How to Choose the Right Heating Solution for Your Manufacturing Needs
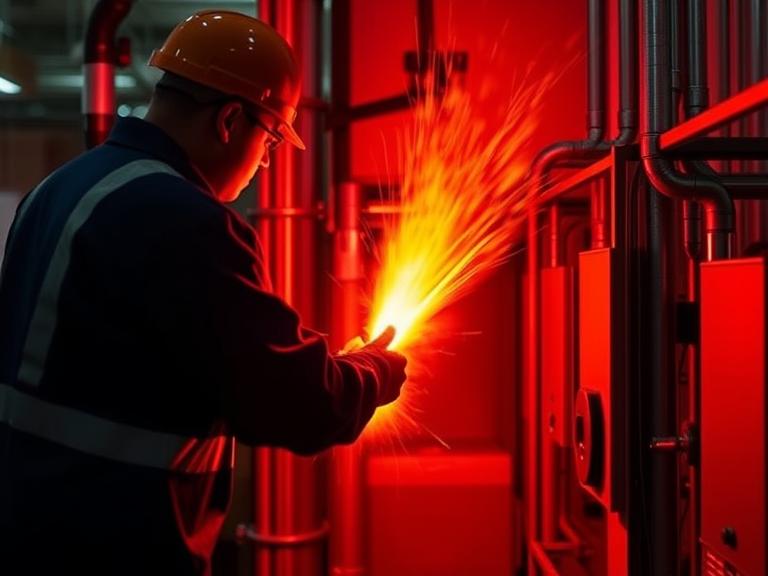
In the world of manufacturing, precision, efficiency, and consistency are essential. Whether you’re working with plastics, metals, chemicals, or food processing, heating systems are at the core of your operations. Choosing the right heating solution can significantly impact your productivity, energy consumption, and product quality. With so many technologies available—from cartridge heaters to infrared panels—how do you determine which one is right for your specific manufacturing needs? At Cheriheater, we specialize in helping manufacturers make informed decisions when it comes to industrial heating solutions. In this guide, we’ll walk you through the key factors to consider when choosing the most effective heating solution for your operation. 1. Understand Your Application Requirements The first step in choosing a heating solution is to thoroughly understand your application’s unique requirements. Every manufacturing process is different and demands specific parameters when it comes to: Temperature range: Some applications require precise, low-temperature control, while others may demand high heat. Heat-up time: Do you need rapid heat-up or is gradual warming acceptable? Material compatibility: Will the heater be in direct contact with your product or surrounding machinery? Environmental conditions: Is your process exposed to moisture, dust, or corrosive chemicals? Clearly identifying these requirements will help you narrow down which heating technologies are most suitable. 2. Evaluate the Type of Heater Needed There are several types of industrial heaters, each with unique benefits and ideal use cases. Some of the most common include: Cartridge Heaters These are compact, cylindrical heaters often used to heat metal blocks, molds, or tools. They offer high watt density and precise temperature control, making them ideal for applications like plastic molding or packaging machinery. Band Heaters Typically used to heat cylindrical surfaces such as pipes, nozzles, or drums. Band heaters are great for injection molding and extrusion equipment. Tubular Heaters These are versatile heaters that can be shaped into various configurations. Ideal for heating air, gases, and liquids, tubular heaters are often used in ovens, immersion tanks, and ducts. Infrared Heaters Perfect for non-contact heating, these are often used in curing, drying, and coating processes. Infrared heaters can offer energy savings and faster response times. Immersion Heaters Used for directly heating liquids, immersion heaters are common in chemical processing, water treatment, and oil heating applications. Matching the heater type to your process needs will ensure efficiency and longer operational life. 3. Assess Power Requirements and Energy Efficiency Another critical factor is the power requirement. How much wattage do you need to achieve and maintain your desired temperature? Choosing a heater with the correct watt density (watts per square inch) is vital to prevent overheating or underperformance. In today’s energy-conscious environment, energy efficiency is more important than ever. Look for heating solutions that offer: Uniform heat distribution Fast response times Integrated temperature sensors or controllers Minimal heat loss to the environment Using advanced controls and sensors not only boosts efficiency but also enhances safety and reduces operating costs. 4. Consider the Control Systems A heating system is only as effective as its controls. Precision in temperature regulation is crucial for many industrial processes. Depending on your process, you might need: Basic thermostats Digital controllers with programmable settings PLC (Programmable Logic Controller) integration for complex automation Choosing the right control system helps maintain consistent temperature levels, reduces waste, and improves product quality. 5. Think About Installation and Maintenance Ease of installation and maintenance are often overlooked but can have long-term cost implications. When choosing a heating solution, ask the following: Is it easy to integrate with existing equipment? Are replacement parts readily available? What is the expected lifespan? Is maintenance frequent or minimal? Opting for heaters that are modular or easy to replace can reduce downtime during maintenance or unexpected failures. 6. Safety and Compliance Standards Industrial heating systems must comply with safety and regulatory standards. Make sure the heater and its components are: Certified by relevant bodies (e.g., CE, UL, RoHS) Designed with built-in safety mechanisms like thermal cutoffs or overload protection Made with materials that suit your industry’s compliance requirements (e.g., food-grade stainless steel) Safety should never be compromised, especially when working in high-temperature or hazardous environments. 7. Work with a Reliable Supplier or Manufacturer One of the most important decisions is choosing who to partner with. A trustworthy heating element manufacturer can provide tailored solutions, expert advice, and after-sales support. Customization is often key in manufacturing, and working with an experienced manufacturer ensures your heating system is designed to your exact specifications. Look for a supplier with a solid track record, client testimonials, and the ability to design, prototype, and produce heaters in-house. This ensures quality control, fast lead times, and scalable production. 8. Factor in Budget vs. Long-Term ROI While initial cost is a key consideration, it’s equally important to evaluate long-term return on investment (ROI). A cheaper heater may save money upfront but could lead to higher energy bills, frequent repairs, or poor process control. Instead, weigh the total cost of ownership: Initial purchase price Installation and integration costs Operating and energy costs Maintenance and downtime Lifespan and reliability Choosing the right heating solution can result in higher productivity, lower energy bills, and fewer equipment failures—making it a smart long-term investment. Conclusion: Selecting the right heating solution for your manufacturing process involves a careful evaluation of technical requirements, energy efficiency, safety, and vendor reliability. By following a structured decision-making process and consulting with experts, you can ensure that your heating system delivers optimal performance and value. At Cheriheater, we pride ourselves on offering high-quality, custom-designed heating solutions for a wide range of industrial applications. Whether you’re in plastics, packaging, chemicals, or food production, we’re here to help you choose the best heating technology for your unique needs. If you’re looking to optimize your heating process, improve energy efficiency, and enhance product quality, contact our team today to discuss your project requirements.
Different Types of Heaters for Industrial Applications
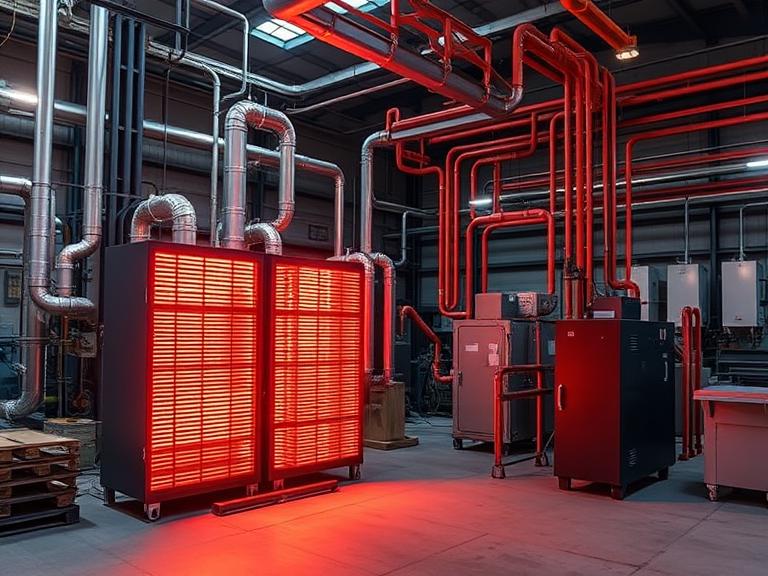
In industrial settings, heating solutions are crucial to ensuring smooth and efficient operations. Whether it’s for manufacturing, food processing, or other industrial processes, selecting the right type of heater can have a major impact on productivity and energy efficiency. With a wide range of options available, businesses must choose the best solution based on their specific needs. In this post, we will explore the various types of industrial heaters, discuss their benefits, and provide guidance on how to choose the best heater for your industrial application. 1. Electric Heaters: Versatile and Efficient Electric heaters are widely used in industrial applications due to their efficiency and precision. They convert electrical energy into heat, making them ideal for controlled environments where temperature regulation is critical. Types of Electric Heaters: Cartridge Heaters: One of the most common forms of electric heaters, cartridge heaters are compact, cylindrical heating elements that are often used in molds, tanks, and machinery requiring concentrated heat. These heaters are known for their high thermal efficiency and ease of integration into industrial systems. They are ideal when you need space-efficient solutions with precise heating control. Band Heaters: These heaters wrap around cylindrical surfaces, such as pipes or barrels, to provide even heat distribution. Commonly used in extrusion processes, they are ideal for operations where uniform heating is required. Why Choose Electric Heaters? Precise Control: Electric heaters, such as cartridge heaters, offer exceptional control, allowing for accurate temperature adjustments that are essential for many industrial processes. Energy Efficiency: They can heat spaces quickly without waste, making them a great choice for businesses aiming to minimize energy costs. Low Maintenance: Electric heaters typically require less maintenance compared to gas-powered models, contributing to lower operational costs. Electric heating solutions are ideal for companies that need reliable and easy-to-maintain heating systems for small or medium-sized applications. 2. Gas Heaters: Cost-Effective for Larger Spaces Gas heaters are commonly used in large industrial spaces where high heat output is necessary. They work by burning natural gas or propane to generate heat, making them more cost-effective for operations that need a significant amount of heat for large areas. Advantages of Gas Heaters: Lower Operating Costs: Gas-powered heaters tend to have lower operating costs when compared to electric heaters, especially for large-scale applications. High Heat Output: Gas heaters can produce a large amount of heat in a relatively short amount of time, making them ideal for large warehouses or production facilities. Versatility: They can be used in both indoor and outdoor applications, though proper ventilation is necessary for indoor use to avoid the accumulation of dangerous gases. While gas heaters are great for large spaces, they do require careful safety management and ongoing maintenance to ensure they function safely and efficiently. 3. Infrared Heaters: Ideal for Spot Heating Infrared heaters provide a unique heating solution by emitting infrared radiation to directly heat objects and surfaces, rather than heating the air around them. This makes infrared heaters especially useful for applications that require localized heating or when traditional convection heating would be inefficient. How Infrared Heaters Work: Infrared heaters emit radiation that directly heats objects in their line of sight. Unlike conventional heating systems that heat the air and rely on convection to spread warmth, infrared heaters focus on the target object, providing rapid heating with minimal energy waste. Applications of Infrared Heaters: Drying and Curing: Infrared heaters are widely used in industries like automotive and manufacturing for drying paint or curing materials. Food Processing: In food production, infrared heating is used for drying or cooking food products quickly and evenly. Why Use Infrared Heaters? Energy Efficient: Infrared heaters provide targeted heating, minimizing energy loss and increasing efficiency. Rapid Heating: Infrared heaters can heat objects almost instantly, reducing waiting times in high-speed production processes. Minimal Air Movement: Infrared heaters are ideal for processes that require minimal air movement, such as in cleanrooms or laboratory settings. Infrared heaters are an excellent option for industries that require quick and efficient spot heating in specific areas. 4. Immersion Heaters: Effective Heating for Liquids Immersion heaters are designed for heating liquids directly within tanks or other containers. This type of heater is commonly used in industries such as chemical processing, food production, and pharmaceuticals, where precise liquid heating is essential. How Immersion Heaters Work: Immersion heaters are placed directly into the liquid that needs to be heated. This direct contact between the heating element and the liquid ensures uniform and efficient heating. Advantages of Immersion Heaters: Direct Heating: Since the heater is submerged in the liquid, it directly heats the fluid, which leads to more efficient heating compared to external heating methods. Cost-Effective: Immersion heaters are often more affordable than other heating systems, making them a popular choice for many businesses. Versatility: They can be used to heat a wide variety of liquids, including water, oils, and chemicals. Immersion heaters are ideal for any industrial application that requires the heating of liquids, such as tanks or vats. 5. Choosing the Right Heater: Key Considerations When selecting the right heating solution for your industrial application, several key factors should be considered to ensure that the system you choose meets your operational needs effectively: 1. Space and Heating Area: For small, localized heating, cartridge heaters are an excellent choice, as they offer high efficiency in tight spaces. Larger spaces or areas requiring significant heat output may be better suited to gas heaters or infrared heating systems. 2. Energy Efficiency: If energy efficiency is a top priority, electric heaters, especially cartridge heaters, provide excellent performance with minimal waste. 3. Temperature Control Requirements: Electric heaters with precise temperature control are ideal for applications requiring constant, reliable heat, such as those in the manufacturing or pharmaceutical industries. 4. Maintenance and Safety: Electric heaters like cartridge heaters tend to require less maintenance than gas heaters. Consider the level of ongoing maintenance your business can handle when making a choice. 5. Application Type: For heating liquids, immersion heaters are the go-to solution. For large areas, gas or infrared heaters