Finned Cartridge Heater – Reliable Heating Solutions for Industrial Applications

Looking for a high-performance heating solution tailored to your industrial needs? Our Finned Cartridge Heater is the ideal choice for businesses that demand efficiency, durability, and consistent performance. Designed with precision engineering, this advanced heater is built to optimize thermal transfer and provide reliable performance across a wide range of applications. Key Features and Benefits Enhanced Heat Transfer The integrated fins maximize the surface area for superior heat dissipation, ensuring consistent temperature control and improved energy efficiency. Customizable Design Available in a variety of diameters, lengths, and watt densities, our finned cartridge heaters can be tailored to suit your specific industrial requirements. Durable Construction Built with high-quality materials, including corrosion-resistant stainless steel, these heaters are designed to withstand harsh operating conditions and ensure long-lasting performance. Versatile Applications Perfect for industrial processes such as drying, air heating, dehumidification, and sealing. The Finned Cartridge Heater is compatible with HVAC systems, packaging equipment, and various other machinery. Efficient Operation By optimizing thermal transfer and reducing energy consumption, this heater helps businesses lower operational costs while maintaining productivity. Industries We Serve Our Finned Cartridge Heater is trusted by a variety of industries, including: Manufacturing: Ideal for heat treatment, drying, and curing processes. HVAC: Used in air handling units and ventilation systems for efficient heating. Automotive: Enhances the performance of machinery requiring precise thermal management. Why Choose Our Finned Cartridge Heater? We understand the unique challenges faced by businesses in demanding industrial environments. That’s why our Finned Cartridge Heaters are designed to deliver unmatched performance and reliability. By partnering with us, you gain: Expert Support: Our team of engineers works closely with you to develop heating solutions that match your exact specifications. Fast Turnaround: We ensure quick delivery times so you can keep your operations running smoothly. Quality Assurance: Every heater undergoes rigorous testing to ensure it meets the highest standards of quality and safety. Custom Solutions for Your Business Whether you need a standard design or a custom-built Finned Cartridge Heater, we’ve got you covered. Our flexible manufacturing process allows us to adapt to your unique requirements, delivering heating solutions that align with your operational goals. Contact Us Today Ready to optimize your industrial heating systems? Contact us today to learn more about our Finned Cartridge Heaters and how they can benefit your business. Our team is here to provide personalized assistance and ensure you find the perfect solution for your needs.
What is the Principle of Immersion Tubular Heater?
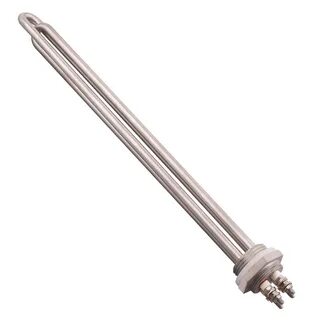
An immersion tubular heater is an efficient, compact, and widely used solution for heating liquids, gases, and other substances in various industries. Understanding its principle is crucial for selecting and maintaining heating solutions in industrial and residential settings. Unlike traditional heating methods, immersion tubular heaters provide direct and targeted heating, making them energy-efficient and reliable. Let’s break down the core principles and key applications to help you maximize their potential. The Core Principle of an Immersion Tubular Heater At its core, the immersion tubular heater operates on the principle of electrical resistance. Here’s how it works: Electrical energy is converted into heat. When electric current flows through a resistive heating element (often made of alloys like nichrome), it generates heat. Direct immersion enhances heat transfer. The tubular heater is submerged in the medium it’s designed to heat (such as water, oil, or chemicals). This eliminates heat loss commonly associated with indirect methods. Uniform heating is achieved. The tubular design ensures even distribution of heat across the medium, preventing hot spots or uneven temperatures. Key Components of an Immersion Tubular Heater Sheath Material: Protects the heating element from corrosion. Common options include stainless steel, titanium, or Incoloy, chosen based on the medium being heated. Heating Element: The core component, responsible for generating heat through resistance. Insulation: Separates the element from the sheath to ensure safety and efficiency. Mounting Options: These include flanged, threaded, or over-the-side designs, catering to diverse applications. Applications of Immersion Tubular Heater These heaters play a vital role across industries due to their versatility and efficiency. Here are some common uses: Industrial Processing: Used in chemical tanks, oil refineries, and water treatment plants for precise temperature control. HVAC Systems: Provides supplemental heat for air-handling units. Food and Beverage Industry: Ensures optimal temperatures in cooking or pasteurization processes. Renewable Energy: Supports thermal storage in solar heating systems. Why They Are Preferred: Energy Efficiency: Direct heating minimizes waste. Compact Design: Saves space without compromising performance. Customizable Options: Tailored to specific industrial or domestic needs. Advantages of Immersion Tubular Heater Over Alternatives When compared to other heating solutions, immersion tubular heaters offer distinct advantages: Faster Heating: Direct immersion ensures rapid heat transfer. Durability: High-grade materials extend lifespan, even in corrosive environments. Cost-Effectiveness: Reduced energy consumption lowers operational costs. Safety Features: Equipped with thermal cutoffs and protective coatings to prevent overheating. Maintenance Tips for Long-Term Performance To ensure the longevity and efficiency of your immersion tubular heater, follow these actionable tips: Inspect Regularly: Check for signs of corrosion, scaling, or physical damage on the sheath. Clean Periodically: Prevent scale buildup, especially in hard water applications, to maintain efficiency. Monitor Electrical Connections: Ensure tight and secure connections to avoid power issues. Replace Damaged Components Promptly: A compromised element or sheath can lead to safety hazards. Match Materials to the Medium: Use corrosion-resistant materials for chemicals or saltwater applications. Innovations in Immersion Tubular Heaters The heating industry is constantly evolving. Some recent advancements in immersion tubular heaters include: Smart Temperature Control: Integration with IoT for real-time monitoring and remote adjustments. Energy Optimization: Use of advanced insulation materials to improve energy retention. Custom Designs: Manufacturers now offer more tailored configurations for niche applications. Final Words The immersion tubular heater remains a cornerstone in efficient and reliable heating. By leveraging its principle of direct heat transfer, industries can achieve precise temperature control while saving energy. Regular maintenance and understanding its core functionality can ensure optimal performance for years. Whether you’re looking to heat water in a residential tank or manage a chemical process in an industrial setup, understanding this heater’s principles equips you to make informed decisions.
How to Pick The Best Electric Tubular Heater Supplier
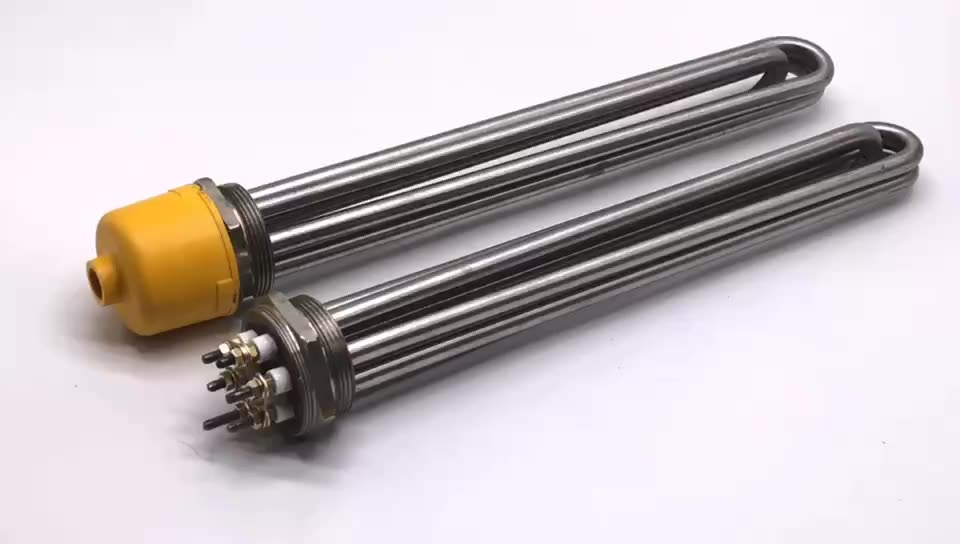
When it comes to selecting an electric tubular heater supplier, your decision can impact everything from energy efficiency to product longevity. A wrong choice might lead to costly replacements, inefficiencies, and disruptions in your operations. With so many options on the market, narrowing down your choice demands a focused and informed approach. This guide will help you pick the best supplier with actionable insights and data-driven tips. Why Your Electric Tubular Heater Supplier Choice Matters The global market for tubular heaters is projected to grow significantly, reaching $1.2 billion by 2030. Industries like manufacturing, healthcare, and food processing depend heavily on these heaters for consistent performance. Poor-quality products or unreliable suppliers can lead to: Increased operational costs. Safety hazards from subpar materials. Unplanned downtime. Partnering with a trusted supplier ensures reliability, quality, and regulatory compliance. Key Factors to Evaluate When assessing suppliers, focus on the following critical elements: 1. Product Quality and Certifications Ensure the supplier offers products that comply with international standards like ISO 9001 and CE. Look for materials like stainless steel or Incoloy, which enhance durability and thermal performance. Check customer reviews or request samples to test the heater’s performance. 2. Experience in the Industry Suppliers with 10+ years of experience typically have refined manufacturing processes and a better understanding of industry needs. Ask questions like: Have they supplied heaters to industries similar to yours? Do they offer customized solutions for specific applications? 3. Energy Efficiency of Their Products With rising energy costs, efficiency is non-negotiable. The best suppliers prioritize energy-efficient designs, reducing electricity consumption by up to 25%. Request data sheets showing energy ratings and performance metrics. How to Verify Electric Tubular Heater Supplier Reliability Relying on claims is risky. Instead, follow these steps to ensure reliability: Check References: Ask for case studies or testimonials from previous clients. Inspect Facilities: If possible, visit the supplier’s manufacturing site to observe quality control measures. Analyze Supply Chain Robustness: Delays in delivery can impact your operations. Verify their logistics capabilities and lead times. Questions to Ask Your Electric Tubular Heater Supplier Make the evaluation process seamless with these questions: Can you provide detailed product specifications and certifications? What’s your standard lead time for bulk orders? How do you ensure consistent product quality across batches? Do you offer after-sales support or warranties? What’s your minimum order quantity, and are discounts available for bulk purchases? Red Flags to Avoid Be cautious of these warning signs: Lack of Transparency: If the supplier hesitates to share certifications or references, it’s a red flag. Unrealistic Pricing: Prices significantly lower than competitors might indicate inferior quality. Inconsistent Communication: Poor customer service early on may signal bigger issues down the line. Final Thoughts Choosing the right electric tubular heater supplier is a decision that extends beyond price. Focus on quality, experience, and reliability. Conduct due diligence, ask the right questions, and prioritize suppliers with a proven track record in your industry. Investing time in this process ensures long-term operational efficiency and cost savings. With the right supplier, your business will have a reliable heating solution tailored to its needs.
Top 3 Industries That Use Cartridge Heater With Thermocouple
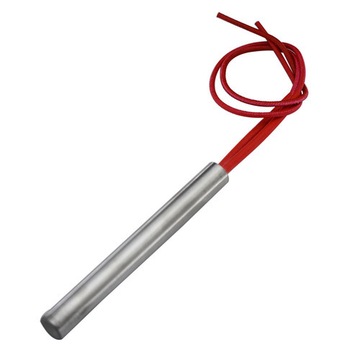
A cartridge heater with thermocouple is a critical tool for industries requiring precise temperature control. By integrating a thermocouple, this heater not only generates heat but also provides real-time temperature feedback. This ensures enhanced accuracy, energy efficiency, and improved process reliability. Below, we’ll examine the top industries benefiting from this advanced technology and how it supports their operations. 1. Plastic Manufacturing Plastic manufacturing heavily relies on cartridge heaters with thermocouples for precision heating. From injection molding to extrusion, these heaters are vital for producing high-quality plastic components. Injection Molding: Maintaining accurate temperature profiles in the mold is essential. Any deviation can result in defective products. A cartridge heater with thermocouple ensures the mold temperature remains consistent, leading to fewer errors. Plastic Extrusion: During the extrusion process, plastic materials must reach precise melting points. A built-in thermocouple monitors the temperature in real-time, avoiding overheating or under-heating that could compromise the product’s integrity. Key Benefits for Plastic Manufacturing: Minimized material wastage. Faster production cycles due to consistent heating. Improved product quality with fewer defects. 2. Pharmaceutical and Medical Device Industry Accuracy and cleanliness are paramount in the pharmaceutical and medical device sectors. A cartridge heater with thermocouple helps maintain sterile conditions while ensuring the precision required for sensitive applications. Sterilization Equipment: Cartridge heaters are used in autoclaves and sterilization chambers, ensuring even heating throughout. The thermocouple continuously monitors the temperature, ensuring compliance with strict regulatory standards. Medical Device Manufacturing: Processes like sealing and welding of medical-grade plastics depend on precise temperatures. Thermocouple feedback ensures these processes meet exact specifications, eliminating risks of contamination or faulty seals. Why It’s Essential in This Industry: Supports strict compliance with FDA and ISO standards. Prevents overheating that could damage sensitive materials. Ensures uniform heating critical for sterile environments. 3. Food and Beverage Processing The food and beverage industry also benefits from cartridge heaters with thermocouples, especially for tasks requiring precision and safety. Packaging Machinery: Sealing food packages requires consistent temperatures to avoid weak or over-sealed packaging. Thermocouple-equipped cartridge heaters provide exact temperature feedback, ensuring every seal is reliable. Liquid Heating: Processes like pasteurization or maintaining the warmth of liquid foods depend on temperature stability. With a cartridge heater and thermocouple, the risk of overheating or uneven heat distribution is eliminated. Key Advantages in Food Processing: Maintains consistent quality across batches. Enhances food safety by preventing under-processing. Reduces energy consumption with real-time temperature adjustments. Why Cartridge Heater With Thermocouple Stands Out The integration of a thermocouple into cartridge heaters provides numerous advantages across industries: Real-Time Monitoring: The thermocouple gives immediate feedback, enabling precise adjustments. Energy Efficiency: By avoiding temperature overshoots, these heaters reduce unnecessary energy use. Reliability: They enhance process consistency, leading to higher output quality. Final Thoughts From plastic manufacturing to pharmaceuticals and food processing, the cartridge heater with thermocouple proves invaluable in applications demanding precision and efficiency. Its ability to provide accurate temperature control, coupled with durability, makes it a staple in modern industrial operations. If you’re searching for a heating solution that delivers consistent results, consider this innovative technology.
5 Common Applications of a Band Heater

Band heaters are an essential component in industries where consistent heat is crucial for processes and production. Their precision, efficiency, and durability make them indispensable. Used in machinery, manufacturing, and various industrial applications, a band heater plays a critical role in optimizing production. In this article, we’ll see five common applications where band heaters are most effective and beneficial. 1. Plastic Injection Molding Plastic injection molding is a complex process requiring exact temperature control. In this application, band heaters are essential for heating the nozzles and barrels that melt plastic pellets before they’re injected into molds. Here’s why band heaters are ideal for this application: Precision Control: Band heaters allow for precise heat application, keeping the plastic at the right temperature for optimal flow. Energy Efficiency: With their direct contact heating, band heaters reduce energy wastage, cutting down on operational costs. Durability: Many band heaters are built to withstand long operational hours, reducing downtime and boosting productivity. 2. Food Processing Equipment Band heaters play a significant role in food processing, particularly in machines that rely on heated cylinders or pipes. From pasteurization to canning and drying processes, band heaters provide consistent heat, ensuring that food products are safe and of high quality. Even Heating: Band heaters apply uniform heat to prevent hotspots, which is critical for food quality and safety. Safety Compliance: Many band heaters are designed with materials and coatings that comply with food-grade safety standards, maintaining cleanliness and preventing contamination. Customizable Temperature: Adjustable temperature controls allow for flexibility across various stages of food processing, from heating to maintaining temperatures. 3. Pharmaceutical Manufacturing In pharmaceutical production, accuracy and consistency are paramount. Band heaters are commonly used in reactors, dryers, and other equipment that require constant heat to process active ingredients, ensuring product stability and quality. Stable Heating for Sensitive Ingredients: Band heaters maintain a stable environment, crucial for sensitive chemical reactions. Enhanced Safety: Pharmaceutical applications demand heaters that minimize the risk of overheating. Band heaters with protective controls help meet this need. Compatibility with Stainless Steel: Many band heaters are compatible with stainless steel reactors, which are standard in pharmaceutical production for their resistance to corrosion. 4. Packaging Machinery Band heaters are also frequently found in packaging machinery, where they heat and seal materials such as plastic, foil, and laminates. Reliable and consistent heating is essential to produce secure seals that protect product quality during transit and storage. High-Quality Seals: Band heaters enable precise temperature control to produce tight, durable seals. Reduced Downtime: Packaging operations run continuously, and band heaters with high thermal efficiency minimize energy consumption and maintenance requirements. Adjustable Heating for Different Materials: Band heaters allow easy adjustments to accommodate various packaging materials, making them versatile for packaging multiple types of goods. 5. Diesel Engine Preheating A band heater is often used in the automotive industry, especially in preheating diesel engines in colder climates. Preheating diesel engines ensures a smoother start, prevents engine damage, and reduces emissions from incomplete combustion. Quick Start in Cold Weather: Band heaters make diesel engines easier to start, even in freezing conditions. Reduced Wear on Engine Components: Preheating reduces stress on engine components, extending engine life. Improved Fuel Efficiency: By optimizing combustion, band heaters help improve fuel efficiency and reduce harmful emissions. Final Thoughts The band heater remains a fundamental solution in industries demanding consistent and efficient heating. Whether it’s for plastic injection molding or ensuring safe food processing, the flexibility, reliability, and efficiency of band heaters make them an excellent choice across various applications.
3 Reasons Why Cartridge Heater is a Must in Industrial Applications
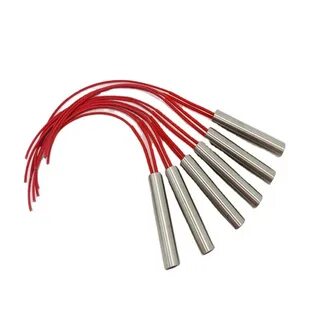
A cartridge heater is indispensable in the industrial sector, widely relied upon to deliver efficient, high-temperature heating for various processes. Known for their compact yet powerful build, these heaters fit into tight spaces, delivering precise heat where it’s needed most. From manufacturing to automotive and beyond, cartridge heaters enhance operational efficiency, help maintain quality, and lower costs. Let’s delve into the top reasons why a cartridge heater is essential in industrial applications, backed by research and real-world insights. 1. High-Temperature Efficiency and Precision Control One of the main advantages of using a cartridge heater in industrial applications is its high-temperature capability and precision. Many industries rely on heating elements that can reach temperatures above 1,200°F (649°C) to ensure effective processing. Here’s how cartridge heaters excel in these demanding environments: Efficient Heat Distribution: Cartridge heaters feature a unique design that allows them to heat up quickly and distribute heat evenly. This is essential in industries like plastic molding and packaging where consistent heat levels directly impact product quality. Precision Control: Advanced cartridge heaters often include control mechanisms that allow for precise temperature adjustments, ensuring no energy is wasted and that materials aren’t damaged by overheating. With these features, cartridge heaters help maintain the thermal stability needed for industries such as automotive manufacturing and 3D printing, where even minor temperature variations can impact the outcome. 2. Durability and Reliability in Harsh Environments Industrial environments are often harsh, with exposure to chemicals, high-pressure settings, and rough handling. Cartridge heaters are designed to withstand these challenges, making them a durable and long-lasting heating solution: Stainless Steel Sheathing: Many cartridge heaters are built with stainless steel or other corrosion-resistant materials, which protect against environmental wear and tear. This is vital in industries like pharmaceutical and chemical processing. High Watt Density: Cartridge heaters can operate at high watt densities, meaning they can produce a lot of heat in a small space without degrading. This allows them to maintain consistent performance over time. In high-demand applications, these heaters often last thousands of hours without requiring replacement, significantly reducing maintenance costs and downtime. 3. Versatility Across Multiple Industrial Uses The versatility of cartridge heaters makes them suitable for a wide array of industrial applications, including food production, metalworking, and automotive manufacturing. They can be customized in terms of size, wattage, and voltage, making them adaptable to specific needs: Plastic Injection Molding: Cartridge heaters provide the precise and rapid heating required for molding materials into specific shapes. Consistent heat application ensures high-quality, defect-free products. Packaging Machinery: Packaging industries rely on cartridge heaters to seal products effectively. The consistent and controlled heat ensures seals are strong and leak-proof, which is especially crucial in food and medical packaging. Hot Runner Systems: These systems use cartridge heaters to keep the plastic material molten, allowing for efficient flow into molds and reducing material waste. Final Words For industrial operations that demand efficient, durable, and precise heating solutions, cartridge heater stands out as a top choice. With their wide adaptability and ability to operate in high-stress environments, cartridge heaters prove essential for optimizing production quality and efficiency.
What Are the Types of Heating Cable
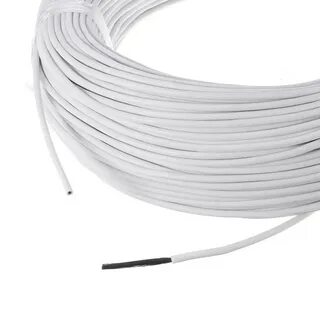
Heating cable technology is a game-changer for maintaining warmth in various environments and is essential in areas where temperature regulation is critical. Heating cable is designed to combat frost, prevent pipes from freezing, and maintain consistent warmth for specific equipment or structures. They are used in industrial settings, homes, and even in agriculture. With advancements in technology, different types of heating cables are now available, each suited to specific needs and applications. In this post, we’ll break down the main types of a heating cable and the benefits of each. 1. Self-Regulating Heating Cables Self-regulating heating cables automatically adjust their output based on the ambient temperature, making them one of the most energy-efficient options. Key Features: Adjusts heating output according to environmental temperature. Offers high safety by reducing the risk of overheating. Suitable for protecting pipes, roofs, and gutters. Application: Commonly used for freeze protection of pipes and maintaining optimal temperatures in process pipes in industrial settings. These cables are also popular for roof and gutter de-icing systems. Benefits: Energy Efficient: Reduces power consumption when the temperature is mild. Long-Lasting: Designed to last years with minimal maintenance. Safe: Automatically adjusts power levels, minimizing overheating risks. 2. Constant Wattage Heating Cables Constant wattage heating cables provide a consistent level of heat regardless of the surrounding temperature. Unlike self-regulating cables, they do not adjust based on external temperatures, making them ideal for situations where steady, continuous heating is required. Key Features: Provides a stable wattage output. Suitable for environments where temperature control is critical. Available in various wattage capacities to meet specific heating demands. Application: These cables are widely used in temperature-sensitive areas like laboratories or environments where the temperature must remain stable. Benefits: Precision Heating: Delivers stable heat output for consistent performance. Wide Application: Useful in both commercial and industrial settings. Effective: Maintains temperature in harsh environments where fluctuations can be problematic. 3. Mineral Insulated (MI) Heating Cables Mineral Insulated heating cables are durable and ideal for high-temperature applications. These cables consist of a metal conductor insulated with magnesium oxide, which can withstand extreme conditions without degrading. Key Features: Withstands temperatures up to 1000°C. Highly resistant to chemical exposure and mechanical stress. Provides reliable heat in high-temperature processes. Application: Used in heavy industries such as oil and gas, power generation, and chemical processing plants. Benefits: High Durability: Ideal for environments with corrosive chemicals and extreme temperatures. High-Performance Output: Delivers steady heat even under demanding conditions. Safety: Highly resistant to fire and can function in explosive environments. 4. Series Resistance Heating Cables Series resistance cables work by maintaining consistent resistance along the cable, delivering heat over its entire length. These cables are used in applications where precise lengths and specific wattages are needed. Key Features: Customizable to specific lengths and wattage requirements. Ensures uniform heating along the cable. Can be tailored for complex installations. Application: Ideal for specialized industrial applications, such as long pipelines or equipment that requires uniform heating over extensive areas. Benefits: Flexible Design: Easily customized to match various industrial setups. Uniform Heating: Delivers consistent warmth across the cable’s length. Customizable: Manufactured to meet precise requirements, making them perfect for unique applications. Final Thoughts Heating cables are a critical component in temperature-sensitive applications across industries, homes, and commercial spaces. Selecting the right type depends on specific requirements, environmental conditions, and budget. Whether you’re looking to keep pipes from freezing, control heat in process applications, or manage de-icing systems, choosing the right heating cable can help ensure reliable performance and energy efficiency.
5 Benefits of a High Temperature Cable
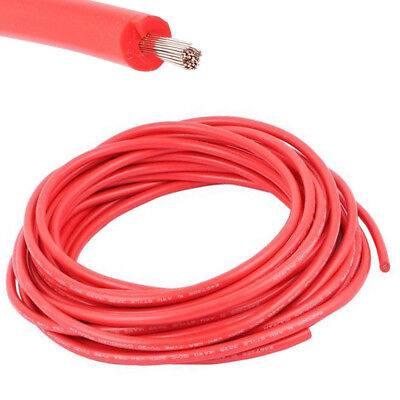
A high temperature cable is essential for industries where heat resistance and performance reliability are critical. These cables are engineered to handle extreme temperatures, ensuring safety and functionality in demanding applications. From industrial machinery to aerospace systems, their role in maintaining seamless operations cannot be overstated. Here are five key benefits of using high-temperature cables, with actionable insights. 1. Enhanced Heat Resistance High-temperature cables are designed to withstand extreme heat without degradation. Temperature Tolerance: These cables can endure temperatures as high as 1,000°F (538°C) or more, depending on the material. Safety Assurance: They minimize the risk of insulation melting, which is critical in aerospace, automotive, and manufacturing industries. This capability ensures longevity and reduces the risk of system failures under heat stress. 2. Durability in Harsh Environments High-temperature cables are built to last, even in environments with harsh conditions like abrasion, chemicals, or moisture. Chemical Resistance: Materials like PTFE and silicone provide resistance to chemicals and oils. Abrasion Protection: Reinforced coatings protect cables from physical wear, ideal for heavy-duty equipment. These features reduce replacement costs and enhance reliability. 3. Electrical Stability Even under high temperatures, these cables maintain consistent electrical properties. Reduced Signal Loss: High-temperature cables minimize signal interference, ensuring precise operations in machinery. Stable Conductivity: They handle voltage fluctuations effectively, safeguarding sensitive systems. This makes them a go-to choice for medical devices and robotics. 4. Versatility Across Industries High temperature cable is adaptable to numerous applications. Industrial Heating: Used in ovens, furnaces, and kilns, they can handle constant exposure to heat. Automotive Systems: Essential for engines and exhaust systems where extreme heat is prevalent. Aerospace Applications: Withstand the high temperatures of aircraft engines and space systems. This versatility ensures their applicability across a wide range of sectors. 5. Compliance with Safety Standards Manufacturers of high-temperature cables adhere to stringent industry standards. ISO and UL Certifications: These certifications ensure that cables meet high-performance criteria. Fire Safety: Many cables are flame-resistant, reducing risks in sensitive environments like data centers and laboratories. This compliance ensures peace of mind for industries requiring robust safety measures. Final Words A high temperature cable is more than just a heat-resistant solution. It is a reliable, durable, and versatile component for various industries. Its ability to perform under extreme conditions ensures efficiency, safety, and cost-effectiveness in critical applications.
How to Select a Hot Runner Heater Supplier
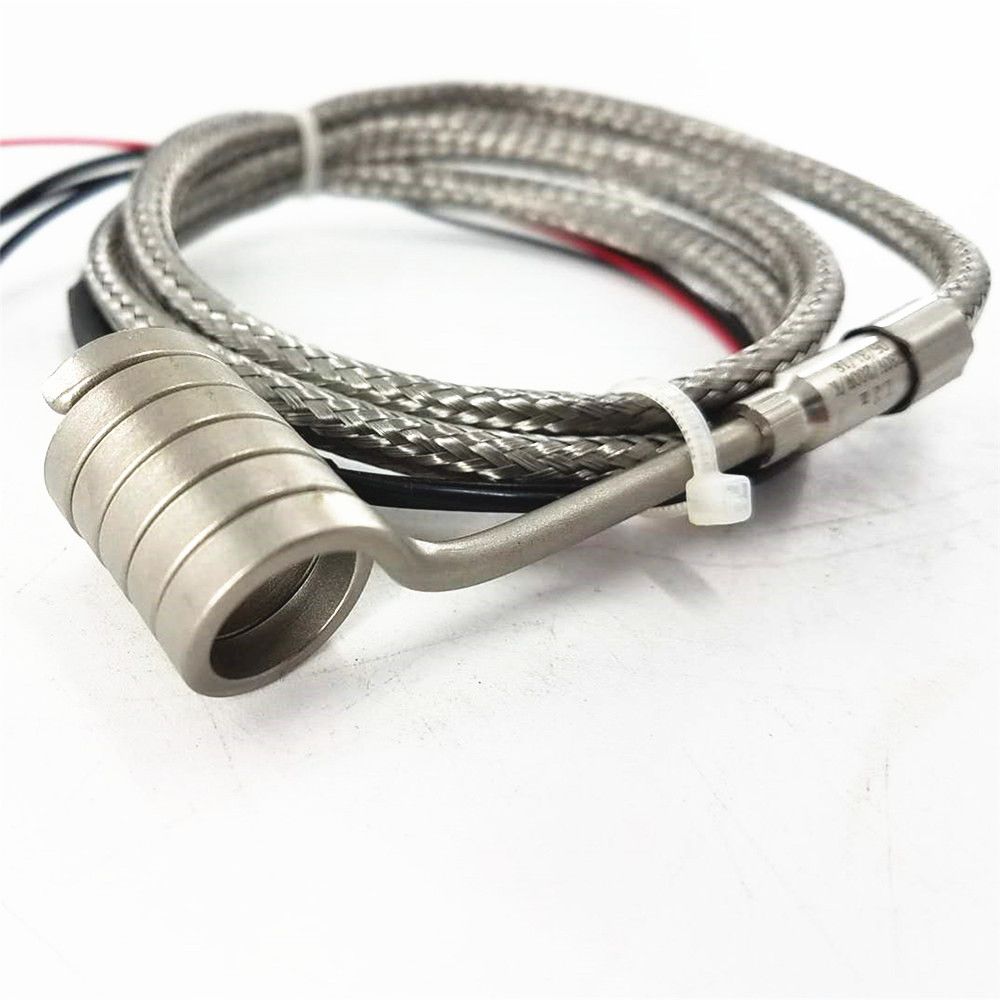
Choosing the right hot runner heater supplier can significantly impact the efficiency and output of your plastic molding processes. A reliable supplier ensures consistent heat delivery, reduced downtime, and superior product quality. However, not all suppliers offer the same level of service and product excellence. Here’s a research-driven guide to selecting the right hot runner heater partner for your industrial heating needs. 1. Evaluate the Supplier’s Product Quality The quality of a hot runner heater directly affects the performance of your system. Before committing to a supplier, verify the durability, efficiency, and reliability of their products. Materials Used: Look for heaters built with high-quality alloys, such as stainless steel or nickel, which resist corrosion and withstand high temperatures. Precision Heating: Check whether the heaters deliver uniform heat distribution. Consistency is essential in plastic molding to avoid product defects. Longevity: A high-quality hot runner heater should last thousands of cycles without degradation. Suppliers should provide data on their products’ lifespan under different operating conditions. 2. Assess Industry Experience and Reputation A supplier with extensive experience in the plastic molding industry is more likely to understand your specific requirements. Proven Track Record: Research the supplier’s history of delivering heaters for industries like automotive, medical, and consumer goods manufacturing. A supplier with expertise in these sectors is familiar with complex heating demands. Client Testimonials and Reviews: Read reviews from existing clients to gauge satisfaction with the supplier’s products and services. Certifications and Standards: Ensure the supplier complies with industry standards such as ISO 9001 or CE certifications. These indicate a commitment to quality and safety. 3. Customization Options for Specific Needs Every molding application has unique requirements. A competent supplier should offer customized hot runner heater solutions tailored to your system. Custom Sizes and Shapes: Suppliers should provide heaters in various diameters and lengths to match the design of your hot runner system. Voltage and Wattage Customization: The ability to fine-tune watt density and power requirements ensures optimal performance. Temperature Sensors: Some suppliers integrate advanced temperature control features, enabling precise adjustments to avoid overheating. 4. Technical Support and After-Sales Services Strong technical support is essential for seamless operations, especially in industries where downtime can be costly. Installation Assistance: Suppliers should provide detailed manuals, videos, or even on-site support for heater installation. Troubleshooting Help: Ensure the supplier offers responsive customer service for resolving issues quickly. Spare Parts Availability: A reliable supplier keeps essential components in stock to minimize delays in case of repairs. 5. Competitive Pricing Without Compromising Quality While pricing is an important factor, it should not come at the expense of quality or reliability. Transparent Quotes: Request detailed quotes that include product specifications, warranties, and delivery timelines. Hidden charges can inflate costs over time. Bulk Discounts: If your operations require large quantities of heaters, explore whether the supplier offers volume-based discounts. Red Flags to Avoid While selecting a supplier, be cautious of: Inconsistent Product Quality: Suppliers with frequent negative reviews about durability or performance. Limited Warranty Periods: Short warranties may indicate a lack of confidence in their products. Poor Communication: Delayed responses and unclear terms can cause operational challenges. Final Words Partnering with the right hot runner heater supplier is crucial for maintaining efficient plastic molding processes. From quality products to robust after-sales support, a supplier’s capabilities should align with your operational needs. For reliable solutions, consider trusted names like Jabeens, who offer expertise and high-performance heaters tailored to modern industry demands.
5 Reasons Why a Pipeline Heater is a Must in Industrial Manufacturing
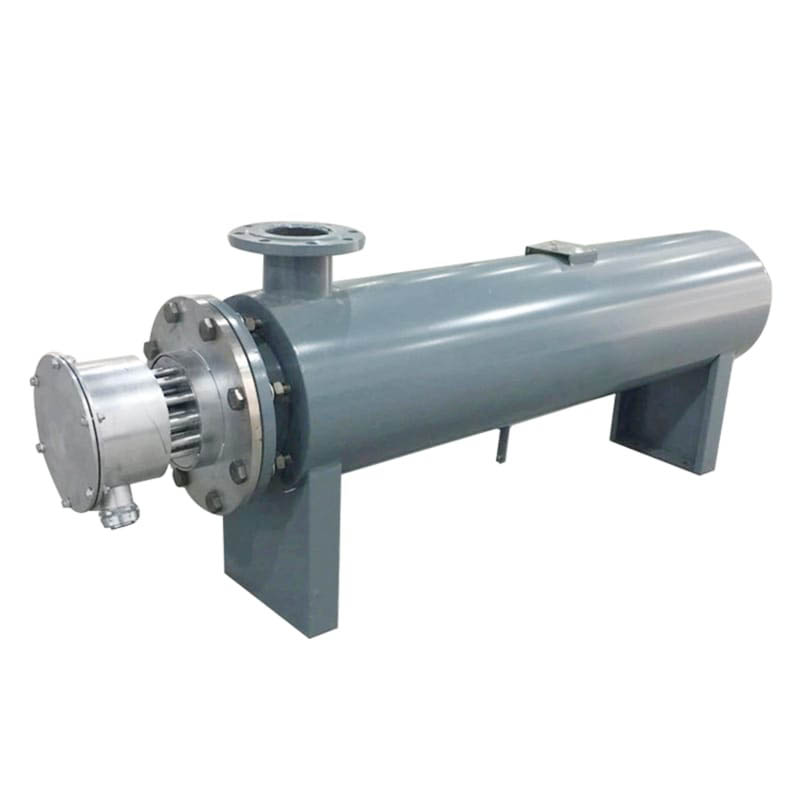
In industries like oil and gas, petrochemical, and food production, maintaining precise temperatures within pipelines is critical. A pipeline heater is a specialized tool designed to regulate the temperature of liquids and gases flowing through pipelines. Without it, efficiency, safety, and product quality can be compromised. This blog explains why a pipeline heater is indispensable in industrial manufacturing and highlights the unique benefits it offers. 1. Enhances Process Efficiency Pipeline heaters are crucial for maintaining consistent temperatures, which directly improves process efficiency. In industries like oil and gas, where substances such as crude oil and natural gas flow through pipelines, maintaining optimal viscosity is vital. Reduces Energy Loss: By keeping materials at the desired temperature, pipeline heaters minimize the energy required to reheat substances later in the process. Prevents Clogging: Materials like crude oil can solidify or thicken at low temperatures. Pipeline heaters ensure a smooth flow, preventing costly clogs. Supports Continuous Operations: With reduced interruptions due to temperature issues, industries can maintain round-the-clock operations efficiently. This efficiency translates to increased output and lower operational costs. 2. Protects Equipment from Wear and Tear Industrial pipelines face significant stress when temperature fluctuations occur. These fluctuations can cause materials to expand and contract, leading to wear and tear. Prevents Corrosion: A consistent temperature prevents condensation, which could lead to corrosion inside the pipeline. Reduces Mechanical Stress: Temperature control mitigates the strain on valves and joints, extending the life of the pipeline infrastructure. By minimizing equipment damage, pipeline heaters save industries significant maintenance costs over time. 3. Ensures Safety and Compliance Temperature mismanagement in pipelines can lead to hazardous situations, especially in industries handling flammable or volatile substances. Pipeline heaters play a vital role in ensuring safety. Prevents Freezing: In cold climates, fluids in pipelines can freeze, causing blockages and potential ruptures. Pipeline heaters eliminate this risk. Reduces Pressure Build-Up: Proper heating ensures that gases expand predictably, avoiding dangerous pressure spikes. Meets Regulatory Standards: Many industries are required to comply with strict temperature and safety regulations. Pipeline heaters help meet these standards reliably. Safety is not just a priority but a necessity in industrial manufacturing. 4. Supports Product Quality In manufacturing, the quality of the final product often depends on maintaining precise conditions during production. Pipeline heaters play a key role in ensuring this consistency. Prevents Contamination: Materials flowing through pipelines are less likely to degrade or mix with impurities when maintained at the correct temperature. Improves End-Product Uniformity: In food manufacturing, for instance, maintaining even heating can prevent texture and taste inconsistencies. By supporting quality assurance, pipeline heaters help industries deliver reliable products. 5. Adapts to Diverse Applications Pipeline heaters are versatile, making them suitable for a wide range of industrial processes. Oil and Gas: Used to heat crude oil, natural gas, and other hydrocarbons, ensuring efficient transport and processing. Chemical Processing: Maintain specific temperatures for reactions and material flows. Food and Beverage: Essential for transporting liquids like syrup or chocolate, which need to stay at precise temperatures. This adaptability ensures that pipeline heaters remain an essential component across diverse industries.