How to Select the Right Cartridge Heater
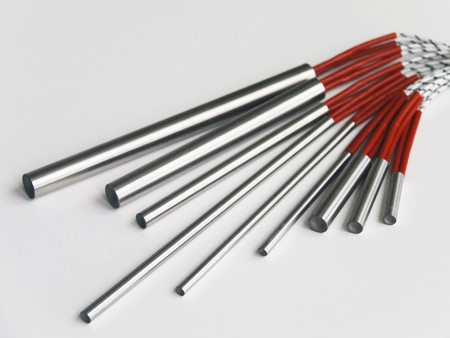
Choosing the right cartridge heater can make a significant difference in achieving optimal heating efficiency for various industrial applications. These heaters are known for their compact design, precise heating, and efficiency, making them essential in industries such as plastic manufacturing, packaging, and medical equipment. However, with a range of options available, finding the right fit can be challenging. In this guide, we’ll discuss key factors to select the right cartridge heater to help you make an informed choice. 1. Understand Your Application’s Temperature Requirements Each application has a unique temperature range and heating duration requirement. A heater that’s too powerful or not powerful enough could lead to uneven heating or even system failure. Here’s what to consider: Max Operating Temperature: Cartridge heaters can operate at temperatures as high as 1400°F (760°C), but always confirm the max operating limits for your application. Thermal Transfer Efficiency: Ensure the heater has optimal heat transfer properties to match the material’s conductivity. Temperature Control Precision: Applications with strict tolerances require heaters that can maintain steady temperatures. 2. Consider the Heater’s Watt Densityof Your Cartridge Heater Watt density (W/in²) is crucial as it determines the heater’s power in relation to its surface area. Selecting the right watt density impacts the heater’s longevity and performance: Low Watt Density (10-30 W/in²): Best for applications needing gentle heat, like food equipment. Medium Watt Density (30-50 W/in²): Ideal for plastics and rubber manufacturing. High Watt Density (50+ W/in²): Suitable for high-temperature applications such as mold heating and metal processing. A miscalculated watt density can lead to excessive heating or premature burnout, so be clear on your application’s needs. 3. Select the Right Sheath Material The heater’s sheath is the outer layer that directly affects its durability and compatibility with the surrounding environment. Common sheath materials include: Stainless Steel: Highly resistant to corrosion and suitable for food and medical industries. Incoloy: Ideal for extreme temperatures and corrosion-prone environments. Nickel: Great for high-conductivity applications where rapid heat transfer is essential. 4. Determine the Proper Diameter and Length of Your Cartridge Heater Your cartridge heater must fit precisely within the drilled holes or mounting points to ensure efficient heat transfer. Measure accurately: Diameter: Ensure a snug fit; the diameter should ideally be 0.002-0.003 inches smaller than the drilled hole. Length: Choose a length that optimally covers the heat transfer area. 5. Ensure Proper Voltage and Power Compatibility Confirm that the heater’s voltage matches the power supply in your facility. Mismatched voltage can lead to inadequate heating or damage to the heater and connected systems. Single-Phase or Three-Phase Options: Industrial heaters often come in both options. Match your facility’s electrical setup. Adjustable Voltage Options: If your application requires variable temperatures, consider heaters that allow for adjustable voltage. 6. Evaluate Lead Type and Exit Options Cartridge heaters offer various lead configurations to suit different environments and handling needs: Flexible Lead Wire: Good for applications with movement; check insulation to withstand high temperatures. Right-Angle Leads: Saves space in compact setups; prevent bending stress. Swaged Leads: Best for high-vibration environments to prevent breakage. Final Words When choosing a Cartridge Heater, reliability and durability should be priorities. Partner with reputable manufacturers like Cheri Heater who offer quality certifications and testing guarantees to ensure longevity and performance.
7 Must-Know Facts About 3D Printer Heaters
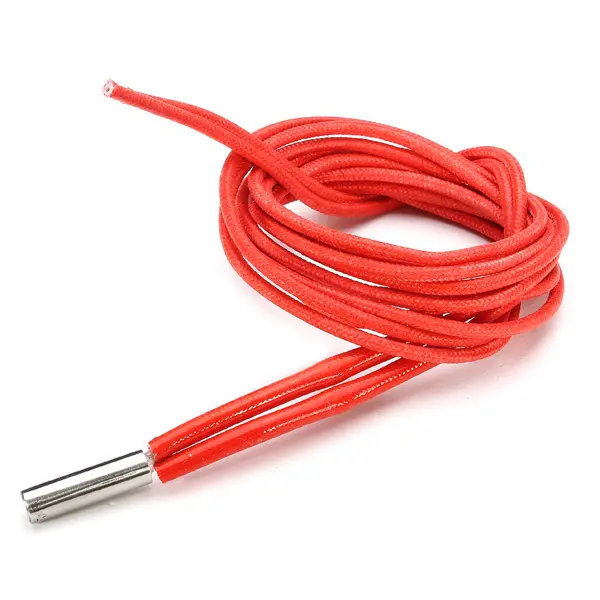
3D printing has changed the way we create objects. At the heart of this technology lies a crucial component – the heater. A 3D printer heater manufacturer plays a key role in the quality and efficiency of 3D prints. This blog post will uncover seven essential facts about 3D printer heaters that every enthusiast and professional should know. 1. The Role of Heaters in 3D Printing 3D printer heaters are the unsung heroes of the printing process. They melt the plastic filament, turning it into a liquid that can be shaped into amazing 3D objects. Without proper heating, your prints would be weak, brittle, or might not even form at all. Heaters work in two main areas of a 3D printer: The extruder: This is where the plastic filament is melted. The print bed: This keeps the printed object warm to prevent warping. The right temperature is crucial. Too hot, and your plastic might burn or lose its properties. Too cold, and it won’t stick together well. That’s why understanding heaters is so important for successful 3D printing. 2. Types of 3D Printer Heaters There are several types of heaters used in 3D printers. Each has its own strengths and best uses: Cartridge Heaters: These are the most common. They’re small, cylindrical, and fit snugly into the heater block. Ceramic Heaters: These heat up quickly and evenly. They’re often used in high-end printers. Silicone Heaters: These are flat and flexible. They’re great for heating print beds. Induction Heaters: These use electromagnetic fields to heat metal. They’re fast but more complex. Nichrome Wire: This is a resistive wire that heats up when electricity flows through it. Choosing the right type depends on your printer design and what you’re printing. Some materials need higher temperatures, while others work best with steady, lower heat. 3. The Impact of Heater Quality on Print Results The quality of your 3D printer heater can make or break your prints. High-quality heaters from reputable manufacturers offer several benefits: Consistent Temperature: They maintain a steady temperature, which is crucial for print quality. Fast Heating: Good heaters reach the desired temperature quickly, saving you time. Durability: They last longer, saving you money and hassle in the long run. Safety: Quality heaters have built-in safety features to prevent overheating. Poor quality heaters can lead to: Uneven heating Temperature fluctuations Slow warm-up times Premature failure Investing in a good heater can significantly improve your 3D printing results. It’s not just about the initial cost – think about the long-term benefits and the quality of your prints. 4. Temperature Control and Its Importance Precise temperature control is vital in 3D printing. Different materials need different temperatures: PLA: 180-230°C ABS: 210-250°C PETG: 230-250°C Nylon: 240-260°C These temperatures aren’t just suggestions. They’re critical for proper melting and layer adhesion. Modern 3D printers use thermistors or thermocouples to measure temperature. These sensors work with the printer’s control board to maintain the right heat. Good temperature control also affects: Layer Adhesion: Proper heat ensures layers stick together well. Warping: Correct bed temperature prevents the base of prints from curling up. Surface Finish: The right temperature gives smoother, more professional-looking prints. Advanced printers even allow for temperature changes during printing. This can help with complex shapes or multi-material prints. 5. Energy Efficiency and Power Consumption 3D printing can use a lot of energy, especially for long prints. Heaters are often the biggest power consumers in a 3D printer. Here’s why efficiency matters: Cost: More efficient heaters mean lower electricity bills. Environmental Impact: Less energy use is better for the planet. Print Time: Efficient heaters warm up faster, reducing overall print time. Some ways to improve efficiency: Insulation: Good insulation around the heater block and print bed reduces heat loss. PID Tuning: This adjusts how the printer controls the heater, optimizing power use. Smart Power Management: Some printers reduce power to heaters when not in use. Modern 3D printer heater manufacturers are focusing on creating more efficient heating systems. This not only saves energy but also improves print quality by maintaining more stable temperatures. 6. Maintenance and Longevity of 3D Printer Heaters Like any part of a 3D printer, heaters need care to last. Proper maintenance can extend the life of your heater and improve print quality. Here are some tips: Regular Cleaning: Remove any plastic buildup around the heater block. Check Connections: Loose wires can cause temperature fluctuations or failures. Monitor Performance: Watch for signs of inconsistent heating or longer warm-up times. Replace Thermistors: These sensors can wear out over time, affecting temperature accuracy. Signs that your heater might need replacement: Inconsistent temperatures Difficulty reaching or maintaining temperature Visible damage to the heater or its wires Most heaters last for hundreds or even thousands of hours of printing. But their lifespan can vary based on usage and quality. Keeping spare heaters on hand can prevent long downtimes if a replacement is needed. 7. Future Trends in 3D Printer Heater Technology The world of 3D printing is always advancing, and heater technology is no exception. Here are some exciting trends to watch: Faster Heating: New materials and designs are allowing for quicker warm-up times. More Precise Control: Advanced algorithms are improving temperature stability. Multi-Zone Heating: Some printers now use multiple heaters for more complex temperature control. Smart Heaters: IoT-enabled heaters that can be monitored and controlled remotely. Energy Harvesting: Some researchers are exploring ways to capture and reuse heat energy in 3D printers. New Materials: Heaters designed for exotic filaments that require very high or precise temperatures. Miniaturization: As 3D printers get smaller, heaters are shrinking too, without losing efficiency. These advancements promise to make 3D printing faster, more efficient, and capable of working with an even wider range of materials. Final Words 3D printer heaters are a critical component that often doesn’t get the attention it deserves. Understanding these seven facts can help you choose the right printer, maintain it properly, and get the best results from your 3D printing projects. As technology continues to advance,
5 Practical Ways to Use Quartz Infrared Tube Heater
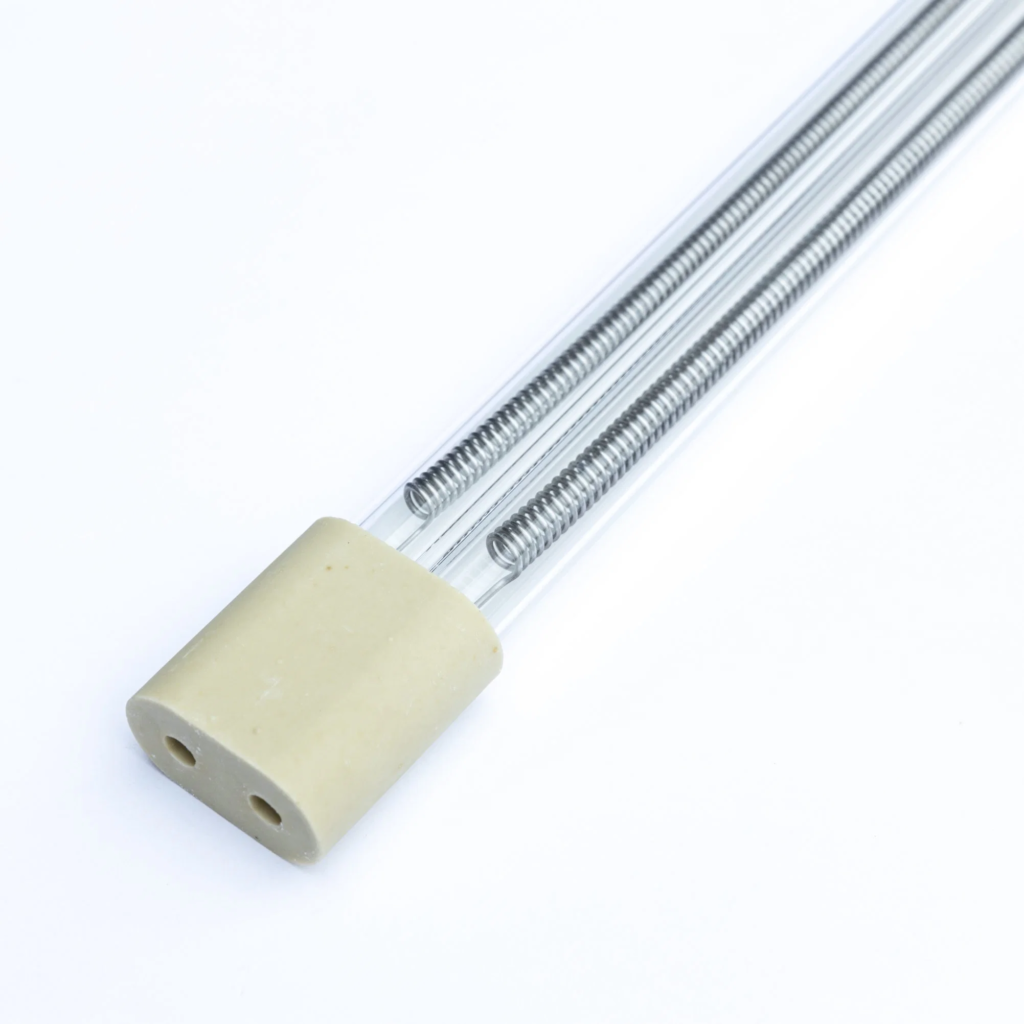
When it comes to efficient heating solutions, the Quartz Infrared Tube Heater stands out. This powerful heating device offers quick and targeted warmth. It’s becoming a go-to choice for many homeowners and businesses. Let’s explore five practical ways to use this versatile heater. 1. Outdoor Patio Heating Extend your outdoor living season with a Quartz Infrared Tube Heater. These heaters are perfect for patios and decks. Quick heat: They warm up in seconds, providing instant comfort. Energy-efficient: They heat objects, not air, saving energy. Weather-resistant: Many models can withstand light rain and wind. A recent study showed that restaurants with outdoor heating increased their revenue by 30% during colder months. One popular café in Chicago used quartz infrared heaters to keep their patio open year-round. They saw a 25% boost in winter sales. 2. Garage Workshop Heating Transform your cold garage into a cozy workshop with a Quartz Infrared Tube Heater. Targeted heating: Focus warmth on your work area. Safe for flammable materials: They don’t heat the air, reducing fire risks. Low maintenance: No moving parts means less wear and tear. John, a woodworker from Minnesota, installed a quartz infrared heater in his garage. He can now work comfortably even when it’s -20°F outside. His productivity increased by 40% during the winter months. 3. Greenhouse Heating Quartz Infrared Tube Heaters are ideal for maintaining optimal temperatures in greenhouses. Plant-friendly: They don’t dry out the air like some heaters. Even heat distribution: Ensures all plants receive equal warmth. Energy-saving: Can be programmed to run only when needed. A small organic farm in Vermont used these heaters to extend their growing season. They were able to harvest fresh tomatoes two months longer than usual. This resulted in a 15% increase in annual revenue. 4. Industrial Spot Heating In large warehouses or factories, heating the entire space can be costly. Quartz Infrared Tube Heaters offer a smart solution. Zone heating: Heat only occupied areas. Quick warm-up: Ideal for areas with high traffic but intermittent use. Silent operation: No noisy fans or motors. A manufacturing plant in Texas installed these heaters above workstations. They reduced their overall heating costs by 35%. Employee comfort and productivity also improved significantly. 5. Sports Arena Seating Keep fans comfortable during outdoor sporting events with strategically placed Quartz Infrared Tube Heaters. Directional heat: Can be aimed at specific seating sections. Instant on/off: No need to pre-heat before the game. Clean heat: No fumes or odors to distract from the game. A minor league baseball stadium in Colorado installed these heaters above their VIP seating area. They saw a 20% increase in premium ticket sales for early and late-season games. As we move towards more energy-efficient solutions, these heaters are likely to become even more popular. Conclusion Quartz Infrared Tube Heaters offer versatile heating solutions for various settings. From outdoor patios to industrial workspaces, they provide efficient and targeted warmth. Their energy-saving features and low maintenance make them a smart choice for many applications. They offer a balance of comfort, efficiency, and practicality. Whether you’re a homeowner looking to extend your outdoor season or a business owner aiming to cut heating costs, consider a Quartz Infrared Tube Heater.
What is the Purpose of a Band Heater?
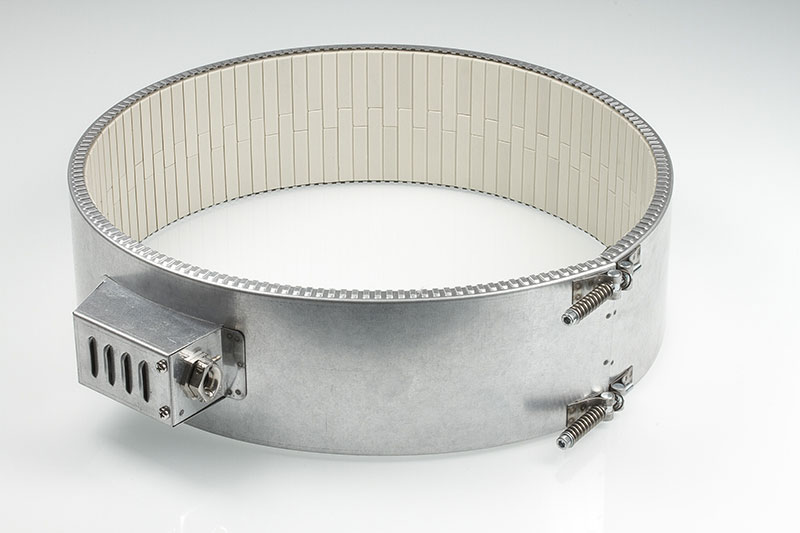
Understanding the role of a band heater is crucial, especially if you’re working with equipment that demands precise temperature control. Whether you’re familiar with industrial heating or just getting started, knowing what a band heater manufacturer offers can make all the difference. These heaters are vital in many industries, ensuring that machines and processes run smoothly and efficiently. How Does a Band Heater Work? Band heaters are cylindrical devices designed to heat cylindrical objects. They fit snugly around the surface of a cylinder, providing even and consistent heat. Sheath Material: The outer layer is usually made of stainless steel, which is durable and resistant to oxidation at high temperatures. Insulation: Inside the heater, layers of insulation, such as mica or ceramic, help prevent heat loss and ensure that most of the energy is directed towards heating the cylinder. Heating Element: The core component is a wire made of materials like nickel-chromium, which heats up when electricity flows through it. This design allows the band heater to evenly distribute heat, which is essential for applications requiring uniform temperatures. What are The Common Applications of Band Heaters Band heaters are used in a variety of settings. Their ability to maintain consistent temperatures makes them invaluable in several industries. Plastic Industry: In plastic injection molding machines, band heaters maintain the temperature of the barrels, ensuring that the plastic melts uniformly. Packaging Industry: They are used to seal packages by providing the necessary heat to bonding surfaces. Food Industry: Band heaters help maintain the temperature of processing equipment, ensuring that food products are cooked or processed at consistent temperatures. Chemical Industry: In chemical processing, maintaining precise temperatures is critical for reactions. Band heaters are used to ensure that vessels and pipes remain at the required temperature. Textile Industry: They keep dye vats and other processing equipment at consistent temperatures, ensuring that colors are applied evenly. What are The Types of Band Heaters There are several types of band heaters, each designed for specific applications. Mica Band Heaters: These are the most common type and are suitable for applications requiring lower watt densities. They are ideal for plastic processing machinery. Ceramic Band Heaters: These are used in applications that require high temperatures and are known for their energy efficiency due to the ceramic insulation. Nozzle Heaters: A specialized type of band heater, nozzle heaters are used in machines that have smaller surfaces to heat, such as the nozzles of injection molding machines. Benefits of Using a Band Heater Band heaters offer several benefits, making them a preferred choice in various industries. Efficient Heat Transfer: Band heaters are designed to provide direct heat to the surface they wrap around, making them highly efficient. Durability: Made from high-quality materials, they are built to withstand harsh industrial environments. Energy Savings: The insulation within band heaters minimizes heat loss, reducing energy consumption. Customizable: A band heater manufacturer can customize these heaters to meet specific needs, including size, wattage, and material. Wrap Up Understanding the purpose of a band heater is essential for anyone involved in industries that require precise temperature control. From their construction to their applications, band heaters play a key role in maintaining the quality and efficiency of various processes. By choosing a reliable band heater manufacturer, you can ensure that your equipment runs efficiently and meets your specific heating needs. These heaters are more than just tools; they are essential components that keep many industries running smoothly.
What is the Purpose of a Tubular Heater?
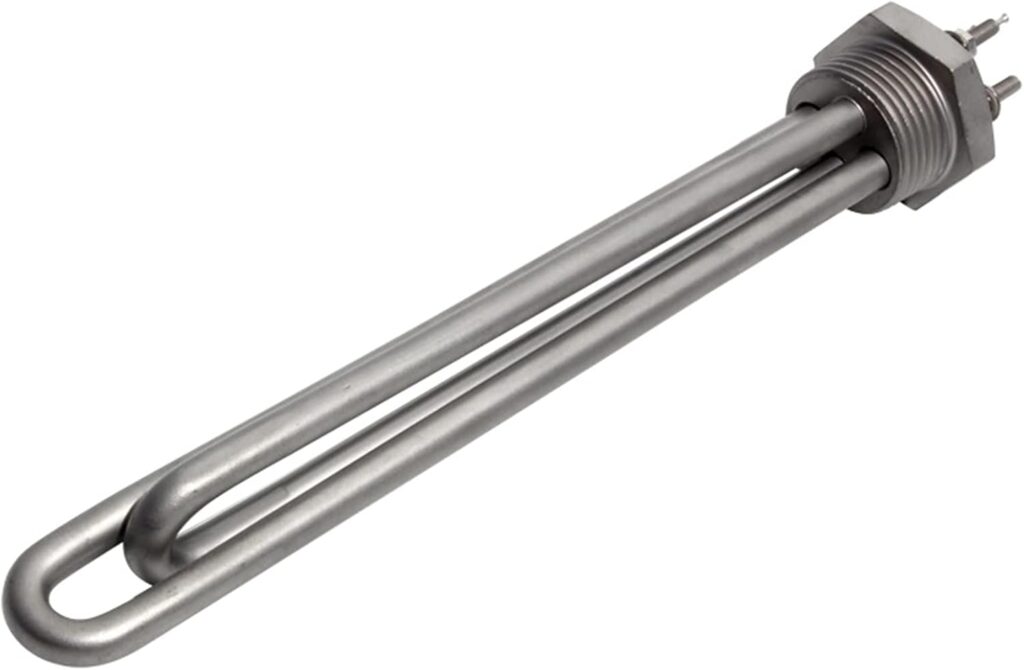
A tubular heater with thermostat is an essential component in various heating applications. Whether you’re dealing with industrial machinery or home appliances, understanding the role of this heating element can significantly enhance the efficiency of your operations. The tubular heater with thermostat provides controlled heat, ensuring that your equipment operates at optimal temperatures without the risk of overheating. How Does a Tube Heater Work? A tube heater operates by converting electrical energy into heat. This heat is then distributed evenly across the surface of the tube, making it ideal for applications that require consistent and reliable heat. Construction: Tube heaters are typically made of a metal sheath, such as stainless steel, which houses the heating element. The element inside is usually a coil of resistance wire, similar to that found in cartridge heaters. Thermostat Integration: The addition of a thermostat allows for precise temperature control. This prevents overheating, which can damage both the heater and the material being heated. Heat Distribution: The design of the tube allows for even heat distribution, making it suitable for applications where uniform heating is crucial. Applications of Tube Heaters Tube heaters are incredibly versatile and can be found in a wide range of applications. Here’s where they shine: Industrial Heating: Tube heaters are commonly used in industrial processes, such as drying, curing, and melting, where precise and reliable heat is required. HVAC Systems: In heating, ventilation, and air conditioning systems, tube heaters help maintain consistent temperatures, ensuring comfort and efficiency. Food Processing: Tube heaters play a critical role in food processing by providing controlled heat for cooking, baking, and maintaining the right temperature for food safety. Greenhouse Heating: Tube heaters are also used in greenhouses to provide consistent warmth, promoting healthy plant growth even in colder climates. Benefits of Using a Tube Heater with Thermostat Choosing a tubular heater with thermostat offers several advantages: Energy Efficiency: The thermostat allows the heater to maintain the desired temperature without consuming excess energy. This leads to lower energy costs and a more sustainable operation. Safety: The built-in thermostat prevents the heater from overheating, reducing the risk of fire or damage to the equipment. Longevity: By preventing overheating, the thermostat also extends the life of the heater, reducing the need for frequent replacements. Versatility: Tube heaters with thermostats can be used in a variety of applications, from industrial processes to residential heating, making them a versatile choice for different heating needs. Final Words The tubular heater with thermostat is a vital tool in various industries, providing controlled and consistent heat where it’s needed most. Understanding its purpose and benefits can help you make informed decisions about its use in your operations. With proper maintenance and the right choice of heater, you can ensure efficient and safe heating for years to come.
What is the Application of a Band Heater?
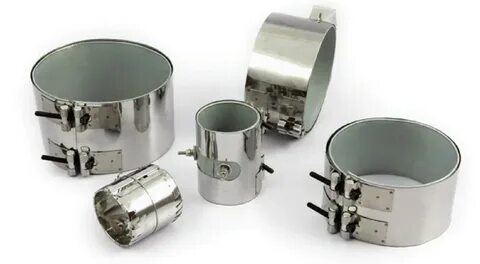
When working with machinery and industrial equipment, maintaining the right temperature is crucial for smooth operation. This is where a band heater plays a vital role. Designed to heat cylindrical surfaces, band heaters are indispensable in many industrial processes. If you are looking for reliable heating solutions, working with a trusted band heater manufacturer ensures you get the right equipment for your needs. Common Applications of Band Heaters Band heaters are versatile and find use in a variety of industries. Below are some of the most common applications: Plastic Injection Molding: In plastic molding, band heaters are used to maintain the correct temperature of the molds. This ensures that the plastic material flows smoothly and sets properly, resulting in high-quality finished products. Extrusion Processes: Band heaters are essential in extrusion processes, where materials like plastic or rubber are pushed through a mold to create products like pipes, sheets, or films. Maintaining the right temperature is crucial for ensuring the material’s consistency and preventing defects. Food and Beverage Industry: Band heaters help maintain the right temperature for food processing equipment, ensuring that products are cooked evenly and safely. They are also used in machinery like coffee urns and food warmers. Chemical and Pharmaceutical Industry: Band heaters are used to heat tanks and vessels, ensuring that chemicals and pharmaceuticals are processed at the correct temperatures. This is essential for reactions and formulations that require precise thermal conditions. Printing Industry: In the printing industry, band heaters help maintain the temperature of ink and rollers, ensuring that the printing process is smooth and the quality of the print is high. How to Choose the Right Band Heater Manufacturer Selecting the right band heater manufacturer is essential for ensuring that you get a product that meets your specific needs. Here are some factors to consider: Customization: A good manufacturer will offer custom options, allowing you to choose the right size, wattage, and sheath material for your application. Quality Control: Reliable manufacturers adhere to strict quality control standards, ensuring that every band heater is built to last and performs reliably. Technical Support: A manufacturer that offers technical support can help you select the right heater and troubleshoot any issues that may arise during installation or operation. Energy Efficiency: Look for manufacturers that design band heaters with energy efficiency in mind, as this can lead to cost savings and reduced environmental impact. Wrap Up Understanding what the application of a band heater is, and how it functions, is essential for anyone involved in industries that rely on precise temperature control. From plastic molding to food processing, band heaters play a critical role in ensuring that industrial processes run smoothly and efficiently. Working with a reputable band heater manufacturer like Cheri ensures that you get a reliable product tailored to your specific needs, backed by quality assurance and technical support. By following proper maintenance practices, you can extend the life of your band heater and keep your operations running at peak efficiency.
Where is a Thermocouple Used?
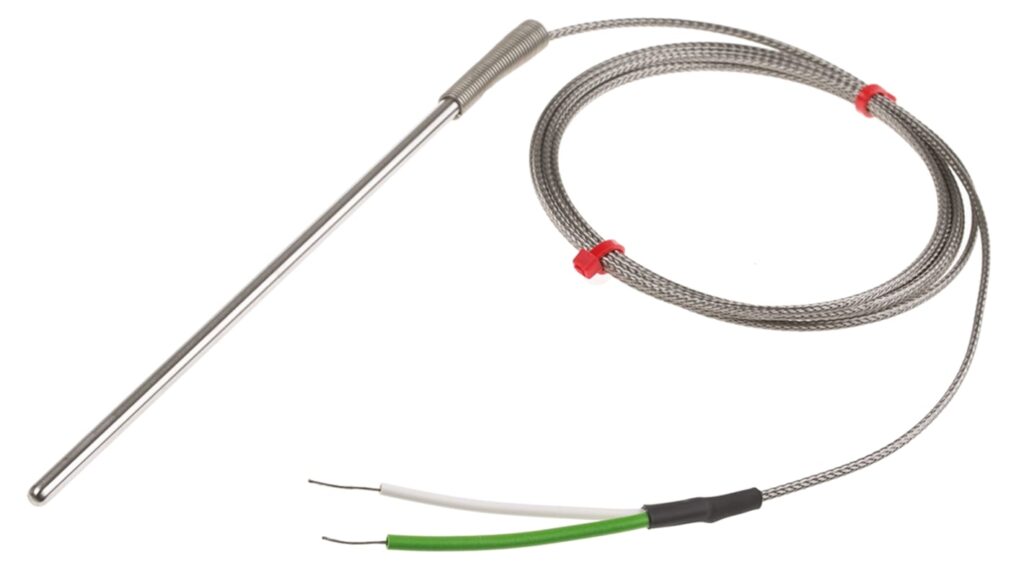
When considering the various devices that measure temperature, the thermocouple stands out for its versatility and reliability. Whether you are familiar with the work of a thermocouple manufacturer or just beginning to explore this field, understanding where thermocouples are used can provide valuable insight. Thermocouples are essential in many industries due to their ability to accurately measure extreme temperatures. How Does a Thermocouple Work? A thermocouple consists of two different metals joined at one end. When these metals experience a temperature difference, they generate a small electrical voltage. This voltage is then interpreted to measure the temperature. The simplicity of this design allows thermocouples to be both durable and responsive, making them suitable for various applications. Durability: Thermocouples are built to withstand harsh environments, from extreme heat to corrosive conditions. Versatility: They can measure temperatures ranging from very low to extremely high, depending on the metals used. Quick Response: The small size and direct contact of thermocouples allow them to respond quickly to temperature changes. Applications of Thermocouples in Different Industries Thermocouples are used across a wide range of industries, each with unique requirements and challenges. 1. Industrial Manufacturing In manufacturing, controlling temperature is critical for ensuring product quality. Thermocouples are used in: Furnaces and Kilns: To monitor and control the high temperatures required for metalworking and ceramics. Plastic Extrusion: Where precise temperature control is needed to shape and form plastic materials. Heat Treatment: To ensure that metals are heated to the correct temperature for processes like hardening or annealing. 2. Aerospace Industry In the aerospace sector, the ability to measure temperature accurately is crucial for safety and performance: Engines: Thermocouples monitor the temperatures in jet engines, ensuring they operate within safe limits. Exhaust Systems: They measure the temperature of exhaust gases to assess engine performance and emissions. Spacecraft: Thermocouples are used in spacecraft to monitor critical systems, ensuring they function correctly in the extreme conditions of space. 3. Medical Field Thermocouples also play a vital role in medical equipment, where precise temperature measurement is often a matter of life and death: Sterilization Equipment: They monitor the high temperatures needed to sterilize medical instruments. Incubators: Thermocouples ensure that the temperature inside infant incubators remains stable and safe. Cryotherapy: They are used in cryotherapy chambers to monitor the extremely low temperatures required for treatment. Why Should I Choose a Thermocouple Manufacturer? Choosing the right thermocouple manufacturer can make a significant difference in the performance and reliability of the thermocouples you use. Here’s why: Customization: A good manufacturer can provide thermocouples tailored to your specific needs, whether that means different metal combinations or special sheathing materials. Quality Control: Reputable manufacturers have strict quality control processes to ensure that each thermocouple meets industry standards. Technical Support: Expert manufacturers offer support to help you select the right type of thermocouple for your application and assist with any issues that arise during use. Types of Thermocouples and Their Specific Uses Different types of thermocouples are designed for specific applications, depending on the materials used: Type K (Nickel-Chromium / Nickel-Alumel): Commonly used in general-purpose applications due to its wide temperature range and affordability. Type J (Iron / Constantan): Often used in older equipment, it’s suitable for lower temperature applications. Type T (Copper / Constantan): Best for low-temperature measurements, such as in cryogenics. Type S (Platinum Rhodium / Platinum): Used in high-temperature applications, like in the aerospace industry and laboratory settings. Maintenance and Care for Thermocouples To ensure your thermocouples function correctly and last as long as possible, regular maintenance is essential: Regular Inspections: Check thermocouples for signs of wear, corrosion, or damage. Calibration: Regularly calibrate thermocouples to ensure accuracy, especially in critical applications. Proper Installation: Ensure thermocouples are installed correctly, with secure connections and appropriate protective sheathing. Wrap Up Understanding where a thermocouple is used offers insight into the importance of this simple yet essential device in various industries. From manufacturing to aerospace and medical applications, thermocouples provide the precise temperature measurements necessary for safe and efficient operations. Partnering with a reliable thermocouple manufacturer ensures that you receive high-quality, customized solutions tailored to your specific needs. With proper care and maintenance, thermocouples can provide accurate temperature readings for many years, making them an invaluable tool in countless applications.
What is a Cartridge Heater?
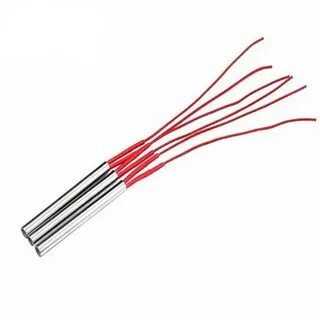
A cartridge heater is an essential tool in various industries, known for its ability to deliver precise, localized heat. Whether you’re involved in manufacturing or exploring options for heating solutions, understanding the importance of choosing a reliable Cartridge Heater Manufacturer is crucial. Cartridge heaters are not just simple devices; they are carefully engineered to provide efficient heating for specific applications. How Do Cartridge Heaters Work? Cartridge heaters are designed to transfer heat effectively to their surroundings, making them ideal for heating metal parts or molds. Here’s a closer look at how they function: Construction: The core of a cartridge heater is a resistance wire made of nickel-chromium, which converts electrical energy into heat. This wire is tightly wound around a ceramic core and encased in a metal sheath, usually made of stainless steel. The sheath protects the heater and ensures even heat distribution. Insulation: The resistance wire is insulated with magnesium oxide, which not only serves as an electrical insulator but also enhances thermal conductivity. This allows the heat generated by the wire to transfer efficiently to the sheath and subsequently to the surrounding material. Design: Cartridge heaters are designed to fit snugly into drilled holes, ensuring close contact with the material being heated. This design maximizes heat transfer and minimizes energy loss. Types of Cartridge Heaters Understanding the different types of cartridge heaters can help in selecting the right one for your needs: High-Density Cartridge Heaters: These heaters offer a high watt density, making them suitable for applications that require rapid heating and high temperatures. Low-Density Cartridge Heaters: Used in applications where lower temperatures are sufficient, these heaters are ideal for sensitive materials. Split-Sheath Cartridge Heaters: Designed to expand when heated, these heaters ensure better contact with the surrounding material, improving heat transfer efficiency. Why Choose a Reputable Cartridge Heater Manufacturer? Selecting a trustworthy Cartridge Heater Manufacturer like Cheri is critical for ensuring the quality and performance of your heaters. Here’s why: Customization: A good manufacturer can provide customized solutions tailored to your specific needs, whether you require a particular size, wattage, or material. Quality Control: Reputable manufacturers adhere to strict quality control standards, ensuring that each heater is reliable and long-lasting. Technical Expertise: With the right manufacturer, you gain access to expert advice and support, helping you choose the best heater for your application and troubleshoot any issues. Durability: High-quality materials and construction techniques result in heaters that can withstand harsh conditions and last longer, reducing the need for frequent replacements. Maintenance Tips for Cartridge Heaters Proper maintenance can extend the life of your cartridge heaters and ensure they perform optimally: Regular Checks: Inspect heaters regularly for signs of wear, such as discoloration or damaged wires. Correct Installation: Ensure that the heater is installed snugly in the drilled hole to optimize heat transfer and prevent damage. Temperature Control: Use temperature controllers to prevent overheating, which can damage both the heater and the material it’s heating. Clean Environment: Keep the heater and its surroundings clean to prevent contamination that could affect performance. Wrap Up Understanding what a cartridge heater is and how it functions is essential for anyone involved in industries that require precise heating solutions. By selecting a reliable Cartridge Heater Manufacturer, you can ensure that your operations run smoothly and efficiently. With the right maintenance practices, your cartridge heaters can provide consistent performance, helping you achieve the desired results in your applications.
5 Applications of Finned Tubular Heater in Industries
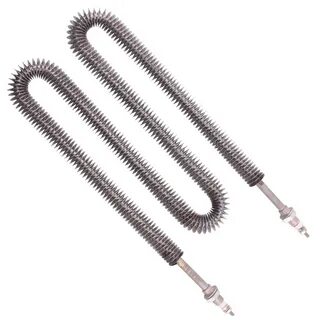
A finned tubular heater always stands out as a powerful and efficient solution in industrial applications. This unique heating device has gained popularity across various sectors due to its versatility and effectiveness. From food processing to aerospace, the Finned Tubular Heater is making waves in how industries approach their heating needs. 1. Food Processing: Maintaining Optimal Temperatures The food industry relies heavily on precise temperature control to ensure product quality and safety. Finned Tubular Heaters play a crucial role in this sector. Uniform heating: The fins on these heaters help spread heat evenly, preventing hot spots that could spoil food. Quick temperature adjustments: Rapid heating and cooling capabilities allow for swift changes in production lines. Sanitary design: The smooth surface of these heaters makes them easy to clean, meeting strict hygiene standards. These heaters are also used in: Chocolate tempering machines Industrial fryers Food packaging equipment The ability to maintain steady temperatures within 1°C has made Finned Tubular Heaters a go-to choice for food processors aiming for top-notch quality. 2. Aerospace: Defrosting and De-icing The aerospace industry faces unique challenges when it comes to heating, especially in harsh weather conditions. Finned Tubular Heaters have found an important place in this field. Aircraft de-icing: These heaters are used in ground equipment to quickly melt ice on aircraft surfaces. Runway heating: Embedded in runway surfaces, they prevent ice formation and ensure safe takeoffs and landings. Sensor protection: Critical sensors on aircraft are kept ice-free using these efficient heaters. The heaters’ ability to operate in extreme cold, sometimes as low as -40°C, makes them ideal for aerospace applications. Their durability in harsh conditions has led to a 50% increase in their use in airport ground equipment over the past five years. 3. Plastic Manufacturing: Precision Molding The plastic industry relies on exact temperature control for molding and extrusion processes. Finned Tubular Heaters excel in this area. Even heat distribution: The finned design ensures uniform heating across molds, preventing defects. Energy efficiency: These heaters transfer heat more effectively, reducing power consumption. Compact size: Their slim profile allows for installation in tight spaces within molding machines. These heaters are also used in: Plastic extrusion lines Blow molding machines Thermoforming equipment The precision offered by Finned Tubular Heaters has led to a 25% increase in their adoption in the plastic industry over the past three years. 4. HVAC Systems: Efficient Air Heating Heating, Ventilation, and Air Conditioning (HVAC) systems benefit greatly from the use of Finned Tubular Heaters. Compact design: These heaters fit easily into ductwork, saving space in HVAC installations. Quick response: They heat up rapidly, allowing for fast temperature adjustments in buildings. Low maintenance: Their simple design means fewer parts that can break down or need replacing. These heaters are also used in: Industrial dryers Air curtains Heat recovery systems The efficiency of Finned Tubular Heaters has led to a 40% increase in their use in commercial HVAC systems since 2020. 5. Chemical Processing: Maintaining Reaction Temperatures In the chemical industry, maintaining precise temperatures is crucial for successful reactions and product quality. Corrosion resistance: Many Finned Tubular Heaters are made with materials that resist chemical corrosion. Explosion-proof options: Special models are available for use in hazardous environments. Fine temperature control: These heaters can maintain temperatures within 0.5°C, crucial for sensitive chemical processes. These heaters are also used in: Distillation columns Storage tank heating Pipeline pre-heating The reliability of Finned Tubular Heaters in maintaining exact temperatures has led to a 35% increase in their adoption in the chemical processing industry over the past four years. Final Words Finned Tubular Heaters have proven their worth across various industries. Their versatility, efficiency, and precision make them an excellent choice for many heating applications. As technology advances, we can expect to see even more innovative uses for these powerful heating devices. From food processing to chemical reactions, Finned Tubular Heaters are helping industries improve their processes, reduce costs, and enhance product quality.
5 Reasons Why You Need a Mold Cartridge Heater Manufacturer for Manufacturing Needs

Mold cartridge heater manufacturers are essential partners in optimizing manufacturing processes. These specialists design, produce, and supply heaters tailored to specific industrial needs, ensuring precise temperature control and efficient heat transfer. Whether you’re in the plastics, rubber, or food industry, collaborating with a reliable mold cartridge heater manufacturer is crucial for achieving production excellence. Reason 1: Consistent and Precise Temperature Control Maintaining consistent and precise temperature control is paramount in manufacturing. Mold cartridge heaters excel in this area, offering several advantages: Uniform Heat Distribution: Cartridge heaters are designed to distribute heat evenly across the mold cavity, preventing hot or cold spots. This uniformity is essential for producing products with consistent dimensions and quality. Rapid Heat-Up and Cool-Down Times: These heaters quickly reach the desired temperature, reducing cycle times and increasing production efficiency. Similarly, they cool down rapidly, allowing for faster mold turnover. Accurate Temperature Regulation: With advanced temperature controllers, mold cartridge heaters can maintain precise temperature settings, ensuring product consistency and minimizing defects. Reason 2: Enhanced Product Quality High-quality products are the cornerstone of business success. Mold cartridge heaters contribute significantly to product quality by: Preventing Defects: Consistent temperature control reduces the risk of defects such as warping, shrinkage, and burns. This leads to a higher percentage of acceptable products and less waste. Improving Product Performance: Precise temperature management can enhance product performance characteristics, such as strength, durability, and flexibility. Meeting Industry Standards: Many industries have stringent quality standards. Mold cartridge heaters help manufacturers meet these requirements by ensuring product consistency and reliability. Reason 3: Increased Production Efficiency Efficiency is key to maximizing profits in manufacturing. Mold cartridge heaters boost production efficiency through: Reduced Cycle Times: Faster heat-up and cool-down times translate to shorter cycle times, allowing for more production runs within a given period. Optimized Energy Consumption: Efficient heat transfer minimizes energy waste, leading to lower operating costs. Improved Equipment Uptime: Reliable mold cartridge heaters reduce downtime caused by equipment failures, maintaining production continuity. Reason 4: Versatility and Adaptability Mold cartridge heaters are incredibly versatile and can be adapted to various manufacturing processes and equipment: Wide Range of Sizes and Wattages: Cartridge heaters are available in various sizes and wattages to suit different mold cavities and heating requirements. Customizable Designs: Manufacturers can often customize cartridge heaters to meet specific application needs, ensuring optimal performance. Easy Installation and Replacement: These heaters are relatively simple to install and replace, minimizing downtime and maintenance costs. Reason 5: Long Lifespan and Durability Investing in high-quality equipment is essential for long-term profitability. Mold cartridge heaters offer: Durable Construction: Constructed from robust materials, cartridge heaters can withstand harsh manufacturing environments and temperature fluctuations. Extended Lifespan: With proper care and maintenance, mold cartridge heaters can have a long lifespan, reducing replacement costs. Cost-Effective Solution: While the initial investment might be higher, the long-term benefits in terms of efficiency, product quality, and reduced downtime make mold cartridge heaters a cost-effective choice. Last Word Mold cartridge heater manufacturers are invaluable partners in achieving manufacturing excellence. By providing custom-designed, high-performance heaters, these experts help businesses optimize production processes, enhance product quality, and improve overall efficiency. If you’re looking to elevate your manufacturing operations, collaborating with a reputable mold cartridge heater manufacturer will be your best decision.