What is Electric Tubular Heater for Greenhouse?
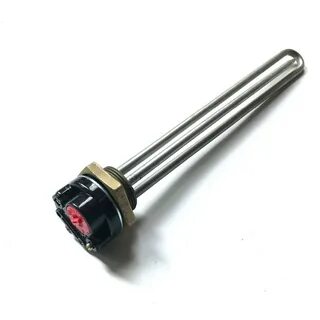
Heating a greenhouse efficiently is crucial for plant growth, especially during colder months. An electric tubular heater offers a reliable and cost-effective solution. These heaters are specifically designed to maintain consistent temperatures, ensuring plants thrive regardless of external weather conditions. This article explains what an electric tubular heater is, how it works, and why it’s an excellent choice for greenhouse heating. We’ll also highlight the latest features and provide actionable tips for greenhouse owners. What is an Electric Tubular Heater? An electric tubular heater is a slim, energy-efficient device designed to produce uniform heat. It consists of a tubular heating element, often made from stainless steel or other durable materials. Key Features: Consistent Heating: Provides even heat distribution, preventing cold spots. Energy Efficiency: Consumes less energy compared to traditional heaters. Compact Design: Fits easily in smaller greenhouses or under benches. Customizable Options: Available in different lengths and power ratings to suit varying greenhouse sizes. Why Are Electric Tubular Heaters Ideal for Greenhouses? Greenhouses require a steady temperature to support plant growth. Drastic temperature drops can stress plants, stunt growth, or even lead to crop loss. Electric tubular heaters address these challenges effectively. Advantages for Greenhouses: Uniform Temperature Control: Prevents frost damage. Ensures optimal conditions for seed germination and plant growth. Cost-Effectiveness: Lower running costs compared to propane or kerosene heaters. Ideal for long-term use due to energy efficiency. Safety Features: Overheat protection to avoid accidental damage. Waterproof and corrosion-resistant designs for humid environments. Low Maintenance: Requires minimal upkeep, saving time and resources. How Does an Electric Tubular Heater Work? An electric tubular heater converts electrical energy into heat using a resistance wire embedded in a metallic tube. This tube is insulated and sealed, making it safe for greenhouse use. Operational Details: Heat Transfer: The heater emits radiant heat, warming the surrounding air evenly. Thermostat Integration: Most models include thermostats for precise temperature control. Mounting Options: Can be mounted on walls, floors, or benches for flexible installation. Latest Innovations in Electric Tubular Heaters Manufacturers have introduced advanced features to enhance the performance of electric tubular heaters for greenhouses: Smart Temperature Control: Wi-Fi-enabled thermostats for remote adjustments. Eco-Friendly Options: Models designed to reduce carbon footprints with improved efficiency. Adjustable Power Settings: Allows users to switch between energy modes for different seasons. Durable Construction: Enhanced materials for longer life in humid greenhouse environments. Tips for Using an Electric Tubular Heater in a Greenhouse Maximizing the efficiency of your heater ensures better results and lower energy bills. Here are actionable tips: Calculate the Right Heater Size: Use a heating calculator to determine the required wattage for your greenhouse size. Position Strategically: Place the heater near vulnerable areas like doors or windows where heat loss occurs. Pair with Insulation: Use bubble wrap or thermal screens to retain heat inside the greenhouse. Monitor Regularly: Check the thermostat settings and clean the heater periodically to maintain efficiency. Final Thoughts An electric tubular heater for greenhouse is more than just a heating device; it’s a reliable partner in ensuring your greenhouse thrives. With the latest advancements and practical usage tips, you can achieve optimal plant growth while reducing energy consumption. Take the step toward better greenhouse management today with this innovative heating solution!
How Do a Ceramic Radiant Tube Heater Work?
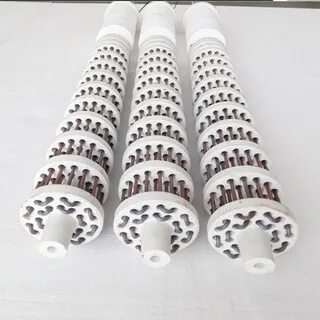
A ceramic radiant tube heater is an efficient and advanced heating solution often found in industrial and commercial settings. Its design leverages radiant heat transfer to deliver warmth effectively, making it a popular choice for high-performance applications. But how does it function, and what sets it apart from other heating systems? Let’s break down the science, components, and real-world advantages of these heaters. The Science Behind Radiant Heating At its core, a ceramic radiant tube heater operates on the principle of radiant heat transfer. Unlike convection heaters that warm the air, radiant heaters emit infrared energy, directly heating objects and surfaces within their range. This ensures targeted and efficient heating, reducing energy waste. Infrared Radiation: These heaters produce infrared waves, which travel through the air without heating it. Direct Heating: The energy is absorbed by objects and people, making it ideal for localized heating needs. Efficiency: Radiant heat reduces energy loss in large, open spaces, a key reason for its widespread use. Key Components of a Ceramic Radiant Tube Heater Understanding how these heaters work requires a look at their essential components: Ceramic Emitter Made from high-grade ceramic, the emitter is the core heating element. It can withstand extreme temperatures, ensuring durability and efficiency. Radiant Tube Usually made from heat-resistant metal alloys, the tube channels the infrared energy. Its reflective properties enhance heat distribution. Gas or Electric Power Source The heater may use natural gas, propane, or electricity. Gas-fired systems burn fuel to heat the ceramic emitter, while electric models use resistive heating. Reflectors Positioned behind the radiant tube, reflectors focus and direct the heat. This design minimizes energy loss and maximizes heat delivery. Control Systems Advanced models feature digital thermostats and smart controls. These allow precise temperature adjustments, reducing operational costs. Benefits of a Ceramic Radiant Tube Heater 1. Energy Efficiency Ceramic radiant tube heaters excel in reducing energy consumption. By directly heating objects instead of air, they eliminate unnecessary heat loss, especially in large, poorly insulated areas. Up to 30% lower energy costs compared to conventional systems. Ideal for warehouses, factories, and outdoor areas. 2. Enhanced Durability The ceramic materials used in these heaters are highly resistant to wear and thermal stress, making them suitable for demanding environments. Long service life with minimal maintenance. Consistent performance even in extreme temperatures. 3. Comfortable and Uniform Heating Radiant heat provides even warmth without creating air currents. This ensures a more comfortable environment for occupants and machinery alike. No dust or allergens stirred up, promoting better air quality. Perfect for precision industries requiring stable temperatures. Practical Applications of Ceramic Radiant Tube Heaters These heaters are used in a variety of settings: Industrial Spaces: Factories and workshops benefit from efficient heating of specific zones. Commercial Buildings: Showrooms, restaurants, and retail stores use them for targeted warmth. Outdoor Areas: Patios and open-air venues rely on radiant heaters for consistent heat in colder months. Specialized Industries: Used in paint drying, food processing, and even aviation for de-icing purposes. How to Choose the Right Ceramic Radiant Tube Heater When selecting a ceramic radiant tube heater, consider the following factors: Size and Heating Capacity Match the heater’s output (measured in BTUs or kW) to the area size. Fuel Type Determine if natural gas, propane, or electric models are most suitable for your facility. Installation Requirements Ensure the heater fits your space constraints and complies with safety standards. Control Options Look for models with programmable thermostats or smart controls for better energy management. Last Word A ceramic radiant tube heater offers an effective and energy-efficient way to provide warmth in industrial and commercial spaces. Its reliance on radiant heat transfer ensures precise and consistent heating, reducing energy costs and improving comfort. Whether you’re looking to heat a warehouse, outdoor area, or a specialized facility, these heaters deliver unmatched performance. By understanding how they work and selecting the right model for your needs, you can achieve optimal heating with minimal energy waste.
5 Unique Facts About Tubular Heater Greenhouse
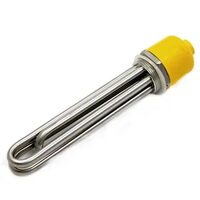
Heating a greenhouse efficiently is critical for plant health and energy savings. A tubular heater is an excellent solution, providing consistent, low-cost warmth. Greenhouse enthusiasts often overlook the potential of this compact heating option. However, beyond its efficiency, there are fascinating and lesser-known facts about using a tubular heater greenhouse setup that can enhance both productivity and sustainability. Here are five unique insights to maximize its benefits. 1. Energy Efficiency That Cuts Costs Dramatically Tubular heaters are designed for low-energy consumption, making them one of the most economical heating solutions for greenhouses. A standard tubular heater uses between 60 to 120 watts of power per foot, significantly lower than fan heaters or radiant systems. Why this matters: Reduced electricity bills: Greenhouses using tubular heaters can save up to 40% compared to conventional electric heating systems. Consistent temperature: They deliver uniform heat distribution, avoiding hotspots that can damage delicate plants. Eco-friendliness: Less energy consumption means a smaller carbon footprint, aligning with sustainable practices. Quick tip: Position your tubular heater near the base of your plants to create a gentle heat rise. This placement prevents temperature extremes and optimizes energy use. 2. Prevention of Frost Damage One of the standout benefits of tubular heaters is their ability to protect plants from frost during cold spells. Unlike other heating systems, their gentle warmth prevents condensation buildup that leads to freezing. Frost-prevention features: 24/7 operation: Most tubular heaters are designed for continuous use, ensuring no sudden temperature drops. Temperature control: Integrated thermostats allow you to maintain an ideal microclimate for frost-sensitive plants like tomatoes and orchids. By installing a tubular heater, you can extend your growing season and safeguard plants against sudden weather changes. 3. Safety Features Make Them Ideal for Enclosed Spaces Unlike traditional heaters, tubular heaters are engineered with safety in mind, making them perfect for confined greenhouse environments. Built-in safety advantages: Low surface temperature: Tubular heaters remain warm but not hot enough to ignite nearby materials. Moisture resistance: Most models are rated IPX4 or higher, ensuring they can withstand greenhouse humidity without malfunctioning. Automatic shutoff: Many tubular heaters include overheat protection, minimizing fire risks. For greenhouses with limited ventilation, these safety measures make tubular heaters a reliable choice. 4. Customizable to Any Greenhouse Size Tubular heaters are modular, meaning you can configure them to suit any greenhouse size or layout. Whether you have a compact backyard setup or a sprawling commercial operation, these heaters can adapt seamlessly. Customization tips: Length options: Tubular heaters are available in sizes ranging from 2 feet to 8 feet. Choose longer models for larger spaces. Link multiple units: Connect multiple heaters to create a network of even heat distribution. Wall-mount or freestanding: Flexible installation options ensure optimal placement for any greenhouse design. This adaptability allows you to scale your heating solution as your greenhouse expands. 5. Longevity and Low Maintenance Investing in a tubular heater is cost-effective in the long run due to its durability and minimal upkeep requirements. What makes them last: Robust construction: Most tubular heaters are built with corrosion-resistant aluminum or stainless steel, ensuring long-term performance in humid conditions. Simple maintenance: Occasional cleaning is all that’s required to keep them functioning optimally. Warranty coverage: Many reputable brands offer warranties ranging from 3 to 5 years, reflecting their reliability. Greenhouse owners can depend on tubular heaters for years without worrying about frequent replacements or high repair costs. Summary of benefits: Significant energy savings Frost prevention for extended growing seasons Enhanced safety for greenhouse environments Scalability for various greenhouse sizes Durable and low-maintenance heating Key Takeaways A tubular heater greenhouse is not just about keeping plants warm. It’s a smart, energy-efficient, and customizable solution that enhances plant health, protects against frost, and reduces operational costs. Final Words To maximize your greenhouse’s potential, invest in a tubular heater that aligns with your specific needs. With its unique advantages, it’s an asset for any grower striving for efficiency and sustainability.
5 Top Benefits of a Thermocouple
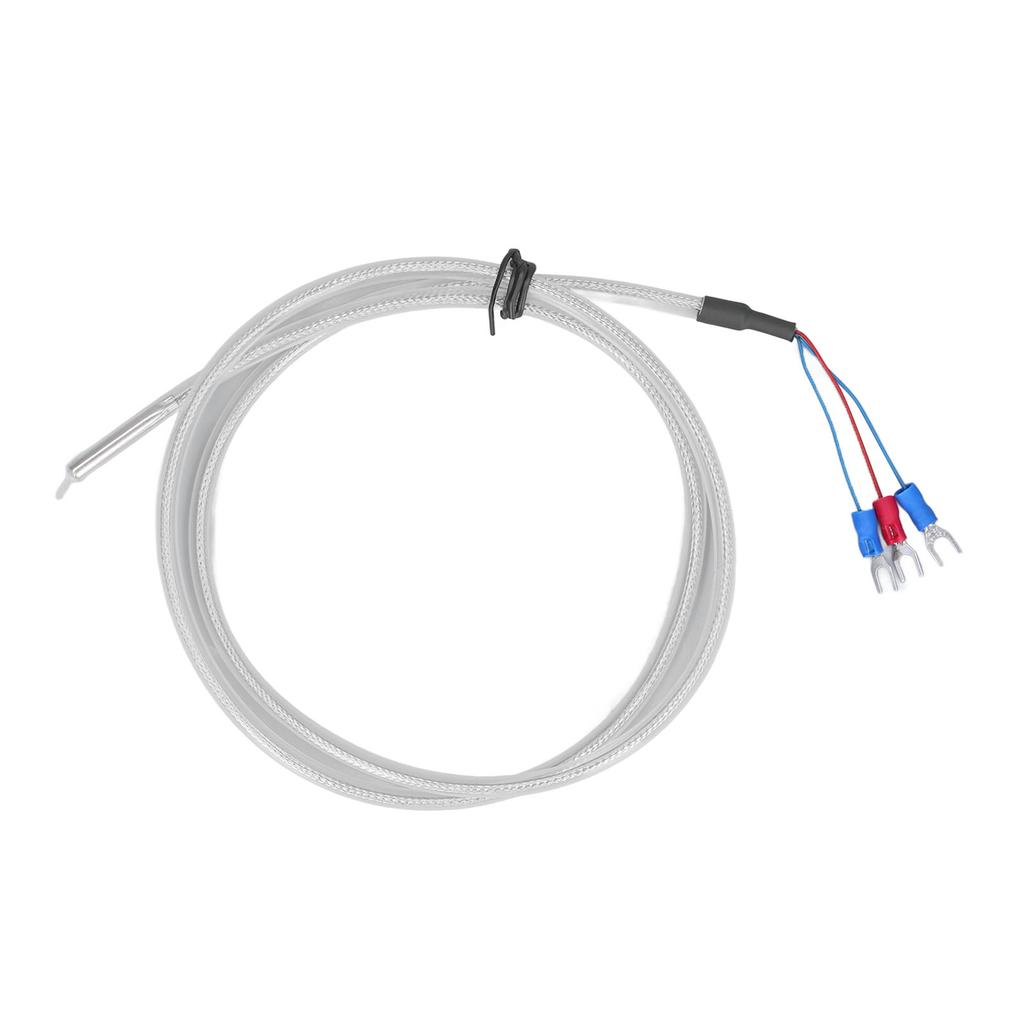
A thermocouple is one of the most reliable tools for measuring temperature in industrial and scientific applications. Known for its durability and precision, it is an essential component across industries like aerospace, automotive, and manufacturing. Whether you’re monitoring extreme heat in a furnace or tracking cooling rates in food processing, thermocouples provide accurate data critical for success. Let’s explore the five key benefits of a thermocouple that makes it indispensable. 1. Wide Temperature Range One of the biggest advantages of a thermocouple is its ability to measure temperatures across a vast range. From cryogenic levels as low as -250°C to extreme heat exceeding 2,300°C, thermocouples outperform most alternatives: Type K Thermocouple: The most commonly used, ideal for temperatures ranging from -200°C to 1,260°C. Type S Thermocouple: Accurate at temperatures above 1,500°C, making it suitable for metallurgy and glass production. This versatility allows industries to rely on thermocouples for diverse processes without switching between instruments. 2. Fast Response Time Thermocouple is designed for real-time temperature readings. They respond instantly to temperature changes due to their compact size and direct contact with the environment being measured. In applications like chemical reactors and gas turbines, rapid readings ensure safety and process efficiency. The absence of lag makes thermocouples ideal for dynamic systems where constant monitoring is essential. This speed gives industries the ability to make quick decisions, minimizing risks and optimizing outcomes. 3. Durability in Harsh Environments Industries often require equipment that can withstand harsh and extreme conditions. Thermocouple is built to perform reliably under such circumstances: Corrosion Resistance: Made with robust materials like stainless steel and Inconel, thermocouples resist damage in chemically aggressive environments. Shock and Vibration Tolerance: Used in engines and turbines, thermocouple continues to deliver accurate readings under constant mechanical stress. Their rugged design makes them an excellent choice for heavy-duty industries like oil and gas and aerospace. 4. Cost-Effective Solution Thermocouple offers an excellent balance between performance and affordability. Their simple construction and wide availability keep manufacturing costs low. Low Maintenance Requirements: Unlike other temperature sensors, thermocouples are durable and often require minimal upkeep. Longevity: A properly installed thermocouple can last for years, reducing the need for frequent replacements. This makes them a practical option for businesses looking to manage costs while maintaining operational efficiency. 5. Compatibility with Advanced Systems Thermocouples integrate seamlessly with modern monitoring systems. They are compatible with: Digital Displays: For easy temperature tracking. Data Loggers: Useful for recording temperatures over time. Automated Controls: Essential for precision manufacturing and process optimization. This adaptability ensures thermocouple remains relevant as industries advance technologically. Real-World Applications of a Thermocouple Furnace Monitoring: Ensures temperature consistency in metal and ceramic production. HVAC Systems: Maintains optimal heating and cooling performance. Food Processing: Tracks cooking and freezing conditions for quality control. Their reliability and versatility make thermocouples a preferred choice across these sectors. Final Words A thermocouple is more than just a temperature sensor; it’s a key to precision, efficiency, and safety in industrial and scientific processes. Its unmatched temperature range, quick responsiveness, and adaptability make it a must-have tool. For industries looking to improve operations while keeping costs under control, thermocouples are the perfect solution.
5 Reasons Why a Silicone Rubber Heater is a Must in Industrial Manufacturing
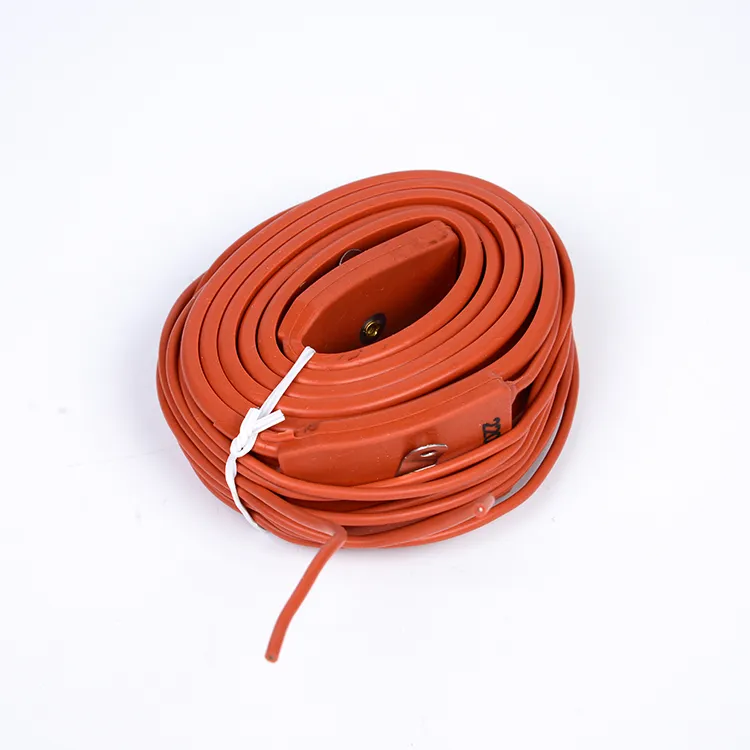
The silicone rubber heater is an essential tool for industries that demand efficient, reliable, and precise heating solutions. Known for its flexibility and durability, this heater stands out in applications where traditional heating elements fall short. Whether in aerospace, medical equipment, or food processing, its unique capabilities make it a critical component in industrial manufacturing. Below, we uncover the top five reasons why the silicone rubber heater is indispensable in this field. 1. Flexibility for Custom Applications The silicone rubber heater is designed for versatility, making it suitable for complex and irregular surfaces. Flexible Construction: Its silicone-based material allows it to bend and conform to different shapes. This makes it ideal for applications like pipes, tanks, and curved equipment surfaces. Custom Sizing and Wattage: Manufacturers can customize the size and watt density to meet specific industrial requirements, ensuring optimal heat distribution and efficiency. This adaptability ensures consistent heating performance even in unconventional setups, reducing the risk of uneven heating or system failures. 2. Durability in Extreme Conditions Industrial environments often subject heating systems to harsh conditions. The silicone rubber heater excels in durability. Temperature Resistance: It operates effectively in a wide range of temperatures, from -60°C to 230°C, ensuring reliability in both freezing and high-heat scenarios. Moisture and Chemical Resistance: Its silicone outer layer protects it from water, chemicals, and environmental exposure, making it highly dependable in humid or corrosive settings. This resilience reduces maintenance needs and extends the heater’s lifespan, even in demanding applications such as medical autoclaves and industrial ovens. 3. Energy Efficiency and Cost Savings Energy efficiency is critical in manufacturing, and the silicone rubber heater delivers on this front. Rapid Heat-Up Time: Its thin and lightweight design allows for faster heating, reducing energy consumption. Precision Heating: Built-in sensors, such as thermocouples, ensure precise temperature control, minimizing energy waste and overheating risks. These features contribute to significant operational cost savings, especially in industries like food processing and pharmaceutical manufacturing, where energy efficiency is a priority. 4. Lightweight and Easy Installation Traditional heaters can be bulky and difficult to install, but the silicone rubber heater offers a lightweight and user-friendly solution. Low Profile: Its slim design makes it easy to integrate into existing systems without requiring significant modifications. Simple Adhesion Options: Many heaters come with self-adhesive backing or mechanical fastening options, ensuring quick and secure installation. This ease of setup reduces downtime, making it a practical choice for industries that demand efficiency and minimal interruptions. 5. Versatility Across Industries The silicone rubber heater is a versatile solution that serves a wide range of industrial sectors. Aerospace: Ensures precise heating in critical components like de-icing systems and fuel lines. Automotive: Keeps batteries warm in electric vehicles for optimal performance during cold weather. Medical: Provides reliable heating in laboratory equipment and patient care devices. This adaptability ensures that manufacturers across industries benefit from its innovative design and capabilities. Final Thoughts A silicone rubber heater is not just another heating element; it’s a critical tool for improving manufacturing efficiency and reliability. Its flexibility, durability, and energy efficiency make it an unmatched solution for industries worldwide. Whether you’re working with precision medical devices or high-capacity industrial systems, this heater is a game-changer for modern manufacturing.
5 Unique Features of a Pipeline Heater
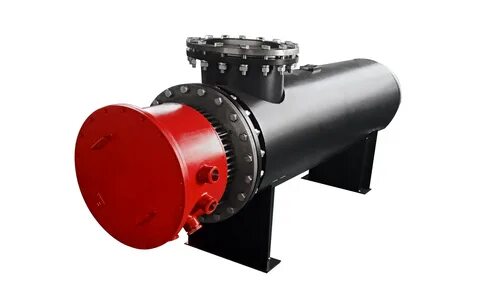
A pipeline heater plays a crucial role in industries that require precise temperature control for the transportation of liquids or gases. From preventing material blockages to ensuring efficient flow, these heaters provide unmatched reliability in challenging environments. Their innovative design and advanced features make them a valuable asset across industries such as oil and gas, chemical processing, and food production. Below are the five unique features of a pipeline heater that set it apart. 1. Exceptional Heat Uniformity Uniform heating is a critical requirement in pipelines, as inconsistent temperatures can lead to blockages and material degradation. Pipeline heaters are designed to deliver consistent heat distribution throughout the pipeline, ensuring smooth operation. Even Heat Transfer: The heaters are engineered to avoid hot or cold spots, critical for materials sensitive to temperature changes. Custom Heating Elements: Many models include heating elements tailored to the pipeline’s material and fluid type, enhancing overall performance. Energy Efficiency: Uniform heating prevents energy waste, reducing operating costs. Industries like chemical manufacturing benefit greatly from this feature as it prevents chemical reactions caused by temperature inconsistencies. 2. High-Temperature Capability Pipeline heaters are built to handle extreme temperatures, making them ideal for demanding applications. Many heaters can achieve operating temperatures above 500°F (260°C), essential for high-temperature processes. Thermal Stability: They maintain consistent output even during temperature fluctuations. Material Compatibility: High-temperature models are compatible with a range of materials, including viscous fluids and heavy oils. In oil and gas pipelines, this feature ensures smooth transportation of crude oil, which often requires elevated temperatures to flow efficiently. 3. Corrosion Resistance for Longevity Pipelines often transport substances that are chemically reactive or corrosive. A key feature of modern pipeline heaters is their corrosion-resistant construction, which ensures long-term durability. Protective Sheathing: Most heaters use materials like stainless steel or Inconel to resist corrosion. Chemical Resistance: Specialized coatings can handle aggressive chemicals and harsh environments. This durability minimizes maintenance costs and prevents unexpected downtime, especially in industries like pharmaceuticals and water treatment. 4. Built-In Safety Mechanisms Safety is paramount in industrial applications, and pipeline heaters incorporate robust features to protect equipment and personnel. Overheat Protection: Sensors detect abnormal temperatures and shut down the system to prevent damage. Explosion-Proof Designs: Heaters in hazardous environments, such as refineries, are engineered to prevent explosions. Leak Detection Systems: Advanced models include systems to identify leaks and immediately alert operators. These safety features make pipeline heaters reliable for high-risk environments, ensuring compliance with industry standards. 5. Customizable Configurations for Versatility Pipeline heaters can be customized to meet the specific needs of any application. This versatility allows them to perform seamlessly across various industries. Size and Wattage Options: They come in a wide range of sizes and power outputs to suit different pipeline lengths and capacities. Fluid-Specific Designs: Heaters can be optimized for transporting oils, gases, or chemicals. Remote Monitoring: Many models now include IoT-enabled systems for real-time monitoring and control. For industries like food production, this adaptability ensures precise temperature control, maintaining product quality and safety. Wrap Up A pipeline heater ensures operational efficiency and product integrity in industries dependent on fluid transportation. Their ability to deliver consistent heat, withstand harsh conditions, and adapt to various needs makes them a must-have solution. By investing in a high-quality pipeline heater, industries can reduce downtime, lower energy costs, and enhance overall productivity.
5 Benefits of a Hot Runner Heater
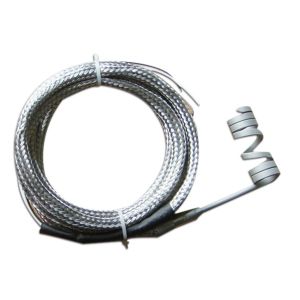
A Hot Runner Heater is critical in industries that rely on injection molding for mass production. Its precise heating capability ensures consistent material flow, reducing waste and improving efficiency. Industries such as automotive, consumer goods, and electronics depend on these systems to meet the growing demand for high-quality products. Here are five key benefits of using a hot runner heater in industrial applications. 1. Enhanced Production Efficiency A hot runner heater is designed to optimize production processes, particularly in injection molding. By keeping the material in a molten state, it minimizes interruptions during molding cycles. Reduced Cycle Times: Materials flow seamlessly through the system, speeding up production cycles. Consistent Flow: Unlike traditional systems, hot runner heaters maintain uniform temperature, ensuring smooth material movement without clogs. This improvement in efficiency directly impacts production output, making it a must-have for large-scale operations. 2. Improved Product Quality Uniform heating is crucial for producing defect-free products. Hot runner heaters excel in maintaining consistent temperatures across all molding cavities. No Cold Spots: The heater eliminates temperature fluctuations, preventing uneven material cooling. Precise Mold Filling: It ensures every cavity is filled correctly, reducing material voids and imperfections. With better temperature control, manufacturers produce higher-quality products with minimal defects. 3. Significant Material Savings Traditional injection molding systems often waste material due to runner scraps. Hot runner heaters eliminate this issue entirely. No Runner Scrap: As the system keeps the material molten, there’s no leftover runner waste. Lower Resin Consumption: Manufacturers save on raw material costs, especially for expensive resins. This reduction in waste directly contributes to lower production costs, making operations more sustainable. 4. Flexibility in Design Hot runner heaters allow for more complex product designs, opening up possibilities for advanced manufacturing. Supports Multi-Cavity Molds: The heaters work efficiently with molds that have multiple cavities, ensuring consistent heating for intricate designs. Improved Aesthetics: By eliminating weld lines and cold slugs, products have a smoother finish. This flexibility is particularly beneficial for industries such as electronics and medical equipment, where precision is paramount. 5. Long-Term Cost Efficiency Although the initial investment for a hot runner system may be higher, the long-term savings are substantial. Reduced Maintenance Costs: The system requires less maintenance compared to cold runner setups, saving time and money. Energy Efficiency: Hot runner heaters are energy-efficient, consuming less power while maintaining optimal performance. Over time, these factors lead to significant operational savings, boosting profitability. Last Word A Hot Runner Heater is more than a heating element; it’s a cornerstone of modern injection molding. Its ability to enhance efficiency, improve quality, save materials, support intricate designs, and reduce long-term costs makes it an invaluable tool for manufacturers. For industries looking to scale production while maintaining quality, hot runner heaters offer a reliable and cost-effective solution.
3 Reasons Why Industries Need High Temperature Cable
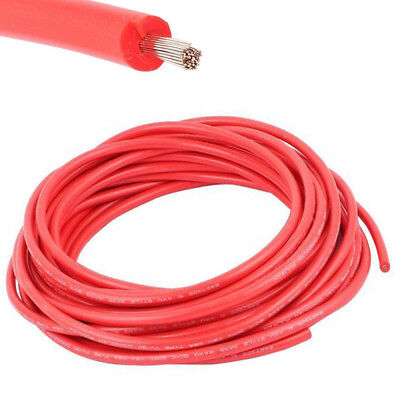
The industrial sector demands reliable and robust components, especially in extreme temperature settings. One crucial element that powers this reliability is the high temperature cable. From manufacturing to aerospace, high-temperature cables are essential for maintaining safety, efficiency, and durability in rigorous conditions. In this article, we’ll uncover the top reasons why a high temperature cable is indispensable for industry, supported by the latest data and insights. 1. Superior Heat Resistance Ensures Safety and Reliability One of the primary benefits of using high temperature cable in industrial settings is its ability to withstand extreme heat while maintaining safe and reliable operation. In environments where temperatures regularly exceed 250°C (482°F), regular cables would degrade or fail, posing severe safety risks. High-temperature cables, however, are engineered for these conditions, making them indispensable for high-stress applications: Enhanced Safety: High-temperature cables prevent fires and system failures by maintaining insulation integrity in high-heat environments. Industries like steel production and oil refineries rely on these cables to prevent accidents caused by cable breakdown. Reliable Operation: Even at peak loads, these cables don’t overheat or degrade, ensuring continuous and safe operations. A study by Grand View Research reports that the global high-temperature cable market is projected to grow at a CAGR of 4.1% from 2023 to 2030, driven largely by the demand for fire-resistant solutions in industrial settings. For facilities operating around-the-clock, high-temperature cables are a critical investment that pays off in both safety and performance. 2. Exceptional Durability Reduces Maintenance Costs Industrial applications demand cables that can withstand not only heat but also wear, abrasion, and exposure to chemicals. High-temperature cables meet these demands with durable materials such as silicone, fiberglass, and PTFE insulation: Extended Cable Lifespan: High-temperature cables offer increased resistance to wear and tear, extending the lifespan of the wiring systems. This reduces the frequency and costs associated with replacements. Low Maintenance: Industries can expect reduced downtime due to cable failures. In fact, maintenance teams report an average reduction of 25% in cable-related issues after switching to high-temperature cables, according to data from market research firm Mordor Intelligence. For industries like automotive manufacturing and food processing, where high temperatures and heavy machinery wear down equipment, these cables provide a cost-effective and low-maintenance solution. 3. Versatile Applications Across Multiple Sectors High-temperature cables are widely adaptable and are used in various industrial sectors due to their flexibility and compatibility with different environments. Here are a few examples of how these cables benefit specific industries: Aerospace: With extreme conditions in aircraft and spacecraft, high-temperature cables are necessary to ensure electrical systems remain functional even during intense heat and pressure. Petrochemical Industry: Refineries and chemical plants need cables that withstand both high temperatures and exposure to corrosive substances. High-temperature cables provide both qualities, protecting critical equipment and reducing environmental risks. Renewable Energy: In solar power plants, high-temperature cables are essential for handling elevated temperatures in PV systems, allowing consistent energy transfer without degradation. These diverse applications highlight how high-temperature cables are tailored to meet specific industrial needs, making them vital in maintaining operational efficiency and worker safety. Advantages of Using High Temperature Cables in Industry In summary, high-temperature cables provide numerous advantages, including: Enhanced Safety: Reduce risks of fire and insulation failure. Cost-Effectiveness: Lower maintenance and replacement costs. Broad Applicability: Suitable for diverse and high-demand sectors. Final Thoughts Investing in high temperature cable solutions is more than just meeting industry standards—it’s about securing reliable and durable connections that enhance productivity and safety across sectors. For any industrial operation facing extreme conditions, high-temperature cables prove essential to maintaining efficiency and minimizing risks.
What is a Heating Cable – A Short Guide
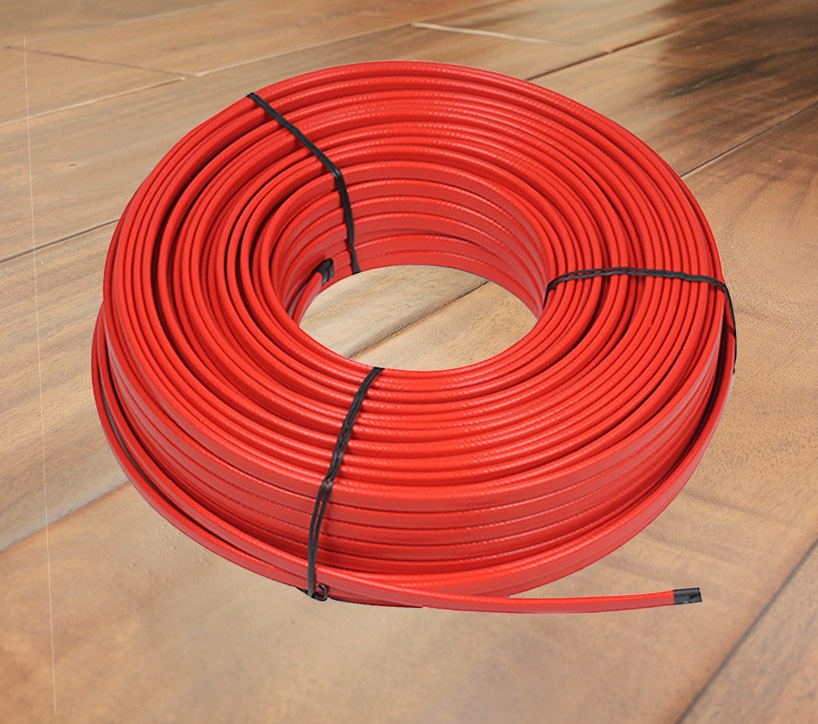
In cold environments, pipes and equipment are at risk of freezing, which can lead to costly damage and hazardous conditions. Heating cable provides a reliable, efficient solution to this problem. Designed to maintain consistent temperatures, heating cables are essential in industries and homes that need to prevent freeze-ups, ensure safety, and maintain smooth operations. In this guide, we’ll explore the uses, types, and benefits of heating cables. Understanding Heating Cable A heating cable is an electrical cable with a built-in heating element that transfers heat directly to pipes, surfaces, or spaces where temperature control is critical. Commonly used in industrial, commercial, and residential settings, heating cables come in various types designed for specific applications, each with unique properties and capabilities. Heating cables not only protect pipes but are also used for de-icing, snow melting, and maintaining specific temperatures in industrial processes. Types of Heating Cable Heating cables are categorized based on how they produce and maintain heat. Here are the most common types: Self-Regulating Heating Cables These cables adjust their heat output depending on the surrounding temperature. They’re energy-efficient, providing more heat when it’s colder and reducing output when the environment warms. Ideal for freeze protection in pipes and roof de-icing. Minimal risk of overheating, as they naturally decrease power in warmer conditions. Constant Wattage Heating Cables These cables supply a consistent level of heat regardless of temperature variations. Often used in applications that require a stable temperature. Suitable for industrial applications where precise heat maintenance is essential. Series Resistance Heating Cables Designed for long lengths, these cables use a specific resistance value to generate heat. Often found in petrochemical and oil facilities for freeze protection and process maintenance. Require careful installation, as their length must match the application to ensure safety. Key Benefits of a Heating Cable Heating cables offer numerous advantages across multiple settings: Pipe Protection: Prevents pipe bursts and flow obstructions in freezing temperatures, saving money on repairs and replacement. Roof and Gutter De-Icing: Keeps gutters and roof edges clear of ice dams, which can damage structures. Snow Melting for Driveways: Offers a safe, slip-free environment by melting snow and ice on outdoor surfaces. Industrial Temperature Maintenance: Maintains necessary temperatures in sensitive industrial processes, ensuring product consistency and safety. Installation and Safety Tips Proper installation is crucial for heating cables to function safely and effectively. Here are a few tips: Avoid Overlapping: Overlapping heating cables can cause overheating and damage the insulation. Always follow the manufacturer’s guidelines. Use Appropriate Insulation: Proper insulation helps heating cables perform efficiently, especially in freezing environments. Monitor and Test Regularly: Periodic checks ensure the cables are in good working condition and reduce the risk of unexpected failure. Final Words Heating cables are a powerful tool for maintaining temperature control in a wide range of applications. Whether you need to protect pipes, prevent ice buildup, or sustain specific temperatures in industrial processes, selecting the right heating cable can offer durability, efficiency, and safety. Reliable providers like Cheri Heater offers a range of heating cables tailored to meet both residential and commercial needs, ensuring your systems stay safe and operational in any environment.
What is a Band Heater – A Short Guide
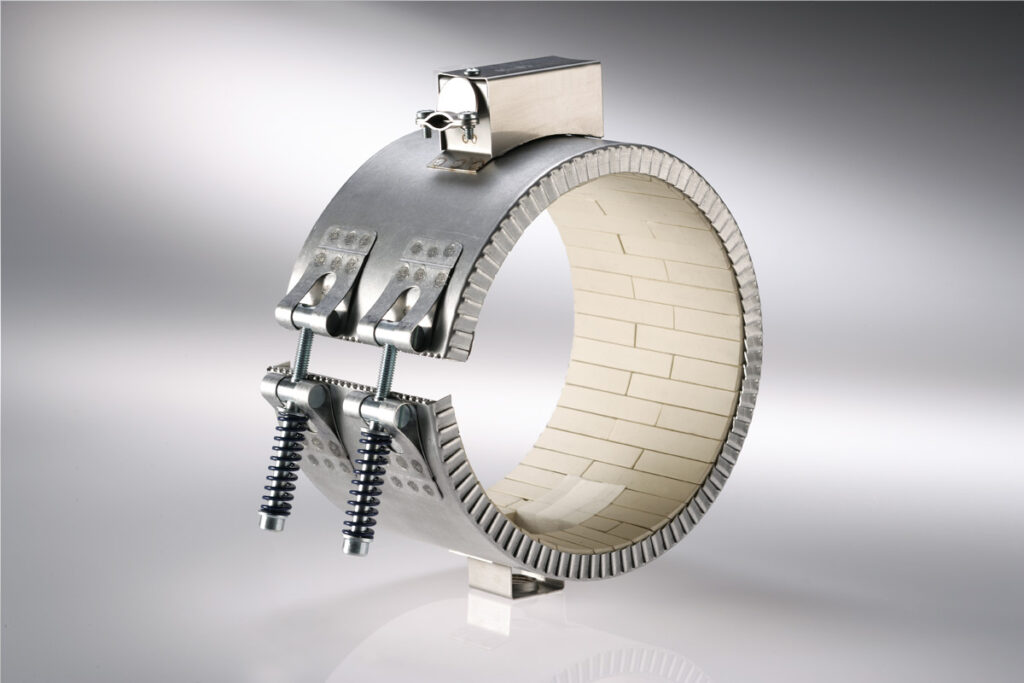
In industrial applications, maintaining precise temperatures is critical. Whether it’s for plastic extrusion, injection molding, or other manufacturing processes, consistent heat is necessary for quality and efficiency. This is where a band heater becomes essential. As one of the most effective heating tools, a band heater offers controlled heat exactly where it’s needed, making it indispensable in many industrial settings. In this guide, we’ll break down what a band heater is and why it’s crucial for numerous applications. What is a Band Heater? A band heater is a heating device primarily designed to encircle cylindrical parts, such as pipes, barrels, or nozzles, and generate heat for processes requiring uniform thermal distribution. It’s essentially a “belt” heater, wrapping around the cylindrical surface to maintain or elevate its temperature. Band heaters are widely used in various industries, including plastics, chemical processing, and food manufacturing. How Does a Band Heater Work? Band heaters operate through electrical resistance. When an electric current passes through the heater’s resistive element, heat is produced. This heat then transfers from the band heater to the external surface of the cylinder or pipe it encases. The key components in a band heater include: Heating Element: Often made from nickel-chromium (Ni-Cr) wire, which converts electric current into heat. Insulation: Reduces heat loss, ensuring efficient energy transfer to the target area. Outer Sheath: Protects the heater and user from exposure to the heating element. It’s usually made from materials like stainless steel or mica. Advantages of Using a Band Heater Using a band heater offers several benefits in industrial applications. Here’s why they are preferred for precision heating: Energy Efficiency: Band heaters are designed to transfer heat directly to the surface they are wrapped around, minimizing energy loss. Even Heat Distribution: The cylindrical shape ensures that heat is spread evenly, which is crucial for maintaining product quality. Precise Temperature Control: Advanced band heaters allow for highly specific temperature adjustments, enabling efficient and consistent heating. Space-Saving Design: Their compact form means they don’t require extensive installation space, making them suitable even for confined areas. How to Choose the Right Band Heater Selecting the appropriate band heater for your application can significantly impact energy efficiency and performance. Consider these factors: Temperature Requirements: Choose a heater type (mica, ceramic, mineral-insulated, or silicone) based on the temperature range required. Size and Fit: Ensure the band heater fits securely around the cylinder or pipe to prevent heat loss. Environmental Conditions: If the environment is prone to moisture, a silicone band heater may be best due to its moisture resistance. Durability: For heavy-duty applications, mineral-insulated heaters offer the highest durability and performance. Maintaining Your Band Heater for Optimal Performance Routine maintenance of band heaters can extend their lifespan and ensure continuous efficiency. Here are some best practices: Inspect Regularly: Check for signs of wear, corrosion, or damaged insulation. Clean Periodically: Remove any dust or residue on the heater to prevent overheating. Secure Connection: Make sure electrical connections are tight and free from damage to avoid energy loss or electrical issues. Temperature Calibration: Regularly test the heater’s temperature accuracy to prevent overheating and ensure consistent performance. Final Words A band heater is indispensable for industrial applications requiring precise temperature management. For those considering reliable industrial heating solutions, band heaters present a smart investment to streamline processes while keeping costs manageable.