How Much Electricity Does a Tubular Heater Needs
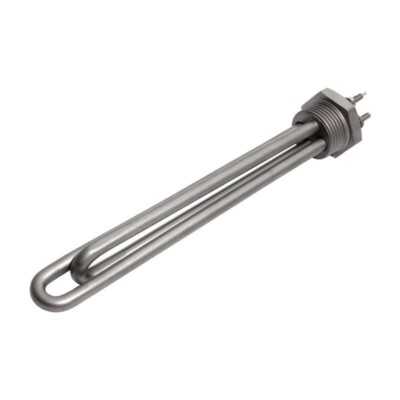
Tubular heaters are popular for applications where compact and efficient heating is needed. They’re used in greenhouses, bathrooms, workshops, and even industrial cabinets. But a common question remains: how much electricity does a tubular heater need? Knowing the answer helps control energy consumption and reduce utility costs. Wattage Ratings and Typical Use Cases Tubular heaters are manufactured in a wide range of wattages. The power requirement varies depending on the length, diameter, and material of the heater. The most common domestic tubular heaters are rated: 60W to 240W for single-room or localized applications 300W to 500W for continuous heating in small spaces Industrial units often exceed 1000W, sometimes reaching 3000W or more. Calculating Electricity Usage Electricity usage is typically calculated in kilowatt-hours (kWh), the standard billing unit used by utility companies. To calculate how much electricity a tubular heater needs, use this formula: Energy Consumption (kWh) = Power (W) x Time (Hours) / 1000 Let’s say you’re using a 250W heater for 10 hours: 250 x 10 = 2,500 watt-hours 2,500 / 1000 = 2.5 kWh If your electricity rate is $0.15 per kWh, that’s $0.375 per day in energy cost. Monthly Estimate Example A 250W heater running 10 hours daily for 30 days: 2.5 kWh/day x 30 = 75 kWh/month 75 x $0.15 = $11.25/month Power vs. Heat Output Efficiency Tubular heaters are nearly 100% efficient in converting electrical energy to heat. That means almost all the electricity drawn is used for warming the space. However, the effectiveness of that heat depends on: Room insulation quality Thermostat usage Heat loss through walls/windows External temperatures Thermostats Save Energy One of the most effective ways to reduce electricity usage is by using a thermostat. It allows the heater to cycle on and off instead of running continuously. For example: A thermostat that maintains 20°C may reduce runtime by 30%-50%. This means a 250W heater could operate for just 5-7 hours instead of 10, reducing costs significantly. Influencing Factors on Power Consumption Several elements affect how much power your heater consumes: Ambient Temperature: Colder environments require longer operation times. Heater Length & Surface Area: Longer tubes cover more area but also draw more power. Material Composition: Aluminum sheaths heat faster than stainless steel, affecting efficiency. Control Systems: Timers and thermostats help manage operation intelligently. Energy Saving Tips Install Timers: Turn the heater off automatically during non-peak hours. Improve Insulation: Seal gaps and add weather stripping to retain heat. Use Reflective Panels: Place them behind the heater to direct heat into the room. Routine Maintenance: Clean dust and debris from the heater to maintain efficiency. Industrial Applications and Power Needs In manufacturing and commercial sectors, tubular heaters are used for pipe heating, fluid warming, and freeze protection. Power needs scale dramatically: 5kW to 15kW systems are not uncommon. These systems often include multi-zone controls to reduce total power use. For example, a 6kW system operating 8 hours a day uses: 6 x 8 = 48 kWh/day At $0.15 per kWh, that’s $7.20/day, or over $200/month Cost vs. Utility Although the cost may seem high, tubular heaters are often preferred for their reliability and compact design. They’re used in places where radiant or convection heating isn’t practical. Their minimal maintenance and ability to deliver targeted heat make them cost-efficient long-term. Safety and Compliance Ensure heaters comply with international standards like CE and UL. Safety features such as: Overheat protection Thermal cut-off switches Enclosure ratings (IP65, etc.) …all contribute to safe operation and indirectly reduce wasteful power consumption. Final Takeaway The electricity required by a tubular heater depends on its wattage, usage pattern, and control features. Small domestic units typically use 1–2.5 kWh/day, while larger industrial systems can use 50 kWh/day or more. By applying intelligent controls and using efficient designs, users can balance performance with energy savings.
What is a Ceramic Furnace
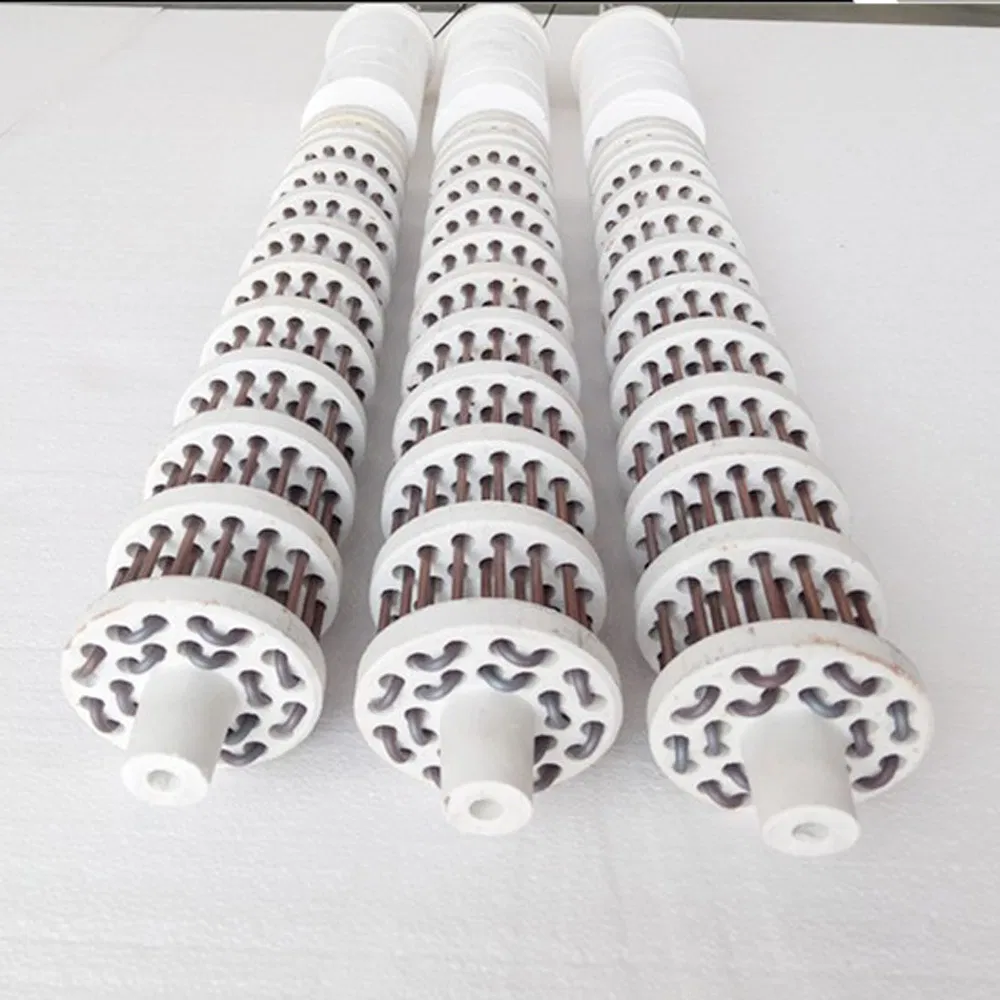
Precision manufacturing, electronics, and advanced materials all depend on controlled high-temperature processes. At the core of many of these processes is a ceramic furnace. But this isn’t just another heat chamber. It’s a critical technology that allows materials to be treated, altered, and perfected with exceptional accuracy. A ceramic furnace heater is a high-temperature heating system specifically designed to process materials using ceramic insulation or ceramic components within its structure. These furnaces are often used for sintering, heat treatment, material testing, and calcination in industries like metallurgy, electronics, and advanced ceramics. The defining characteristic of a ceramic furnace is its ability to maintain uniform, stable temperatures up to 1800°C (3272°F), depending on the model. This stability is crucial for processes like ceramic sintering, where consistent heat is necessary to bond particles without melting them. There are two primary configurations: Chamber Furnaces: Fully enclosed systems with ceramic fiber insulation lining the heating chamber. Used for batch processing. Tube Furnaces: Cylindrical chambers with ceramic tubes. Ideal for controlled atmosphere reactions and small-scale research. Why Ceramic Furnaces Matter Traditional metal-based furnaces can’t handle certain conditions without deforming or contaminating the materials being processed. Ceramic furnaces, however, are chemically stable and thermally resistant. That makes them essential for: High-purity environments: No risk of contamination from metal parts. Extreme temperatures: Ceramics withstand more heat than metal. Energy efficiency: Modern ceramic insulation reduces heat loss. Ceramic insulation materials, such as alumina (Al₂O₃), zirconia (ZrO₂), or mullite, are engineered to trap heat and reflect thermal energy back into the chamber. These materials exhibit: Low thermal conductivity High refractoriness Excellent dimensional stability Key Applications Ceramic furnaces aren’t just for research labs. They play a central role in many industrial workflows: Ceramic and glass sintering: Powders are consolidated into dense, durable parts. Powder metallurgy: Metal powders are heat-treated to form strong components. Semiconductor processing: Used for diffusion and oxidation in chip fabrication. Material testing: Simulates extreme environments for aerospace and automotive parts. Atmosphere Control Options In some cases, materials must be treated in inert or reducing atmospheres to prevent oxidation. Tube-type ceramic furnaces are often paired with gas flow systems that allow precise atmosphere regulation. Common gases used include: Argon Nitrogen Hydrogen This capability is critical for synthesizing advanced materials like battery cathodes, fuel cells, and nanomaterials, where air exposure could ruin results. Choosing the Right Ceramic Furnace When selecting a ceramic furnace, several factors should be evaluated: Maximum temperature: Match the furnace to your process requirements. Heating elements: MoSi₂ and SiC are the most common. MoSi₂ can handle higher temperatures but is more brittle. Chamber size: Depends on whether you’re doing research or industrial-scale production. Atmosphere compatibility: Not all ceramic furnaces support gas environments. Final Thoughts Ceramic furnaces offer unmatched precision and thermal control for industries that demand high-performance heat treatment. For engineers, researchers, and manufacturers, understanding the capabilities and limitations of ceramic furnaces isn’t optional. It’s essential for pushing material performance to new levels. If you’re investing in quality, consistency, and advanced material processing, then knowing how a ceramic furnace works and choosing the right one can directly impact the success of your operation.
Are Cartridge Heaters Waterproof ?
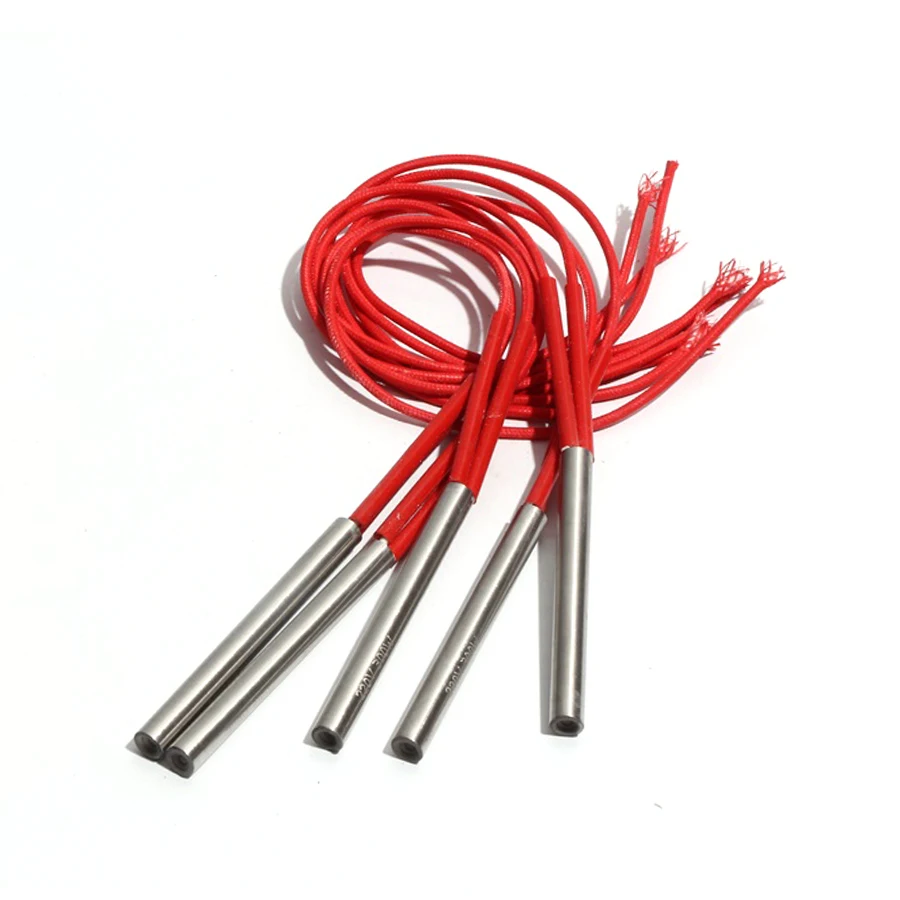
A cartridge heater is often used in industrial applications where precision, durability, and high heat density are crucial. But when it comes to environments with moisture, water splashes, or full submersion, a key question surfaces: are cartridge heaters waterproof? The short answer is ‘standard cartridge heaters are not inherently waterproof’. However, specific design modifications can improve their resistance to moisture, especially for micro cartridge heater models used in compact or sealed systems. Let’s unpack what this means in practical terms. What Is a Cartridge Heater? A cartridge heater or a micro cartridge heater is a cylindrical heating element that transfers heat through direct contact. It’s inserted into drilled holes in metal blocks, molds, or platens to heat solids, liquids, or gases. These heaters are known for: High watt density Rapid heat transfer Tight tolerances Precise temperature control Micro cartridge heaters are smaller variants designed for compact spaces like 3D printing nozzles, medical devices, or aerospace tools. Water and Electricity: A Dangerous Mix Water is highly conductive. When it seeps into a cartridge heater, it can lead to: Electrical short circuits Corrosion of internal components Premature failure Shock hazards Standard cartridge heaters have a stainless steel sheath and internal insulation, often made of magnesium oxide (MgO). While MgO is an excellent thermal conductor and electrical insulator, it’s hygroscopic and it absorbs moisture. When that happens, the insulation becomes conductive, compromising the heater’s safety and function. Are Any Cartridge Heaters Waterproof? Technically, no cartridge heater is truly “waterproof” unless it’s been hermetically sealed. Most off-the-shelf models are moisture-resistant at best. However, certain designs offer varying degrees of water protection. Here’s how manufacturers improve water resistance: Sealed leads: Epoxy potting, Teflon seals, or silicone overmolds at the lead exit area help block water entry. Hermetic sealing: High-end micro cartridge heaters can be laser welded or glass-sealed to prevent any moisture ingress. IP-rated designs: Some custom heaters meet Ingress Protection (IP) standards like IP65 or IP67, which define protection against dust and water. Important: Even if a cartridge heater is IP67-rated (protected against immersion up to 1 meter), that doesn’t mean it can withstand prolonged submersion or pressurized jets without failure. Applications Requiring Waterproof Heaters Some environments absolutely require moisture protection: Food processing Medical sterilization Laboratory equipment Marine instrumentation Outdoor industrial heating In these cases, micro cartridge heaters must be specifically engineered for exposure to water, humidity, or steam. For example, in autoclave sterilizers, the heater must withstand repeated cycles of pressurized steam at over 120°C. Should You Choose a Waterproof Micro Cartridge Heater? If your application involves: High humidity Steam exposure Frequent washdowns Condensation risks Then yes, investing in a sealed or IP-rated micro cartridge heater is smart. It extends lifespan, improves safety, and reduces downtime. Before placing an order, ask your supplier the following: “Is this heater sealed at the lead end?” “What is the maximum moisture it can withstand?” “Can it be customized for my application environment?” Final Takeaway Standard cartridge heaters aren’t waterproof. They can be damaged or fail prematurely when exposed to moisture. But with the right construction, sealed ends, protective coatings, and possibly hermetic welding, a micro cartridge heater can resist moisture and work reliably even in wet environments. Choosing the right heater is not just about heat, it’s about environmental fit. Always match your equipment to its operating conditions for long-term success.
What is The Significance of Fins In a Heater
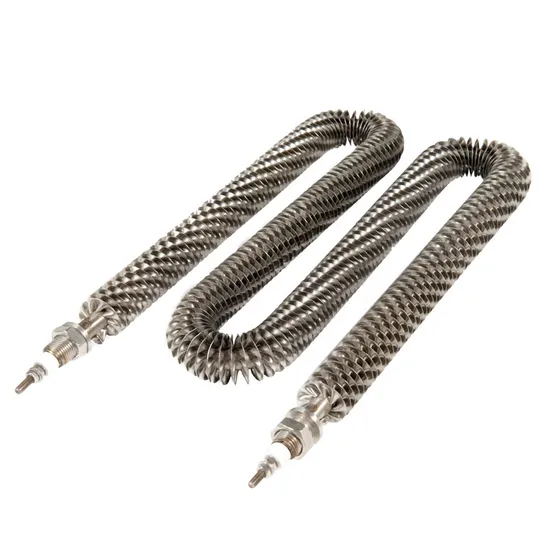
A Finned Cartridge Heater is only as efficient as its surface area allows. That’s where fins come into play. These thin metal extensions dramatically increase the surface area of a heater, improving heat transfer to air or gas without requiring extra power. They’re a small component with a major impact on efficiency, durability, and cost savings. So, what exactly are fins, and how do they work in a heater? Fins in a heater are metallic extensions attached to the surface of the heater sheath. Their primary job is to transfer more heat to the surrounding environment by increasing the surface area. Think of them as heat amplifiers small parts that make a big difference. Why fins are essential in industrial heating In industries that rely on precise heating, such as plastics, packaging, food processing, and HVAC, finned heaters outperform traditional designs. They offer: Faster heat dissipation Lower sheath temperature Longer heater life Energy savings Compact size with higher efficiency These benefits are particularly important in air heating and convection heating applications, where the surrounding medium (air or gas) isn’t a good conductor. How fins increase efficiency Finned Cartridge Heaters use aluminum or stainless steel fins welded or mechanically fixed to the outer sheath. This design promotes superior airflow contact, allowing the heater to transfer thermal energy at a faster rate. Here’s what happens: Heater core generates heat. Heat travels to the sheath. Fins attached to the sheath absorb and radiate heat outward. Air or gas moving past the fins picks up this heat efficiently. Without fins, much of the heat would stay trapped at the surface or be transferred slowly, leading to higher energy costs and potentially shorter heater life due to thermal stress. Where fins are most effective Finned heaters shine in these use cases: Air ducts – More heat is delivered over a shorter length. Drying systems – Uniform airflow and consistent heat are critical. HVAC systems – Better heat control in smaller enclosures. Industrial ovens – Faster heating with reduced energy draw. These environments require consistent, safe, and cost-effective heating. That’s where fins prove their worth. Material and design considerations Not all fins are created equal. The material and shape of the fins determine how effective they are. Common fin materials include: Aluminum – Lightweight, great for high-velocity airflow, and cost-effective. Stainless steel – Durable, corrosion-resistant, ideal for high-temp or harsh environments. Fin shapes and patterns affect performance: Helical wrap – A continuous spiral that boosts airflow contact. Louvered fins – Improve turbulence and enhance thermal exchange. Straight fins – Simple and durable, suitable for slow-moving air. Choosing the right fin design depends on application variables like airflow speed, target temperature, and space constraints. Maintenance and safety factors Finned heaters require less maintenance than traditional heaters due to lower surface temperatures and better efficiency. However, for optimal performance: Clean fins regularly to prevent dust buildup, especially in air ducts. Avoid blocking airflow, as restricted movement reduces thermal transfer and can overheat the unit. Ensure correct mounting, as vibration or poor alignment affects fin contact and reduces performance. Final Thoughts Fins are more than just metal attachments they are a crucial enhancement to the Finned Cartridge Heater design. By expanding the heater’s surface area, fins boost heat transfer, lower energy consumption, and extend operational life. If you’re in a business where reliable heat is mission-critical, understanding how fins affect heater performance isn’t just helpful, it’s necessary. Smart fin selection and heater design can be the difference between consistent productivity and costly downtime.
What is a Mica Band Heater Used For
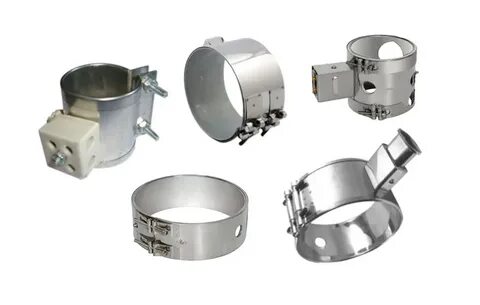
A Band Heater Manufacturer makes heaters that go around things like metal barrels or pipes to make them hot. One type they make is a mica band heater. These heaters are wrapped around machines that need heat to melt or soften stuff. They’re super helpful in places like factories. People working with plastic or food often use them. In this blog, you will learn where mica band heaters are used, how they work, and why they matter. What is a Mica Band Heater? A mica band heater is a round heater. It fits tightly around a metal surface. It has a metal shell, mica sheets inside, and a heating wire. The mica sheets hold the heat in place. The wire gets hot when you plug it in. The metal shell keeps the heat from going out too fast. These heaters work best for things with a round shape. Key parts of a mica band heater: Outer shell: Made of steel or stainless steel Mica layers: Help to hold the wire and send heat Heating wire: Usually made from nickel or chrome Clamping device: Keeps it stuck tightly to the machine Where are Mica Band Heaters Used? Mica band heaters are seen in many big machines. They help when things must stay hot or melt. Here are some common uses: Plastic injection machines: Heat plastic so it can be shaped Extruders: Keep plastic flowing smoothly Blow molding tools: Help form bottles and containers Food packaging lines: Keep food flowing or sealing right Drum heating: Warm up sticky liquids like glue or oil 3D printers: Heat parts that need steady warmth Table of industries and how they use mica band heaters: Industry Use Case Plastic manufacturing Melts and molds plastic Food processing Keeps chocolate or sauces warm Chemical plants Heats up tanks or mixing drums Printing Keeps ink at the right thickness Oil & gas Warms up barrels for smooth flow Why Do Companies Choose Mica Band Heaters? These heaters are easy to fit. They heat up fast. They are not too costly. They last a long time if used right. Most companies like them because they don’t waste much power. Main benefits include: Fast heating: Gets hot quickly Even heat spread: No cold spots Low cost: Cheaper than ceramic heaters Easy to install: Simple clamps hold them in place Custom sizes: Can be made for many shapes How Do You Pick the Right Mica Band Heater? Picking the best one is key. You need the right size, shape, and heat level. A Band Heater Manufacturer can help with this. They check your machine and make a heater that fits just right. Things to know when picking one: Size of the barrel or pipe Temperature needed Power source (volts and watts) Type of metal surface Room conditions (wet, dusty, etc.) Always talk to experts before buying. They help you avoid mistakes. How to Keep Your Heater Working Long? These heaters last longer when cared for. They must be kept tight and clean. If they get loose, heat escapes. That can burn the wires. Helpful care tips: Check for loose clamps Keep surface dry and clean Don’t touch wires too much Use the right power supply Turn off when not in use If your heater breaks, it can stop the whole machine. This can cost a lot of money. Final Thoughts A mica band heater is small but strong. It helps in plastic, food, oil, and other big jobs. It keeps machines warm so they can do their work. If you need steady and safe heat, ask a trusted band heater manufacturer to make one for your job. They’ll help you find what fits best and lasts long. Need help choosing the right one? Talk to a Cheri Heater today.
5 Common Industrial Heating Challenges (and How to Solve Them)
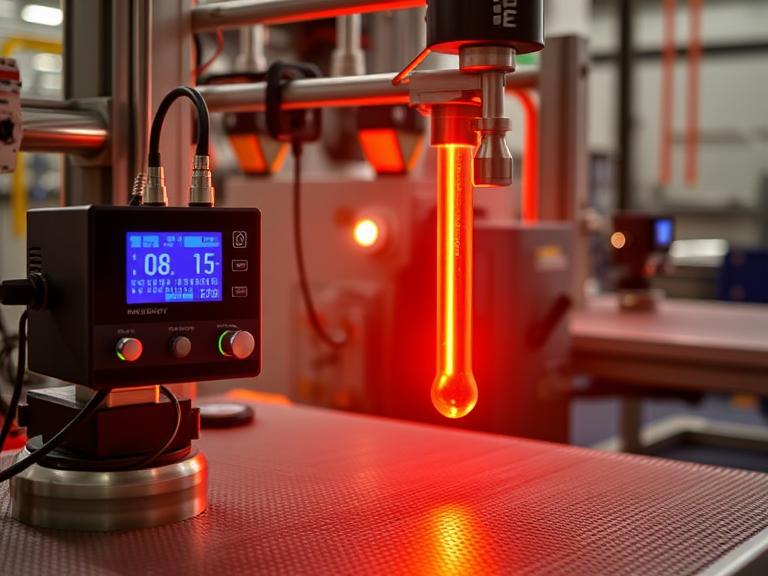
In industrial processes, efficient and consistent heating is vital to ensuring product quality, energy efficiency, and smooth operations. However, even the most advanced heating systems encounter challenges that can affect productivity and lead to costly downtimes. Whether you’re in manufacturing, food processing, chemical production, or any other industry relying on thermal systems, understanding common heating challenges — and knowing how to address them — is key to maintaining operational efficiency. In this post, we’ll explore the five most common industrial heating challenges and provide practical solutions to help you overcome them. 1. Inconsistent Temperature Control The Challenge: One of the most frequent issues in industrial heating systems is temperature fluctuation. Inconsistent temperatures can compromise product quality, especially in processes requiring precise thermal conditions. Factors contributing to this include poor insulation, aging components, and inefficient control systems. The Solution: Implement advanced temperature controllers with PID (Proportional-Integral-Derivative) algorithms. These controllers adjust heat output in real-time based on feedback, reducing overshooting and temperature swings. Additionally, regularly calibrate sensors and check insulation to maintain thermal efficiency. Pairing this with robust data logging helps operators spot irregularities early. 2. Energy Inefficiency and High Operating Costs The Challenge: Heating processes are among the largest energy consumers in industrial facilities. Inefficient systems lead to excessive energy use and inflated utility bills. This not only affects profitability but also contributes to a higher carbon footprint. The Solution: Optimize energy consumption by upgrading to high-efficiency heating elements and integrating automation. Using timers, motion sensors, and programmable logic controllers (PLCs) helps reduce unnecessary heating during downtimes. Additionally, consider energy audits to pinpoint inefficiencies and recover waste heat through heat exchangers or thermal insulation upgrades. 3. Equipment Wear and Short Lifespan The Challenge: Industrial heaters often operate under harsh conditions — high temperatures, corrosive environments, and long operating hours. Over time, these conditions degrade the heating elements, reducing their efficiency and increasing the risk of breakdowns. The Solution: Use heaters made from durable materials such as Incoloy, stainless steel, or ceramic-coated elements, depending on the application. Schedule preventive maintenance, and monitor performance metrics to detect early signs of wear. Investing in quality components and performing routine inspections can significantly extend equipment life and minimize unexpected failures. 4. Slow Heat-Up Times The Challenge: Long heat-up periods can delay production schedules and decrease overall throughput. This often results from underpowered heating elements, poor heat transfer, or system design limitations. The Solution: Evaluate the system design to ensure it matches the heating demand. Improving heat transfer surfaces, optimizing element placement, and using faster-response heaters can drastically cut down heat-up time. In certain scenarios, switching to an immersion cartridge heater can improve direct heat transfer and reduce energy waste — especially in liquid heating applications. 5. Control System Failures The Challenge: Many industrial heating problems stem from outdated or malfunctioning control systems. When controllers fail, they can either shut down operations or allow heaters to overrun, leading to overheating and equipment damage. The Solution: Modernize your control systems with digital interfaces and IoT-enabled sensors that provide real-time data and remote monitoring. Regular software updates, diagnostics, and system redundancy planning ensure that a single point of failure doesn’t cripple your operation. With smart control integration, businesses gain both safety and efficiency. Bonus Tips to Enhance Heating System Performance While solving specific challenges is essential, taking a holistic approach can elevate your heating system’s overall performance. Here are some bonus tips: Use Predictive Maintenance Tools: Technologies like vibration analysis, thermography, and smart sensors help anticipate failures before they occur. Monitor Energy Use: Real-time energy monitoring platforms allow facilities to make data-driven decisions, cutting down on waste. Train Your Staff: Well-trained technicians can identify minor issues before they turn into major disruptions. Invest in regular training and certifications. Conduct Seasonal System Reviews: Temperature and humidity variations can affect performance. A quarterly or seasonal review can help adjust settings and catch problems early. Final Thoughts Industrial heating systems are the backbone of countless operations. Addressing common challenges like inconsistent temperatures, energy waste, equipment degradation, and slow responsiveness can lead to significant performance and cost benefits. With the right combination of technology upgrades, preventive maintenance, and smart system design, you can enhance reliability and boost productivity. By identifying and solving these challenges proactively, industries not only avoid unplanned downtimes but also future-proof their operations in an increasingly energy-conscious market. Remember, each heating application is unique. Whether you’re managing a large manufacturing plant or a specialized chemical processing unit, choosing the right components — such as an immersion cartridge heater for targeted, efficient heat delivery — can make all the difference.
How to Improve Temperature Accuracy in Small-Scale Manufacturing
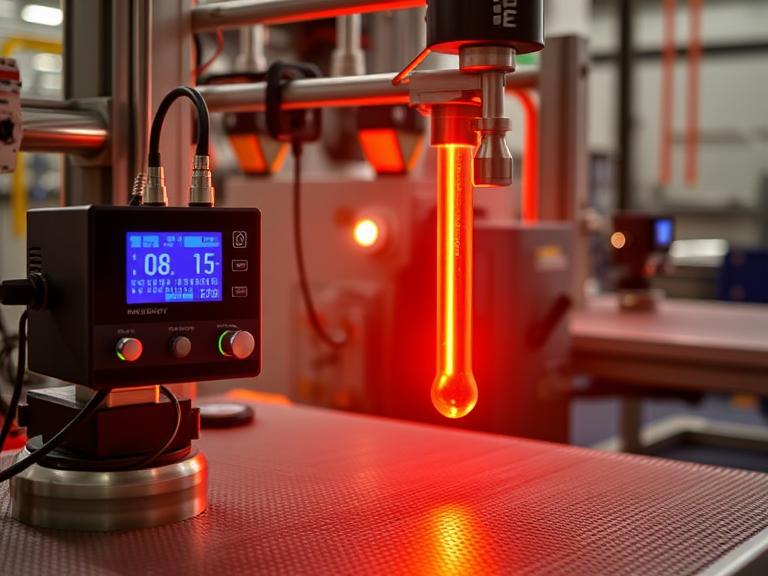
In today’s rapidly evolving industrial landscape, efficiency and control are the backbone of every high-performing system. Whether it’s plastic molding, packaging, laboratory experiments, or food processing, accurate temperature management plays a crucial role in ensuring consistent output, energy savings, and operational safety. At Cheriheater, we understand how even the smallest improvement in thermal performance can drive major gains. That’s why we focus on reliable heating technologies built for demanding environments. In this blog post, we’ll take a deeper look into how modern heating components can streamline processes, improve product quality, and reduce energy waste, plus how to choose the right tools for the job. The Challenge of Industrial Heating Heating systems are the lifeblood of many industries. From maintaining molten plastic in an injection molding machine to sealing food packages or sterilizing equipment, heat is a required force. But here’s the challenge: inconsistent heating leads to uneven results. Imagine trying to mold plastic with fluctuating temperatures—you’d end up with warped or defective parts. Or think about lab testing where even a few degrees off can distort your entire dataset. It’s not just about heat; it’s about controlled, precise, reliable heat. Why Precision Heating Is Non-Negotiable 1. Minimizes Waste Consistent heat ensures uniformity. That means fewer rejected products and more efficient production cycles. 2. Protects Equipment When components are not overheated or exposed to thermal shock, their life expectancy increases significantly. 3. Improves Energy Efficiency Controlled heating eliminates unnecessary power usage. Less energy wasted equals more money saved. 4. Enhances Safety Overheating or erratic temperature swings can lead to system failures or even fire hazards. With the right equipment, these risks are minimized. Key Features to Look for in a Heating Solution Choosing the right heating component is not just about wattage or size—it’s about compatibility with your system and control over performance. Here are the top features to look out for: ● Rapid Heat-Up Time You want a heater that can reach operating temperature quickly without overshooting. ● Uniform Heat Distribution The element should provide even heating throughout the surface area to prevent hot spots. ● Compact Design In many cases, space is limited. A heating element should be powerful, yet compact enough to fit within tight setups. ● Integrated Sensing Advanced models include built-in temperature sensing components for real-time monitoring. Meet the Unsung Hero: Cartridge Heaters Cartridge heaters are cylindrical heating elements designed to be inserted into holes drilled in metal blocks. These heaters offer an excellent solution for localized heating and are widely used in dies, molds, platens, and packaging machinery. They are valued for: High watt density Efficient heat transfer Tight fit installation Long service life Many industries rely on these compact units to maintain heat directly where it’s needed, reducing energy loss and improving response time. Precision Gets an Upgrade: Thermocouples To go a step further, thermocouples are added to heating systems to monitor temperature in real time. These tiny devices generate a voltage signal based on the temperature difference between two dissimilar metals, making them highly accurate and responsive. Pairing a heater with a thermocouple is like adding a speedometer to a car—it doesn’t change how the car works, but it ensures you know exactly how it’s performing. For example, if you’re operating a precision-driven process like seal bar heating in packaging, you don’t want guesswork—you want exact numbers, consistent performance, and fast adjustments when needed. This is where a cartridge heater with thermocouple becomes incredibly effective, combining compact power with intelligent feedback in one integrated solution. Common Applications Here are just a few of the places where precision heating matters—and where solutions like cartridge heaters shine: Plastic Injection Molding Packaging & Sealing Machines Laboratory Instruments 3D Printing Platforms Food Processing Units Medical & Sterilization Equipment Each of these applications requires consistent, controlled heating within tight tolerances. That’s where engineered components make all the difference. Tips for Choosing the Right Heating Element If you’re planning to upgrade your heating setup or start from scratch, keep these practical tips in mind: 1. Know Your Operating Temperature Different applications call for different heat levels. Ensure the element is rated for your target range. 2. Measure Installation Area Precisely Cartridge heaters are typically press-fitted, so accurate sizing is essential. 3. Factor in Heat Loss Think about where heat might escape in your system—choose a heater that compensates accordingly. 4. Consider Lead Wire Configuration Lead wires should match the environmental and mechanical conditions of your setup. Why Choose Cheriheater? At Cheriheater, we’re more than just a heating element supplier—we’re your partner in precision heating. We manufacture and customize heaters that are trusted in applications around the world, with performance, safety, and durability at the core of every product. Our team is ready to help you select the right solution, whether it’s off-the-shelf or built to spec. From consultation to after-sales support, we’re committed to quality you can count on. Final Thoughts Precision heating is not a luxury—it’s a requirement in today’s industrial world. With the right tools in place, you can improve performance, ensure consistency, and protect your systems from unnecessary wear and tear. The combination of a smart design, reliable components, and responsive support can transform how your systems operate—and boost your bottom line.
How to Choose the Right Heating Solution for Your Manufacturing Needs
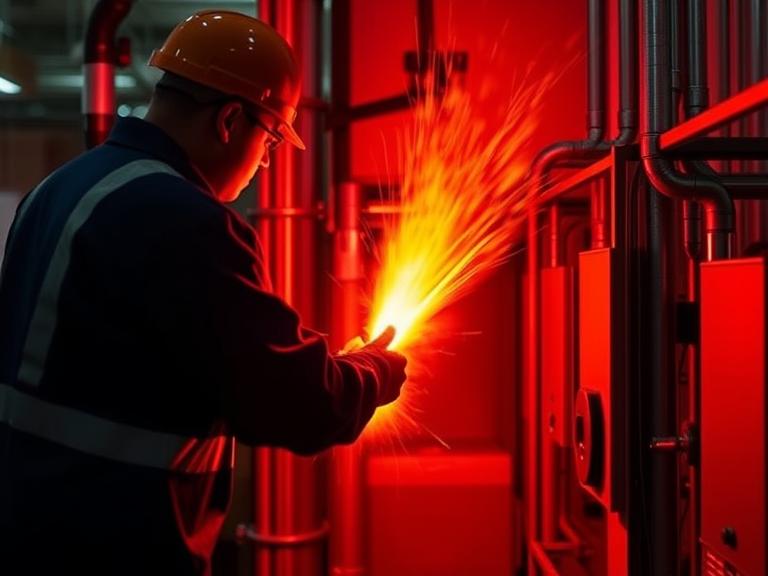
In the world of manufacturing, precision, efficiency, and consistency are essential. Whether you’re working with plastics, metals, chemicals, or food processing, heating systems are at the core of your operations. Choosing the right heating solution can significantly impact your productivity, energy consumption, and product quality. With so many technologies available—from cartridge heaters to infrared panels—how do you determine which one is right for your specific manufacturing needs? At Cheriheater, we specialize in helping manufacturers make informed decisions when it comes to industrial heating solutions. In this guide, we’ll walk you through the key factors to consider when choosing the most effective heating solution for your operation. 1. Understand Your Application Requirements The first step in choosing a heating solution is to thoroughly understand your application’s unique requirements. Every manufacturing process is different and demands specific parameters when it comes to: Temperature range: Some applications require precise, low-temperature control, while others may demand high heat. Heat-up time: Do you need rapid heat-up or is gradual warming acceptable? Material compatibility: Will the heater be in direct contact with your product or surrounding machinery? Environmental conditions: Is your process exposed to moisture, dust, or corrosive chemicals? Clearly identifying these requirements will help you narrow down which heating technologies are most suitable. 2. Evaluate the Type of Heater Needed There are several types of industrial heaters, each with unique benefits and ideal use cases. Some of the most common include: Cartridge Heaters These are compact, cylindrical heaters often used to heat metal blocks, molds, or tools. They offer high watt density and precise temperature control, making them ideal for applications like plastic molding or packaging machinery. Band Heaters Typically used to heat cylindrical surfaces such as pipes, nozzles, or drums. Band heaters are great for injection molding and extrusion equipment. Tubular Heaters These are versatile heaters that can be shaped into various configurations. Ideal for heating air, gases, and liquids, tubular heaters are often used in ovens, immersion tanks, and ducts. Infrared Heaters Perfect for non-contact heating, these are often used in curing, drying, and coating processes. Infrared heaters can offer energy savings and faster response times. Immersion Heaters Used for directly heating liquids, immersion heaters are common in chemical processing, water treatment, and oil heating applications. Matching the heater type to your process needs will ensure efficiency and longer operational life. 3. Assess Power Requirements and Energy Efficiency Another critical factor is the power requirement. How much wattage do you need to achieve and maintain your desired temperature? Choosing a heater with the correct watt density (watts per square inch) is vital to prevent overheating or underperformance. In today’s energy-conscious environment, energy efficiency is more important than ever. Look for heating solutions that offer: Uniform heat distribution Fast response times Integrated temperature sensors or controllers Minimal heat loss to the environment Using advanced controls and sensors not only boosts efficiency but also enhances safety and reduces operating costs. 4. Consider the Control Systems A heating system is only as effective as its controls. Precision in temperature regulation is crucial for many industrial processes. Depending on your process, you might need: Basic thermostats Digital controllers with programmable settings PLC (Programmable Logic Controller) integration for complex automation Choosing the right control system helps maintain consistent temperature levels, reduces waste, and improves product quality. 5. Think About Installation and Maintenance Ease of installation and maintenance are often overlooked but can have long-term cost implications. When choosing a heating solution, ask the following: Is it easy to integrate with existing equipment? Are replacement parts readily available? What is the expected lifespan? Is maintenance frequent or minimal? Opting for heaters that are modular or easy to replace can reduce downtime during maintenance or unexpected failures. 6. Safety and Compliance Standards Industrial heating systems must comply with safety and regulatory standards. Make sure the heater and its components are: Certified by relevant bodies (e.g., CE, UL, RoHS) Designed with built-in safety mechanisms like thermal cutoffs or overload protection Made with materials that suit your industry’s compliance requirements (e.g., food-grade stainless steel) Safety should never be compromised, especially when working in high-temperature or hazardous environments. 7. Work with a Reliable Supplier or Manufacturer One of the most important decisions is choosing who to partner with. A trustworthy heating element manufacturer can provide tailored solutions, expert advice, and after-sales support. Customization is often key in manufacturing, and working with an experienced manufacturer ensures your heating system is designed to your exact specifications. Look for a supplier with a solid track record, client testimonials, and the ability to design, prototype, and produce heaters in-house. This ensures quality control, fast lead times, and scalable production. 8. Factor in Budget vs. Long-Term ROI While initial cost is a key consideration, it’s equally important to evaluate long-term return on investment (ROI). A cheaper heater may save money upfront but could lead to higher energy bills, frequent repairs, or poor process control. Instead, weigh the total cost of ownership: Initial purchase price Installation and integration costs Operating and energy costs Maintenance and downtime Lifespan and reliability Choosing the right heating solution can result in higher productivity, lower energy bills, and fewer equipment failures—making it a smart long-term investment. Conclusion: Selecting the right heating solution for your manufacturing process involves a careful evaluation of technical requirements, energy efficiency, safety, and vendor reliability. By following a structured decision-making process and consulting with experts, you can ensure that your heating system delivers optimal performance and value. At Cheriheater, we pride ourselves on offering high-quality, custom-designed heating solutions for a wide range of industrial applications. Whether you’re in plastics, packaging, chemicals, or food production, we’re here to help you choose the best heating technology for your unique needs. If you’re looking to optimize your heating process, improve energy efficiency, and enhance product quality, contact our team today to discuss your project requirements.
Different Types of Heaters for Industrial Applications
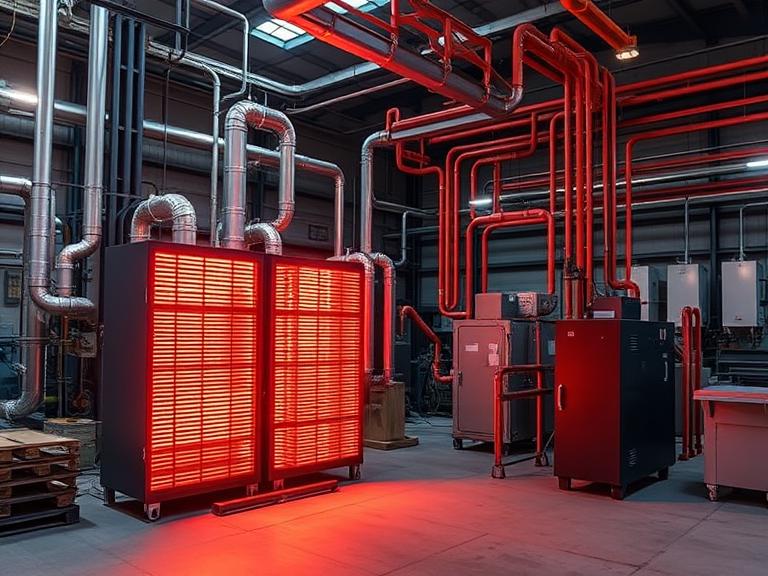
In industrial settings, heating solutions are crucial to ensuring smooth and efficient operations. Whether it’s for manufacturing, food processing, or other industrial processes, selecting the right type of heater can have a major impact on productivity and energy efficiency. With a wide range of options available, businesses must choose the best solution based on their specific needs. In this post, we will explore the various types of industrial heaters, discuss their benefits, and provide guidance on how to choose the best heater for your industrial application. 1. Electric Heaters: Versatile and Efficient Electric heaters are widely used in industrial applications due to their efficiency and precision. They convert electrical energy into heat, making them ideal for controlled environments where temperature regulation is critical. Types of Electric Heaters: Cartridge Heaters: One of the most common forms of electric heaters, cartridge heaters are compact, cylindrical heating elements that are often used in molds, tanks, and machinery requiring concentrated heat. These heaters are known for their high thermal efficiency and ease of integration into industrial systems. They are ideal when you need space-efficient solutions with precise heating control. Band Heaters: These heaters wrap around cylindrical surfaces, such as pipes or barrels, to provide even heat distribution. Commonly used in extrusion processes, they are ideal for operations where uniform heating is required. Why Choose Electric Heaters? Precise Control: Electric heaters, such as cartridge heaters, offer exceptional control, allowing for accurate temperature adjustments that are essential for many industrial processes. Energy Efficiency: They can heat spaces quickly without waste, making them a great choice for businesses aiming to minimize energy costs. Low Maintenance: Electric heaters typically require less maintenance compared to gas-powered models, contributing to lower operational costs. Electric heating solutions are ideal for companies that need reliable and easy-to-maintain heating systems for small or medium-sized applications. 2. Gas Heaters: Cost-Effective for Larger Spaces Gas heaters are commonly used in large industrial spaces where high heat output is necessary. They work by burning natural gas or propane to generate heat, making them more cost-effective for operations that need a significant amount of heat for large areas. Advantages of Gas Heaters: Lower Operating Costs: Gas-powered heaters tend to have lower operating costs when compared to electric heaters, especially for large-scale applications. High Heat Output: Gas heaters can produce a large amount of heat in a relatively short amount of time, making them ideal for large warehouses or production facilities. Versatility: They can be used in both indoor and outdoor applications, though proper ventilation is necessary for indoor use to avoid the accumulation of dangerous gases. While gas heaters are great for large spaces, they do require careful safety management and ongoing maintenance to ensure they function safely and efficiently. 3. Infrared Heaters: Ideal for Spot Heating Infrared heaters provide a unique heating solution by emitting infrared radiation to directly heat objects and surfaces, rather than heating the air around them. This makes infrared heaters especially useful for applications that require localized heating or when traditional convection heating would be inefficient. How Infrared Heaters Work: Infrared heaters emit radiation that directly heats objects in their line of sight. Unlike conventional heating systems that heat the air and rely on convection to spread warmth, infrared heaters focus on the target object, providing rapid heating with minimal energy waste. Applications of Infrared Heaters: Drying and Curing: Infrared heaters are widely used in industries like automotive and manufacturing for drying paint or curing materials. Food Processing: In food production, infrared heating is used for drying or cooking food products quickly and evenly. Why Use Infrared Heaters? Energy Efficient: Infrared heaters provide targeted heating, minimizing energy loss and increasing efficiency. Rapid Heating: Infrared heaters can heat objects almost instantly, reducing waiting times in high-speed production processes. Minimal Air Movement: Infrared heaters are ideal for processes that require minimal air movement, such as in cleanrooms or laboratory settings. Infrared heaters are an excellent option for industries that require quick and efficient spot heating in specific areas. 4. Immersion Heaters: Effective Heating for Liquids Immersion heaters are designed for heating liquids directly within tanks or other containers. This type of heater is commonly used in industries such as chemical processing, food production, and pharmaceuticals, where precise liquid heating is essential. How Immersion Heaters Work: Immersion heaters are placed directly into the liquid that needs to be heated. This direct contact between the heating element and the liquid ensures uniform and efficient heating. Advantages of Immersion Heaters: Direct Heating: Since the heater is submerged in the liquid, it directly heats the fluid, which leads to more efficient heating compared to external heating methods. Cost-Effective: Immersion heaters are often more affordable than other heating systems, making them a popular choice for many businesses. Versatility: They can be used to heat a wide variety of liquids, including water, oils, and chemicals. Immersion heaters are ideal for any industrial application that requires the heating of liquids, such as tanks or vats. 5. Choosing the Right Heater: Key Considerations When selecting the right heating solution for your industrial application, several key factors should be considered to ensure that the system you choose meets your operational needs effectively: 1. Space and Heating Area: For small, localized heating, cartridge heaters are an excellent choice, as they offer high efficiency in tight spaces. Larger spaces or areas requiring significant heat output may be better suited to gas heaters or infrared heating systems. 2. Energy Efficiency: If energy efficiency is a top priority, electric heaters, especially cartridge heaters, provide excellent performance with minimal waste. 3. Temperature Control Requirements: Electric heaters with precise temperature control are ideal for applications requiring constant, reliable heat, such as those in the manufacturing or pharmaceutical industries. 4. Maintenance and Safety: Electric heaters like cartridge heaters tend to require less maintenance than gas heaters. Consider the level of ongoing maintenance your business can handle when making a choice. 5. Application Type: For heating liquids, immersion heaters are the go-to solution. For large areas, gas or infrared heaters
Top Applications of Micro Cartridge Heaters in Modern Industry
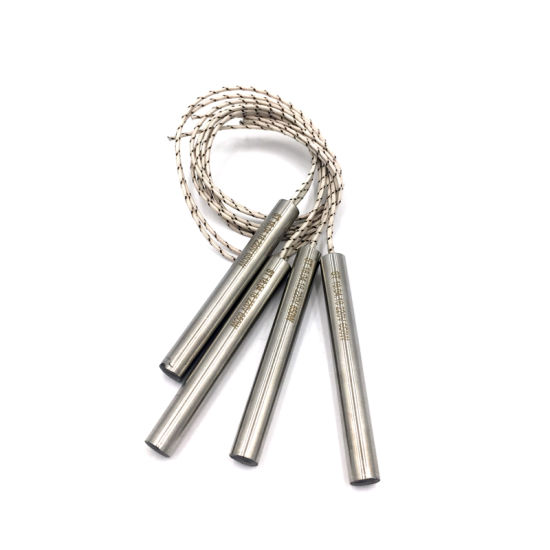
Micro cartridge heaters are compact, high-performance heating elements used in a wide range of modern industrial applications. Designed for precision, reliability, and efficiency, these small heaters deliver concentrated heat exactly where it’s needed. Their versatility and robust construction make them essential components across many industries. Here’s a closer look at the top applications of micro cartridge heaters today: 1. Medical Equipment In the medical field, precision and consistency are crucial. Micro cartridge heaters are widely used in devices such as blood analyzers, diagnostic equipment, and surgical instruments. Their ability to maintain exact temperatures helps ensure accurate test results and improves patient safety. Additionally, these heaters are ideal for fluid warming applications, helping maintain critical temperatures for IV fluids and surgical irrigation. 2. Plastic Injection Molding Plastic manufacturing heavily relies on micro cartridge heaters, especially for mould heating. They provide fast, even heat to small, confined spaces within molds, ensuring optimal material flow and product quality. Their compact design allows them to fit perfectly into mold cavities, improving cycle times and reducing production costs. 3. Aerospace Industry Aerospace technology demands high precision under extreme conditions. Micro cartridge heaters are used in de-icing systems, fluid delivery systems, and instrumentation. They help maintain stable temperatures for critical sensors and valves, ensuring aircraft performance and safety in various environments. 4. Packaging Machinery Modern packaging machines require consistent, controllable heat for processes such as sealing, cutting, and forming. Micro cartridge heaters are ideal for heating sealing bars, nozzles, and other small areas in packaging equipment. Their quick heating capabilities improve operational efficiency and ensure high-quality packaging results. 5. Semiconductor Manufacturing Semiconductor production involves extremely delicate processes that require clean, controlled environments. Micro cartridge heaters are used to heat chambers, wafers, and gas delivery systems. Their high precision and clean operation ensure minimal contamination, which is critical for producing high-quality semiconductor components. 6. Food and Beverage Processing Maintaining specific temperatures is vital in food and beverage processing for product quality and safety. Micro cartridge heaters are commonly used in coffee machines, food packaging equipment, and filling machines. Their fast response times and reliability help manufacturers meet strict hygiene and performance standards. 7. 3D Printing Additive manufacturing, particularly 3D printing, benefits greatly from micro cartridge heaters. These heaters maintain the correct temperature of the printer’s nozzle and build platform, ensuring smooth material extrusion and strong layer adhesion. As 3D printing technology evolves, the demand for precise, efficient heating solutions like micro cartridge heaters continues to grow. 8. Die-Casting In die-casting processes, maintaining consistent mold temperatures is essential to achieving high-quality metal parts. Micro cartridge heaters provide the necessary heat control in die-casting molds, reducing defects such as porosity and improving the structural integrity of the final product. Conclusion Micro cartridge heaters have become indispensable across various industries due to their precision, reliability, and adaptability. From medical devices to aerospace systems, their role in improving efficiency, safety, and product quality cannot be overstated. As industries continue to innovate, the applications of micro cartridge heaters are expected to expand even further, making them a cornerstone of modern manufacturing technology.