How Cartridge Heaters Can Optimize Your Manufacturing Process
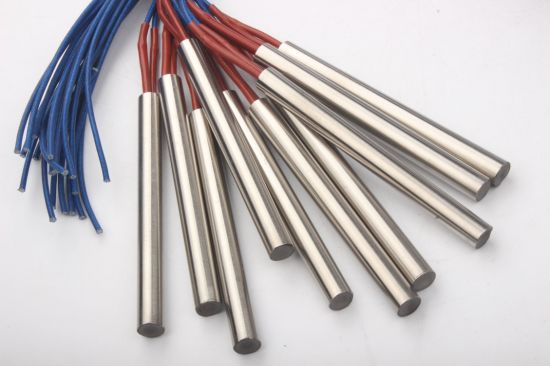
Imagine a world where heating elements are precise, efficient, and adaptable to various manufacturing needs. This isn’t science fiction! A cartridge heater manufacturer offers a solution: compact, versatile heating elements called cartridge heaters. These powerful tools can significantly optimize your manufacturing process by delivering precise and controlled heat exactly where it’s needed. In this guide, we’ll explore how cartridge heaters can revolutionize your production line, boosting efficiency, improving product quality, and reducing costs. What are Cartridge Heaters? Cartridge heaters are cylindrical-shaped heating elements designed for direct insertion into machinery or equipment. They consist of a metal sheath containing a high-resistance wire coil and insulating magnesium oxide. When electricity passes through the coil, it generates heat that transfers directly to the surrounding object. Benefits of Using Cartridge Heaters in Manufacturing: Precise Heat Control: Cartridge heaters offer exceptional temperature control due to their close contact with the target object. This ensures consistent and even heating, crucial for many manufacturing processes. Fast Heating and Cooling: The compact design of cartridge heaters allows for rapid heating and cooling cycles. This minimizes downtime between cycles and improves overall production efficiency. High-Watt Densities: Cartridge heaters pack a punch! They can generate high heat outputs despite their small size, making them ideal for various applications requiring concentrated heat. Durability and Versatility: Cartridge heaters are built to withstand harsh industrial environments. They come in various sheath materials, diameters, and lengths to meet diverse manufacturing needs. Long Service Life: The robust design and high-quality materials ensure a long lifespan for cartridge heaters, minimizing replacement costs and downtime. Easy Installation and Maintenance: Cartridge heaters are simple to install and require minimal maintenance. This reduces production setup time and ongoing maintenance costs. Applications of Cartridge Heaters in Manufacturing: Cartridge heaters have a wide range of applications across various manufacturing industries. Here are some examples: Plastic Processing: Used for melting and molding plastics in processes like injection molding, thermoforming, and heat sealing. Food and Beverage Industry: Heating food processing equipment, sterilizing containers, and maintaining specific temperatures during food production. Packaging Industry: Sealing packages, activating adhesives, and maintaining consistent temperatures for heat-shrink wrapping. Textile Manufacturing: Drying fabrics, activating dyes, and heat-setting textiles for wrinkle resistance. Electronics Manufacturing: Soldering components, curing adhesives, and maintaining precise temperatures for delicate electronic components. Medical Device Manufacturing: Sterilizing equipment, heating components during assembly, and maintaining specific temperatures for medical device production. Choosing the Right Cartridge Heater Manufacturer: With so many cartridge heater manufacturers on the market, selecting the right partner is crucial. Here are some factors to consider: Experience and Expertise: Choose a manufacturer with a proven track record and extensive experience in your specific industry. Product Quality and Certifications: Look for a manufacturer that prioritizes quality materials and adheres to relevant industry standards and certifications. Customizability Options: Many manufacturers offer custom cartridge heaters to meet your specific needs. Choose one that can accommodate your unique requirements. Customer Service and Support: Reliable customer service and technical support are essential for troubleshooting and ensuring smooth operation. Optimizing Your Manufacturing Process with Cartridge Heaters By incorporating cartridge heaters into your manufacturing process, you can achieve significant benefits: Improved Product Quality: Precise heat control ensures consistent product quality, reducing rejects and rework. Enhanced Production Efficiency: Faster heating and cooling cycles minimize downtime and increase production output. Reduced Energy Consumption: The efficient design of cartridge heaters minimizes energy waste, lowering your operating costs. Minimized Downtime: Durable construction and easy maintenance reduce equipment failures and downtime. Wrap Up Cartridge heaters are a powerful tool for any manufacturer seeking to optimize their production process. Their versatility, efficiency, and precise heat control can significantly improve product quality, boost production output, and ultimately, contribute to your business success. So, consider partnering with a reputable cartridge heater manufacturer and explore how these innovative heating elements can revolutionize your manufacturing line!
5 Things to Look for When Choosing a Reputable Heating Element Manufacturer
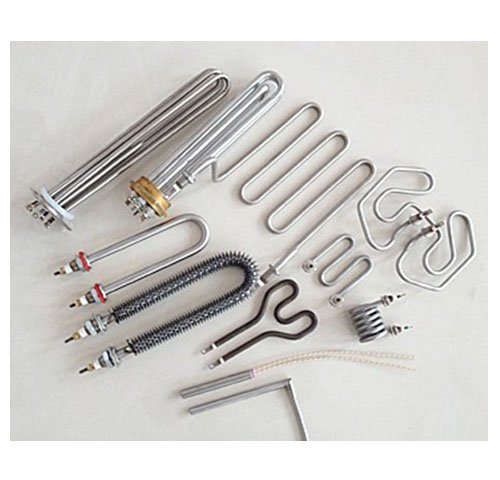
Selecting the right heating element manufacturer is crucial for any project that relies on heat, from household appliances to industrial machinery. A dependable manufacturer ensures quality, safety, and performance for your heating needs. But with numerous options available, how do you choose the best one? Here are 5 key factors to consider when selecting a reputable heating element manufacturer: Experience and Expertise: A manufacturer’s experience and expertise directly impact the quality and reliability of their heating elements. Look for companies with a proven track record in your industry. Here’s what to consider: Years in Business: Companies with a long history demonstrate their ability to adapt and thrive in the market. Industry Specialization: Look for manufacturers with experience in your specific industry. They understand the unique heating requirements of your application. Customer Testimonials and Reviews: Read online reviews and testimonials to see what other customers say about the manufacturer’s expertise and product quality. Product Quality and Certifications: Heating elements operate under high temperatures and pressures. Quality materials, construction, and safety certifications are essential. Consider these aspects: Material Selection: Ensure the manufacturer uses high-quality materials suitable for your application’s temperature range and environment. Manufacturing Processes: Look for companies that employ advanced manufacturing techniques and rigorous quality control procedures. Safety Certifications: Choose a manufacturer whose heating elements comply with relevant safety standards for your region. Common certifications include UL (Underwriters Laboratories) and CSA (Canadian Standards Association). Customization and Engineering Capabilities Not all heating element applications are one-size-fits-all. The ability to customize elements for specific needs is a valuable asset: Custom Design Options: Does the manufacturer offer custom design services to cater to your unique heating requirements? Engineering Support: Look for companies with a team of engineers who can assist with technical questions, application recommendations, and even co-development of new heating element designs. Variety of Heating Element Types: The manufacturer should offer a diverse selection of heating element types to suit your project’s needs, such as cartridge heaters, tubular heaters, immersion heaters, or band heaters. Customer Service and Support Excellent customer service is essential throughout the buying process and beyond. Here’s what to look for: Responsiveness: Does the manufacturer have a dedicated customer service team that responds promptly to inquiries? Technical Support: Is there access to technical support personnel who can answer your questions about product selection, installation, and troubleshooting? Warranty and After-Sales Service: A strong warranty demonstrates the manufacturer’s confidence in their product quality. Look for clear warranty terms and readily available after-sales support. Competitive Pricing and Lead Times Finding a balance between cost and quality is important. Consider these factors: Price Transparency: Does the manufacturer provide clear pricing information or quotes based on your project specifications? Competitive Pricing: Compare prices from several reputable manufacturers to ensure you’re getting a fair deal. Lead Times: Understand the manufacturer’s production lead times to ensure they align with your project timeline. Making an Informed Decision By carefully considering these 5 factors, you can make an informed decision when choosing a reputable heating element manufacturer. Remember, a reliable manufacturer becomes a valuable partner in your project’s success, providing quality heating elements that meet your specific needs and ensure long-lasting performance.
5 Things to Consider When Choosing the Right Mica Band Heater for Your Application
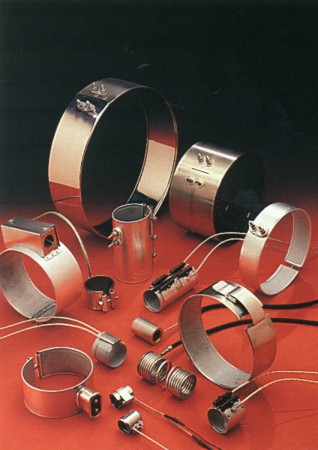
Mica band heaters are versatile and reliable heating elements used in various industrial processes. They efficiently transfer heat to cylindrical objects by wrapping around them like a band. Choosing the right mica band heater for your application is crucial for optimal performance and safety. Here are 5 key factors to consider: Size and Wattage: Diameter and Length: Measure the diameter and length of the object you want to heat. Mica band heaters come in various sizes to ensure proper fit and even heat distribution. Wattage and Heating Requirements: Consider the desired heating speed and temperature range for your application. Higher-wattage heaters generate more heat faster, while lower-wattage options provide gentler heating. Termination Styles: Mica band heaters offer different termination styles for electrical connection: Lead Wire Terminations: These heaters have exposed lead wires for connection to a terminal block or control panel. They are simple to install but require proper wiring expertise. Terminal Box Terminations: These heaters come with a built-in terminal box for secure and protected electrical connections. They offer a safer and more finished look. Plug and Play Options: Some mica band heaters come with pre-wired plugs for easy connection to a standard power outlet. This is ideal for low-voltage applications that don’t require complex controls. Material and Construction: Heating Element: Most mica band heaters use a nickel-chromium resistance wire for heating. This material offers durability, high-temperature resistance, and efficient heat generation. Insulation: Mica, a naturally occurring mineral, is a common insulator in mica band heaters. It provides excellent heat resistance and electrical insulation. Outer Shell: The outer shell protects the heating element and insulation. Stainless steel is a popular choice for its durability and resistance to corrosion. Temperature Control: Thermocouple Compatibility: Some mica band heaters come with built-in thermocouples for temperature sensing. Ensure your heater and control system are compatible for accurate temperature monitoring. External Controllers: For precise temperature control, consider using an external temperature controller with your mica band heater. This allows for setting and maintaining specific target temperatures. Application Considerations: Environment: Think about the environment where you’ll use the heater. For harsh environments with moisture or chemicals, consider options with special coatings or enclosures for added protection. Safety Features: Some mica band heaters offer built-in safety features like thermostats or fuses to prevent overheating. These features are crucial for applications requiring precise temperature control or using flammable materials. Additional Features: Multiple Heat Zones: Certain mica band heaters have multiple heating zones for controlled heating of different sections of a cylindrical object. Customizable Options: Many manufacturers offer a custom mica band heater tailored to specific size, wattage, and termination requirements. Wrap Up By considering these 5 factors, you can select the ideal mica band heater for your application. Remember, consulting with a reputable mica band heater supplier can provide valuable guidance and ensure you get the right heater for your needs. They can answer your questions, recommend suitable options, and even offer custom solutions if needed.
3 Key Benefits of Using a Ceramic Band Heater Over Traditional Heating Elements
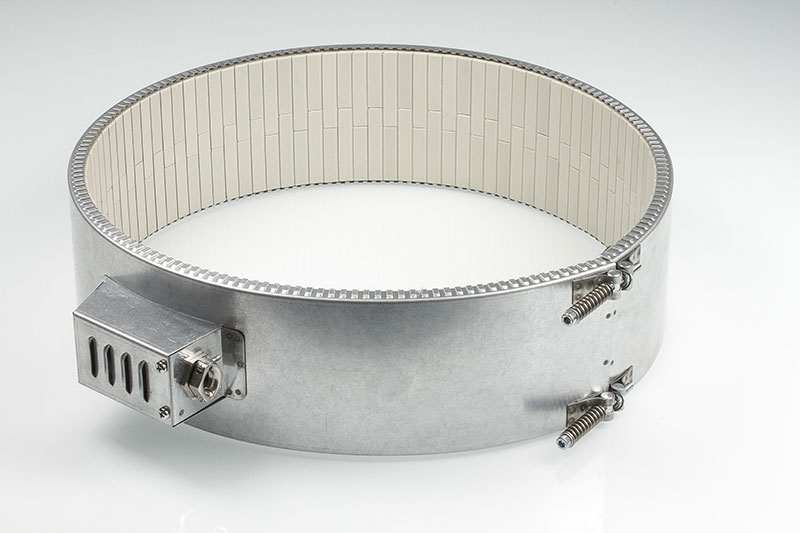
A ceramic band heater is rapidly becoming the go-to choice for a wide range of industrial heating applications. These versatile heating elements offer several advantages over traditional methods like open flame heating or radiant heaters. If you’re looking for a more efficient, reliable, and uniform heating solution, then ceramic band heaters might be the perfect fit for your needs. Let’s explore the top 3 benefits of using a quality ceramic band heater: Superior Heat Transfer and Efficiency: Even Heat Distribution: Ceramic band heaters are designed to wrap around pipes, tubes, or vessels, providing 360-degree heat distribution. This ensures a consistent and uniform heating process, eliminating hot spots and cold zones commonly found with other methods. Reduced Energy Consumption: The efficient design of ceramic band heaters minimizes heat loss to the surrounding environment. This translates to lower energy consumption and cost savings on your heating operations. Fast Heating Up Times: Ceramic band heaters have excellent thermal conductivity, allowing them to reach desired temperatures quickly. This minimizes downtime and improves overall production efficiency. Here’s a table summarizing the efficiency benefits of ceramic band heaters: Benefit Description Even Heat Distribution 360-degree heating eliminates hot spots and cold zones. Reduced Energy Consumption Minimizes heat loss for lower energy costs. Fast Heating Up Times Reaches desired temperatures quickly for improved efficiency. Exceptional Durability and Long Lifespan: High-Temperature Resistance: Every ceramic band heater is built with robust ceramic material that can withstand high operating temperatures. This makes them ideal for a variety of industrial applications involving hot melts, adhesives, or other heat-intensive processes. Chemical Resistance: The ceramic material in these heaters is resistant to many chemicals and solvents commonly encountered in industrial settings. This reduces the risk of damage or corrosion, extending the lifespan of the heater. Rugged Construction: Ceramic band heaters are built to last. The sturdy construction can handle demanding industrial environments and frequent heating cycles. Here’s a table summarizing the durability benefits of a ceramic band heater: Benefit Description High-Temperature Resistance Withstands high operating temperatures for various applications. Chemical Resistance Resists chemicals and solvents commonly found in industrial settings. Rugged Construction Built to last for demanding industrial environments and frequent use. Precise Temperature Control and Versatility: Integrated Thermocouples: Many ceramic band heaters come equipped with built-in thermocouples. These sensors allow for precise temperature control and monitoring, ensuring consistent and accurate heating processes. Wide Range of Sizes and Wattages: Ceramic band heaters come in a variety of sizes and wattages to accommodate a wide range of heating requirements. You can find the perfect heater size and power output for your specific application. Easy Installation and Maintenance: Ceramic band heaters are typically easy to install and maintain. Their flexible design allows for them to be wrapped around objects of various shapes and sizes. Additionally, the robust construction minimizes the need for frequent replacements. Here’s a table summarizing the versatility benefits of a ceramic band heater: Benefit Description Integrated Thermocouples Allows for precise temperature control and monitoring. Wide Range of Sizes and Wattages Accommodates various heating requirements for different applications. Easy Installation and Maintenance Simple installation and minimal maintenance needs. Last Word If you’re looking for a reliable heating solution for your industrial applications, then a quality ceramic band heater is worth considering. Its superior heat transfer, exceptional durability, and precise temperature control make it a valuable asset for various industries.
5 Benefits of Using Silicone Fiberglass Cable in High-Temperature Applications
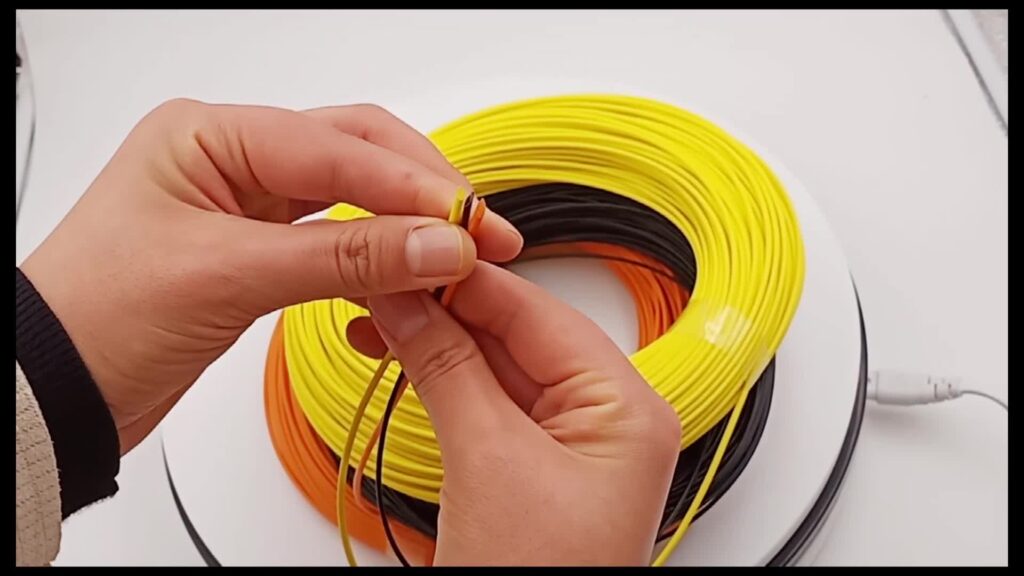
Silicone fiberglass cable is becoming increasingly popular for applications that deal with extreme heat. Unlike traditional cable insulation materials that melt or become brittle at high temperatures, silicone fiberglass cables offer exceptional heat resistance, making them a reliable and safe choice for various demanding environments. Let’s explore the five key benefits of using a silicone fiberglass cable in high-temperature applications: Exceptional Heat Resistance: The primary advantage of silicone fiberglass cables is their ability to withstand scorching temperatures. Here’s a breakdown: Silicone Rubber Insulation: Silicone rubber, the core insulator in these cables, boasts remarkable thermal stability. It can continuously operate at temperatures ranging from -60°C (-76°F) to a staggering +200°C (+392°F). Fiberglass Braid: The additional layer of fiberglass braid further enhances heat resistance. Fiberglass inherently possesses excellent thermal insulation properties. This exceptional heat tolerance makes silicone fiberglass cables ideal for various high-temperature applications, including: Industrial Ovens and Furnaces: These cables can withstand the intense heat generated by industrial ovens and furnaces, ensuring reliable power delivery to control systems and monitoring equipment. Power Generation: In power plants, silicone fiberglass cables can be used for critical connections near boilers, turbines, and other heat-generating machinery. Welding Equipment: These cables can handle the high heat associated with welding processes, providing safe and reliable power for welding tools. Superior Flame Retardance: Safety is paramount, especially when dealing with high temperatures. Silicone fiberglass cables excel in this area: Self-Extinguishing: Silicone rubber is a self-extinguishing material. This means it won’t continue burning once the source of ignition is removed, minimizing fire risks. Low Smoke Emission: In the unlikely event of a fire, silicone fiberglass cables generate minimal smoke, improving visibility and reducing the risk of inhalation hazards. These flame-retardant properties make silicone fiberglass cables perfect for applications where fire safety is crucial, such as: Aerospace and Defense Industries: These cables are used in aircraft and military equipment due to their ability to withstand extreme temperatures and minimize fire risks. Mass Transit Systems: In trains, buses, and other mass transit vehicles, silicone fiberglass cables can be used for critical electrical connections where fire safety is a top priority. Building Construction: These cables can be used in high-rise buildings and other structures with stringent fire safety regulations. Enhanced Flexibility and Durability: Silicone fiberglass cables offer a winning combination of flexibility and resilience: Silicone Rubber: Silicone rubber is known for its elasticity, allowing for easy cable routing and installation, even in tight spaces. This flexibility is maintained even at high temperatures. Fiberglass Braid: While offering heat resistance, the fiberglass braid also provides structural reinforcement, making the cable more resistant to wear and tear. This unique blend of flexibility and durability makes silicone fiberglass cables well-suited for: Robotics and Automation: The flexibility allows for easy integration into robotic arms and automated machinery that move in various directions. Medical Equipment: These cables can be used in medical devices that require movement and manipulation without compromising performance or safety. Harsh Environments: The durability of these cables makes them suitable for harsh environments with exposure to dust, moisture, and vibrations. Chemical Resistance: Many high-temperature environments also involve exposure to harsh chemicals. Silicone fiberglass cables can handle these challenges: Silicone Rubber: Silicone rubber exhibits excellent resistance to a wide range of chemicals, including oils, solvents, and acids. This resistance prevents cable degradation and ensures reliable performance. This chemical resistance makes silicone fiberglass cables a great choice for: Chemical Processing Plants: These cables can be used for control systems and equipment monitoring in chemical plants where exposure to various chemicals is a constant factor. Oil and Gas Industry: In refineries and other oil and gas facilities, silicone fiberglass cables can withstand exposure to oils and other chemicals without degrading. Food Processing Facilities: The chemical resistance makes these cables suitable for use near food processing equipment where hygiene and sanitation are paramount. Long Service Life: Silicone fiberglass cables are built to last: Heat and Flame Resistance: The exceptional heat and flame resistance of these cables contribute to a longer lifespan. They can withstand high temperatures and harsh environments without degrading quickly. Durability and Chemical Resistance: The durability and chemical resistance properties further extend the service life of these cables. They can endure wear and tear, chemical exposure, and maintain reliable performance for extended periods.
5 Applications of an RTD Sensor in Industrial Temperature Measurement
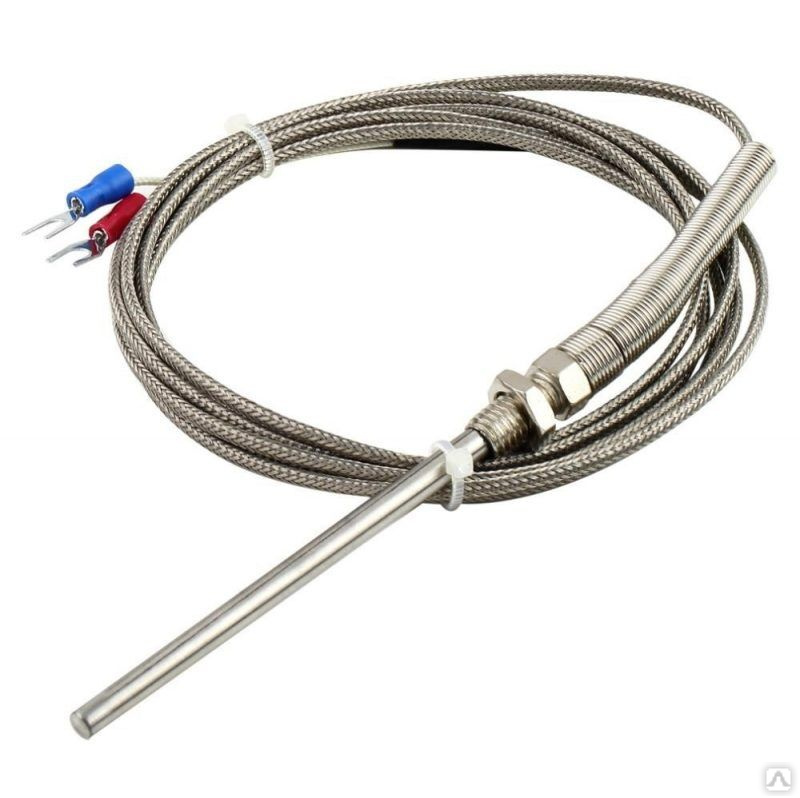
RTD sensor (Resistance Temperature Detector) is a workhorse in the world of industrial temperature measurement. These reliable and accurate sensors play a vital role in various industrial processes, ensuring smooth operation and product quality. But how exactly are RTD sensors used? Let’s explore five key applications of an industrial RTD sensor: Oil and Gas Industry: Accurate Monitoring in Refineries: RTD sensors are crucial in oil refineries, monitoring temperatures throughout the refining process. From crude oil distillation to product storage, precise temperature control is essential for safety, efficiency, and product quality. Pipeline Temperature Monitoring: An RTD sensor ensures the safe and efficient transportation of oil and gas products by monitoring pipeline temperatures. This helps prevent leaks, explosions, and product degradation during transportation. Chemical and Pharmaceutical Manufacturing: Reaction Vessel Temperature Control: Chemical reactions are often highly sensitive to temperature. RTD sensors provide accurate temperature readings in reaction vessels, ensuring precise control and consistent product quality. Maintaining Sterile Environments: In pharmaceutical manufacturing, maintaining sterile environments is critical. RTD sensors monitor temperatures in sterilization chambers and cleanrooms, ensuring they reach and maintain the required levels for effective sterilization. Power Generation: Optimizing Power Plant Efficiency: RTD sensor plays a vital role in power plants by monitoring temperatures in boilers, turbines, and other critical equipment. This data helps ensure optimal efficiency and prevent equipment failure. Combustion Control: For efficient and clean power generation, precise control of combustion temperatures is essential. RTD sensors provide real-time temperature data in the combustion chamber, allowing operators to optimize fuel burning and minimize emissions. Food and Beverage Production: Ensuring Food Safety: Maintaining proper temperatures during food processing is crucial for safety and preventing spoilage. RTD sensors monitor temperatures in ovens, freezers, pasteurizers, and other food processing equipment. Maintaining Product Quality: Temperature control plays a significant role in maintaining the taste, texture, and overall quality of food and beverage products. RTD sensors help ensure consistent temperatures throughout production processes. Building Automation and HVAC Systems: Maintaining Comfortable Building Temperatures: RTD sensors are used in thermostats and building automation systems to monitor and regulate indoor air temperature. This ensures a comfortable environment for occupants while optimizing energy consumption. Process Cooling in Industrial Settings: Many industrial processes generate significant heat. RTD sensors monitor temperatures in cooling systems like chillers and air conditioning units, ensuring they function properly and maintain optimal operating temperatures. Benefits of Using RTD Sensors: High Accuracy: RTD sensors offer excellent accuracy over a wide temperature range, making them reliable for critical industrial applications. Wide Range of Options: RTD sensors come in various configurations and materials to suit diverse temperature measurement needs in different industrial settings. Stable Performance: RTD sensors exhibit stable performance over time, ensuring consistent and reliable temperature readings. Durable Construction: Industrial-grade RTD sensors are built to withstand harsh environments and demanding industrial applications. Relatively Simple Design: The basic design of RTD sensors makes them relatively easy to install, maintain, and calibrate. Wrap Up RTD sensor is a versatile and valuable tool for industrial temperature measurement. Its combination of accuracy, reliability, and durability makes it a preferred choice for various applications across diverse industries. By understanding different applications and choosing the right RTD sensor, you can ensure precise temperature control, optimize processes, and achieve consistent product quality in your industrial setting.
5 Essential Things to Know Before Installing MI Heating Cables
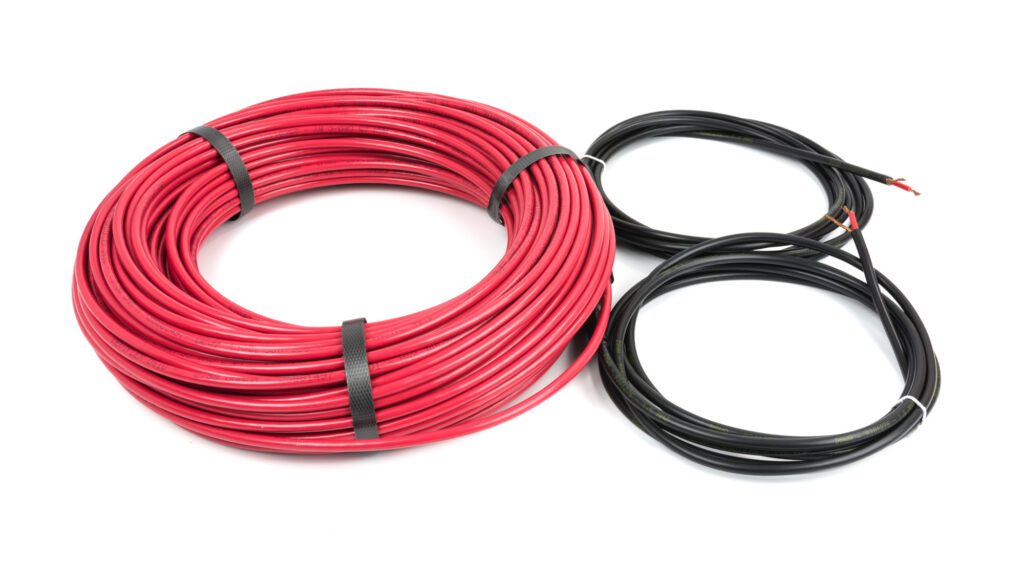
MI heating cables, also known as mineral-insulated heating cables, are a reliable and efficient way to prevent freezing and maintain consistent temperatures in pipes and vessels. But before you install one yourself, it’s crucial to understand these cables and the process. Here are 5 essential things to know before installing MI heating cables: Understanding MI Heating Cable Basics: Construction: MI heating cables consist of a heating element encased in a mineral insulation layer, all protected by a durable metallic sheath. This design ensures safe and efficient heat distribution while withstanding harsh environments. Applications: MI heating cables are commonly used in residential and commercial settings to prevent freezing in pipes carrying water, oils, or other liquids. They can also maintain desired temperatures in vessels for process control applications. Safety Features: MI heating cables come with built-in grounding conductors and are often flame-retardant, providing additional safety during operation. Choosing the Right MI Heating Cable: Selecting the right MI heating cable depends on several factors: Pipe Size and Material: MI heating cables come in various diameters to fit snugly around different pipe sizes. The cable’s wattage (heat output) also needs to be sufficient for your pipe material (metal pipes require higher wattage than plastic). Application Temperature: Consider the desired temperature you want to maintain in your pipes or vessel. Choose a cable with enough wattage to reach and maintain that temperature effectively. Length Requirements: Measure the length of the pipe or vessel needing heating to determine the required cable length. Remember to factor in some extra length for connection purposes. Regulatory Requirements: In some regions, specific approvals or certifications might be necessary for MI heating cables used in certain applications. Check with local building codes or consult a qualified electrician for guidance. Planning and Preparation for Installation: Proper planning is key for a successful and safe MI heating cable installation: Turn Off Power: Always turn off the power supply to the affected pipes or equipment before starting the installation process. Clear the Work Area: Clear the workspace around the pipes to allow for easy cable placement and connection. Gather Tools and Materials: Have all the necessary tools and materials on hand, including the MI heating cable, cable ties, insulation tape, thermostat (if needed), and appropriate cutting tools. Read and Understand Instructions: Carefully read and understand the manufacturer’s instructions for your specific MI heating cable model. This ensures proper installation and safe operation. Installation Tips and Techniques: Here are some key points to remember during MI heating cable installation: Maintain Minimum Bending Radius: Avoid bending the cable too sharply. Respect the minimum bending radius specified by the manufacturer to prevent damage to the internal heating element. Secure the Cable Properly: Use cable ties or straps to securely fasten the MI heating cable along the pipe or vessel at regular intervals. Ensure a snug fit but avoid over-tightening. Terminate the Cable Ends: MI heating cables require proper termination at both ends for connection to a power source and thermostat (if used). Consult a qualified electrician if unsure about cable termination techniques. Insulate the System: After installing the cable, apply appropriate thermal insulation around the pipes or vessel to minimize heat loss and improve energy efficiency. Safety Precautions and Considerations: Safety is paramount when working with electrical components like MI heating cables: Leave Electrical Work to Professionals: If you’re uncomfortable with electrical work, consider hiring a licensed electrician for installation. They have the expertise and experience for safe and proper cable installation. Double-Check Connections: Before turning on the power, double-check all electrical connections to ensure they are secure and made according to the manufacturer’s instructions. Grounded System: Ensure the MI heating cable system is properly grounded to prevent electrical hazards. Consult an electrician for grounding requirements if needed. Test and Maintain: Once installed, test the MI heating cable system to verify its functionality. Regularly inspect the cable and connections for any signs of damage and perform maintenance as the manufacturer recommends. Wrap Up By understanding these essential points, you can approach your MI heating cable installation project with confidence. Remember, consulting a qualified electrician is always the safest and most reliable option for complex installations or if you lack electrical expertise. They can ensure a professional installation that meets all safety standards and code requirements.
What is a Thermocouple – A Short Guide
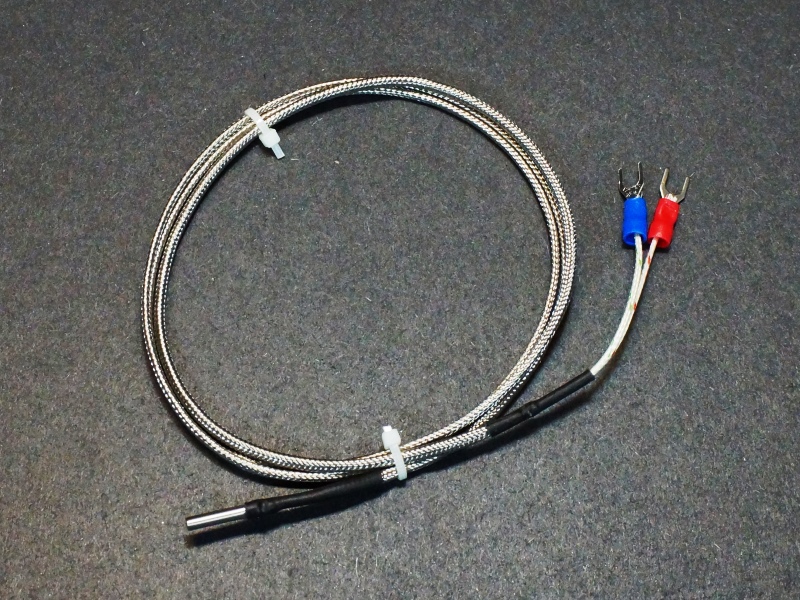
In the world of temperature measurement, thermocouples reign supreme. These simple yet powerful devices are the unsung heroes of countless industries. Thermocouples quietly keep things running smoothly from steel production to your home oven. Let’s dive into the fascinating world of thermocouples and explore their inner workings. Understanding Thermocouples At its core, a thermocouple is an elegantly simple device. It consists of two different metal wires joined at one end. This junction creates a small electrical voltage when exposed to temperature changes. Thermocouple manufacturers have honed this principle into a precise science. Types of Thermocouples Every thermocouple manufacturer produces a variety of types, each suited for specific applications. The most common types include: Type K: The workhorse of the thermocouple world, suitable for a wide range of applications Type J: Ideal for reducing atmospheres and vacuum applications Type T: Excellent for low-temperature and cryogenic applications Type E: High sensitivity makes it perfect for low-temperature measurements Type N: Superior stability in high-temperature oxidizing environments Types R and S: Platinum-based thermocouples for high-temperature precision measurements Type B: Another platinum-based type for extremely high temperatures How Thermocouples Work Thermocouple manufacturers design these devices to operate on a simple yet ingenious principle. When the junction of two dissimilar metals is heated, it generates a small voltage. This voltage increases as the temperature rises, following a predictable curve. The Measurement Process The thermocouple junction is exposed to the temperature to be measured The temperature difference creates a small voltage (typically millivolts) This voltage is measured and converted to a temperature reading Compensation is applied for the reference junction (usually at room temperature) Applications of Thermocouples The versatility of thermocouples makes them indispensable in numerous industries. Thermocouple manufacturers produce sensors for a wide range of applications, including: Industrial Processes: Monitoring temperatures in furnaces, kilns, and reactors Automotive: Engine management systems and exhaust gas temperature measurement Aerospace: Jet engine monitoring and spacecraft thermal management Food and Beverage: Ensuring proper cooking and storage temperatures HVAC: Controlling heating and cooling systems in buildings Medical Equipment: Monitoring sterilization processes and patient temperatures Scientific Research: Precise temperature control in laboratories Advantages of a Thermocouple Thermocouple manufacturers highlight several key benefits that make their products indispensable: Wide Temperature Range: Some types can measure from -270°C to over 2300°C Durability: Rugged construction suitable for harsh industrial environments Fast Response: Quick reaction to temperature changes Simplicity: No power supply is required at the measuring point Cost-Effective: Relatively inexpensive compared to other temperature sensors Versatility: Available in various sizes and configurations for different applications The Future of Thermocouple Technology Thermocouple manufacturers continue to innovate, pushing the boundaries of what’s possible. Some emerging trends include: Smart Thermocouples: Integrated electronics for improved accuracy and diagnostics Nanotechnology: Exploring new materials and structures for enhanced performance Wireless Thermocouples: Eliminating the need for physical connections in some applications Advanced Alloys: Developing new metal combinations for extreme environments Integrated Systems: Combining thermocouples with other sensors for comprehensive monitoring Wrap Up Despite its simplicity, a thermocouple remains essential in modern industry and research. Their wide range, durability, and cost-effectiveness make them invaluable in countless applications. As technology advances, thermocouple manufacturers continue to refine and improve these versatile sensors. Whether you’re monitoring an industrial furnace or ensuring your turkey is perfectly cooked, a thermocouple is likely quietly doing its job. Understanding the principles behind these devices can help you appreciate their importance and select the right sensor for your needs.
What is a Finned Tubular Heater: A Comprehensive Guide
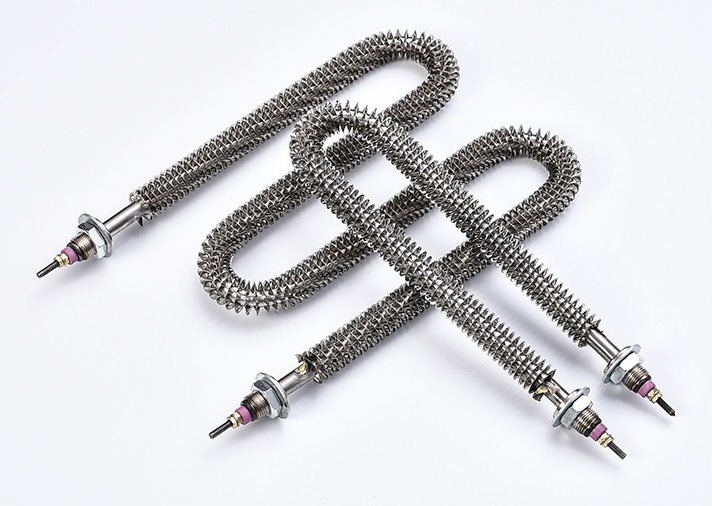
Heating technology has advanced greatly in recent years. One of the most efficient and versatile options available today is the finned tubular heater. This innovative heating solution combines the best of both worlds: the reliability of traditional tubular heaters and the enhanced heat transfer of finned designs. Let’s explore a finned tubular heater’s features, benefits, and applications. Basics of a Finned Tubular Heater Finned tubular heaters are a type of electric heating element. They consist of a metal tube with external fins attached to its surface. The core of the heater houses a heating element. This element generates heat when electricity passes through it. The fins on the exterior serve a crucial purpose. They increase the surface area for heat dissipation. Key Components of a Finned Tubular Heater Metal Tube: Usually made of stainless steel or copper Heating Element: Typically, a resistive wire Fins: Attached to the exterior of the tube Insulation: Surrounds the heating element inside the tube Terminal Connections: For electrical power input How Finned Tubular Heaters Work The operation of a finned tubular heater is straightforward yet ingenious. When electrical current flows through the heating element, it generates heat. This heat is then transferred to the metal tube. The fins attached to the tube’s exterior play a crucial role. They significantly increase the surface area available for heat dissipation. Advantages of a Finned Tubular Heater Finned tubular heaters offer several advantages over other heating solutions. Their unique design contributes to their popularity across various industries. Let’s explore some of these benefits: Increased Efficiency: The finned design allows for better heat transfer. Compact Size: Despite their high output, these heaters are relatively compact. Versatility: They can be used in air, liquid, and solid applications. Durability: The robust construction ensures a long operational life. Cost-Effective: Higher efficiency leads to lower energy costs over time. Easy Maintenance: Simple design makes cleaning and maintenance straightforward. Customizable: Can be tailored to specific heating requirements. These advantages make finned tubular heaters a popular choice in many heating applications. They offer a balance of performance, efficiency, and cost-effectiveness. Applications of a Finned Tubular Heater The versatility of finned tubular heaters makes them suitable for various applications. They are used across various industries and settings. Here are some common applications: Industrial Applications Process Heating: Used in manufacturing processes requiring precise temperature control Food Processing: For heating ovens, fryers, and other food preparation equipment Chemical Processing: In reactors and vessels requiring controlled heating Plastics Industry: For heating molds and extruders HVAC Applications Air Duct Heating: For warming the air in ventilation systems Frost Prevention: Used in refrigeration systems to prevent frost buildup Space Heating: In large industrial or commercial spaces Other Applications Automotive: In engine block heaters and defrosting systems Marine: For heating systems on ships and offshore platforms Agriculture: In greenhouse heating and animal husbandry The wide range of applications demonstrates the versatility and effectiveness of finned tubular heaters. They can be adapted to meet specific heating needs across diverse industries. Future Trends in Finned Tubular Heater Technology The world of heating technology is constantly evolving. Finned tubular heaters are no exception. Here are some trends to watch: Smart Controls: Integration with IoT for remote monitoring and control Advanced Materials: Development of more efficient and durable materials Improved Fin Designs: Research into optimal fin shapes for even better heat transfer Hybrid Systems: Combination with other heating technologies for enhanced performance Miniaturization: Smaller, more compact designs for specialized applications These advancements promise to make finned tubular heaters even more efficient and versatile. Wrap Up As we look to the future, finned tubular heaters will likely play an increasingly important role in heating solutions. Their adaptability to various industries and applications makes them a valuable tool in our quest for efficient and effective heating. Whether you’re considering a finned tubular heater for your industrial process or any other application, it’s clear that these innovative heaters offer significant benefits. Their combination of performance, efficiency, and cost-effectiveness makes them a smart choice for many heating needs.
What is a Cartridge Heater: A Comprehensive Guide
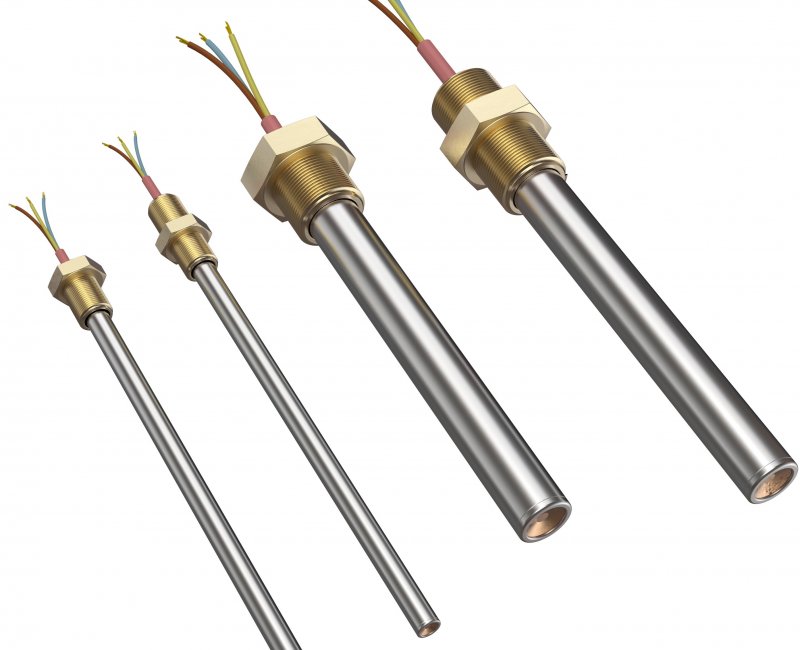
Heating solutions come in various forms, but few are as versatile and efficient as a cartridge heater. These compact powerhouses of heat generation have revolutionized countless industries. Cartridge heaters are crucial in maintaining precise temperatures from manufacturing to food processing. Let’s explore the world of a cartridge heater and its features, applications, and benefits. Understanding Cartridge Heaters Cartridge heaters are cylindrical heating elements designed for insertion into drilled holes or cavities. They provide localized heating in a variety of industrial and commercial applications and are known for their high watt density and ability to transfer heat efficiently. Key Components of a Cartridge Heater Heating Element: Typically made of nickel-chromium resistance wire Insulation: Usually magnesium oxide (MgO) for excellent heat transfer Sheath: Outer metal casing, often stainless steel or Incoloy Lead Wires: For connecting to a power source End Seal: Protects internal components from moisture and contaminants Cartridge heaters are designed to maximize heat transfer while maintaining durability. Their construction allows for efficient heating in confined spaces. How Cartridge Heaters Work The operation of a cartridge heater is based on simple yet effective principles. When an electrical current passes through the resistance wire, it generates heat, which is then transferred through the insulation to the outer sheath. Heat Transfer Process Electrical energy converts to heat in the resistance wire Heat transfers through the insulation to the metal sheath The sheath conducts heat to the surrounding material or medium Types of Cartridge Heaters Cartridge heaters come in various types to suit different applications. Here are some common varieties: Standard Cartridge Heaters: General-purpose heaters for most applications High-Watt Density Cartridge Heaters: For applications requiring intense heat Swaged Cartridge Heaters: Offer improved heat transfer and longer life Miniature Cartridge Heaters: For small spaces and precision heating Customized Cartridge Heaters: Tailored to specific application requirements Applications of Cartridge Heaters The versatility of cartridge heaters makes them suitable for a wide range of industries. Here are some common applications: Plastic Processing: Heating molds and nozzles in injection molding Food Industry: Maintaining temperatures in food processing equipment Medical Equipment: Sterilization and temperature control in medical devices Aerospace: Heating components in aircraft and spacecraft Packaging: Sealing and shrink-wrapping processes Automotive: Engine block heating and component testing 3D Printing: Maintaining precise temperatures for material extrusion Benefits of Using a Cartridge Heater Cartridge heaters offer several benefits that make them popular across industries: Compact Size: Fit easily into small spaces High Watt Density: Provide intense heat in a small package Precise Temperature Control: Allow for accurate heating Durability: Designed to withstand harsh industrial environments Versatility: Suitable for a wide range of applications Energy Efficiency: Concentrate heat where it’s needed most Easy Installation: Simple to insert and replace Selecting the Right Cartridge Heater Choosing the appropriate cartridge heater is crucial for optimal performance. Consider the following factors: Watt Density: Determine the heat output required Diameter and Length: Ensure proper fit in the application Sheath Material: Choose based on the operating environment Voltage: Match the heater to your power supply Temperature Requirements: Consider maximum operating temperature Special Features: Such as thermocouples or moisture resistance Energy Efficiency and Cost Considerations Cartridge heaters can be an energy-efficient heating solution when used correctly. Here’s why: Targeted Heating: Concentrates heat where it’s needed most Precise Control: Allows for accurate temperature management Quick Heat-Up: Reduces energy waste during warm-up periods Longevity: Quality cartridge heaters have a long operational life While the initial cost of a cartridge heater may be higher than that of some alternatives, its efficiency and longevity often result in long-term cost savings. Wrap Up As heating technology evolves, we expect even more cartridge heater design and functionality innovations. For now, these efficient and reliable heaters remain at the forefront of industrial and commercial heating solutions. Whether you’re considering cartridge heaters for a new application or looking to optimize your current heating processes, these versatile devices offer many benefits. Their ability to provide concentrated, controlled heat in a compact package makes them a valuable tool in our increasingly technology-driven world.