How to Use a Flange Heater
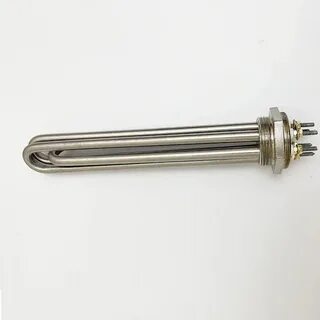
Precision matters when managing heat in industrial processes. Incorrect heating not only wastes energy but also risks damaging equipment. That’s where the flange tubular heater proves its worth. It’s engineered for reliability in high-demand environments such as tanks, reservoirs, and pressure vessels. But knowing how to use it properly is what ensures both safety and efficiency. A flange heater consists of tubular heating elements welded or brazed into a flange, then mounted into a pipe or tank. It’s built to heat liquids or gases directly. That makes it ideal for water, oil, solvents, and corrosive solutions. Here’s how to put it to work effectively. Select the Right Heater for Your Application Before anything else, match the heater with the right job. Flange heaters vary in voltage, watt density, flange size, and material construction. Choosing the wrong one leads to failure or worse, overheating or corrosion. Key factors to assess: Medium to be heated: Water requires different materials than oil or corrosive chemicals. Tank or pipe volume: Impacts wattage requirements. Desired temperature range Heating time expectations Material compatibility: Stainless steel for corrosive fluids; Incoloy for high temperatures. Check compatibility charts from ASME or your supplier’s datasheet to ensure proper selection. Installation Must Be Precise Improper installation shortens lifespan or causes accidents. Always follow the manufacturer’s technical drawings and wiring diagrams. But certain best practices apply universally. Steps to install a flange tubular heater correctly: Verify power is off before starting any installation. Inspect the flange face for damage or warping. Use appropriate gaskets (e.g., spiral wound or graphite) based on fluid and temperature. Tighten bolts using a star pattern to ensure even pressure distribution. Apply torque per ASME standards to prevent leaks. Confirm grounding for safety and regulation compliance. Avoid using Teflon tape or sealants on the flange face; this leads to leaks or joint failure. Wire It According to Load and Power Specs Wiring must match the heater’s voltage and amperage rating. Overloading the circuit can result in failure or a fire hazard. Best practices for wiring: Use copper wires rated for the load current. Install a control panel with temperature sensors and safety cutoffs. Include a contactor and thermostat to regulate performance. Test connections with a multimeter before powering on. For high-wattage units, a dedicated breaker is often required. Refer to the National Electric Code (NEC) or consult a licensed electrician. Temperature Control Enhances Efficiency Without proper control, overheating or underheating can lead to poor results or equipment damage. Flange heaters work best when paired with advanced controls. Components that improve control: Thermocouples or RTDs for precise sensing Digital PID controllers for maintaining setpoints High-limit sensors to shut down the heater if temperatures exceed thresholds Use proportional-integral-derivative (PID) logic for tight control over fluctuating loads. This not only protects the fluid and tank but also prolongs the heater’s life. Perform Routine Maintenance Even durable heaters need attention. Build-up of scale, sediment, or corrosion reduces heating efficiency and can cause early burnout. Maintenance checklist: Inspect terminals for oxidation or loose wires every 3-6 months. Check for leaks or flange warping Flush tanks periodically to remove sediment. Test temperature sensors for accuracy. Clean elements with compatible solvents if scaling appears. Keep a maintenance log. This helps track heater performance and predict when replacement or deep cleaning is needed. Final Thoughts The flange tubular heater is a workhorse in industrial settings. But its performance depends entirely on how it’s selected, installed, and maintained. By following proven steps and using the right controls, you ensure that your system runs safely, efficiently, and for years to come.
How Much Electricity Does a Tubular Heater Needs
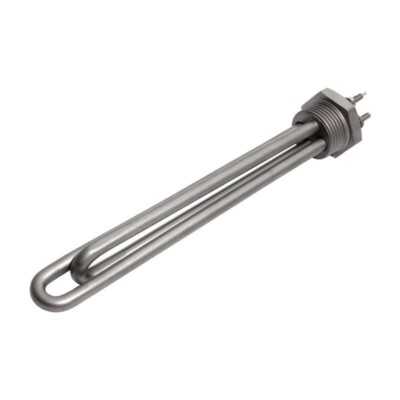
Tubular heaters are popular for applications where compact and efficient heating is needed. They’re used in greenhouses, bathrooms, workshops, and even industrial cabinets. But a common question remains: how much electricity does a tubular heater need? Knowing the answer helps control energy consumption and reduce utility costs. Wattage Ratings and Typical Use Cases Tubular heaters are manufactured in a wide range of wattages. The power requirement varies depending on the length, diameter, and material of the heater. The most common domestic tubular heaters are rated: 60W to 240W for single-room or localized applications 300W to 500W for continuous heating in small spaces Industrial units often exceed 1000W, sometimes reaching 3000W or more. Calculating Electricity Usage Electricity usage is typically calculated in kilowatt-hours (kWh), the standard billing unit used by utility companies. To calculate how much electricity a tubular heater needs, use this formula: Energy Consumption (kWh) = Power (W) x Time (Hours) / 1000 Let’s say you’re using a 250W heater for 10 hours: 250 x 10 = 2,500 watt-hours 2,500 / 1000 = 2.5 kWh If your electricity rate is $0.15 per kWh, that’s $0.375 per day in energy cost. Monthly Estimate Example A 250W heater running 10 hours daily for 30 days: 2.5 kWh/day x 30 = 75 kWh/month 75 x $0.15 = $11.25/month Power vs. Heat Output Efficiency Tubular heaters are nearly 100% efficient in converting electrical energy to heat. That means almost all the electricity drawn is used for warming the space. However, the effectiveness of that heat depends on: Room insulation quality Thermostat usage Heat loss through walls/windows External temperatures Thermostats Save Energy One of the most effective ways to reduce electricity usage is by using a thermostat. It allows the heater to cycle on and off instead of running continuously. For example: A thermostat that maintains 20°C may reduce runtime by 30%-50%. This means a 250W heater could operate for just 5-7 hours instead of 10, reducing costs significantly. Influencing Factors on Power Consumption Several elements affect how much power your heater consumes: Ambient Temperature: Colder environments require longer operation times. Heater Length & Surface Area: Longer tubes cover more area but also draw more power. Material Composition: Aluminum sheaths heat faster than stainless steel, affecting efficiency. Control Systems: Timers and thermostats help manage operation intelligently. Energy Saving Tips Install Timers: Turn the heater off automatically during non-peak hours. Improve Insulation: Seal gaps and add weather stripping to retain heat. Use Reflective Panels: Place them behind the heater to direct heat into the room. Routine Maintenance: Clean dust and debris from the heater to maintain efficiency. Industrial Applications and Power Needs In manufacturing and commercial sectors, tubular heaters are used for pipe heating, fluid warming, and freeze protection. Power needs scale dramatically: 5kW to 15kW systems are not uncommon. These systems often include multi-zone controls to reduce total power use. For example, a 6kW system operating 8 hours a day uses: 6 x 8 = 48 kWh/day At $0.15 per kWh, that’s $7.20/day, or over $200/month Cost vs. Utility Although the cost may seem high, tubular heaters are often preferred for their reliability and compact design. They’re used in places where radiant or convection heating isn’t practical. Their minimal maintenance and ability to deliver targeted heat make them cost-efficient long-term. Safety and Compliance Ensure heaters comply with international standards like CE and UL. Safety features such as: Overheat protection Thermal cut-off switches Enclosure ratings (IP65, etc.) …all contribute to safe operation and indirectly reduce wasteful power consumption. Final Takeaway The electricity required by a tubular heater depends on its wattage, usage pattern, and control features. Small domestic units typically use 1–2.5 kWh/day, while larger industrial systems can use 50 kWh/day or more. By applying intelligent controls and using efficient designs, users can balance performance with energy savings.
What is a Ceramic Furnace
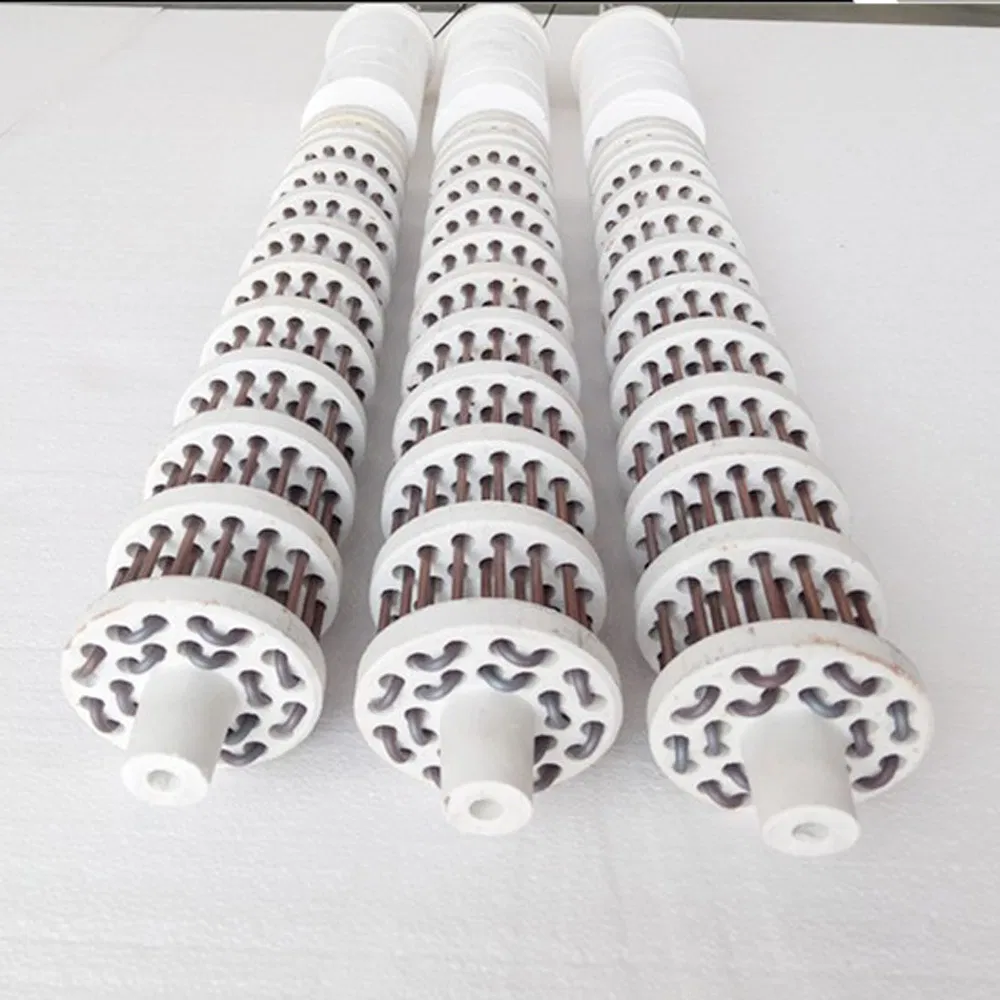
Precision manufacturing, electronics, and advanced materials all depend on controlled high-temperature processes. At the core of many of these processes is a ceramic furnace. But this isn’t just another heat chamber. It’s a critical technology that allows materials to be treated, altered, and perfected with exceptional accuracy. A ceramic furnace heater is a high-temperature heating system specifically designed to process materials using ceramic insulation or ceramic components within its structure. These furnaces are often used for sintering, heat treatment, material testing, and calcination in industries like metallurgy, electronics, and advanced ceramics. The defining characteristic of a ceramic furnace is its ability to maintain uniform, stable temperatures up to 1800°C (3272°F), depending on the model. This stability is crucial for processes like ceramic sintering, where consistent heat is necessary to bond particles without melting them. There are two primary configurations: Chamber Furnaces: Fully enclosed systems with ceramic fiber insulation lining the heating chamber. Used for batch processing. Tube Furnaces: Cylindrical chambers with ceramic tubes. Ideal for controlled atmosphere reactions and small-scale research. Why Ceramic Furnaces Matter Traditional metal-based furnaces can’t handle certain conditions without deforming or contaminating the materials being processed. Ceramic furnaces, however, are chemically stable and thermally resistant. That makes them essential for: High-purity environments: No risk of contamination from metal parts. Extreme temperatures: Ceramics withstand more heat than metal. Energy efficiency: Modern ceramic insulation reduces heat loss. Ceramic insulation materials, such as alumina (Al₂O₃), zirconia (ZrO₂), or mullite, are engineered to trap heat and reflect thermal energy back into the chamber. These materials exhibit: Low thermal conductivity High refractoriness Excellent dimensional stability Key Applications Ceramic furnaces aren’t just for research labs. They play a central role in many industrial workflows: Ceramic and glass sintering: Powders are consolidated into dense, durable parts. Powder metallurgy: Metal powders are heat-treated to form strong components. Semiconductor processing: Used for diffusion and oxidation in chip fabrication. Material testing: Simulates extreme environments for aerospace and automotive parts. Atmosphere Control Options In some cases, materials must be treated in inert or reducing atmospheres to prevent oxidation. Tube-type ceramic furnaces are often paired with gas flow systems that allow precise atmosphere regulation. Common gases used include: Argon Nitrogen Hydrogen This capability is critical for synthesizing advanced materials like battery cathodes, fuel cells, and nanomaterials, where air exposure could ruin results. Choosing the Right Ceramic Furnace When selecting a ceramic furnace, several factors should be evaluated: Maximum temperature: Match the furnace to your process requirements. Heating elements: MoSi₂ and SiC are the most common. MoSi₂ can handle higher temperatures but is more brittle. Chamber size: Depends on whether you’re doing research or industrial-scale production. Atmosphere compatibility: Not all ceramic furnaces support gas environments. Final Thoughts Ceramic furnaces offer unmatched precision and thermal control for industries that demand high-performance heat treatment. For engineers, researchers, and manufacturers, understanding the capabilities and limitations of ceramic furnaces isn’t optional. It’s essential for pushing material performance to new levels. If you’re investing in quality, consistency, and advanced material processing, then knowing how a ceramic furnace works and choosing the right one can directly impact the success of your operation.
Are Cartridge Heaters Waterproof ?
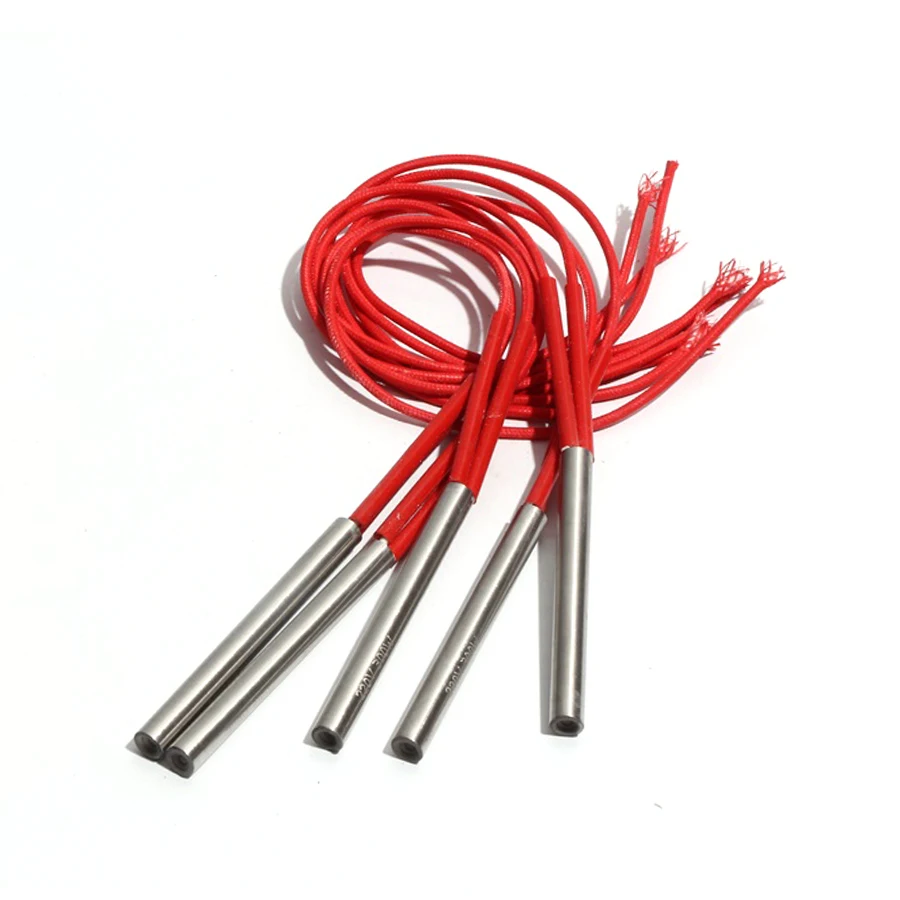
A cartridge heater is often used in industrial applications where precision, durability, and high heat density are crucial. But when it comes to environments with moisture, water splashes, or full submersion, a key question surfaces: are cartridge heaters waterproof? The short answer is ‘standard cartridge heaters are not inherently waterproof’. However, specific design modifications can improve their resistance to moisture, especially for micro cartridge heater models used in compact or sealed systems. Let’s unpack what this means in practical terms. What Is a Cartridge Heater? A cartridge heater or a micro cartridge heater is a cylindrical heating element that transfers heat through direct contact. It’s inserted into drilled holes in metal blocks, molds, or platens to heat solids, liquids, or gases. These heaters are known for: High watt density Rapid heat transfer Tight tolerances Precise temperature control Micro cartridge heaters are smaller variants designed for compact spaces like 3D printing nozzles, medical devices, or aerospace tools. Water and Electricity: A Dangerous Mix Water is highly conductive. When it seeps into a cartridge heater, it can lead to: Electrical short circuits Corrosion of internal components Premature failure Shock hazards Standard cartridge heaters have a stainless steel sheath and internal insulation, often made of magnesium oxide (MgO). While MgO is an excellent thermal conductor and electrical insulator, it’s hygroscopic and it absorbs moisture. When that happens, the insulation becomes conductive, compromising the heater’s safety and function. Are Any Cartridge Heaters Waterproof? Technically, no cartridge heater is truly “waterproof” unless it’s been hermetically sealed. Most off-the-shelf models are moisture-resistant at best. However, certain designs offer varying degrees of water protection. Here’s how manufacturers improve water resistance: Sealed leads: Epoxy potting, Teflon seals, or silicone overmolds at the lead exit area help block water entry. Hermetic sealing: High-end micro cartridge heaters can be laser welded or glass-sealed to prevent any moisture ingress. IP-rated designs: Some custom heaters meet Ingress Protection (IP) standards like IP65 or IP67, which define protection against dust and water. Important: Even if a cartridge heater is IP67-rated (protected against immersion up to 1 meter), that doesn’t mean it can withstand prolonged submersion or pressurized jets without failure. Applications Requiring Waterproof Heaters Some environments absolutely require moisture protection: Food processing Medical sterilization Laboratory equipment Marine instrumentation Outdoor industrial heating In these cases, micro cartridge heaters must be specifically engineered for exposure to water, humidity, or steam. For example, in autoclave sterilizers, the heater must withstand repeated cycles of pressurized steam at over 120°C. Should You Choose a Waterproof Micro Cartridge Heater? If your application involves: High humidity Steam exposure Frequent washdowns Condensation risks Then yes, investing in a sealed or IP-rated micro cartridge heater is smart. It extends lifespan, improves safety, and reduces downtime. Before placing an order, ask your supplier the following: “Is this heater sealed at the lead end?” “What is the maximum moisture it can withstand?” “Can it be customized for my application environment?” Final Takeaway Standard cartridge heaters aren’t waterproof. They can be damaged or fail prematurely when exposed to moisture. But with the right construction, sealed ends, protective coatings, and possibly hermetic welding, a micro cartridge heater can resist moisture and work reliably even in wet environments. Choosing the right heater is not just about heat, it’s about environmental fit. Always match your equipment to its operating conditions for long-term success.
What is The Significance of Fins In a Heater
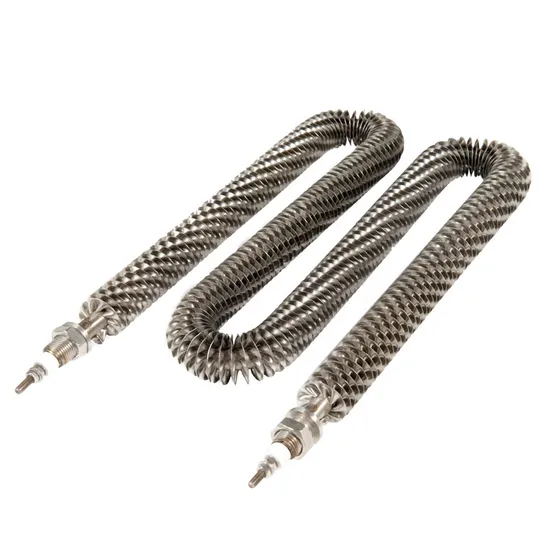
A Finned Cartridge Heater is only as efficient as its surface area allows. That’s where fins come into play. These thin metal extensions dramatically increase the surface area of a heater, improving heat transfer to air or gas without requiring extra power. They’re a small component with a major impact on efficiency, durability, and cost savings. So, what exactly are fins, and how do they work in a heater? Fins in a heater are metallic extensions attached to the surface of the heater sheath. Their primary job is to transfer more heat to the surrounding environment by increasing the surface area. Think of them as heat amplifiers small parts that make a big difference. Why fins are essential in industrial heating In industries that rely on precise heating, such as plastics, packaging, food processing, and HVAC, finned heaters outperform traditional designs. They offer: Faster heat dissipation Lower sheath temperature Longer heater life Energy savings Compact size with higher efficiency These benefits are particularly important in air heating and convection heating applications, where the surrounding medium (air or gas) isn’t a good conductor. How fins increase efficiency Finned Cartridge Heaters use aluminum or stainless steel fins welded or mechanically fixed to the outer sheath. This design promotes superior airflow contact, allowing the heater to transfer thermal energy at a faster rate. Here’s what happens: Heater core generates heat. Heat travels to the sheath. Fins attached to the sheath absorb and radiate heat outward. Air or gas moving past the fins picks up this heat efficiently. Without fins, much of the heat would stay trapped at the surface or be transferred slowly, leading to higher energy costs and potentially shorter heater life due to thermal stress. Where fins are most effective Finned heaters shine in these use cases: Air ducts – More heat is delivered over a shorter length. Drying systems – Uniform airflow and consistent heat are critical. HVAC systems – Better heat control in smaller enclosures. Industrial ovens – Faster heating with reduced energy draw. These environments require consistent, safe, and cost-effective heating. That’s where fins prove their worth. Material and design considerations Not all fins are created equal. The material and shape of the fins determine how effective they are. Common fin materials include: Aluminum – Lightweight, great for high-velocity airflow, and cost-effective. Stainless steel – Durable, corrosion-resistant, ideal for high-temp or harsh environments. Fin shapes and patterns affect performance: Helical wrap – A continuous spiral that boosts airflow contact. Louvered fins – Improve turbulence and enhance thermal exchange. Straight fins – Simple and durable, suitable for slow-moving air. Choosing the right fin design depends on application variables like airflow speed, target temperature, and space constraints. Maintenance and safety factors Finned heaters require less maintenance than traditional heaters due to lower surface temperatures and better efficiency. However, for optimal performance: Clean fins regularly to prevent dust buildup, especially in air ducts. Avoid blocking airflow, as restricted movement reduces thermal transfer and can overheat the unit. Ensure correct mounting, as vibration or poor alignment affects fin contact and reduces performance. Final Thoughts Fins are more than just metal attachments they are a crucial enhancement to the Finned Cartridge Heater design. By expanding the heater’s surface area, fins boost heat transfer, lower energy consumption, and extend operational life. If you’re in a business where reliable heat is mission-critical, understanding how fins affect heater performance isn’t just helpful, it’s necessary. Smart fin selection and heater design can be the difference between consistent productivity and costly downtime.
What is a Mica Band Heater Used For
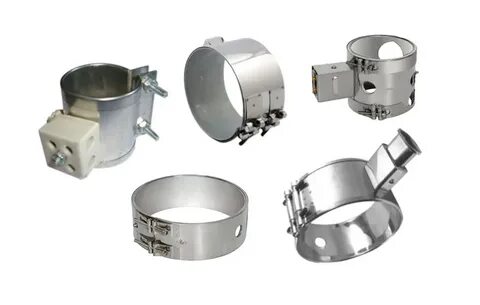
A Band Heater Manufacturer makes heaters that go around things like metal barrels or pipes to make them hot. One type they make is a mica band heater. These heaters are wrapped around machines that need heat to melt or soften stuff. They’re super helpful in places like factories. People working with plastic or food often use them. In this blog, you will learn where mica band heaters are used, how they work, and why they matter. What is a Mica Band Heater? A mica band heater is a round heater. It fits tightly around a metal surface. It has a metal shell, mica sheets inside, and a heating wire. The mica sheets hold the heat in place. The wire gets hot when you plug it in. The metal shell keeps the heat from going out too fast. These heaters work best for things with a round shape. Key parts of a mica band heater: Outer shell: Made of steel or stainless steel Mica layers: Help to hold the wire and send heat Heating wire: Usually made from nickel or chrome Clamping device: Keeps it stuck tightly to the machine Where are Mica Band Heaters Used? Mica band heaters are seen in many big machines. They help when things must stay hot or melt. Here are some common uses: Plastic injection machines: Heat plastic so it can be shaped Extruders: Keep plastic flowing smoothly Blow molding tools: Help form bottles and containers Food packaging lines: Keep food flowing or sealing right Drum heating: Warm up sticky liquids like glue or oil 3D printers: Heat parts that need steady warmth Table of industries and how they use mica band heaters: Industry Use Case Plastic manufacturing Melts and molds plastic Food processing Keeps chocolate or sauces warm Chemical plants Heats up tanks or mixing drums Printing Keeps ink at the right thickness Oil & gas Warms up barrels for smooth flow Why Do Companies Choose Mica Band Heaters? These heaters are easy to fit. They heat up fast. They are not too costly. They last a long time if used right. Most companies like them because they don’t waste much power. Main benefits include: Fast heating: Gets hot quickly Even heat spread: No cold spots Low cost: Cheaper than ceramic heaters Easy to install: Simple clamps hold them in place Custom sizes: Can be made for many shapes How Do You Pick the Right Mica Band Heater? Picking the best one is key. You need the right size, shape, and heat level. A Band Heater Manufacturer can help with this. They check your machine and make a heater that fits just right. Things to know when picking one: Size of the barrel or pipe Temperature needed Power source (volts and watts) Type of metal surface Room conditions (wet, dusty, etc.) Always talk to experts before buying. They help you avoid mistakes. How to Keep Your Heater Working Long? These heaters last longer when cared for. They must be kept tight and clean. If they get loose, heat escapes. That can burn the wires. Helpful care tips: Check for loose clamps Keep surface dry and clean Don’t touch wires too much Use the right power supply Turn off when not in use If your heater breaks, it can stop the whole machine. This can cost a lot of money. Final Thoughts A mica band heater is small but strong. It helps in plastic, food, oil, and other big jobs. It keeps machines warm so they can do their work. If you need steady and safe heat, ask a trusted band heater manufacturer to make one for your job. They’ll help you find what fits best and lasts long. Need help choosing the right one? Talk to a Cheri Heater today.