Cartridge Heater: 10 Tips for Efficient Use
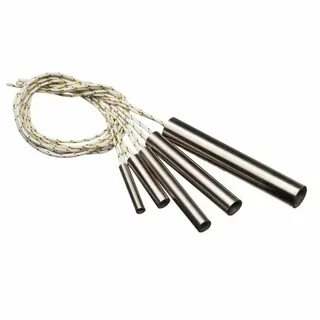
Today, every cartridge heater manufacturer produces these industrial workhorses to provide precise heat in various applications. But even the best cartridge heater needs proper care and attention to deliver optimal performance and longevity. Let’s delve into ten essential tips to maximize the efficiency and lifespan of your cartridge heaters. Tip 1: Understand Your Cartridge Heater Before diving into operation, grasp the fundamentals of your cartridge heater. This includes its wattage, voltage, length, diameter, and sheath material. Wattage and voltage: Ensure correct power supply for optimal performance and safety. Dimensions: Accurate measurements prevent installation issues and heat transfer problems. Sheath material: Choose the right material based on the application environment. Tip 2: Proper Installation Incorrect installation can lead to premature failure and safety hazards. Follow manufacturer guidelines meticulously. Secure mounting: Use suitable clamps or brackets to prevent movement. Thermal conductivity: Ensure good thermal contact between the heater and the heated medium. Electrical connections: Tighten connections to avoid overheating and potential fires. Tip 3: Temperature Control Overheating can drastically reduce a cartridge heater’s lifespan. Invest in a reliable temperature controller. Accurate sensors: Use precise temperature sensors for effective control. PID controllers: Consider advanced PID controllers for precise temperature regulation. Regular calibration: Ensure accurate temperature readings through calibration. Tip 4: Prevent Overloading Overloading can cause the heater to burn out. Calculate the required wattage carefully. Load matching: Ensure the heater’s wattage aligns with the application’s heat demand. Thermal calculations: Conduct proper heat transfer calculations to prevent overloading. Safety margins: Incorporate safety factors to avoid unexpected surges. Tip 5: Clean Regularly Accumulated dirt and debris can hinder heat transfer and reduce efficiency. Inspection schedule: Regularly inspect the heater for contaminants. Cleaning methods: Use appropriate cleaning methods based on the environment. Preventative measures: Implement measures to minimize contamination. Tip 6: Monitor Wear and Tear Regular inspections help identify potential issues before they escalate. Visual checks: Look for signs of damage, such as cracks or discoloration. Performance evaluation: Monitor heating performance for any decline. Replacement planning: Have spare heaters ready to avoid production disruptions. Tip 7: Optimize Thermal Conductivity Efficient heat transfer is crucial for optimal performance. Thermal interface materials: Use thermal paste or grease to improve contact. Heater placement: Position the heater for maximum heat dissipation. Material selection: Choose materials with high thermal conductivity for the heated components. Tip 8: Consider Thermal Cycling Frequent on/off cycles can shorten heater life. Minimize thermal shock. Ramp-up and cool-down times: Gradually increase and decrease temperature. Soft starters: Use soft starters to reduce voltage spikes. Insulation: Insulate the heater to maintain temperature during off-cycles. Tip 9: Emergency Shutdown Implement safety measures to protect against overheating and fires. Thermal cut-offs: Install thermal cut-offs as a backup safety measure. Fire suppression systems: Consider using fire suppression systems in hazardous areas. Emergency procedures: Develop clear emergency procedures for heater-related incidents. Tip 10: Proper Storage Store unused cartridge heaters in a cool, dry place to preserve their condition. Original packaging: Use original packaging or protective containers. Moisture protection: Store heaters in moisture-free environments. Avoid physical damage: Handle heaters carefully to prevent damage. By following these tips, you can significantly extend the life of your cartridge heaters and optimize their performance. Remember, preventive maintenance is key to avoiding costly breakdowns and ensuring uninterrupted production.
Top 5 MI Heating Cable Benefits for Industries
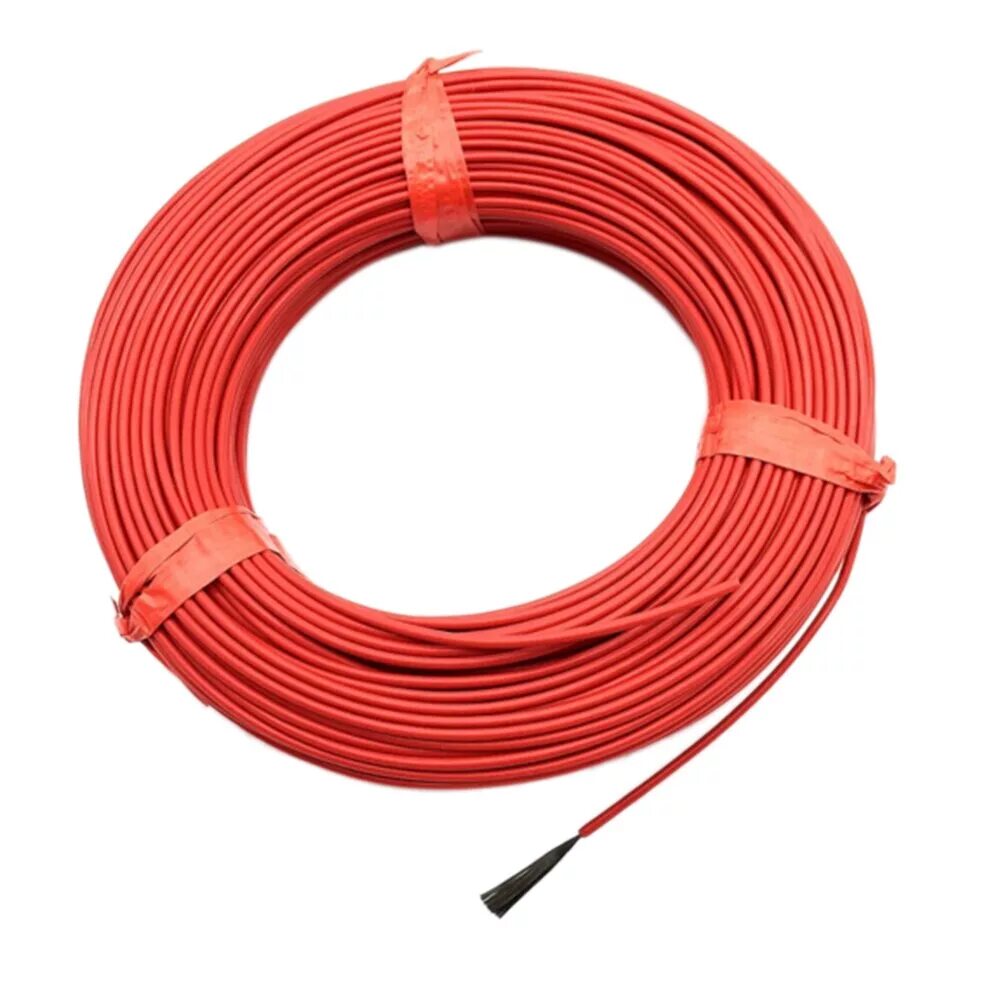
Reliable heating solutions are crucial in every industrial application. MI Heating Cable stands out as a top choice for many industries. This innovative technology offers numerous advantages that can boost efficiency and safety in various applications. Let’s explore the top five benefits of MI Heating Cable and why it’s becoming increasingly popular among industry professionals. 1. Superior Temperature Control One of the most significant advantages of MI Heating Cable is its ability to provide precise temperature control. This feature is essential in many industrial processes where maintaining a specific temperature is critical. Consistent heat distribution: MI Heating Cable ensures even heat distribution along its entire length, eliminating hot or cold spots. Quick response time: The cable reacts rapidly to temperature changes, allowing for swift adjustments. Wide temperature range: It can operate effectively from sub-zero temperatures up to 600°C (1112°F). Real-life example: In a pharmaceutical manufacturing plant, MI Heating Cable is used to maintain a constant temperature in storage tanks. This precise control helps preserve the quality and efficacy of sensitive medications. 2. Durability and Longevity MI Heating Cable is built to last, making it an excellent investment for industries looking for long-term heating solutions. Robust construction: The cable’s mineral insulation and metal sheath provide exceptional protection against mechanical damage. Resistance to harsh environments: It can withstand extreme conditions, including high temperatures, chemicals, and moisture. Minimal maintenance: Due to its sturdy design, MI Heating Cable requires less upkeep compared to other heating systems. According to a recent study, MI Heating Cable installations have an average lifespan of 20-30 years, significantly longer than many alternative heating solutions. 3. Energy Efficiency In an era where energy conservation is paramount, MI Heating Cable offers impressive energy efficiency benefits. Low heat loss: The cable’s design minimizes heat loss, ensuring that most of the energy is used for its intended purpose. Zoned heating: It allows for targeted heating of specific areas, reducing overall energy consumption. Compatibility with smart controls: MI Heating Cable can be integrated with advanced control systems for optimized energy use. A food processing plant reported a 15% reduction in energy costs after switching to MI Heating Cable for their pipe freeze protection system. 4. Versatility in Applications The adaptability of MI Heating Cable makes it suitable for a wide range of industrial applications. Process temperature maintenance: Keeps pipes, tanks, and vessels at the required temperature. Freeze protection: Prevents water lines and equipment from freezing in cold climates. Snow and ice melting: Used in walkways, ramps, and roofs to prevent ice buildup. Heat tracing: Maintains viscosity in fluid transport systems. For example, an oil refinery in Alaska uses MI Heating Cable to prevent crude oil from solidifying in pipelines during harsh winter months. 5. Enhanced Safety Features Safety is a top priority in any industrial setting, and MI Heating Cable offers several features that contribute to a safer working environment. Low fire risk: The mineral insulation is non-flammable, reducing the risk of fires. No toxic fumes: Unlike some plastic-insulated cables, MI Heating Cable doesn’t emit harmful fumes when heated. Grounded metal sheath: Provides an extra layer of electrical safety. Fail-safe design: If damaged, the cable typically fails in an open circuit, preventing overheating. A chemical processing facility reported zero safety incidents related to their heating system in the five years since installing MI Heating Cable. Final Words MI Heating Cable offers numerous benefits for industries, from superior temperature control to enhanced safety features. Its durability, energy efficiency, and versatility make it an excellent choice for a wide range of applications. By choosing MI Heating Cable, businesses can improve their processes, reduce energy costs, and create safer working environments. As technology advances, we can expect to see even more innovative applications for this versatile heating solution in the future.
5 Practical Ways to Use Immersion Tubular Heater
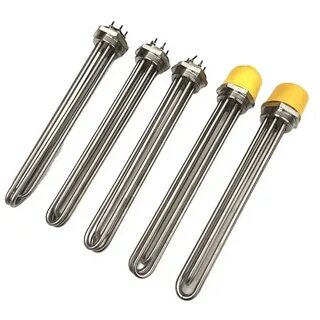
Heating solutions play a crucial role in many industries and everyday applications. The Immersion Tubular Heater stands out as a versatile and efficient option. This powerful heating device can transform various processes and improve outcomes in surprising ways. We will explore five practical uses for the Immersion Tubular Heater that show its flexibility and effectiveness. 1. Enhancing Food Processing In the food industry, maintaining precise temperatures is key to quality and safety. Immersion Tubular Heaters excel in this area, offering several benefits: Consistent heating: They provide even heat distribution, crucial for large-scale cooking and pasteurization. Quick temperature changes: Rapid heating and cooling help in processing different food items efficiently. Sanitary design: Their smooth surface is easy to clean, meeting strict food safety standards. A recent study showed that using Immersion Tubular Heaters in dairy pasteurization improved energy efficiency by 15% compared to traditional methods. 2. Improving Chemical Processing Chemical reactions often require specific temperatures to proceed correctly. Immersion Tubular Heaters offer precise control, making them ideal for this industry. Temperature accuracy: They can maintain temperatures within ±1°C, crucial for sensitive reactions. Corrosion resistance: Many models come with special coatings to withstand harsh chemicals. Customizable designs: Heaters can be shaped to fit various tank sizes and configurations. In a real-world example, a pharmaceutical company used custom Immersion Tubular Heaters to speed up their drug synthesis process by 20%. This led to faster production times and lower costs. 3. Enhancing Water Treatment Clean water is essential, and Immersion Tubular Heaters play a vital role in water treatment processes. Efficient heating: They can quickly heat large volumes of water for purification. Energy-saving: Direct immersion means less heat loss compared to external heating methods. Scalability: Heaters can be easily added or removed to adjust to changing needs. 4. Powering Industrial Cleaning Many industries rely on hot water and steam for cleaning. Immersion Tubular Heaters offer an efficient solution for these applications. High-temperature capability: They can produce water hot enough for steam generation. Durability: Built to withstand frequent use in demanding environments. Safety features: Many models include automatic shut-off to prevent overheating. 5. Supporting Renewable Energy Systems As the world shifts towards renewable energy, Immersion Tubular Heaters are finding new roles in supporting these systems. Solar thermal support: They can provide backup heating for solar water heaters on cloudy days. Biomass processing: Heaters help maintain optimal temperatures in biogas digesters. Energy storage: They’re used in thermal energy storage systems to store excess renewable energy as heat. Last Word The immersion tubular heater proves its worth across various industries and applications. From food processing to renewable energy support, its versatility and efficiency make it a valuable tool. As technology advances, we can expect to see even more innovative uses for these powerful heating devices. Whether you’re in manufacturing, water treatment, or exploring new energy solutions, consider how an immersion tubular heater might improve your processes.
5 Applications of Best Flange Tubular Heater in Manufacturing
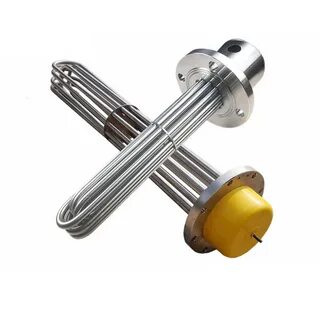
Heating plays a crucial role in many manufacturing processes. The best flange tubular heater stands out as a top choice for various industrial applications. These heaters are known for their efficiency, durability, and versatility. Let’s explore five key ways manufacturers are using these heaters to improve their operations and product quality. 1. Plastic Molding and Extrusion Plastic molding and extrusion processes rely heavily on precise temperature control. The best flange tubular heater excels in this area, offering several benefits: Even heat distribution: These heaters provide uniform heat across the mold or extruder barrel. Quick temperature changes: They can rapidly heat up or cool down, allowing for faster production cycles. Energy efficiency: Flange tubular heaters use less energy compared to other heating methods. A recent study showed that manufacturers using flange tubular heaters in plastic molding saw a 15% increase in production speed. This boost in efficiency can lead to significant cost savings over time. 2. Food Processing Equipment In the food industry, maintaining proper temperatures is crucial for safety and quality. Flange tubular heaters are ideal for various food processing applications: Cooking and baking: They provide consistent heat for ovens and cooking equipment. Sterilization: These heaters can reach the high temperatures needed for sterilizing equipment. Packaging: They help seal packaging materials safely and efficiently. For example, a large bakery in Chicago switched to flange tubular heaters in their ovens. They reported a 20% improvement in baking consistency and a 10% reduction in energy costs. 3. Chemical Processing Chemical reactions often require specific temperatures to occur. The best flange tubular heater offers precise control for these sensitive processes: Reactor vessels: They can maintain exact temperatures for complex chemical reactions. Storage tanks: These heaters keep chemicals at the right temperature during storage. Distillation columns: They provide the heat needed for the effective separation of compounds. 4. Aerospace Manufacturing The aerospace industry demands high precision in all aspects of manufacturing. Flange tubular heaters meet these strict requirements: Composite curing: They provide the exact heat needed for curing advanced materials. Metal heat treatment: These heaters can reach the high temperatures required for treating aerospace alloys. Environmental testing: They’re used in chambers that simulate extreme conditions for aircraft parts. 5. Semiconductor Production The semiconductor industry relies on ultra-clean and precise manufacturing processes. Flange tubular heaters play a vital role: Wafer processing: They provide the heat needed for various stages of chip production. Clean room heating: These heaters can be designed to meet strict cleanliness standards. Chemical vapor deposition: They supply the heat for this critical step in semiconductor manufacturing. A major chip manufacturer in Taiwan reported a 40% decrease in heating-related defects after upgrading to high-quality flange tubular heaters. Wrap Up The best flange tubular heater has proven its worth across various manufacturing sectors. As industries continue to evolve, the role of these heaters is likely to grow even further. Manufacturers looking to improve their processes should consider the benefits of flange tubular heaters. With their versatility and performance, they can be a game-changer in many industrial applications. The examples we’ve seen show that investing in quality heating solutions can lead to significant improvements in productivity and product quality.
How Do Electric Tube Heaters Work?
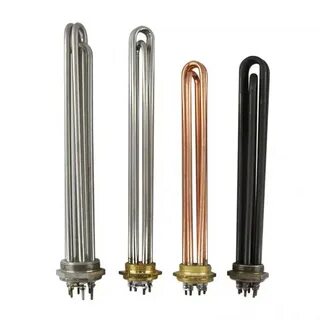
An electric tubular heater is a vital tool used in various industries for efficient and targeted heating. Understanding how these heaters work is essential, whether you’re looking to improve your knowledge or make informed decisions for your business. This blog post will enlighten you about the mechanics of electric tube heaters, breaking down their components and applications in simple terms. What is an Electric Tubular Heater? Electric tubular heaters are versatile heating elements used for warming solids, liquids, and gases. They are designed to convert electrical energy into heat with high efficiency. The heaters are made of a metal tube, usually stainless steel, with an insulated heating coil inside. This coil heats up when electricity passes through it, and the surrounding metal tube transfers the heat to the material being heated. Sheath Material: The outer tube is typically made from durable materials like stainless steel or Incoloy, which can withstand high temperatures and resist corrosion. Heating Coil: Inside the tube, a coil made of resistance wire (usually nickel-chromium) is the primary source of heat. Insulation: Magnesium oxide powder surrounds the heating coil inside the tube. This material not only insulates the coil electrically but also transfers heat from the coil to the tube efficiently. How Does an Electric Tubular Heater Work? Electric tubular heaters operate by generating heat through electrical resistance. When electricity flows through the resistance wire in the heating coil, it generates heat. This heat is then conducted to the outer metal sheath, which transfers it to the medium that needs to be heated, whether it’s air, water, oil, or another substance. These heaters can be designed to provide either direct or indirect heating. In direct heating, the heater comes into direct contact with the material to be heated, such as in immersion heaters used for heating water. In indirect heating, the heater warms the surrounding air or liquid, which then heats the target material, like in ovens or industrial heating systems. Applications of Electric Tubular Heaters Electric tubular heaters are used in various industries due to their versatility and reliability. HVAC Systems: They are commonly used in heating, ventilation, and air conditioning systems to maintain comfortable temperatures in buildings. Food Processing: In the food industry, these heaters ensure consistent temperatures for cooking, baking, and drying processes, maintaining food safety and quality. Industrial Equipment: They are used in machinery that requires controlled heating, such as plastic molding machines and packaging equipment. Laboratory Instruments: In laboratories, electric tubular heaters provide precise and consistent heat for experiments and testing. Water Heating: Electric tubular heaters are often used in water heaters and boilers, providing efficient and reliable heating. Benefits of Electric Tubular Heater Electric tubular heaters offer several advantages that make them a popular choice across various applications. Energy Efficiency: These heaters are designed to convert nearly all the electrical energy into heat, making them highly efficient. Durability: Made from robust materials like stainless steel, they can withstand high temperatures and harsh conditions, ensuring long-lasting performance. Versatility: With the ability to heat solids, liquids, and gases, electric tubular heaters are versatile and can be customized for specific applications. Precise Temperature Control: These heaters offer accurate and consistent heating, which is crucial in processes where temperature control is vital. Last Word Understanding how an electric tubular heater works is crucial for anyone involved in industries that rely on precise and efficient heating. These heaters offer a combination of energy efficiency, durability, and versatility that makes them invaluable in various applications. By choosing the right heater and maintaining it properly, you can ensure optimal performance and longevity, making them a reliable choice for your heating needs.
What is the Difference Between Cartridge Heater and Immersion Heater?
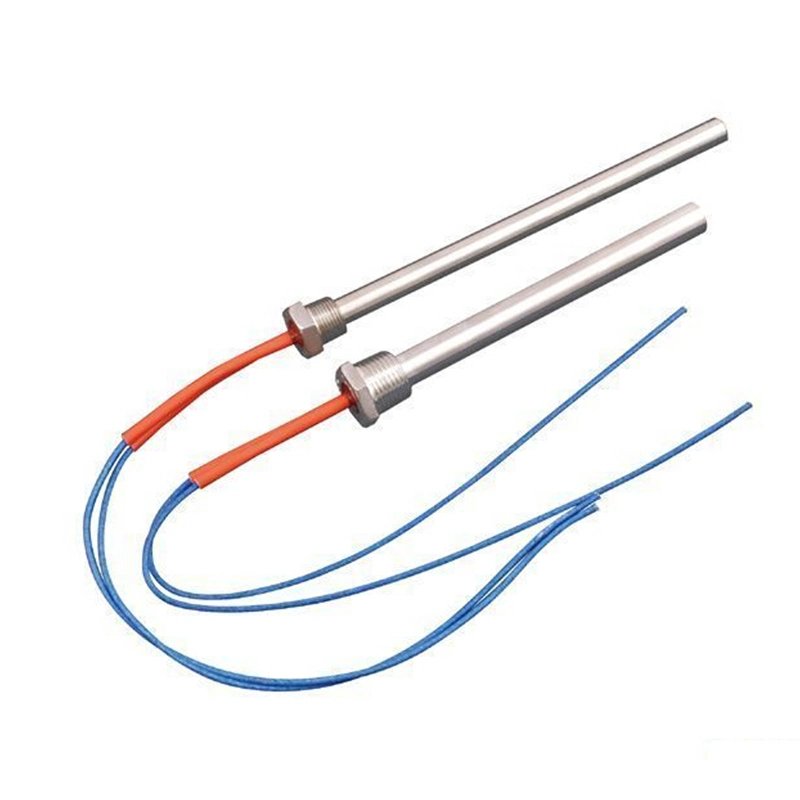
When comparing heating elements for industrial or commercial use, understanding the differences between a cartridge heater with thermocouple and an immersion heater is crucial. Both serve the purpose of heating, but they do so in distinct ways, making them suitable for different applications. Understanding Cartridge Heaters Cartridge heaters are compact, cylindrical heating elements designed to fit into holes or spaces within a material. They are primarily used to heat metal parts, molds, or dies where precise temperature control is needed. Construction: A cartridge heater consists of a resistance coil, typically made of nickel-chromium, that is insulated by magnesium oxide powder. This coil is housed within a sheath, often made of stainless steel or Incoloy, which protects it from high temperatures and corrosion. Thermocouple Integration: A key feature of the cartridge heater with thermocouple is its ability to monitor and control the temperature. The thermocouple is embedded within the heater, providing real-time temperature feedback, which helps in maintaining precise control over the heating process. Applications: Cartridge heaters are ideal for applications requiring focused, high-temperature heating. They are commonly used in the plastics industry, packaging machines, medical devices, and the automotive industry. Understanding Immersion Heaters Immersion heaters, on the other hand, are designed to be immersed directly into the fluid or material that needs to be heated. They are widely used in industries where large volumes of liquid or gas require efficient heating. Construction: Immersion heaters consist of tubular heating elements that are submerged in the medium to be heated. The heating elements are typically made of copper, steel, or Incoloy, depending on the application. The elements can be shaped in different configurations, such as U-shaped, straight, or circular, to fit the specific needs of the application. Thermocouple Integration: Like cartridge heaters, immersion heaters can also be equipped with a thermocouple for precise temperature control. The thermocouple monitors the temperature of the fluid, allowing for automatic adjustments to maintain the desired heat level. Applications: Immersion heaters are used in various industries, including chemical processing, oil and gas, food and beverage, and water heating systems. They are ideal for heating large volumes of liquid, such as water, oils, or chemicals. Key Differences Between Cartridge Heaters and Immersion Heaters While both cartridge heaters and immersion heaters are designed to provide heat, they differ in several key aspects: Heating Method: Cartridge Heater: Provides localized heat directly to solid materials or small spaces. Immersion Heater: Heats liquids or gases by direct immersion in the medium. Applications: Cartridge Heater: Best suited for precise heating of metal parts, molds, or confined spaces. Immersion Heater: Ideal for heating large volumes of fluids or gases, such as in industrial tanks or containers. Installation: Cartridge Heater: Typically installed in a drilled hole or small cavity within the material to be heated. Immersion Heater: Installed by submerging the heating element directly into the liquid or gas to be heated. Temperature Control: Cartridge Heater with Thermocouple: Provides highly accurate temperature control, making it suitable for applications requiring exact temperature regulation. Immersion Heater: While it can also be equipped with a thermocouple, it is generally used for applications where broader temperature control is acceptable. Choosing the Right Heater for Your Needs Selecting between a cartridge heater with thermocouple and an immersion heater depends on the specific requirements of your application. If precision is key, and you need to heat a small area or solid object, a cartridge heater is the better choice. The integration of a thermocouple ensures you can maintain tight control over the temperature, which is critical in processes like plastic molding or die casting. If you are heating large volumes of liquid or gas, an immersion heater is the way to go. It’s designed to efficiently heat larger spaces, making it perfect for industries that require bulk heating, like water treatment or chemical processing. Last Word Understanding the differences between a cartridge heater and an immersion heater helps in making an informed decision for your heating needs. Each has its strengths and is designed for specific applications, ensuring that you can achieve the desired temperature control and efficiency in your processes. Whether you need the pinpoint accuracy of a cartridge heater with thermocouple or the broad heating capacity of an immersion heater, knowing these distinctions will guide you to the best choice for your industrial needs.
Ultimate Guide to Tubular Heaters with Thermostat
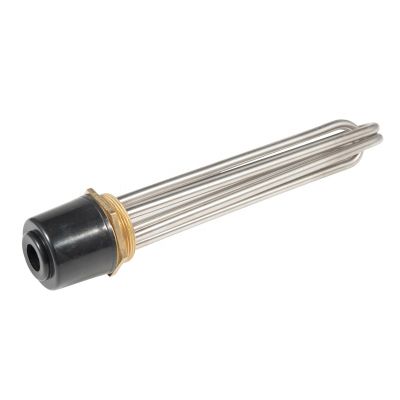
A tubular heater with thermostat is more than just a heating device; it’s a tailored climate control solution. It’s the unsung hero of many spaces, delivering consistent warmth without breaking the bank. But with countless options flooding the market, choosing the right one can feel like searching for a needle in a haystack. Fear not! This guide will illuminate the path, transforming you from a heating novice to a thermostat-savvy expert. Understanding Tubular Heaters with Thermostat At its core, a tubular heater is a long, slender heating element encased in a protective sheath. It’s often made of aluminum or stainless steel. The “tubular” part refers to its shape, while the “heater” part signifies its function – to generate heat. But what truly sets it apart is the thermostat. This intelligent companion ensures your space stays at the desired temperature, preventing overheating and optimizing energy consumption. How Tubular Heaters with Thermostat Work The magic happens within the heater’s core. Electricity flows through the resistive element, generating heat. This heat is then transferred to the surrounding environment. The thermostat, acting as the brain of the operation, continuously monitors the temperature. If it drops below the set point, it signals the heater to turn on. Conversely, if the temperature rises above the set point, it switches off. This constant cycle maintains a steady temperature. Types of Tubular Heaters with Thermostat Not all tubular heaters are created equal. Understanding the different types is crucial for selecting the perfect fit. Standard Tubular Heaters: These are the most common type, offering basic heating functionality with a thermostat. They’re ideal for general-purpose heating in spaces like garages, workshops, or greenhouses. Explosion-Proof Tubular Heaters: Designed for hazardous environments, these heaters are built to withstand explosive atmospheres. They are commonly used in industrial settings. Waterproof Tubular Heaters: Perfect for damp areas, these heaters have a protective coating to prevent water damage. They are often used in bathrooms, kitchens, or outdoor spaces. Factors to Consider When Choosing a Tubular Heater with Thermostat Selecting the right tubular heater involves several factors: Size of the Area: The heater’s wattage should match the room’s size to ensure efficient heating. Desired Temperature: Consider the ideal temperature for your space and choose a heater with a suitable thermostat range. Mounting Options: Wall-mounted, floor-standing, or portable options are available based on your preferences. Safety Features: Look for features like overheat protection, tip-over switches, and IP ratings for safety. Energy Efficiency: Consider the heater’s energy consumption to minimize utility bills. Installation and Maintenance Proper installation is essential for optimal performance and safety. Most tubular heaters come with installation instructions. If you’re unsure, consult a professional electrician. Regular maintenance is key to prolonging the heater’s lifespan. Clean the heater regularly to remove dust and debris. Check the thermostat’s accuracy periodically. If you notice any issues, contact the manufacturer or a qualified technician. Common Applications of Tubular Heaters with Thermostat Tubular heaters with thermostats find applications in various settings: Residential: Heating garages, basements, workshops, and bathrooms. Commercial: Maintaining temperature in warehouses, factories, and retail spaces. Agricultural: Providing warmth for livestock, greenhouses, and poultry farms. Industrial: Preventing frost in pipes, tanks, and equipment. Safety Tips for Using Tubular Heaters Never leave a heater unattended, especially when children or pets are present. Keep combustible materials away from the heater. Use the heater on a stable, level surface. Regularly inspect the power cord for damage. By understanding the nuances of tubular heaters with thermostats, you can make an informed decision and enjoy the benefits of consistent warmth in your space.
Cartridge Heaters with Thermocouples: A Comprehensive Buying Guide
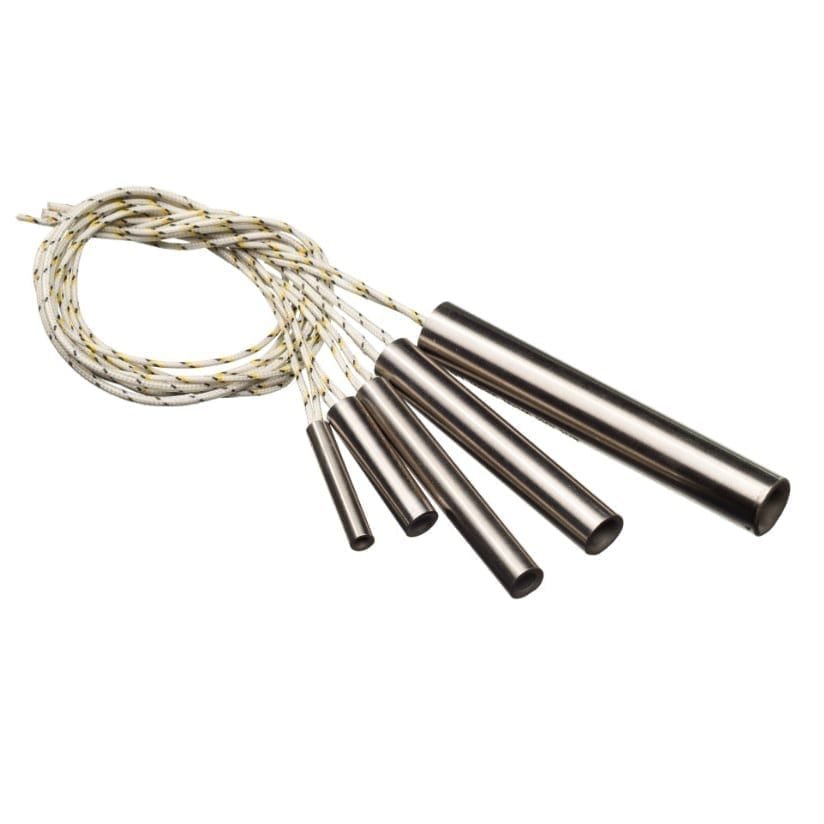
Cartridge heater with thermocouple is a crucial component in many industrial and commercial applications. Selecting the right one can be daunting due to the various options available. This guide will equip you with essential knowledge to make an informed decision. Understanding Cartridge Heaters with Thermocouples A cartridge heater is a cylindrical heating element inserted into a drilled hole to provide localized heat. Integrating a thermocouple into the heater offers precise temperature control. Key Components: Sheath: The outer protective layer, often made of stainless steel, protects the heating element. Heating Element: Converts electrical energy into heat. Magnesium Oxide: Insulating material between the heating element and sheath. Thermocouple: Measures the heater’s temperature and sends signals to a controller. Factors to Consider When Buying Several factors influence the choice of a cartridge heater with a thermocouple: Wattage: Determines the heater’s power output. Higher wattage for faster heating, lower for delicate applications. Voltage: Matches the available power supply. Common options include 110V, 220V, and 240V. Diameter and Length: Ensure the heater fits the target application’s hole size. Thermocouple Type: Choose between J, K, or other types based on temperature range and accuracy needs. Sheath Material: Select based on the environment, considering factors like corrosion resistance and temperature limits. Lead Wire Length: Ensure sufficient length for connection to the controller. Mounting Style: Consider options like straight, angled, or flanged based on installation requirements. Applications of Cartridge Heaters with Thermocouples Cartridge heaters with thermocouples find applications in various industries: Plastics: Mold heating, extrusion processes, and hot plate applications. Packaging: Sealing and cutting processes. Food Processing: Cooking, heating liquids, and sterilization. Medical Equipment: Sterilization, temperature control, and warming devices. Automotive: Engine block heating, component drying, and paint curing. Benefits of Using Cartridge Heaters with Thermocouples Precise Temperature Control: The thermocouple ensures accurate temperature maintenance. Efficiency: Targeted heating minimizes energy consumption. Versatility: Suitable for various applications and industries. Durability: Built to withstand harsh environments. Safety: Integrated thermocouple enhances safety by preventing overheating. Installation and Maintenance Tips Proper installation and maintenance are crucial for optimal performance and longevity. Clean Installation Area: Remove debris to prevent damage to the heater. Secure Mounting: Use appropriate clamps or holders to prevent movement. Thermal Conductivity: Ensure good thermal contact between the heater and the heated material. Regular Inspection: Check for signs of wear, damage, or contamination. Calibration: Periodically calibrate the thermocouple for accuracy. Choosing the Right Supplier Selecting a reputable supplier is essential for obtaining high-quality cartridge heaters. Consider the following: Experience and Expertise: Choose a supplier with a strong track record in the industry. Product Range: Ensure the supplier offers a variety of options to meet your needs. Customization Capabilities: Look for suppliers that can provide custom solutions. Customer Support: Reliable after-sales support is crucial. Last Word By carefully considering these factors and following best practices, you can select the ideal cartridge heater with thermocouple for your application and optimize your system’s performance.
How to Choose the Right Cartridge Heater Manufacturer
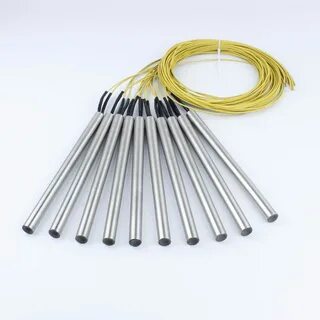
Selecting the right Cartridge heater manufacturer is crucial for ensuring optimal performance and longevity in your industrial processes. With countless options available, making an informed decision can be overwhelming. This guide will walk you through key factors to consider when choosing a cartridge heater manufacturer, empowering you to make a confident choice. Understanding Your Specific Needs Before diving into manufacturer selection, clearly define your cartridge heater requirements. Application: Identify the specific application where the heater will be used. Different applications demand different heater specifications. Temperature Range: Determine the desired operating temperature range. This will influence the choice of materials and heater design. Wattage: Calculate the required wattage based on the heat output needed for your application. Dimensions: Measure the available space for the heater, including diameter and length. Environment: Consider the operating environment, such as exposure to moisture, chemicals, or extreme temperatures. Evaluating Cartridge Heater Manufacturers Once you have a clear understanding of your needs, it’s time to evaluate potential manufacturers. Experience and Expertise: Look for manufacturers with a proven track record in the industry. Experience translates to quality products and reliable service. Product Range: Ensure the manufacturer offers a wide range of cartridge heaters to accommodate various applications and requirements. Customization Capabilities: Flexibility to customize heaters based on specific needs is a valuable asset. Quality Control: Investigate the manufacturer’s quality control measures, including certifications and testing procedures. Material Selection: Assess the manufacturer’s knowledge of different materials and their suitability for various applications. Manufacturing Process: Understand the manufacturing process to ensure consistency and reliability. Lead Times: Consider the manufacturer’s lead times to meet your production schedule. Customer Support: Evaluate the manufacturer’s responsiveness and willingness to assist with technical inquiries and troubleshooting. Requesting Samples and Testing To make an informed decision, request samples of cartridge heaters from potential manufacturers. Performance Testing: Conduct thorough tests under your specific operating conditions. Compatibility Check: Verify compatibility with your equipment and processes. Longevity Evaluation: Assess the heater’s durability and lifespan. Compare Performance: Compare the performance of different samples to identify the best option. Considering Cost and Value While cost is a factor, it’s essential to balance it with quality and long-term performance. Total Cost of Ownership: Consider factors beyond the initial purchase price, such as energy efficiency, maintenance costs, and heater lifespan. Value Proposition: Evaluate the overall value offered by the manufacturer, including product quality, customer support, and warranty. Cost-Benefit Analysis: Compare the cost of different options against the expected benefits. Building a Strong Partnership The relationship with your cartridge heater manufacturer is crucial for long-term success. Communication: Maintain open and clear communication with the manufacturer. Collaboration: Work together to find solutions to challenges and optimize heater performance. Trust and Reliability: Choose a manufacturer you can trust to deliver consistent quality and meet your needs. Wrap Up By following these guidelines and conducting thorough research, you can confidently select the right cartridge heater manufacturer to meet your specific requirements and drive your business success.
3 Reasons Why a Mica Band Heater Boosts Efficiency in Your Projects
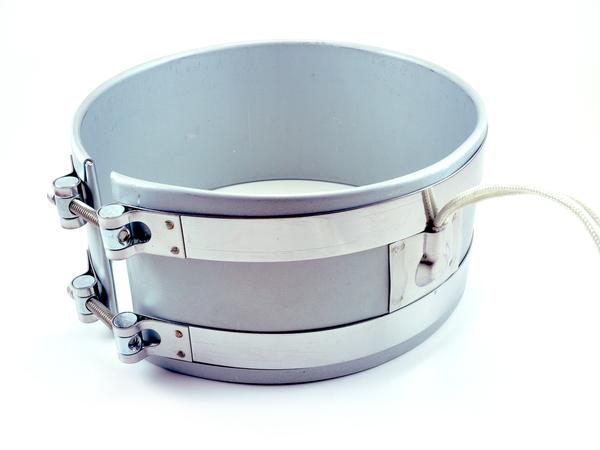
Imagine needing to heat a pipe for a specific task. You could use a bulky heating element that wastes energy and heats the surrounding air. But what if there was a better way? Enter the mica band heater: a thin, flexible heating solution that delivers targeted heat precisely where you need it, boosting efficiency in various applications. This blog post explores 3 key reasons why a mica band heater can significantly improve the efficiency of your heating projects: Excellent Heat Transfer for Focused Heating: Efficient Conductor: Mica band heaters use mica, a naturally occurring mineral with exceptional thermal conductivity. This means the heat generated by the internal resistance wire travels quickly and efficiently to the outer surface of the heater. Targeted Heating: Unlike bulky heating elements that radiate heat in all directions, mica band heaters conform to the shape of the object being heated. This minimizes wasted heat loss and ensures the desired temperature is reached quickly and precisely. Here’s a table summarizing the benefits of an excellent heat transfer in mica band heater: Superior Insulation for Minimized Heat Loss: Mica’s Insulating Properties: The mica layer in a mica band heater acts as a natural insulator. This traps heat within the element, preventing it from escaping to the surrounding environment. Reduced Ambient Heating: By minimizing heat loss, mica band heaters reduce the overall temperature in your workspace. This creates a more comfortable working environment and can even help lower your air conditioning costs. Here’s a table summarizing the benefits of a superior insulation in mica band heater: Durable Design for Long-Lasting Performance: Mica’s Strength and Stability: Mica is a naturally robust material that can withstand high temperatures and harsh environments. This translates to a longer lifespan for your mica band heater, reducing the need for frequent replacements. Flexible Construction: The mica band heater’s flexible design allows it to conform to various shapes and sizes. This versatility makes it suitable for a wider range of applications compared to rigid heating elements. Choosing the Right Mica Band Heater for Your Needs: With so many benefits, it’s easy to see why mica band heaters are a popular choice for various industrial and commercial heating applications. When selecting a mica band heater, consider these factors: Wattage: Choose a heater with enough wattage to reach and maintain the desired temperature for your specific application. Size: Ensure the heater size fits the circumference of the object you’re heating. Voltage: Select a heater compatible with your electrical system’s voltage. Terminations: Choose the appropriate terminal type (screw terminals, lead wires, etc.) for easy installation. Wrap Up Mica band heaters offer a powerful combination of targeted heating, excellent insulation, and a durable design. These key features translate to significant efficiency gains in various applications. If you’re looking for a precise and energy-saving heating solution, consider incorporating mica band heaters into your next project!