to withstand high temperatures. Right-Angle Leads: Saves space in compact setups; prevent bending stress. Swaged Leads: Best for high-vibration environments to prevent breakage. Final Words When choosing a Cartridge Heater, reliability and durability should be priorities. Partner with reputable manufacturers like Cheri Heater who offer quality certifications and testing guarantees to ensure longevity and performance.
What is a Band Heater – A Short Guide
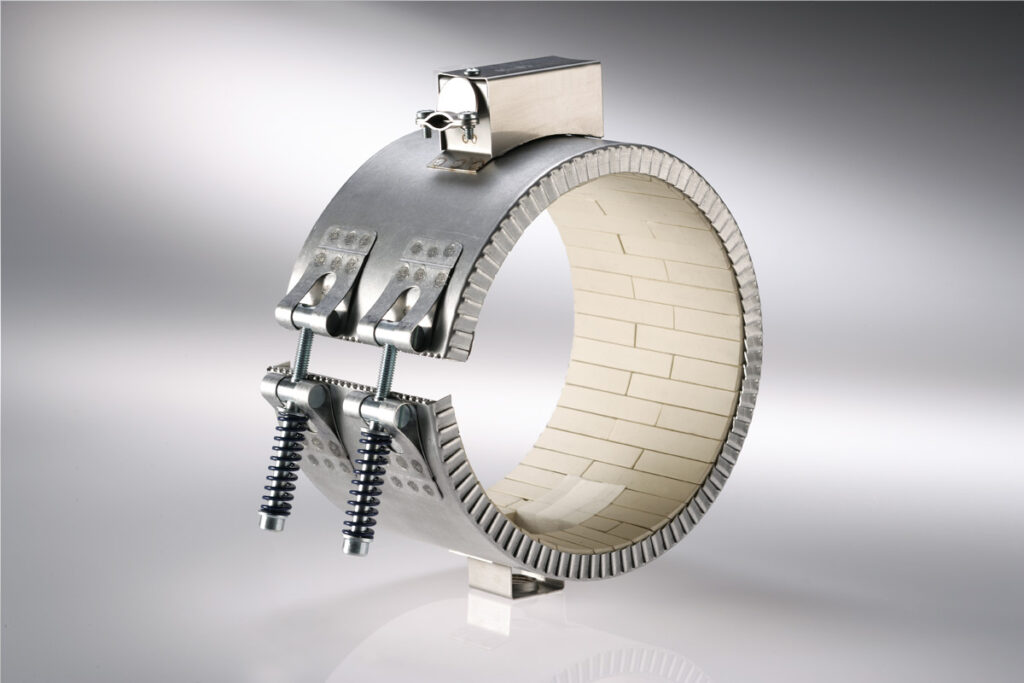
In industrial applications, maintaining precise temperatures is critical. Whether it’s for plastic extrusion, injection molding, or other manufacturing processes, consistent heat is necessary for quality and efficiency. This is where a band heater becomes essential. As one of the most effective heating tools, a band heater offers controlled heat exactly where it’s needed, making it indispensable in many industrial settings. In this guide, we’ll break down what a band heater is and why it’s crucial for numerous applications. What is a Band Heater? A band heater is a heating device primarily designed to encircle cylindrical parts, such as pipes, barrels, or nozzles, and generate heat for processes requiring uniform thermal distribution. It’s essentially a “belt” heater, wrapping around the cylindrical surface to maintain or elevate its temperature. Band heaters are widely used in various industries, including plastics, chemical processing, and food manufacturing. How Does a Band Heater Work? Band heaters operate through electrical resistance. When an electric current passes through the heater’s resistive element, heat is produced. This heat then transfers from the band heater to the external surface of the cylinder or pipe it encases. The key components in a band heater include: Heating Element: Often made from nickel-chromium (Ni-Cr) wire, which converts electric current into heat. Insulation: Reduces heat loss, ensuring efficient energy transfer to the target area. Outer Sheath: Protects the heater and user from exposure to the heating element. It’s usually made from materials like stainless steel or mica. Advantages of Using a Band Heater Using a band heater offers several benefits in industrial applications. Here’s why they are preferred for precision heating: Energy Efficiency: Band heaters are designed to transfer heat directly to the surface they are wrapped around, minimizing energy loss. Even Heat Distribution: The cylindrical shape ensures that heat is spread evenly, which is crucial for maintaining product quality. Precise Temperature Control: Advanced band heaters allow for highly specific temperature adjustments, enabling efficient and consistent heating. Space-Saving Design: Their compact form means they don’t require extensive installation space, making them suitable even for confined areas. How to Choose the Right Band Heater Selecting the appropriate band heater for your application can significantly impact energy efficiency and performance. Consider these factors: Temperature Requirements: Choose a heater type (mica, ceramic, mineral-insulated, or silicone) based on the temperature range required. Size and Fit: Ensure the band heater fits securely around the cylinder or pipe to prevent heat loss. Environmental Conditions: If the environment is prone to moisture, a silicone band heater may be best due to its moisture resistance. Durability: For heavy-duty applications, mineral-insulated heaters offer the highest durability and performance. Maintaining Your Band Heater for Optimal Performance Routine maintenance of band heaters can extend their lifespan and ensure continuous efficiency. Here are some best practices: Inspect Regularly: Check for signs of wear, corrosion, or damaged insulation. Clean Periodically: Remove any dust or residue on the heater to prevent overheating. Secure Connection: Make sure electrical connections are tight and free from damage to avoid energy loss or electrical issues. Temperature Calibration: Regularly test the heater’s temperature accuracy to prevent overheating and ensure consistent performance. Final Words A band heater is indispensable for industrial applications requiring precise temperature management. For those considering reliable industrial heating solutions, band heaters present a smart investment to streamline processes while keeping costs manageable.