5 Benefits of a Tubular Heating Element
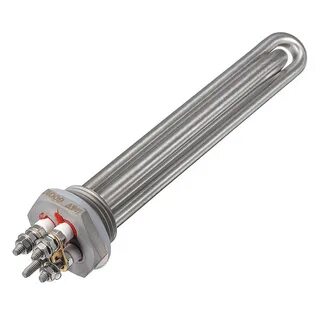
When it comes to heating solutions, tubular heater technology stands out due to its versatility and efficiency. These heating elements are used in countless applications, from industrial machinery to domestic appliances. But why are they so widely chosen? Below are five key benefits of a tubular heater that make it a top choice for heating systems. 1. Efficient Heat Distribution A tubular heater provides uniform heating over a wide surface area. Its design ensures that heat is evenly distributed, which is essential for many applications like: Home appliances: Like ovens or water heaters, where consistent heating is needed. Industrial uses: In manufacturing processes that require uniform temperature control. By ensuring a consistent temperature, tubular heaters can improve performance, reduce energy waste, and prevent hotspots that could damage sensitive equipment. 2. Versatility Across Industries One of the main reasons tubular heaters are so widely used is their flexibility in design. They can be customized to meet the specific needs of different environments. Some key areas where tubular heaters excel include: Residential: Water heaters, underfloor heating, and air conditioning systems. Commercial: Food warmers, beverage dispensers, and vending machines. Industrial: Tanks, pipes, and machinery that require precise temperature control. The ability to adapt the heater’s shape and size to different applications is a major advantage. 3. Long Lifespan and Durability Durability is another standout feature of a tubular heater. When properly maintained, these heaters have a long lifespan, even in harsh environments. Factors contributing to their durability include: Corrosion resistance: Many tubular heaters are designed with materials like stainless steel, which can withstand exposure to moisture and corrosive substances. Heat resistance: They perform well in high-temperature conditions without degradation. As a result, these heaters often require less frequent replacement, offering significant cost savings over time. 4. Energy Efficiency and Cost Savings Energy consumption is always a key consideration in heating systems. Tubular heaters are designed to operate efficiently, converting most of the electrical energy into heat. This leads to: Lower operating costs: Because more energy is converted into heat, the system doesn’t need to work as hard, reducing energy bills. Reduced maintenance costs: Their longevity and durability mean fewer repairs and replacements are required. This efficiency is especially critical for businesses that rely on large-scale heating systems, where reducing energy waste can translate into substantial savings. 5. Easy Installation and Maintenance Unlike some other types of heating elements, tubular heaters are straightforward to install and maintain. Their design makes them easy to integrate into existing systems, and maintenance is relatively simple: Quick installation: Due to their modular design, they can be easily added to a system without significant changes. Low-maintenance: With proper care, they require minimal upkeep, lowering operational downtime. The simplicity of both installation and maintenance makes them a practical choice for both residential and industrial applications. Final Words From consistent heat distribution to ease of installation, tubular heaters provide a range of benefits that make them indispensable in various applications. Whether you’re looking for an energy-efficient heating solution or need a durable, long-lasting heating element, a tubular heater is a wise investment. Their versatility across industries, combined with low maintenance and cost-effectiveness, ensures that they remain one of the best choices for heating needs.
5 Top Benefits of a Silicone Rubber Heater
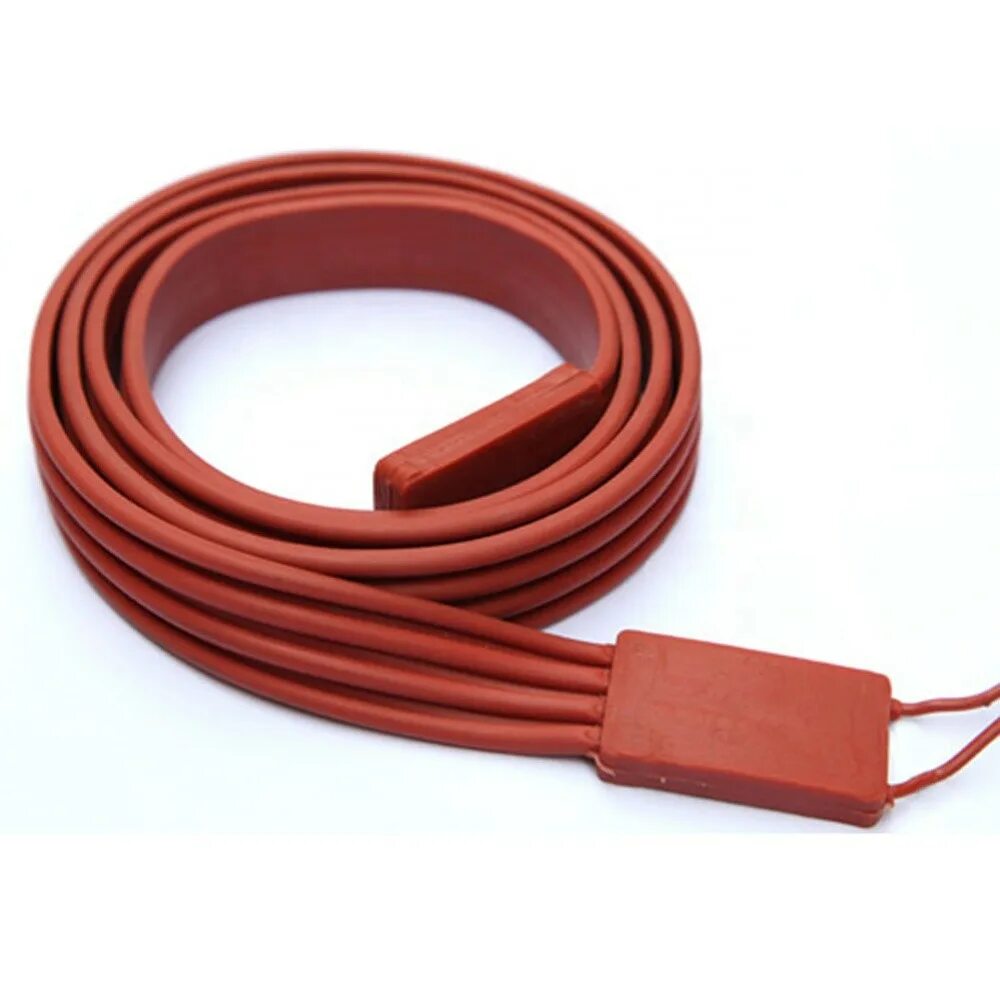
A silicone rubber heater stands out as a versatile and efficient heating solution across industries. Known for its flexibility and durability, it delivers reliable performance in diverse applications, from medical devices to aerospace. This heater type combines innovative materials and technology to provide precise temperature control, essential for critical processes. Here are the top benefits that make a silicone rubber heater an indispensable tool for industries. 1. Flexibility in Design and Application Silicone rubber heaters offer unmatched design flexibility. Their lightweight and thin construction allow them to be custom-made to fit complex surfaces, enabling precise heating in applications that require intricate shapes. Custom Shapes and Sizes: These heaters can be tailored to match unique contours, such as irregular or cylindrical surfaces. Ease of Installation: Adhesive backing or vulcanized attachments make them easy to integrate into equipment. This flexibility is especially beneficial in industries like medical diagnostics, where equipment demands heating precision without adding bulk. 2. Superior Temperature Control and Uniform Heat Distribution Consistency is critical when it comes to industrial heating. A silicone rubber heater ensures uniform heat distribution, eliminating cold spots that could disrupt operations. Temperature Range: These heaters operate efficiently between -60°C to 230°C, accommodating a variety of industrial needs. Integrated Sensors: Many silicone rubber heaters come with built-in thermocouples or RTDs for accurate temperature monitoring. Such precise control is invaluable in processes like 3D printing, where consistent heat directly impacts product quality. 3. Exceptional Durability in Challenging Environments Harsh environments demand robust heating solutions. Silicone rubber heaters excel in such conditions due to their resilient materials. Moisture and Chemical Resistance: The silicone outer layer protects the heater from water, oil, and chemical damage, making it ideal for food processing and pharmaceutical applications. Mechanical Toughness: Their durability ensures they can withstand repeated flexing and mechanical stress without compromising functionality. This resilience contributes to longer service life, reducing downtime and replacement costs. 4. Energy Efficiency and Cost-Effectiveness Silicone rubber heaters are designed for energy efficiency. They generate heat precisely where needed, reducing energy wastage. Low Thermal Mass: Their thin construction enables rapid heating and cooling, which lowers energy consumption. Localized Heating: They eliminate the need for heating entire systems, focusing on specific areas to improve efficiency. This efficiency not only reduces operational costs but also minimizes the carbon footprint, aligning with modern sustainability goals. 5. Wide Range of Industrial Applications The adaptability of silicone rubber heaters extends their use across numerous industries, such as: Medical: Pre-heating diagnostic devices and ensuring consistent performance in imaging equipment. Aerospace: De-icing components and maintaining optimal temperatures in sensitive avionics. Automotive: Warming batteries in electric vehicles for enhanced performance during colder climates. Electronics: Protecting sensitive components from temperature fluctuations. Their versatility makes them a go-to solution for industries that demand precision and reliability. Final Words A silicone rubber heater is not just a heating element; it’s a strategic asset for industries requiring precision, durability, and efficiency. From customized designs to consistent performance in harsh environments, these heaters cater to the most demanding applications. Their role in improving operational efficiency and reducing costs makes them indispensable for modern industrial processes.
5 Best Uses of a Thermocouple
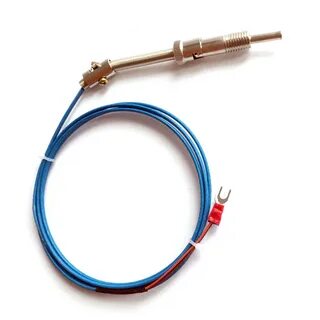
A thermocouple is one of the most reliable and widely used temperature measurement tools in industrial and scientific applications. Its ability to measure extreme temperatures with accuracy makes it indispensable. From manufacturing to energy management, thermocouples serve as critical components in systems where temperature control is vital. This article will uncover unique and specific ways a thermocouple is transforming operations across industries. 1. Industrial Temperature Monitoring In manufacturing and heavy industries, thermocouples are essential for accurate temperature control: Steel and Metal Processing: Thermocouples are used to monitor high-temperature furnaces, ensuring metals like steel and aluminum achieve their desired properties during processing. Chemical Manufacturing: Precise temperature readings are critical during chemical reactions to avoid process failures or unsafe outcomes. Industries requiring temperatures above 1,800°F rely heavily on thermocouples because of their durability and capability to handle extreme conditions. 2. Power Generation Systems Thermocouples play a critical role in energy management and power generation: Gas Turbines: In power plants, thermocouples measure turbine temperatures to optimize performance and prevent overheating. Boiler Systems: Temperature feedback ensures that boilers maintain the required steam pressure for efficient power generation. By providing real-time data, thermocouples contribute to the efficiency and safety of energy systems, minimizing downtime and potential hazards. 3. Food Processing and Safety The food industry depends on thermocouples for maintaining the safety and quality of products: Cooking and Pasteurization: Thermocouples are used to verify that food reaches the right internal temperatures to eliminate harmful bacteria. Cold Storage Monitoring: Low-temperature thermocouples ensure food stays within the safe range during storage and transport. With foodborne illnesses a major concern globally, thermocouples ensure compliance with safety standards and help prevent contamination. 4. Medical and Laboratory Applications Thermocouples are integral in the healthcare and scientific research sectors: Sterilization Equipment: Autoclaves use thermocouples to monitor high-temperature steam sterilization processes. Cryogenics: Thermocouples measure ultra-low temperatures in applications like organ preservation and vaccine storage. In laboratories, thermocouples support experiments requiring exact temperature settings, ensuring consistent and repeatable results. 5. Automotive and Aerospace Industries Modern vehicles and aerospace systems depend on thermocouples for efficiency and safety: Engine Testing: Thermocouples monitor internal engine temperatures to enhance performance and reduce emissions. Aircraft Safety: In aviation, thermocouples measure temperatures in jet engines and exhaust systems to ensure optimal operation under extreme conditions. With the growing focus on sustainability, thermocouples are helping manufacturers meet stringent efficiency standards. Why Thermocouples Are Essential Thermocouples are valued for their: Wide Temperature Range: Capable of measuring from -200°C to over 2,000°C, they are versatile across applications. Durability: They function reliably in extreme environments, from industrial furnaces to cryogenic systems. Cost-Effectiveness: With simple construction and high reliability, thermocouples are economical for long-term use. Final Words Thermocouples are much more than temperature sensors; they are enablers of efficiency, safety, and quality across industries. Their ability to withstand extreme conditions while providing accurate data makes them indispensable. Whether in manufacturing, food safety, or aerospace, thermocouples ensure processes run smoothly and products meet the highest standards.
How to Clean a Ceramic Radiant Tube Heater?
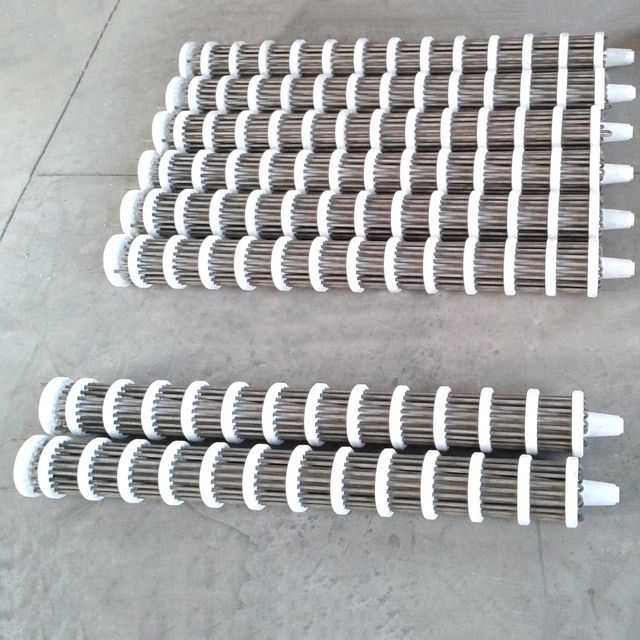
A ceramic radiant tube heater is a reliable choice for efficient heating in various industrial and residential settings. However, neglecting regular maintenance can reduce its efficiency and lifespan. Proper cleaning not only ensures optimal performance but also minimizes energy consumption and potential safety hazards. This step-by-step guide will help you clean your radiant tube heater effectively while protecting its delicate components. Why Cleaning a Ceramic Radiant Tube Heater Is Crucial Dust, dirt, and carbon build-up can accumulate on the surface of your ceramic radiant tube heater over time. These deposits obstruct heat transfer, leading to: Reduced heating efficiency Higher energy bills Increased wear and tear on the heating element Potential fire hazards due to overheating A regular cleaning schedule ensures the heater operates at peak performance and lasts longer. Tools and Materials You’ll Need Before starting, gather the following essentials: Soft-bristle brush (non-abrasive to avoid damaging the ceramic surface) Microfiber cloth (to prevent scratches) Vacuum cleaner with a hose attachment Isopropyl alcohol (for stubborn stains or grease) Compressed air canister (optional, for hard-to-reach areas) Protective gloves (to avoid direct contact with debris or cleaning agents) Safety Precautions Before Cleaning Safety should always come first. Follow these steps before cleaning your ceramic radiant tube heater: Turn off the heater and unplug it from the power source. Allow the heater to cool completely to avoid burns. Wear protective gloves to handle components safely. Read the user manual for any specific cleaning instructions or warnings. Step-by-Step Cleaning Guide 1. Remove Surface Dust and Debris Start by cleaning visible dirt: Use a soft-bristle brush to gently loosen dust on the ceramic elements and surrounding areas. Employ a vacuum cleaner with a hose attachment to remove loosened debris. If the heater has a grille or vent, clean it thoroughly with the brush. 2. Clean the Ceramic Surface The ceramic surface is delicate and requires careful handling: Dampen a microfiber cloth with isopropyl alcohol. Wipe the surface gently to remove stains or grease. Avoid soaking the cloth to prevent moisture from seeping into electrical components. 3. Inspect and Clean the Heating Element Examine the heating element for dirt or residue: Use a compressed air canister to blow away any debris from tight spaces. If accessible, lightly brush the element with a soft-bristle brush. 4. Check Ventilation Areas Clogged ventilation can impact the heater’s efficiency: Vacuum or wipe down vents and air intake areas. Ensure no obstructions remain that could block airflow. Maintenance Tips to Extend the Life of Your Heater Clean every three months if the heater operates in dusty or greasy environments. Inspect the heater for wear or damage during each cleaning session. Store the heater in a dry, dust-free environment when not in use. Replace worn-out parts, such as grilles or filters, to maintain performance. FAQs About Ceramic Radiant Tube Heater Cleaning How often should I clean my ceramic radiant tube heater? Clean it every 3–6 months, depending on usage and environmental conditions. Can I use water to clean the heater? Avoid using water directly. Instead, use a damp microfiber cloth to clean surfaces safely. What if my heater still smells after cleaning? A lingering smell may indicate deeper issues. Contact a professional for inspection. Final Thoughts Regular cleaning of your ceramic radiant tube heater is a simple yet essential task. It ensures efficiency, enhances safety, and prolongs the device’s lifespan. By following these detailed steps and maintenance tips, your heater will deliver consistent performance for years to come. Keep your heating system in top condition, and enjoy its benefits without unnecessary downtime or costs.
What are the Types of Cartridge Heater With Thermocouple
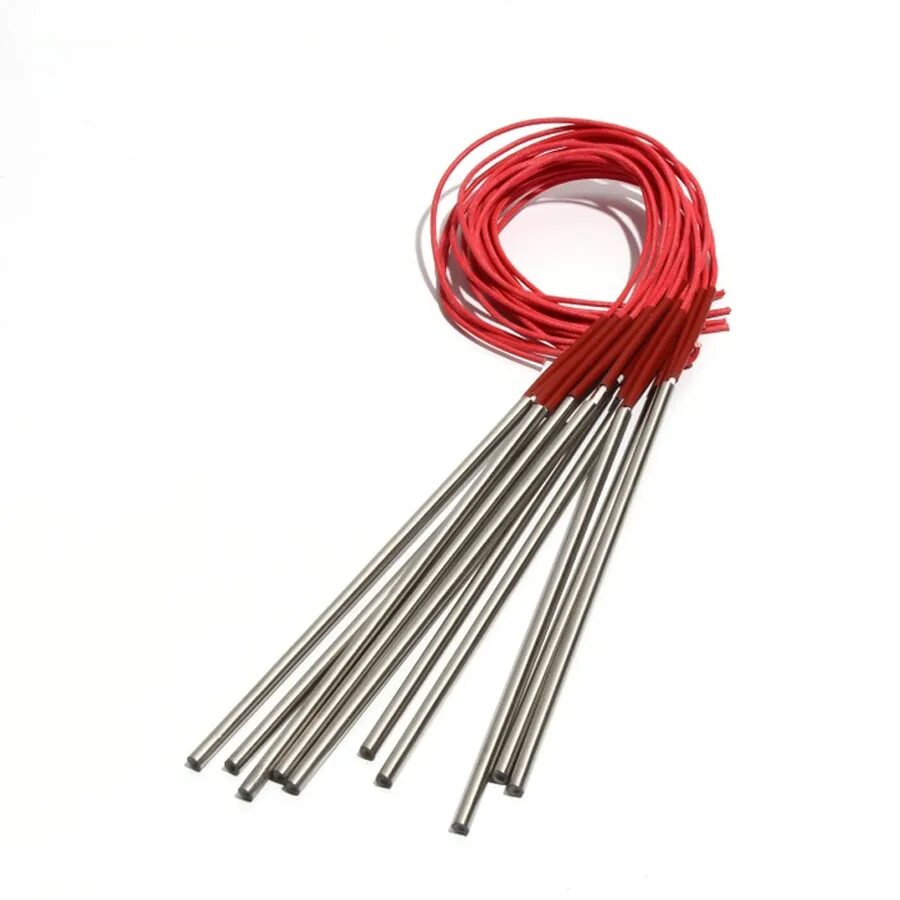
Industrial heating systems demand precision, and a cartridge heater with thermocouple is one of the most reliable tools for the job. This combination provides consistent heat delivery and accurate temperature monitoring, essential for various industrial applications. From manufacturing to food processing, understanding the types of a cartridge heater with thermocouple can help you choose the right solution for your operations. Why Combine a Cartridge Heater with a Thermocouple? The integration of a thermocouple in a cartridge heater enhances temperature regulation. This feature is critical in applications requiring precise heat control. It ensures that materials are neither overheated nor under-processed, protecting equipment and ensuring consistent production outcomes. Key benefits include: Real-Time Temperature Monitoring: Thermocouples provide instant feedback on temperature fluctuations. Energy Efficiency: By preventing overheating, this system reduces energy waste. Process Optimization: Industries like plastic molding and pharmaceutical manufacturing benefit from controlled heating environments. Let’s examine the different types of cartridge heaters with thermocouples and their applications. 1. Standard Cartridge Heater With Thermocouple This is the most common type used across industries. It features an integrated thermocouple, often placed internally or externally, depending on the application. Internal Thermocouple: Placed inside the heater for direct measurement of core temperature. This is ideal for high-precision tasks like scientific instrument heating. External Thermocouple: Positioned outside the heater for surface temperature monitoring. Commonly used in metalworking and packaging machinery. The versatility of these heaters makes them suitable for both low-watt density and high-watt density applications. 2. Swaged Cartridge Heater With Thermocouple Swaged heaters are designed for high-performance applications. These heaters are built with compacted insulation, which enhances heat transfer and durability. Advantages: High Watt Density: Can deliver significant heat within small spaces. Durability: Resistant to vibration and thermal cycling, making it perfect for automotive manufacturing. The thermocouple in these heaters ensures tight temperature control, critical for minimizing material waste. 3. Split Cartridge Heater With Thermocouple Split cartridge heaters offer flexibility and easy installation. Their design allows them to expand or contract, ensuring a secure fit in varying diameters. Key Applications: Injection Molding: Perfect for maintaining consistent temperatures in molds. Food Processing: Ensures uniform heat for tasks like sealing and cooking. The embedded thermocouple provides accurate temperature readings, helping maintain product quality. 4. Miniature Cartridge Heater With Thermocouple Compact but powerful, miniature cartridge heaters are ideal for applications with limited space. Despite their small size, they deliver precise heating and temperature control. Best For: Medical Equipment: Used in devices requiring delicate heat control. 3D Printing: Ensures stable heating in intricate printing components. Thermocouples integrated into these heaters ensure the accuracy needed for sensitive tasks. Choosing the Right Cartridge Heater With Thermocouple When selecting a heater, consider the following: Application Requirements: High-precision industries like aerospace demand swaged heaters, while food processing may need split designs. Temperature Range: Evaluate the maximum and minimum temperatures needed for your processes. Installation Space: Miniature heaters are ideal for tight spaces, while standard options fit broader applications. Final Words A cartridge heater with thermocouple offers unmatched precision, durability, and versatility. Whether it’s for manufacturing, medical, or food processing, understanding the various types can optimize your processes and improve operational efficiency.
5 Best Applications of a Warm Floor Cable
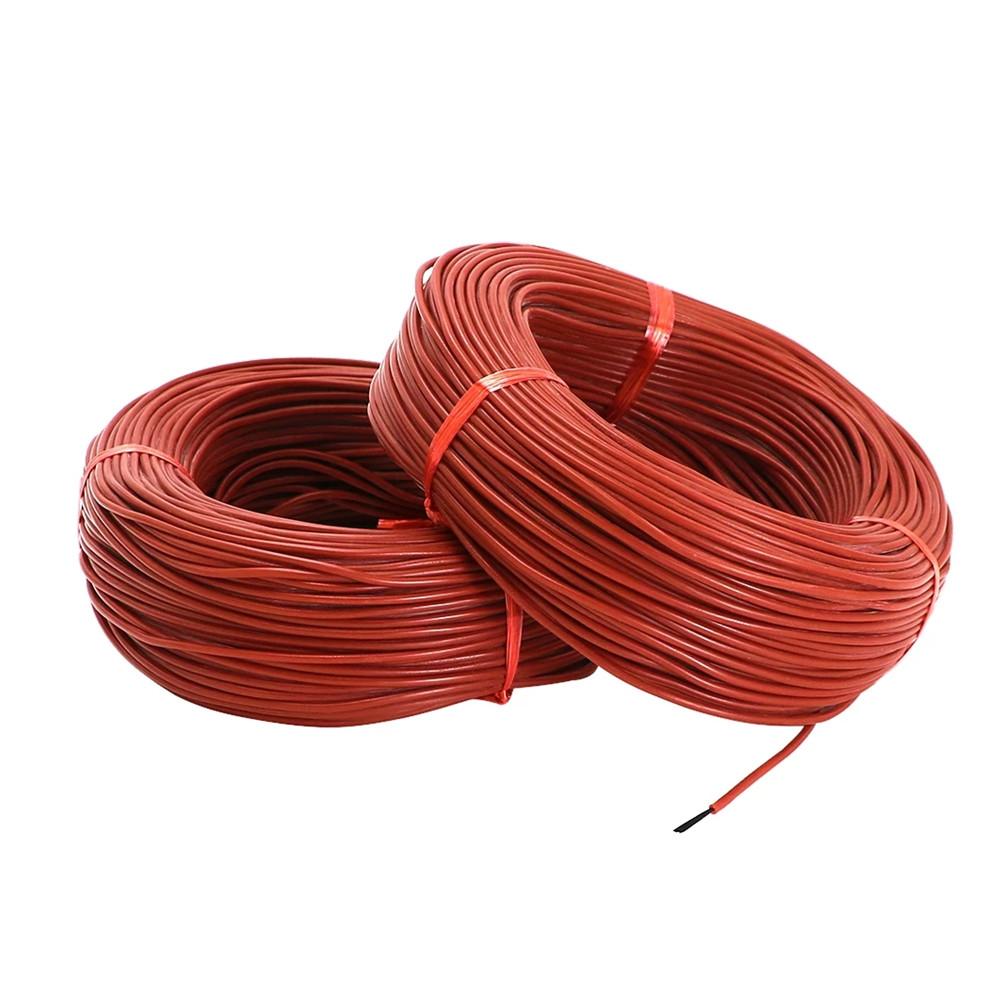
A warm floor cable is an essential component for efficient underfloor heating systems. It provides consistent and cost-effective heating, ensuring comfort in residential, commercial, and industrial spaces. Unlike traditional heating systems, these cables work seamlessly beneath the flooring, offering even heat distribution. With the rising demand for energy-efficient solutions, let’s uncover the top applications of a warm floor cable and their advantages across different scenarios. 1. Residential Floor Heating Systems Warm floor cables are widely used in homes to create comfortable and cozy living spaces. Their ability to provide consistent warmth makes them ideal for cold climates or areas with harsh winters. Key uses include: Bathroom Heating: These cables are perfect for ensuring warm floors in bathrooms, eliminating the discomfort of stepping onto cold tiles during winter mornings. Living Room Comfort: They help create evenly heated living spaces without the need for bulky radiators or forced air systems. Energy Efficiency: Homes with warm floor cables can reduce heating costs by up to 30% compared to conventional systems. Warm floor cable also enhances property value by offering an energy-efficient, modern heating solution. 2. Commercial Applications In commercial buildings, warm floor cables provide heating solutions that are both efficient and discreet. They work well in areas where large heating systems may be impractical: Retail Spaces: Warm floor cables keep customer areas comfortable, especially in high-traffic locations. Hotels: They improve guest experiences by offering heated floors in lobbies, bathrooms, and spa areas. Offices: In workspaces, these cables maintain a consistent temperature, increasing productivity and reducing energy costs. 3. Industrial Use Cases Warm floor cables are not just for comfort—they’re also functional in industrial settings. They offer solutions for challenges such as frost protection and maintaining specific floor temperatures. Common industrial uses include: Warehouses: These cables prevent freezing on warehouse floors, ensuring safe working conditions. Factories: In manufacturing, warm floor cables help maintain optimal temperatures for certain processes or materials. Cold Storage Facilities: They prevent frost damage and ensure temperature-sensitive items are stored safely. Industrial applications benefit significantly from the durability and efficiency of warm floor cables, which reduce maintenance and downtime. 4. Frost Protection for Outdoor Spaces Warm floor cables can also be installed outdoors to prevent frost and ice buildup. This application is especially important for ensuring safety and convenience in winter months. Typical uses include: Driveways: Keep driveways ice-free to prevent accidents and improve vehicle traction. Walkways and Stairs: Ensure safe pedestrian access by melting snow and ice on outdoor pathways. Loading Docks: In commercial areas, warm floor cables ensure smooth operations during freezing conditions. This type of installation is both practical and cost-efficient, minimizing risks and the need for constant manual de-icing. 5. Underfloor Heating in Renovation Projects For renovations, warm floor cables are an excellent way to upgrade old heating systems. They integrate easily into modern flooring designs and improve the overall energy efficiency of older buildings. Benefits for renovation projects include: Retrofitting in Existing Homes: Warm floor cables can be installed beneath various flooring types, including tiles, laminate, and hardwood. Space Optimization: They eliminate the need for visible heaters, freeing up space for aesthetic and functional purposes. Improved Energy Ratings: Homes and commercial properties with underfloor heating often achieve higher energy performance ratings. Final Words Warm floor cables are a versatile and energy-efficient solution for modern heating needs. Whether you’re upgrading your home, enhancing safety in outdoor spaces, or improving commercial heating systems, these cables provide unmatched performance.
What is a MI Heat Trace Cable?
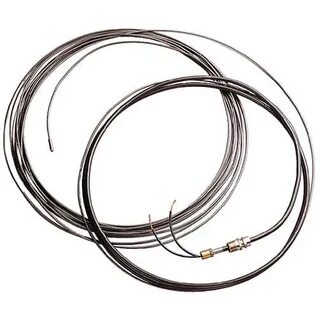
Industrial heating systems rely heavily on advanced solutions like the MI heating cable to ensure efficiency, safety, and precision. Known for their robust construction and ability to deliver consistent heat in challenging environments, MI heating cables are a critical component in applications ranging from petrochemical plants to food processing facilities. Let’s take an in-depth look at what makes MI heating cables indispensable, their functionality, and their unique benefits. What is an MI Heating Cable? A Mineral Insulated (MI) heating cable is a highly durable electric heating cable used for maintaining or raising temperatures in pipes, tanks, and industrial equipment. Unlike conventional heating cables, MI heating cables consist of a metallic sheath and mineral insulation (typically magnesium oxide), which protect the heating elements from moisture, corrosion, and mechanical damage. This robust design ensures unmatched performance in extreme conditions, such as high temperatures, high-pressure environments, and exposure to chemicals. These features make MI heating cables a preferred choice for critical industries like oil and gas, pharmaceuticals, and chemical processing. How Does an MI Heating Cable Work? The working principle of an MI heating cable is simple yet efficient. It uses resistance heating to generate heat: Electrical current flows through the heating element within the cable. Heat is generated by resistance, which is then evenly distributed across the surface. The mineral insulation ensures maximum thermal conductivity while protecting the heating core. This construction allows MI heating cables to operate reliably at temperatures exceeding 1,000°C (1,832°F), far surpassing the capabilities of polymer-based heating cables. Key Features of MI Heating Cables MI heating cables stand out due to their unique design and capabilities. Here’s what sets them apart: High Temperature Tolerance: With the ability to operate at extreme temperatures, these cables ensure stable performance in demanding environments. Corrosion Resistance: The metallic sheath and mineral insulation provide excellent resistance to moisture, chemicals, and other corrosive elements. Durability: The rugged design prevents damage from mechanical stress, ensuring a long operational life. Precision Heating: These cables deliver uniform heat, making them ideal for applications requiring consistent thermal control. Common Applications of MI Heating Cables MI heating cables are versatile and serve a wide range of industrial and commercial applications, including: Freeze Protection: Preventing pipework and tanks from freezing in cold climates. Process Temperature Maintenance: Ensuring stable temperatures for chemical reactions and fluid transfer in industrial systems. Tank Heating: Maintaining product temperatures in storage tanks, especially in oil and gas facilities. Floor Heating: Providing underfloor heating in high-end architectural projects. Why MI Heating Cables Are Critical for Modern Industries MI heating cables offer several advantages that make them irreplaceable in many sectors: Energy Efficiency: Reduced energy loss due to excellent thermal conductivity. Safety Compliance: Meets stringent safety standards for hazardous and non-hazardous environments. Customizability: Tailored solutions for specific lengths, wattages, and voltage ratings. Longevity: With minimal maintenance, they outperform traditional cables in terms of lifespan. Final Thoughts The MI heating cable is a technological marvel designed to meet the most demanding industrial heating needs. Its durability, high-temperature tolerance, and versatility make it an essential solution for industries requiring reliable heat management systems. For businesses looking to optimize performance and safety, MI heating cables provide unmatched efficiency and peace of mind.
3 Top Benefits of Mica Heat Proof Cable Box
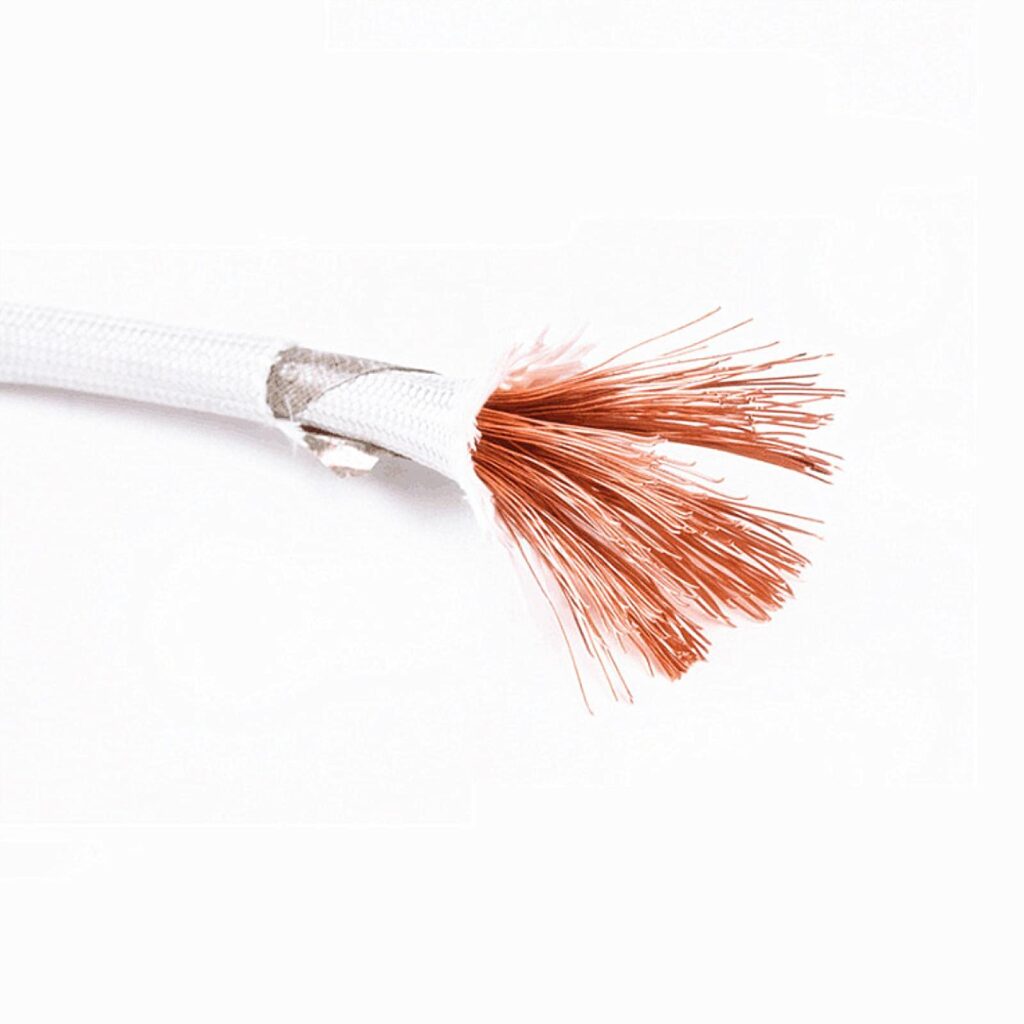
Choosing the right materials for electrical insulation is critical in high-temperature environments. One solution stands out for its durability and safety—the mica heat proof cable box. This essential component is transforming industrial and residential wiring by providing unmatched resistance to heat and electrical hazards. Below, we break down the top benefits of this innovative technology. 1. Unmatched Heat Resistance The primary advantage of a mica heat proof cable box lies in its ability to withstand extreme temperatures. Here’s why this matters: Thermal Stability: Mica can endure temperatures up to 1000°C without compromising performance. This makes it ideal for industrial settings with high heat exposure. Safety Enhancement: The box prevents heat transfer to surrounding components, reducing the risk of fire and system failures. Prolonged Lifespan: Unlike traditional materials, mica doesn’t degrade when exposed to heat over long periods, ensuring consistent functionality. Industries such as power generation, steel manufacturing, and aerospace rely heavily on these boxes to maintain operational safety. Even in residential applications, they provide an added layer of protection against overheating and electrical faults. 2. Exceptional Electrical Insulation Another game-changing benefit is its superior electrical insulation. Mica is a naturally dielectric material, making it an ideal choice for safe electrical installations. Minimal Current Leakage: It offers high dielectric strength, minimizing power loss and preventing hazardous current leaks. Resistance to Arc Faults: Mica remains stable under electrical arcing conditions, a common hazard in high-voltage systems. High Voltage Handling: It supports voltage levels of up to 1500V, ensuring reliability even in heavy-duty environments. This ensures that sensitive equipment and wiring remain unaffected, promoting operational efficiency and reducing maintenance costs. 3. Environmental and Cost Efficiency In addition to safety, mica heat proof cable boxes contribute to environmental and financial sustainability. Here’s how: Eco-Friendly: Mica is a naturally occurring mineral, free from harmful chemicals, and easily recyclable. This minimizes its environmental footprint. Reduced Energy Consumption: Its insulating properties prevent energy loss, lowering electricity usage in both industrial and residential systems. Low Maintenance Costs: With its resistance to wear and tear, mica boxes require fewer repairs and replacements, reducing long-term expenses. Moreover, its durability ensures that infrastructure upgrades are needed less frequently, making it a cost-effective solution for businesses aiming to optimize their operations. Key Applications of Mica Heat Proof Cable Box This versatile product is used across multiple industries due to its unique properties: Industrial Furnaces: Ensures safe wiring in high-temperature zones. Electric Vehicles (EVs): Protects against heat and electrical overload in advanced battery systems. Construction: Enhances fire safety in modern building wiring systems. Final Thoughts The mica heat proof cable box is more than just a component—it’s a necessity in environments where safety and durability are non-negotiable. Its heat resistance, insulation capabilities, and cost efficiency make it a smart choice for both industrial and residential applications. By investing in this technology, businesses and homeowners can ensure long-term safety, reliability, and sustainability. When choosing materials for your electrical systems, prioritize solutions that deliver proven performance. The mica heat proof cable box is a benchmark in innovation and reliability.
How to Use Immersion Tubular Heater
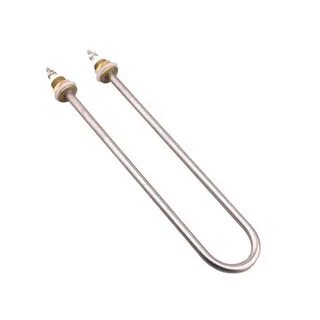
Immersion tubular heaters are indispensable in industries and households for their efficiency and reliability. Whether you’re looking to heat liquids, oils, or even gases, these heaters offer a cost-effective solution. However, understanding the right way to use an immersion tubular heater is essential to maximize performance and extend the equipment’s lifespan. This guide provides actionable steps and facts to help you make the most of your heater. What Is an Immersion Tubular Heater? An immersion tubular heater is a versatile heating element designed to be directly immersed in a medium—usually liquid or gas. The heat generated by the element is efficiently transferred, making it ideal for applications requiring rapid and consistent heating. Common industries that rely on these heaters include: Chemical processing: For heating chemicals and solutions. Food and beverage: To maintain safe processing temperatures. Water treatment: For sterilizing and heating water. Manufacturing: For heating oils, fuels, and other materials. Step-by-Step Guide: How to Use an Immersion Tubular Heater 1. Understand the Specifications Before using an immersion tubular heater, check its specifications: Voltage and wattage ratings. Material compatibility (stainless steel, Incoloy, or titanium for corrosive environments). Maximum operating temperature and pressure. 2. Prepare the Medium Ensure the liquid or gas being heated is free from debris. Particles can adhere to the heater, causing inefficient heating or damage over time. For water heating: Use filtered or soft water to minimize scaling. For chemicals: Verify the heater’s material compatibility to avoid corrosion. For oils: Ensure the oil’s viscosity is suitable for the heater’s power output. 3. Correct Placement Submerge the heater entirely in the medium to avoid dry firing. Maintain the recommended clearance around the element for even heat distribution. Use mounting brackets if required to secure the heater. Warning: Operating an immersion tubular heater outside the medium can cause overheating and failure. 4. Monitor Temperature Always use a thermostat or temperature controller to regulate the heating process. Overheating can damage both the heater and the medium. Set the thermostat to a safe operating range. Monitor temperature changes to prevent overheating accidents. 5. Perform Regular Maintenance Routine maintenance ensures your heater remains efficient and safe. Inspect for scaling or residue buildup regularly. Clean the heater with non-corrosive solutions. Replace worn-out components like gaskets or seals. Key Benefits of Proper Use Using an immersion tubular heater correctly delivers: Reduced energy costs due to efficient heat transfer. Increased lifespan of the heater through proper maintenance. Improved safety by minimizing risks of overheating or damage. Latest Trends in Immersion Tubular Heaters Smart controllers: Integration with IoT devices for remote monitoring and control. Eco-friendly materials: Manufacturers are focusing on recyclable and sustainable components. Enhanced corrosion resistance: New alloys like Inconel 825 improve longevity in harsh environments. Last Word An immersion tubular heater is a versatile and efficient tool when used correctly. By following the steps outlined—preparation, placement, temperature monitoring, and maintenance—you can ensure safe and effective operation. Invest time in understanding the specifications and stay updated with the latest trends to get the best out of your heater. With proper care, this equipment can provide years of reliable service. Ready to heat smarter and safer? Start applying these tips today!
What Is Finned Tubular Heater Used For?
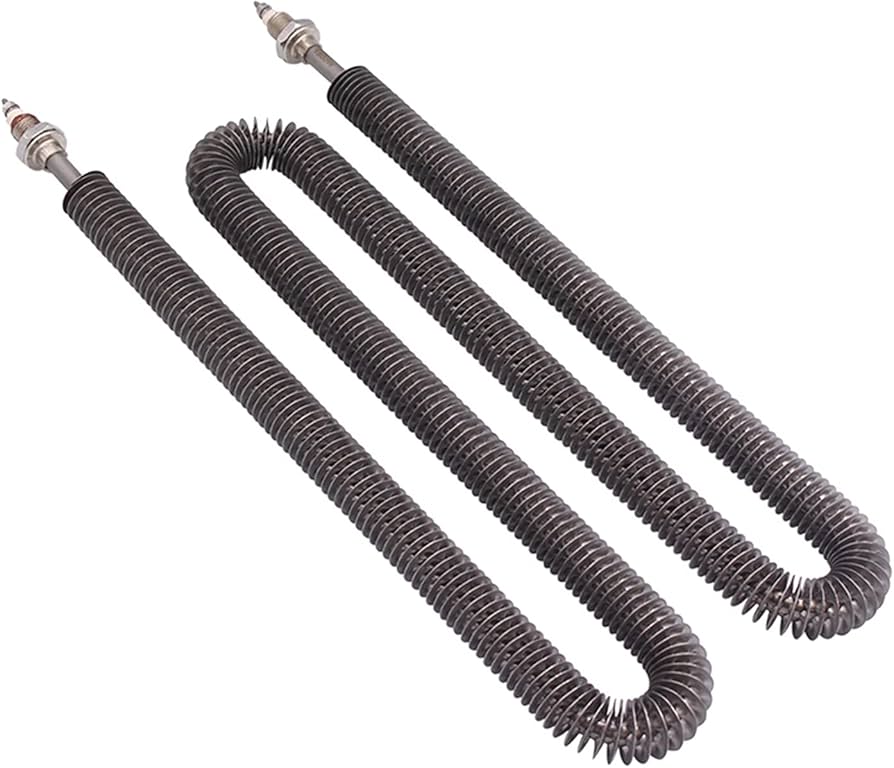
A finned tubular heater is a highly efficient heating solution widely used across industries due to its enhanced heat transfer capabilities. These heaters combine a tubular element with metal fins to increase surface area, enabling faster heat dissipation. But what exactly are they used for? Let’s break it down with actionable insights and practical applications. How Does a Finned Tubular Heater Works? Before understanding its uses, let’s clarify how it operates. A finned tubular heater works by converting electrical energy into heat. The fins attached to the heating element improve thermal conductivity and airflow, making the heater ideal for high-demand environments. Key benefits of its design include: Improved heat transfer through the fins. Durable materials like stainless steel or Incoloy for harsh conditions. Customizable configurations to suit diverse applications. This unique functionality makes the finned tubular heater indispensable in various settings. Common Uses of Finned Tubular Heater 1. Industrial Drying Applications Industries requiring controlled drying processes rely heavily on these heaters. Their precise temperature control ensures consistent results, making them ideal for: Drying textiles, paper, and wood. Baking coatings and adhesives. Removing moisture in packaging processes. Why it works: The extended surface area increases airflow efficiency, reducing drying times. 2. HVAC Systems Heating, Ventilation, and Air Conditioning (HVAC) systems benefit from the finned tubular heater’s ability to quickly heat large air volumes. These heaters are commonly found in: Duct heating systems. Air handlers for commercial spaces. Residential heating units. Pro Tip: They reduce energy consumption compared to traditional heaters, cutting operational costs. 3. Food and Beverage Industry Food safety regulations demand precise temperature control, and finned tubular heaters deliver just that. They are used for: Cooking and baking equipment. Sterilization of utensils and machinery. Keeping food warm in buffet setups. Their durability ensures consistent performance, even under continuous operation. 4. Chemical and Pharmaceutical Processing In sensitive environments like chemical plants and labs, heating needs to be efficient and reliable. Finned tubular heaters excel in: Heating tanks and vats. Maintaining the right temperatures for chemical reactions. Providing uniform heat for lab equipment. Their corrosion-resistant materials handle aggressive chemicals effortlessly. 5. Freezing Prevention in Cold Climates Preventing freezing in pipes and equipment is crucial for industries operating in extreme weather. Finned tubular heaters are used for: Heating pipelines and valves. Defrosting refrigeration units. Protecting critical systems in oil rigs and outdoor machinery. Their rugged construction withstands low temperatures while ensuring uninterrupted operations. Factors to Consider When Choosing a Finned Tubular Heater Selecting the right heater requires evaluating your specific needs. Here’s what to keep in mind: Watt density: Higher watt density is better for industrial tasks, while lower is ideal for gentle heating. Material compatibility: Choose materials like stainless steel for moisture-prone environments. Size and configuration: Match the heater size to the available space for optimal performance. Voltage requirements: Ensure compatibility with your power supply. Final Words A finned tubular heater is a versatile heating solution trusted across industries for its efficiency, reliability, and adaptability. Whether drying, heating air, or safeguarding equipment, these heaters prove invaluable in diverse applications. Understanding their features and benefits ensures you make the right choice for your specific needs.